Эффективный ленточный конвейер в подземной системе транспортирования руды
Авторы: Robert Krol, Witold Kawalec, Lech Gladysiewicz
Автор перевода: Д. Л. Клименко
Аннотация
В статье предложена инновационная конструкция ленточного конвейера для системы подземного транспорта. Разработанная энергоэффективная конвейерная лента и оптимизированные роликоопоры являются ключевыми элементами нового поколения подземных ленточных конвейеров. Опыт эксплуатации показал, что предлагаемые решения могут обернуться значительной экономией энергии и меньшими затратами на обслуживание.
1. Введение
Технологические процессы в горнодобывающей промышленности включают различные операции по транспортировке сырья, которые потребляют значительное количество энергии и составляют значительную долю общих затрат на добычу полезных ископаемых. Наибольшая экономия может быть достигнута в результате оптимизации планирования и проектирования горных работ [1], но существующая транспортная система в шахте все еще может быть улучшена, для того чтобы соответствовать растущим потребностям сокращения удельных транспортных расходов и снижения выбросов CO2. Однако, энергоэффективность и экономия затрат не должны преобладать над требованиями надежности и достаточной пропускной способности любой горнотранспортной системы. В подземных выработках – из соображений безопасности и относительно сложных условий обслуживания оборудования транспортной техники – опытные технические специалисты обычно предпочитают машины негабаритных размеров. Внедрение нового решения должно предшествовать пройденным комплексным испытаниям, которые гарантируют соответствие всем требованиям безопасности, а также технологическим требованиям.
Транспортные системы, используемые в подземных рудниках KGHM по добыче медной руды, были выбраны и спроектированы для камерной и колонковой систем разработки [2]. Характерной особенностью горизонтального транспорта на всех трех рудниках KGHM является использование на различных этапах и в разном масштабе как циклического транспорта (погрузочно-доставочные машины – ПДМ, грузовики и железнодорожный транспорт), так и непрерывного транспорта большой вместительности (ленточные конвейеры – ЛК ). Общая протяженность подземных ленточных конвейеров превышает 165 км. Приблизительно 2/3 всех установленных в горных выработках конвейеров являются участковыми, они непосредственно загружаются ПДМ и грузовиками. Остальные конвейеры работают на магистральных транспортных маршрутах. Эти конвейеры собирают руду с нескольких участковых конвейеров и доставляют ее в шахтные бункеры.
Основная цель управления системой ленточного конвейерного транспорта на подземных рудниках KGHM – поддержание высокого уровня общего объема добычи руды. Одно из главных требований горнодобывающих предприятий – избегать задержек с разгрузкой карьерных самосвалов и ПДМ из-за любых остановок ленточных конвейеров. Такие задержки приводят к уменьшению количества выполненных циклов для самосвалов – меньше руды будет выдано из очистного забоя. Поэтому обычно предполагается, что ленточные конвейеры, которые получают руду от циклического транспорта, будут работать в течение всей рабочей смены. Несмотря на то, что существует множество бункеров для руды (рис. 1), их полная вместительность необходима для того, чтобы дать возможность непрерывно работать очистному забою даже в случае непредвиденной остановки какого-либо из ленточных конвейеров.
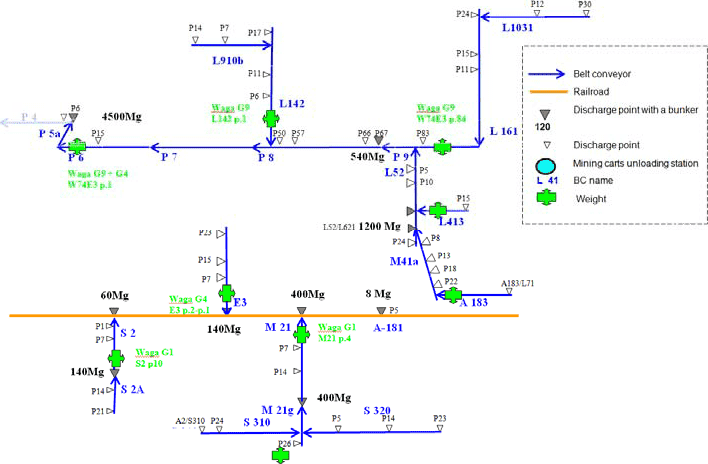
Рисунок 1 – Схематический вид выбранной ветви системы ленточного конвейерного
транспорта на шахте KGHM Lubin
Холостой режим работы ленточного конвейерного транспорта при подземной транспортировке руды является результатом того, что на первое место в списке приоритетов ставят высокую производительность очистных забоев. Таким образом, для достижения значительной экономии энергии при транспортировке руды в подземной системе конвейерного ленточного транспорта необходимо принять меры по снижению удельного энергопотребления ленточными конвейерами за счет снижения энергопотребления их холостого хода. Достигнуть этого можно непосредственно при помощи улучшения конструкции ленточного конвейера с целью снижения потребления энергии. Способы снижения энергопотребления ленточного конвейера во время холостого хода [3, 4, 5]:
- тщательный выбор конвейерной ленты с учетом параметров резиновой смеси, подобранной индивидуально для планируемых условий эксплуатации на используемом объекте;
- усовершенствованные роликоопоры с пониженным сопротивлением движению;
- точное вычисление размеров элементов конвейера (требует использования современных компьютерных средств проектирования).
