Повышение эффективности контурной обработки на станках с ЧПУ путем коррекции траектории и режимов резания
Автор:В.П. Маунг
Источник:1. В.П. Маунг. Обеспечение качества поверхностного слоя материала деталей машин / Тимирязев В.А., Хостикоев М.З.,Схиртладзе А.Г., ВэйПьо Маунг, Агеева В.Н. // Ж. «Технология машиностроения», №1 Тимирязев В.А., Хостикоев М.З., Схиртладзе А.Г., Ж. «Технология машиностроения», №1 (139).2014, с 7-12.
2. В.П. Маунг. Возможности управления качеством резьб, обрабатываемых накатыванием / Хостикоев М.З., Мнацаканян В.У.,Темников В.А., В.П. Маунг. // Ж. «Станки и инструмент» (СТИН) №8, 2014.
3. Вэй Пьо Маунг. Эффективность комплексной технологии изготовления деталей сложной геометрии на современных многоцелевых станках / Тимирязев В.А., Хостикоев М.З., Дудко С.В., Таиров И.Е., В.П. Маунг. // Ж. Технология машиностроения №10, 2014.
Вэй Пьо Маунг В работе рассматривается такой вопрос как повышении эффективности контурной обработки сложно профильных деталей машин на станках с ЧПУ путем управления процессом формообразования и режимами резания, как на этапе разработки управляющей программы, так и в процессе выполнения операции.
ОБЩАЯ ХАРАКТЕРИСТИКА РАБОТЫ
Актуальность темы диссертации. Развитие современной техники при тенденции повышения качества и снижения металлоёмкости изделий расширило состав и количество деталей машин сложной геометрической формы, изготовление которых осуществляется на дорогостоящих многоцелевых станках и на станках с ЧПУ. Поэтому проблема повышения эффективности использования такого оборудования является актуальной.
Изготовление на станках с ЧПУ многоэлементных деталей сложной геометрии –корпусов топливных и гидравлических систем аэрокосмической техники, полостей штампов и пресс-форм, шаблонов, кулачков, лопаток турбин и других представляет сложную технологическую задачу.
Входные параметры заготовки (припуск, твердость, жесткость) и инструмента (износ, затупление) изменяются как от детали к детали, так и в пределах одной детали. Эти параметры в большинстве случаев являются случайными, между тем как учесть при программировании только систематические составляющие этих факторов не просто.
Все эти вопросы особенно усугубляются при обработке деталей сложной геометрии концевыми фрезами, имеющими малую жесткость, или при обработке нежестких заготовок.
При контурной обработке программирование траектории и режимов резания затруднено из-за сложности учета углов сопряжения смежных поверхностей, изменения глубины, ширины фрезерования и угла контакта фрезы с обрабатываемой поверхностью.
Достижение требуемой точности обработки путем уменьшения влияния упругих деформаций при выполнении нескольких чистовых проходов существенно снижает производительность станка. Если на универсальном станке рабочий может в процессе обработки учесть изменения припуска, ширины фрезерования, степень затупления инструмента и угол его контакта с заготовкой, то на станке с ЧПУ оператор такой возможности не имеет.
Существенная потеря производительности возникает также при необходимости доработки углов сопряжения смежных поверхностей контура, которую, в ряде случаев, приходится выполнять не на станках с ЧПУ, а переносить на обычные универсально фрезерные станки.
Таким образом, задача создания эффективного программно-технологического обеспечения процесса формообразования сложно-профильных деталей, изготавливаемых на станках с ЧПУ, является актуальной и имеет как научную, так и практическую значимость.
Работа выполнялась в МГТУ СТАНКИН
в рамках Федеральной целевой программы «Исследования и разработки по приоритетным направлениям развития научно-технического комплекса России на 2007-2013 годы № 02.532.12.9002.
Цель работы состоит в повышении эффективности контурной обработки сложно профильных деталей машин на станках с ЧПУ путем управления процессом формообразования и режимами резания, как на этапе разработки управляющей программы, так и в процессе выполнения операции.
Методы исследования. Результаты диссертационной работы получены на основе теоретических и экспериментальных исследований с использованием системного анализа, методов математического моделирования, на базе фундаментальных положений технологии машиностроения, теории размерных цепей, теории баз, теории резания и программного управления станочным оборудованием.
