Разработка экологически чистой технологии и конструкции установки для переработки растительного сырья и бытовых отходов
Авторы: Федоренко В.А., Старостина Е.Н., Ошовский В.В.
Источник: Охрана окружающей среды и рациональное использование природных ресурсов: сборник докладов ХII Международной конференции аспирантов и студентов / ДОННТУ, ДонНУ. – Донецк: ГОУ ВПО «ДОННТУ», 2018. – 231 с.
Аннотация
Федоренко В.А., Старостина Е.Н., Ошовский В.В. – Разработка экологически чистой технологии и конструкции установки для переработки растительного сырья и бытовых отходов. Разработана принципиальная схема установки и приведена технология для получения биотоплива и древесно-полимерного композита (ДПК). Детально описана система управления и контроля за технологией производства с применением новейших контрольно-измерительных приборов.
Общая постановка проблемы
Переработка растительного сырья и бытовых отходов в наше время является важным этапом улучшения жизни человека, как с экологической, так и с технической стороны. Актуальность данной темы обусловлена малой интенсивностью переработки данного сырья и большими предпосылками получения качественного материала. Ценовой всплеск на рынке нефти и нефтепродуктов, рост цен на не возобновляемое твёрдое и газообразное топливо, поощряют потребителей активнее переходить на альтернативные виды энергоносителей. Кроме экономических способствуют этому и экологические предпосылки. Наш мир служит огромным резервуаром для скопления большого количества бытовых и сельскохозяйственных отходов, которые пагубно влияют на состояние окружающей среды.
Биоэнергетика – это инновационная отрасль экономики, основанная на производстве из биомассы топлива и энергии. В результате применения термохимических и биотехнологий по преобразованию энергии биомассы растений и возобновляемых ресурсов получают тепло, электричество, моторное биотопливо (биоэтанол, биобутанол, биодизель и прочие).
Главное преимущество биоэнергетики по сравнению с традиционными способами получения энергии – это возможность утилизации отходов и выбросов углекислого газа в атмосферу, что приводит к улучшению экологической обстановки.
Биоэнергетика является основным, но не единственным способом переработки растительного сырья и бытовых отходов. На сегодняшний день из этих компонентов производят новый высокопрочный экологически чистый, не подвержен гниению материал – термопластический древесно-полимерный композит (ДПК).
Материалы из древесно-полимерного композита сегодня широко применяются в Америке, европейских странах, Японии. По внешнему виду они схожи с древесиной и вместе с тем не подвержены гниению и плесени, не впитывают влагу, не имеют дефектов поверхности, высокотехнологичны в получении, и, наконец преимущество такой продукции – её экологичности. Кроме того, разработка технологии производства ДПК позволяет не только получить инновационную конкурентоспособную продукцию, но и решить вопросы переработки полимерных отходов [1].
Анализ существующих конструкционных схем
Для разработки конструкции установки и технологии производства , нужно проанализировать существующие конструкционные схемы.
Известные способы изготовления брикетов из измельченного растительного исходного сырья основаны на прессовании сырья в шнековом экструдере при нагревании цилиндра экструдера и формующей головки посредством электрических нагревателей. В процессе прессования материал твердеет, при этом наружный слой формованного брикета приобретает наиболее плотную структуру. Для того чтобы уменьшить неоднородность полученного готового изделия в поперечном сечении его изготавливают цилиндрической формы с полостью в центре [2].
При этом брикетирование древесины (древесных отходов) происходит без связующего. За счет повышения температуры, лигнин который содержится в сырье размягчается и склеивает брикеты. Для прессования другого растительного сырья за частую используют связующее. В качестве связующего могут выступать отходы коксохимических или нефтехимических предприятий, в небольших количествах: патока, глина и животные остатки.
Недостатками при таком брикетировании является малая механическая прочность, которая при транспортировке приводит к разрушению топливных брикетов.
Известно брикетированное топливо, в котором в качестве связующего выступают пластиковые отходы (полиэтилен, пластиковые бутылки).
Изобретение относится к твердому топливу, которое может быть использовано в промышленности и для коммунально-бытовых нужд для утилизации пластмассовых отходов и отходов растительного происхождения. Предложенное твердое топливо содержит материал растительного происхождения и связующее [3].
Этом метод и взят за основу разработки технологии производства топлива из растительного сырья и бытовых отходов.