Единственный возможный путь успешного улучшения элементов ленточных конвейеров, предназначенных для работы в тяжелых условиях эксплуатации подземных шахт – обширное обеспечение проведения испытаний на месте в сочетании с точными расчетами требуемой мощности привода ЛК с учетом альтернативных вариантов подбора оборудования для ЛК [3]. Внедряемые решения более подробно описаны ниже.
2. Решения для подземных ленточных конвейеров, транспортирующих руду
Теоретические и экспериментальные (проводимые в лабораторных условиях, а также на местах) исследования ленточных конвейеров большой грузоподъемности в области главных факторов сопротивления движению выполняются в течение многих лет [6, 7, 8]. Основа исследования, проведенного на Факультете Геоинженерии, Горного дела и Геологии во Вроцлавском технологическом университете – это анализ процессов потерь энергии в конвейерной ленте и в потоке материалов, а также анализ взаимодействия между лентой и роликоопорами [9]. Эти процессы зависят от большого набора технических, физических и эксплуатационных характеристик ленты, транспортируемого сыпучего материала, конструктивных характеристик конвейера и условий эксплуатации конвейера [7]. Физические свойства ленты и сыпучего материала, а также геометрия конвейера были использованы в алгоритме для определения основных сопротивлений движению ленточного конвейера: сопротивление движения роликоопор, сопротивление вдавливания, сопротивления изгиба ленты и сыпучего материала и сопротивление скольжения ленты на холостом ходу.
Сведения об использовании и обслуживании больших транспортных систем подтверждаются информационными [11] и диагностическими [12] системами, которые отслеживают и анализируют рабочие параметры, записанные с работающих ленточных конвейеров. Полученные результаты позволяют выбрать технические усовершенствования в оборудовании ленточных конвейеров, которые должны обеспечить необходимую экономию энергии и средств при сохранении надежности и безопасности стандартных подземных ленточных конвейеров.
Исследования в области создания эффективного подземного ленточного конвейера для транспортировки медной руды состояли из трех ключевых элементов:
- Идентификация условий эксплуатации ленточных конвейеров в подземной транспортной системе – распределение нагрузки, типовая длина маршрута конвейера и наклон, эксплуатационные опасности, использование имитационных моделей [13].
- Лабораторные испытания предварительно выбранных решений для усовершенствованных конвейерных лент [14] и роликоопор [15] для выбора предпочтительных из них, а также всесторонние испытания предложенных решений на месте [16, 17].
- Разработка методов расчета сопротивления движению ленточного конвейера с учетом индивидуальных характеристик усовершенствованного оборудования и принятых условий эксплуатации подземных конвейерных транспортных систем [18].
Параметры изученных ленточных конвейеров (как испытанных на месте, так и рассчитанных на основе их фактических или предполагаемых параметров) представлены в таблице 1.
Параметр | Значение |
Транспортируемая продукция; плотность, кг/м3 | Медная руда, 1700 |
Температура окружающей среды, °C | 25 |
Длина, м; наклон маршрута | 500, 700, 1500; горизонтальный |
Ширина конвейерной ленты, мм | 1000 |
Тип ленты; толщина обкладок, мм | Трудносгораемые; EP2000/4 6+3 или 1000 ST 2000 8+6 |
Скорость ленты, м/с | 2, 2.3 |
Расстояние между роликоопорами, м | Варианты: 0.83; 1.25; 1.66 (использовалось: 0.83) |
Сопротивление движению верхнего натяжного ролика, Н | Согласно приведенным характеристикам |
Фактическая производительность, т/ч | 0, 200–1400 |
Натяжная станция | С поправкой на максимальную нагрузку |
2.1 Усовершенствованная конвейерная лента
Улучшение оборудования ленточных конвейеров было сосредоточено на уменьшении сопротивления движению холостого хода и сопротивления вдавливанию, которые вместе составляют до 70% от общей силы сопротивления движению ленточного конвейера [7, 9]. Согласно теоретическому анализу, сопротивление вдавливанию зависит от двух параметров ленты: коэффициента демпфирования ленты, подвергаемой циклическому сжатию, и поперечной жесткости на изгиб [5, 6]. Правильный выбор материала для резиновых нижних обкладок ленты может значительно снизить сопротивление вдавливанию.