Научная новизна работы - новое решение актуальной научной задачи – выявление связей между режимами и геометрией обрабатываемой поверхности, позволивших разработать программно-технологические методы повышения эффективности и точности контурной обработки сложно профильных деталей на станках с ЧПУ, что имеет существенное научное и практическое значение. Составляющими научной новизны являются:
- выявленные закономерности формирования отклонений контура при резких изменениях вектора силы резания, возникающих в результате изменении припуска, ширины и кривизны фрезеруемой поверхности;
- раскрытие технологических связей процесса контурного фрезерования, что позволило разработать технологические рекомендации по выбору последовательности выполнения переходов, по программированию траектории и направления обхода контура, по выбору расстояния между смежными строками и величины перекрытия с учетом параметров применяемых фрез;
- программируемые гибкие технологически циклы доработки углов сопряжения смежных поверхностей контура, позволяющие в автоматическом режиме фрезой меньшего диаметра выбрать в углах и карманах остающийся материал;
- установление связей между параметрами циклов доработки углов сопряжения, что позволило разработать стандартные подпрограммы, применение которых с программами зеркального отображения и поворота координатных систем, позволяет осуществить выборку остающегося припуска в других углах контура детали;
- выявление технологических связей, позволивших предложить методы управления точностью контурного фрезерования на этапе разработки УП; они предусматривают выбор режимов обработки и геометрии фрезы, при которых радиальная сила резания оказывает на отклонения контура минимальное влияние, а также коррекцию управляющей программы по результатам измерения первой изготовленной детали;
- методы компенсации отклонений контура, обусловленных погрешностью установки заготовки, режущего инструмента и отклонениями размера динамической настройки, порождаемыми действием случайных и систематических факторов; это достигается применением системы коррекции в исходном положении и адаптивных систем регулирования контурной подачи или размера статической настройки в процессе резания.
Практическая ценность работы:
- разработанное для многоцелевых станков и станков с ЧПУ программное обеспечение цикла доработки углов по схеме маятникового фрезерования;
- программное обеспечение цикла доработки углов по схеме многопроходного контурного фрезерования, позволяющего удалить металл в труднодоступных местах;
- практические рекомендации для выбора режимов контурного фрезерования, обеспечивающих минимальное влияние составляющей РY на точность контура детали;
- рекомендации по программированию скорости гидроабразивной резки нержавеющей стали, алюминия и гранита для достижения требуемого уровня качества реза при различной толщине материала.
В первой главе излагается анализ состояния проблемы, рассматриваются технологические задачи повышения эффективности и точности контурной обработки сложно профильных деталей машин на многоцелевых станках и на станках с ЧПУ, обосновываются цель и задачи исследования.
Вопросы повышения точности и эффективности изготовления деталей на многоцелевых станках и на станках с ЧПУ рассматривались в работах Б.С. Балакшина, Ю.М. Соломенцева, А.С. Васильева, А.А. Кутина, В.В. Морозова, В.А. Ратмирова, В.Л. Сосонкина, А.Г. Схиртладзе, В.А. Тимирязева, Д.В. Чарнко А.С. Ямникова и др. Задачам проектирования технологий для станков с ЧПУ посвящены работы В.А. Гречишникова, Г.Б. Евгеньева, Ю.В. Максимова, В.Г. Мартинова, П.П.Серебрицкого, А.П. Сиротенко, О.В.Хазановой, М.З. Хостикоева, В.Ю.Шишмарева и др.
В соответствии с поставленной целью - повышения эффективности и точности контурной обработки сложно профильных деталей на станках с ЧПУ определена необходимость решения следующих научных задач:
- выявить факторы, определяющие причины формирования отклонений и потери производительности контурной обработки;
- исследовать механику формирования отклонений контурных поверхностей, возникающих на этапах установки, статической и динамической настройки технологической системы;
- разработать и исследовать программируемые циклы доработки углов сопряжения смежных поверхностей, обеспечивающих удаление в углах и карманах лишнего материала;
- выявить программно-технологические решения и дать рекомендации, позволяющие управлять процессом достижения точности и производительности контурной обработки деталей сложной геометрии как на этапе разработки УП, так и в процессе резания.