Преимуществом данного метода является:
– высокая прочность изделия, которая предотвращает разрушение брикетов при транспортировке;
– высокая гидрофобность, позволяет уменьшить затраты на хранение продукта;
– брикеты могут использоваться для производства синтез газа.
При сжигании брикетов с пластмассовым связующим происходит выделение синтез газа, при сгорании которого увеличивается КПД топлива.
Следует отметить, что разрабатывается технология производства, которая позволит применять одни и те же компоненты для производства разных материалов. Важным этапом является сохранения состава исходных компонентов и получения различных по своим свойствам продуктов. Всё это достигается с помощью смены температурного режима и скорости подачи материала из бункера в зону нагрева.
Этапы работы
Первым этапом работы является разработка оборудования для переработки растительного сырья и бытовых отходов (пластика). Вторым важным этапом работы является разработка новой технологии получения продукта.
Установка, которая представлена в работе (рис.1), позволит получать топливные брикеты и термопластический древесно-полимерный композит.
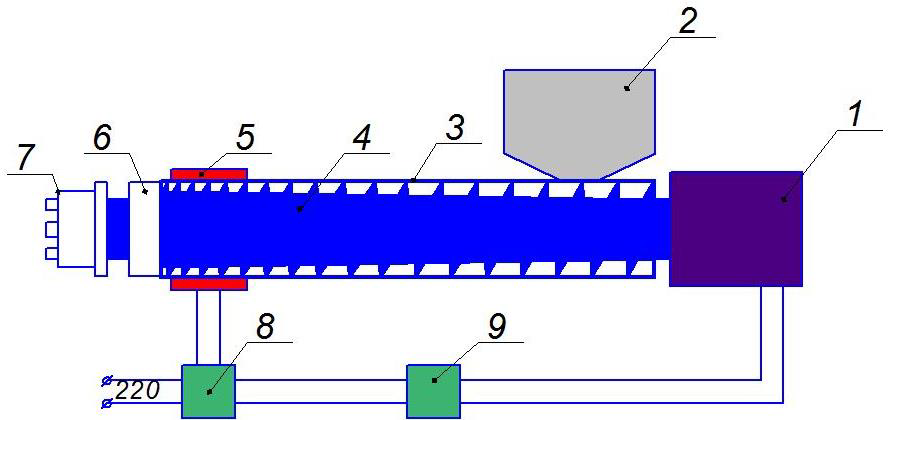
1 – двигатель; 2 – загрузочный бункер; 3 – гильза; 4 – шнек; 5 – хомут-нагреватель; 6 – фильтр; 7 – головка; 8 – терморегулятор; 9 – микроконтроллерный регулятор.
Рисунок 1 – Принципиальная схема установки для получения биотоплива и ДПК
Процесс получения продукта можно представить в виде следующих стадий:
– подготовка сырья перед процессом брикетирования (обязательно нужно тщательно измельчить все компоненты и равномерно перемешать);
– загрузка бункера шихтой;
– продвижение смеси шнеком по гильзе в зону нагрева, где происходит процесс нагрева и уплотнение;
– выдача готового продукта, через сменную экструзионную головку и охлаждение до комнатной температуры.
Преимуществом данной установки является автоматизация процесса нагрева, и контроля за процессом. С помощью электронного терморегулятора можно задавать наилучшую температуру процесса с высокой точностью. Новый нагревательный элемент позволяет произвести интенсивный нагрев за короткое время. Особую роль в процессе автоматизации играет специальный микроконтроллерный регулятор, который автоматически при изменении температуры управляет количеством оборотов двигателя. Данная автоматика позволяет перерабатывать сырьё с разной влажностью. Это позволяет исключить из цикла предварительную сушку исходных компонентов.
Сменой экструзионной головки в данной установке можно гибко изменять технологический процесс производства различных композиционных материалов.
Недостатками данной установки является:
– установка не оснащена сигнализацией, в бункере исходного материала не имеется датчика загрузки или подвисания сырья;
– бункер не оснащен вибрацией (при работе с сырьём разной влажности – это необходимое условие).
Выводы
На данном этапе работы, главной целью является запуск установки, диагностика автоматического регулирования температурного режима, а также наблюдение за работой установки. Особую роль занимает программирование микроконтроллерного регулятора, который отвечает за качество выходящего продукта. В конечном итоге, это даст возможность получить качественный материал при минимальных затратах.