Свойства различных резиновых смесей исследовались на специальном испытательном стенде в климатической камере, где с помощью циклического прессования моделировались условия работы ленты [17]. Характеристики и параметры, определенные в лаборатории, были затем внедрены в компьютерную модель ленточного конвейера [18]. Исходя из них и принятых условий эксплуатации подземных ленточных конвейеров, было рассчитано удельное потребление энергии (количество энергии, необходимое для перемещения 1 кг транспортируемой руды на горизонтальное расстояние 1 м) магистрального ленточного конвейера (табл. 2). В таблице приведен анализ нескольких новых энергоэффективных конвейерных лент с инновационной резиновой смесью (B…D), а также проведено сравнение со стандартной лентой – A. Лента B была отобрана для проведения дальнейших испытаний и, в конечном итоге, была внедрена в эффективный ленточный конвейер.
Тип конвейерной ленты (A – стандартная лента) | Удельный расход энергии ЛК (L = 1500 м) [Вт/кг] | Удельный расход энергии верхней ветвью ЛК [Вт/кг] |
A | 0.455 | 0.302 |
B | 0.372 | 0.239 |
B+ | 0.399 | 0.253 |
C | 0.422 | 0.274 |
D | 0.396 | 0.275 |
Полученная почти 20% экономия удельного расхода энергии была достигнута для данных рабочих параметров ленточного конвейера (распределение нагрузки, длина, температура окружающей среды), однако, это не означает, что такой результат будет повторяться для ленточных конвейеров другой конструкции. Сравнение результатов серии теоретических расчетов с результатами испытаний на месте показало, что условия эксплуатации (особенно фактическое распределение нагрузки и возникновение режима холостого хода в течение рабочего времени) могут увеличивать или уменьшать фактическую экономию энергии ленточным конвейером.
2.2 Усовершенствованные роликоопоры
Роликоопора – пример продукта, который выглядит просто, но из-за суровых условий эксплуатации и конфликтных требований (низкое сопротивление движению и легкая конструкция в сравнении с долговечностью) должен быть тщательно спроектирован и испытан, для того чтобы стать надежной частью ленточного конвейера. Условия эксплуатации в подземном руднике с его агрессивной влажностью, пылью и наличием больших кусков руды, ударяющих роликоопоры через ленту, являются настоящей проблемой для поставщиков горного оборудования.
Был представлен проект комплексного проектирования и испытаний для разработки нового поколения
энергоэффективных и надежных роликоопор применяемых в подземных работах
[10, 15, 16]. После лабораторных
испытаний [15] отобранные роликоопоры были установлены на экспериментальном ленточном
конвейере в шахте KGHM Lubin
(рис. 1). Продолжительные испытания на месте
[16] дали адекватные результаты, которые подтверждают эффективность решения.
Усовершенствования коснулись конструкции валков, уплотнений подшипников, смазки и компоновки всей
роликоопоры (подвесная конструкция роликоопоры заменена на жестко установленную). График на рисунке
2 показывает полученное снижение сопротивления движению роликоопоры.
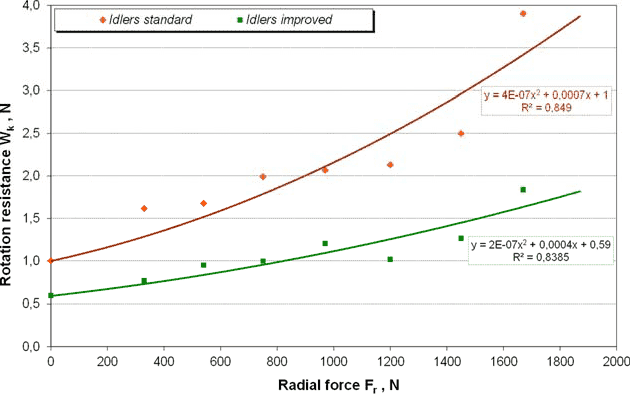
Рисунок 2 – Среднее значение сопротивления движению роликоопоры 133×370 мм в зависимости от радиального усилия (для стандартных и усовершенствованных роликоопор)
Жестко установленные роликоопоры помогают снизить сопротивление скольжению (может быть вызвано горизонтальным перекосом боковых валков), что положительно сказывается на симметричной нагрузке боковых валков. Любые различия между вертикальными силами на боковых валках означают, что один из них может быть перегружен и его срок службы значительно сократится (рис. 3).