Во второй главе рассматриваются вопросы формирования отклонений параметров точности деталей при контурном фрезеровании. К точности 8 контурной обработки предъявляют повышенные требования: точность получаемых размеров 0,05…0,2 мм, погрешность формы в пределах 0,3…0,5 шероховатость поверхности Ra = 1,6...3,2 мкм, а точность диаметральных размеров отверстий по квалитетам IT8… IT7. При малой жесткости концевых фрез (менее 10000 Н/мм) изменения угла контакта фрезы с заготовкой, ширины В(В 1… В max) и глубины резания t (tн…tmax), обусловленные сложной конфигурацией детали (рис.1)
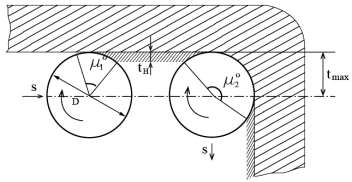
Рисунок 1 – Изменения параметров обработки при контурном фрезеровании концевой фрезой:
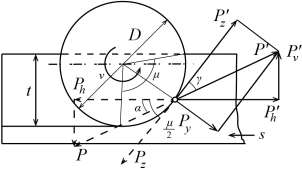
Рисунок 2 – Схемы действия сил резания при встречном
Исследования показывают, что доминирующее влияния на отклонения размера Aд оказывает боковая составляющая Рv, которая при различных значениях глубины t, ширины фрезерования В и контурной подачи s меняет как величины, так и направление, вызывая отклонения Aд (см. рис. 3).
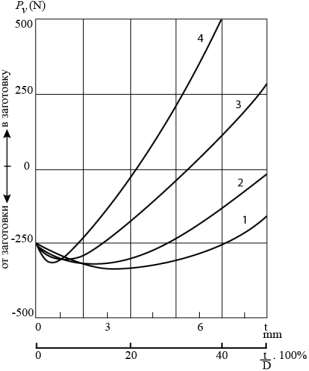
Рисунок 3 – Характер изменения боковой составляющей силы резания при изменении параметров обработки
1 - sz =0,02мм/зуб; 2 - sz = 0,04мм/зуб;
3- sz= 0,08мм/зуб; 4 - sz = 0,016мм/зуб.
В третьей главе рассматриваются вопросы достижения требуемой геометрии контура путем рационального составления программ и доработки углов сопряжения смежных поверхностей. Упрощенное описание контура обрабатываемой поверхности позволяет сократить запись управляющей программы за счет сосредоточения в одном - двух кадрах информации, описание которой обычно требует большего числа кадров УП. При этом представляется возможным осуществить сглаживание углов, исключив необходимость вычисления ряда размеров в опорных точках сопряжения поверхностей.
Припуск, оставляемый после контурной обработки углов и карманов фрезами большого диаметра, требует удаления, которое на практике выполняют на универсальных станках или путем осевого заглубления фрезами малого диаметра. Для исключения этих малопроизводительных технологий разработаны два высокоэффективных цикла доработки углов – цикл маятникового фрезерования и цикл многопроходного контурного фрезерования.
В четвертой главе рассматриваются технологические методы управления процессом контурного формообразования как на этапе разработки УП, так и в процессе выполнения операции, что позволяет повысить эффективность и точность контурной обработки сложно профильных деталей на станках с ЧПУ.
Для компенсации погрешностей, возникающих на этапе формирования размера установки Aу (отклонения положения заготовки, спутника и режущего инструмента) предложено использовать систему коррекции в исходном положении. Отклонения инструмента целесообразно компенсировать путем эквидистантной коррекции траектории (подготовительные функции G41,G42) или путем программируемого смещения контура детали G60, а отклонение положения заготовки путем смещения и поворота ее координатной системы (функции G138, G139).
Выводы
В работе содержится новое решение актуальной научной задачи – выявление связей между режимами обработки, траекторией движения, геометрией детали и инструмента, позволивших разработать программно-технологические методы повышения эффективности и точности контурной обработки сложно профильных деталей машин на станках с ЧПУ, что имеет существенное научное и практическое значение для развития технологии машиностроения.
