Распределенная система многоуровневого управления подсистемой транспорта угольной шахты
Авторы: Р. В. Федюн, Н. В. Жукова, В. А. Попов
Источник: Научные труды ДонНТУ. Серия: Вычислительная техника и автоматизация, Выпуск 90. – Донецк, ДонНТУ, 2005. – С. 43 – 48.
Аннотация
В статье рассмотрены вопросы построения многоуровневой системы управления конвейерного транспорта. Подсистема конвейерного транспорта представляет собой многомерный и многопараметрический объект управления. Предложено разделение системы управления на три уровня. Разработана блок-схема системы управления.
Общая постановка проблемы. Ограниченность запасов нефти и газа в Украине при одновременном увеличении стоимости импортного сырья и возрастании потребления энергии определяют необходимость развития угольной промышленности, основной производственной единицей которой является шахта.
Современная угольная шахта представляет собой сложный объект автоматизации, который характеризуется распределенностью в пространстве, многомерностью, многосвязностью, наличием большого количества различных технологических процессов и оборудования, кроме того, на работу подземной части шахты оказывает большое влияние наличие газа, пыли, обводненность, меняющиеся случайным образом горно-геологические условия [1]. Производительность угольной шахты определяется суммарной производительностью добычных участков и может ограничиваться системой транспорта. В настоящее время на большинстве угольных шахт Украины применяется конвейерный транспорт. Каждая шахта имеет разветвленную, протяженную структуру конвейерного транспорта, включающую в себя большое количество различных конвейеров и бункеров. Построение комплексной системы автоматизации конвейерного транспорта позволит повысить эффективность функционирования данного технологического процесса.
Системы автоматического управления такими сложными объектами могут быть одноуровневыми централизованными, одноуровневыми децентрализованными или многоуровневыми. В настоящее время для получения максимальной эффективности управления объектами такого класса применяются многоуровневые системы автоматического управления, основанные на применении современных цифровых технологий. Использование многоуровневых систем управления позволяет наиболее полно учесть взаимосвязанность технологических процессов, их многомерность, распределенность, а также максимально компенсировать влияние внешних и внутренних возмущающих воздействий. Поэтому, необходимо разработать принципы и систему комплексной автоматизации системы конвейерного транспорта угольной шахты с использованием многоуровневого подхода и современных телекоммуникационных технологий.
Задачи исследования. Для построения комплексной системы автоматизированного управления конвейерным транспортом угольной шахты необходимо решить следующие основные задачи:
- выполнить анализ технологического процесса транспорта как объекта автоматизированного управления;
- определить наиболее оптимальное количество уровней управления данным технологическим процессом;
- определить с точки зрения иерархии системы управления задачи, решаемые на каждом уровне управления;
- разработать структуру комплексной системы управления конвейерным транспортом угольной шахты;
- обосновать выбор комплекса технических средств для реализации предложенной системы.
Решение поставленных задач и результаты исследований. Современные подземные конвейерные линии характеризуются значительной протяженностью и использованием мощных многодвигательных конвейеров для перевозки грузов и людей, а также наличием нескольких маршрутов. Это сложные объекты автоматизации, как с позиции управления ими, так и обеспечения безопасности их эксплуатации.
Объектом автоматизации выступает система конвейерного транспорта, которую можно условно разделить на три уровня. Нижним уровнем является конвейер. На большинстве шахт используют два типа конвейеров – ленточные и скребковые. Последние используются в добычных забоях и входят в состав механизированных комплексов. Участковый и магистральный транспорт осуществляется ленточными конвейерами [1, 2]. Объектом регулирования САУ нижнего уровня выступает ленточный конвейер, который может быть представлен тремя звеньями: электродвигателем конвейера ДК, вход которого – частота питающего напряжения fдв;, а выход – частота вращения вала двигателя ωдв; приводом конвейера ПК, вход которого – частота вращения вала двигателя ωдв;, а выход – скорость ленты на приводных барабанах vбп; тяговым органом ТО, вход которого – скорость ленты на приводных барабанах vбп; а выход – скорость ленты на натяжном барабане vбн (рис. 1.).
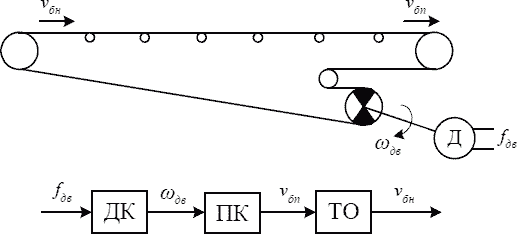
Рисунок 1 – Технологическая схема и функциональная блок-схема ленточного конвейера
В качестве приводного электродвигателя на ленточных конвейерах применяют асинхронные электродвигатели. Наиболее приемлемым способом управления асинхронным электродвигателем выступает изменение частоты питающего напряжения. Асинхронный электродвигатель с короткозамкнутым ротором при данном способе управления состоит из двух последовательно соединенных звеньев WЭЛ, WМ и описывается следующими передаточными функциями:
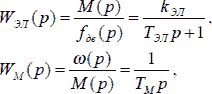
где М – момент на валу электродвигателя; ω – угловая скорость двигателя; fдв – частота управляющего напряжения; kЭД – коэффициент передачи электродвигателя; TЭЛ – постоянная времени электромагнитных процессов в электродвигателе; TМ – механическая постоянная времени.