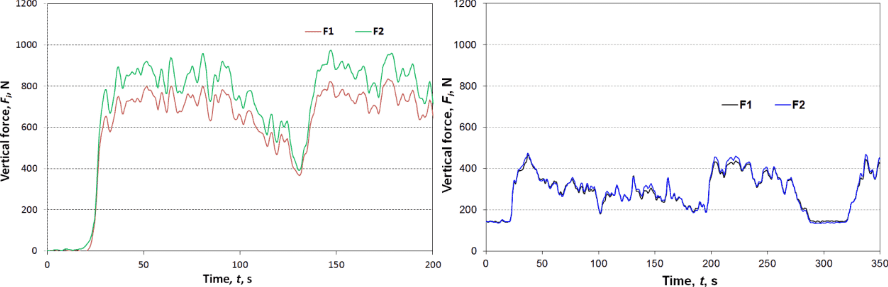
Рисунок 3 – Регистрируемые вертикальные силы на боковых валках подвесных роликоопор (слева) и жестко установленных роликоопор (справа)
Расчеты, выполненные на основании результатов измерений [10], показали, что расстояние между роликоопорами, стандартное значение которого составляет 0.83 м, можно увеличить как минимум до 1.25 м для участковых конвейеров, без потери их надежности. Такая компоновка еще не проходила натурных испытаний.
2.3 Комбинированные результаты
Отобранные и испытанные усовершенствования энергоэффективной резинотросовой конвейерной ленты и новых роликоопор в конечном итоге были реализованы в экспериментальном ленточном конвейере, за которым в течение длительного времени наблюдали с помощью специально собранного измерительного стенда [16]. Сопротивление движению регистрировали в широком диапазоне нагрузок и сравнивали с результатами измерений, полученными на стандартном конвейере. Сравнение представлено на рисунке 4.
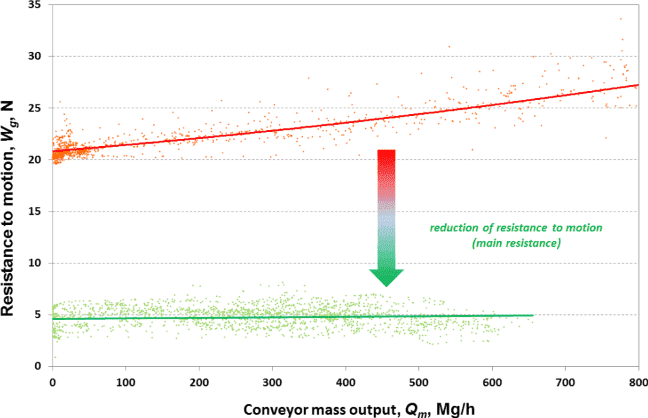
Рисунок 4 – Сравнение измеренных сопротивлений движению стандартного (верхняя линия) и эффективного (нижняя линия) ленточных конвейеров
Полученный результат является многообещающим и показал, что принятые технические решения оправдали ожидания. Экспериментальный ленточный конвейер работает в тяжелых условиях типичной горной выработки. Следует подчеркнуть, что испытанные улучшения не требуют серьезного обновления существующего оборудования. Конвейерная лента и роликоопоры заменяются в связи с их нормальным износом, таким образом стандартные элементы могут быть заменены на более эффективные.
3. Ожидаемая экономия для подземных систем транспортировки руды
Замена стандартных подземных ленточных конвейеров на более эффективные возможна, но компания должна знать, может ли принести это пользу. Результаты измерения сопротивления движению (подтвержденные расчетами) должны быть приведены к числам, которые представят количество энергии, потребляемой ленточным конвейером во время среднестатистической нагрузки.