Проведенный анализ фрезерных переходов, траекторий перемещения фрез и связей между требованиями точности детали, параметрами фрезы (ее диаметром, радиусом режущих кромок на торце) и величиной перекрытия, позволили разработать технологические рекомендации по выбору последовательности выполнения переходов, по программированию траектории и направления обхода контура, по выбору расстояния между смежными строками.
Для достижения требуемой геометрической точности обрабатываемой контурной поверхности и исключения на ней «зарезов», величина которых достигает 0,5…1 мм при допуске на размер 0,1..0,2 мм, нельзя допускать в рабочем цикле остановку движения фрезы или резкого изменения подачи при соприкосновении инструмента с обрабатываемой поверхностью.
Установлено, что отклонения размера динамической настройки при контурном фрезеровании обусловлены резкими изменениями вектора силы резания, возникающими при изменении припуска, ширины и кривизны обрабатываемой поверхности. При этом наибольшее влияние на точность оказывает боковая Рv составляющая, которая в местах изменения кривизны контура меняют как величину, так и направление. В результате на замыкающем звене происходит многократное изменение упругих перемещений (до 10 и более раз), что приводит к значительным отклонениям параметров точности детали.
Для упрощения программы фрезерования сложных контурных поверхностей и уменьшения числа кадров УП, программирование целесообразно осуществлять с использованием схем рационального (упрощенного) описания контура с применением вложенных подпрограмм, позволяющих осуществить допустимое сглаживание углов, исключив при этом необходимость выявления дополнительных опорных точек и их координат в местах сопряжения смежных поверхностей. Все это возможно реализовать в развитых системах ЧПУ класса CNC с высоким уровнем программного обеспечения.
Для удаления припуска, оставляемого в углах и карманах после контурной обработки фрезами большого диаметра, разработаны два высокоэффективных цикла доработки углов – цикл маятникового фрезерования и цикл многопроходного контурного фрезерования. Применение новых циклов позволяет выполнить полную обработку контурной поверхности за одну установку заготовки, исключив потери, связанные с необходимостью доработки углов на универсальных станках. Использование подпрограмм зеркального отображения и поворота координатных систем, позволяет применять эти циклы для доработки однотипных углов контура, расположенных на других участках детали.
Установлено, что отклонения контура гидроабразивного реза, обусловленные искривлением оси гидроабразивной струи, и удаление остающегося в полостях невыбранного материала возможно осуществить путем использования разработанных циклов доработки полостей и коррекции траектории перемещения гидроабразивной головки.
Компенсация отклонений размера динамической настройки, порождаемых при резании действием случайных и систематических факторов, достигается путем применения адаптивных систем, осуществляющих регулирование контурной подачи или размера статической настройки на основе прямых или косвенных измерений отклонений на замыкающем звене. 10. Использование разработанных технологических решений - циклов доработки углов, систем коррекции отклонений, позволяет в два, три раза повысить точность контура, уменьшить машинное время и количество кадров УП, что позволяет на 25..30%. повысить производительность станка. Результаты исследования нашли внедрение на производстве и в учебном процессе вуза. Годовой экономический эффект, получаемый от внедрения на одном многоцелевом станке, составляет не менее 1,3 млн. руб.
Список использованной литературы
В.П. Маунг. Обеспечение качества поверхностного слоя материала деталей машин / Тимирязев В.А., Хостикоев М.З.,Схиртладзе А.Г., В.П. Маунг, Агеева В.Н. // Ж. «Технология машиностроения», №1 Тимирязев В.А., Хостикоев М.З., Схиртладзе А.Г., Ж. «Технология машиностроения», №1 (139).2014, с 7-12.
В.П. Маунг. Возможности управления качеством резьб, обрабатываемых накатыванием / Хостикое М.З., Мнацаканян В.У., Темников В.А., В.П. Маунг. // Ж. «Станки и инструмент» (СТИН) №8, 2014.
Вэй Пьо Маунг. Эффективность комплексной технологии изготовления деталей сложной геометрии на современных многоцелевых станках / Тимирязев В.А., Хостикоев М.З., Дудко С.В., Таиров И.Е., В.П. Маунг. // Ж. Технология машиностроения №10, 2014.