Передаточная функция тягового органа ТО может быть представлена в следующем виде:

Значения параметров передаточной функции WТО(p) T1, T2 и τ зависят от типа конвейера, его длины, материала ленты. При прочих равных условиях перечисленные параметры для конвейеров с резинотканевой лентой на порядок больше, чем для конвейеров с резинотросовой лентой.
При автоматизации отдельных ленточных конвейеров возникает задача управления конвейером с многодвигательным приводом в переходных режимах работы. Данная задача успешно решается при использовании ПИД-закона управления, что подтверждается результатами моделирования (рис. 2).
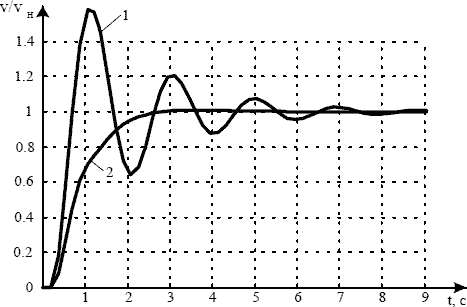
Рисунок 2 – Кривые переходного процесса в ленточном конвейере без регулятора (кривая 1) и с использованием ПИД-регулятора (кривая 2)
На рисунке приведены кривые переходных процессов по выходной величине – скорости тягового органа у натяжного барабана vбн в системе без регулятора (кривая 1), и при использовании ПИД-регулятора (кривая 2). Анализ данных кривых позволяет сделать вывод о значительном улучшении качества управления.
Второй уровень представляет собой неразветвленную конвейерную линию. Основная задача автоматизации данного уровня – обеспечение согласованной работы конвейеров линии в различных режимах.
Третий уровень – верхний уровень, к которому можно отнести всю систему конвейерного транспорта, включающую разветвленные конвейерные линии, а также бункера (рис. 3). На данном уровне система автоматизации должна обеспечивать оптимальное управление системой конвейерного транспорта с целью обеспечения заданной пропускной способности технологического процесса транспортирования при минимальных затратах.
Приведенная схема конвейерного транспорта угольной шахты (рис. 3) включает все вышерассмотренные элементы: отдельные ленточные конвейеры соединены в неразветвленные линии, которые при помощи бункеров образуют разветвленную схему транспорта. Все конвейерные линии делятся на участковые и магистральные, которые отличаются мощностью конвейеров, производительностью, протяженностью.
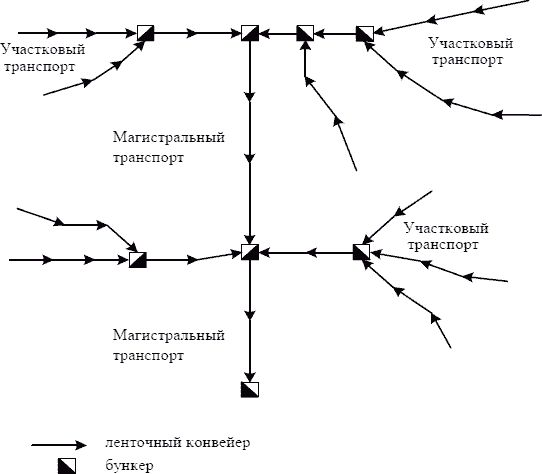
Рисунок 3 – Схема конвейерного транспорта угольной шахты
Многоуровневая структура системы управления обеспечивает ее надежность, оперативность, ремонтопригодность, эффективность функционирования. При этом обеспечивается оптимальный уровень децентрализации управления с минимальным количеством средств технологического контроля, управления и линий связи между ними. Построение систем автоматизации по уровням управления определяется целями (критериями) управления соответствующими элементами технологического процесса. Задачи, решаемые на каждом уровне объекта управления – системы конвейерного транспорта, определяют требования к многоуровневой системе автоматизации. На верхнем уровне решается задача обеспечения оптимальной работы всей системы конвейерного транспорта. В результате система управления верхнего уровня выдает оптимальные значения технологических параметров, которые являются задающими воздействиями для систем управления нижних уровней.
Вышеизложенный анализ особенностей системы конвейерного транспорта угольной шахты позволяет определить целесообразность деления систему управления на три уровня: нижний уровень – управление отдельным конвейером, промежуточный уровень – управление неразветвленной конвейерной линией, верхний уровень – управление системой конвейерного транспорта в целом. Структурная схема многоуровневой системы управления конвейерным транспортом угольной шахтой представлена на рисунке 4.