На основании длины участковых и магистральных ленточных конвейеров отдельной ветви транспортной системы шахты
KGHM Lubin
(рис. 1) была рассчитана возможная экономия. Участковые конвейеры работают около
4000 часов в год при средней производительности 192 т/ч. Магистральные конвейеры работают намного дольше
(около 6000 часов в год), их средняя производительность также выше и составляет около 834 т/ч. Удельный
расход энергии был рассчитан для всего диапазона загрузки конвейеров транспортируемой рудой. Значения в
4-м столбце таблицы 3 представляют собой средневзвешенные значения распределения массы потока
транспортируемой руды, зарегистрированной для участковых и магистральных ленточных конвейеров
[10]. Высокое значение удельного расхода энергии для участковых ленточных конвейеров
обусловлено тем, что около 30% их рабочего времени занимает режим холостого хода. Как упоминалось
выше, этого нелегко избежать по специфичным для горной промышленности причинам.
Предполагаемая стоимость энергии не включает в себя различные коэффициенты и тарифы, которые применяются к электроэнергии, потребляемой днем и ночью.
Тип конвейерного транспорта | Тип ЛК | Средняя производительность [т/ч] | Удельный расход энергии ЛК [Вт/кг] | Годовое потребление энергии ЛК [кВтч/м] | Общегодовое потребление энергии [МВтч] | Ориентировочная годовая стоимость энергии (60 €/МВтч) [тыс. €] |
Участковый | стандартный | 192 | 1.705 | 364 | 4320 | 260 |
эффективный | 192 | 0.92 | 197 | 2330 | 140 | |
экономичный | 192 | 0.78 | 167 | 1990 | 120 | |
Магистральный | стандартный | 834 | 0.48 | 667 | 5182 | 311 |
эффективный | 834 | 0.234 | 326 | 2530 | 152 | |
экономичный | 834 | 0.245 | 341 | 2652 | 159 |
Представленная оценка показывает, что только по анализируемой ветви экономия на счетах за электроэнергию может составить около 0.3 млн евро. Экономия энергии и затрат на электроэнергию для всех подземных рудников KGHM представлена в таблице 4. Эти оценки менее точны, поскольку общая длина ленточных конвейеров была разделена следующим образом: ленточные конвейеры – 75%, магистральные конвейеры – 25%. Затем средневзвешенная годовая экономия энергии умножается на общую протяженность маршрутов ленточных конвейеров в каждой шахте компании KGHM.
Шахта | Полная протяженность конвейерных маршрутов [м] | Ожидаемая годовая экономия потребления энергии [МВтч] | Расчетная годовая экономия затрат на электроэнергию (60 €/МВтч) [млн. €] |
Rudna | 51185 | 10774 | 0.646 |
Lubin | 40185 | 8459 | 0.508 |
Sier-Pol | 75755 | 15946 | 0.957 |
Всего | 167125 | 35180 | 2.111 |
Предполагаемая экономия энергии в размере 35 ГВтч за счет модернизации подземных ленточных конвейеров является существенной и должна способствовать предлагаемым улучшениям. Прогнозируемая большая экономия с сохранением эффективности ленточного конвейера достигается за счет: оптимизированного расстояния между роликоопорами [10] и предотвращения режима холостого хода (когда это возможно).
4. Выводы
Были разработаны технические усовершенствования для нового поколения подземных ленточных конвейеров, транспортирующих руду, которые включают в себя энергоэффективную конвейерную ленту и оптимизированные роликоопоры.
Предлагаемые решения были всесторонне протестированы в лаборатории и на экспериментальном ленточном
конвейере, который был установлен в горной выработке шахты KGHM Lubin
для обеспечения проведения
горных работ. Были также проведены испытания на долговременную надежность, чтобы руководство шахты могло
убедиться, что новое энергоэффективное оборудование не нарушит требований времени работы.
Результаты измерений также были отражены (как конкретные характеристики оборудования) в точных методиках расчета сопротивления движению для ленточного конвейера. Расчеты использовались как для исследования рабочих параметров модернизированных ленточных конвейеров, так и для оценки возможной экономии энергии и средств после внедрения эффективных ленточных конвейеров в подземных транспортных системах на рудниках KGHM. Можно сэкономить около 35 ГВтч электроэнергии, что составляет более чем 2 миллиона евро затрат на покупку электроэнергии.
Столь существенное снижение потребляемой энергии означает не только снижение прямых счетов за электроэнергию,
но и помогает компании избежать дополнительных расходов на углеродные
лимиты. Любые энергоэффективные
решения создают горнодобывающей компании более экологичное
лицо, что важно для ее общественного
имиджа, независимо от реальных технических достижений.
Подтверждение(я)
Работа выполнена при финансовой поддержке Министерства науки и высшего образования Польши в качестве научного проекта № 0401/0166/16.
Ссылки
- T. D. Lee,
Planning and mine feasibility study – An owner perspective
. In: Proceedings of the 1984 NWMA Short CourseMine Feasibility – Concept to Completion
. (G.E. McKelvey, compiler) Spokane, WA, 1984. - M. Hardygora, L. Gladysiewicz,
Analysis Of Transportation Systems In Polish Mining Industry
, Proceedings of 12th International Symposium on MPES 2003, Kalgoorlie, Western Australia, 2003. - L. Gladysiewicz, W. Kawalec,
Energy saving solutions for belt conveying
. Proceedings of the Eleventh International Symposium on Mine Planning and Equipment Selection, Bouzov, Czech Republic, 9–11 September 2002, VSB – Technical University of Ostrava, 2002. - G. Lodewijks,
The next generation low loss conveyor belts
, Bulk Solids Handling 32 (1): 52–56, January 2012. - J. I. O’Shea, C. A. Wheeler, P. J. Munzenberger, D. G. Ausling,
The Influence of Viscoelastic Property Measurements on the Predicted Rolling Resistance of Belt Conveyors
, J. Appl. Polym. Sci. 2014. - G. Lodewijks,
The rolling resistance of conveyor belts
. Bulk Solids Handling, Volume 15, Number 1, January/March. 1995. - L. Gladysiewicz,
Belt conveyors. Theory and calculations
, Wroclaw University of Technology Publishing House, Wroclaw (in Polish), 2003. - L. Gladysiewicz, M. Hardygora, W. Kawalec,
Determining belt resistance
. Bulk Handling Today, No.5, 2009. - L. Gladysiewicz, W. Kawalec,
The possibilities of decreasing the belt conveyors main drive power demand
, Proceedings of the Conference Bulk Europe 2008, Prague, 2008. - L. Gladysiewicz, W. Kawalec, R. Krol,
Selection of carry idlers spacing of belt conveyor taking into account random stream of transported bulk material
. Eksploatacja i Niezawodnosc – Maintenance and Reliability, vol. 18, nr 1, pp. 32–37, 2016. - M. Kacprzak, P. Kulinowski, D. Wedrychowicz,
Computerized information system used for management of mining belt conveyors operation
, Eksploatacja i Niezawodnosc – Maintenance and Reliability, 2/2011 s 81–93. 2011. - M. Bajda, R. Blazej, L. Jurdziak, A. Kirjanow,
Condition monitoring of textile belts in the light of research results of their resistance to punctures investigations
. 16th International Multidiscyplinary Scientific Geoconference (SGEM 2016): Albena, Bulgaria, 30 June – 6 July, 2016, vol. 2,Exploration and mining, mineral processing, 2016. art. pp. 165–172, 2016. - P. Kulinowski,
Simulation studies as the part of an integrated design process dealing with belt conveyor operation
, Eksploatacja i Niezawodnosc – Maintenance and Reliability 2013, vol. 15 nr.1 s. 83–88. 2013. - M. Bajda, R. Blazej, M. Hardygora,
Impact of selected parameters on the fatigue strength of splices on multiply textile conveyor belts
, World Multidisciplinary Earth Sciences Symposium (WMESS 2016): 5–9 September 2016, Prague, Czech Republic. IOP Publishing, 2016. art. 052021, pp. 1–6. 2016. - R. Krol, W. Kisielewski, D. Kaszuba, L. Gladysiewicz,
Laboratory tests of idlers rotational resistance – selected issues
. Procedia: Earth and Planetary Science 2015, vol. 15, s. 712–719, World Multidisciplinary Earth Sciences Symposium, WMESS. 2015. - R. Krol, W. Kisielewski, D. Kaszuba, L. Gladysiewicz,
Testing belt conveyor resistance to motion in underground mine conditions
. International Journal of Mining Reclamation and Environment. 2017, vol. 31, pp. 78–90, 2017. - M. Bajda, R. Krol,
Experimental tests of selected constituents of movement resistance of the belt conveyors used in the underground mining
. Procedia: Earth and Planetary Science 2015, vol. 15, s. 702–711, World Multidisciplinary Earth Sciences Symposium, 2015. - W. Kawalec, P. Kulinowski, Computations of belt conveyors. Transport Przemyslowy 1(27), 2007 (in Polish)