Функции управления отдельным конвейером, реализация ПИД-закона управления, а также все необходимые защиты и блокировки осуществляет блок управления локальным объектом (рис. 4) это нижний уровень системы управления. Для управления и координации работы неразветвленной конвейерной линии используется блок БУКЛ – промежуточный уровень системы. Оптимизация работы конвейерных линий и бункеров осуществляется на верхнем уровне, функции которого реализует ПЭВМ (рис. 4).
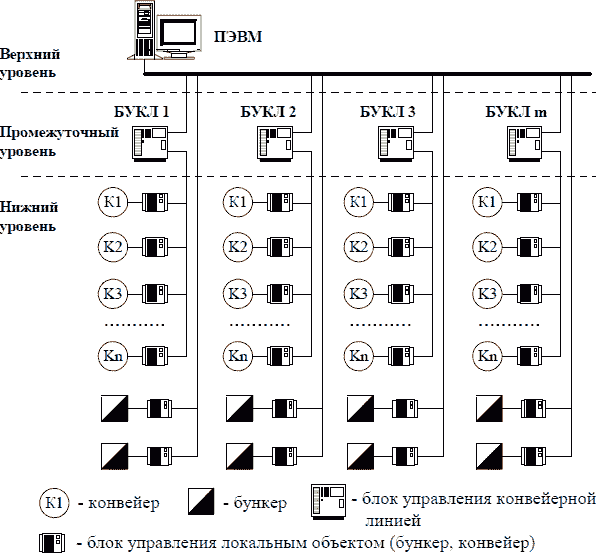
Рисунок 4 – Структура распределенной системы многоуровневого управления конвейерным транспортом угольной шахты
Дальнейшее совершенствование эксплуатации конвейеров, особенно в условиях расширения их использования, требует разработки систем, оптимизирующих режим их работы по критерию минимума затрат на транспортировку полезного ископаемого. В условиях неравномерности потока угля из забоев одним из путей решения этой задачи является построение САУ в целях стабилизации погонной нагрузки конвейеров как за счет регулирования скорости рабочего органа конвейера, как за счет регулирования скорости рабочего органа конвейера, так и использования промежуточной управляемой емкости (бункера, бункер-конвейера). САУ стабилизации погонной нагрузки конвейеров позволяет обеспечить полную загрузку конвейеров, особенно магистральных, исключить холостую работу конвейерных линий. Реализация данной функции осуществляется устройствами управления промежуточного и верхнего уровня.
При построении систем управления распределенными объектами используются два подхода. Классический подход к автоматизации сложных распределенных объектов предусматривает подключение каждого датчика к центральному контроллеру отдельным (и довольно дорогим) высококачественным кабелем. Это же относится и к подключению исполнительных органов. Альтернативой описанному подходу, являются системы автоматического управления, построенные с использованием промышленных шин – fieldbus. К наиболее известным и применяемым в мире открытым промышленным сетям относятся: CAN, LON, Profibus, Interbus-S, FIP, ControlNet, Foundation Fieldbus, DeviceNET, ASI, HART, MicroLAN, и некоторые другие [3, 5]. Каждая из перечисленных систем имеет свои особенности, достоинства и предназначена для применения на определенном уровне системы управления.
Переход на fieldbus-технологию обеспечивает улучшение качества, снижение затрат и повышение эффективности конечной системы [4]. Каждое устройство может выполнять функции управления, обслуживания и диагностики. Это существенно увеличивает эффективность системы в целом и снижает затраты по ее сопровождению. Таким образом, на современном этапе развития систем автоматизации при построении систем управления распределенными объектами и процессами необходимо ориентироваться на использование телекоммуникационных сетей класса fieldbus.
При построении многоуровневых систем автоматизации, особенно остро, стоят задачи организации информационного обмена между уровнями. В одном случае необходим обмен комплексными сообщениями на средних скоростях. В другом – быстрый обмен короткими сообщениями с использованием упрощенного протокола обмена (уровень датчиков и исполнительных механизмов). Для этих случаев наиболее подходит телекоммуникационная система Profibus [4, 5]. В настоящее время под этим общим названием понимается совокупность трех отдельных протоколов: Profibus-FMS, Profibus-DP и Profibus-PA. Протокол Profibus-DP был спроектирован для организации быстрого канала связи с уровнем датчиков и исполнительных механизмов. Протокол Profibus-FMS предназначен для работы на так называемом цеховом (верхнем) уровне. Здесь требуется высокая степень функциональности, и этот критерий важнее критерия скорости. FMS-протокол допускает гибридную архитектуру взаимодействия узлов. Протокол Profibus-PA – это расширение DP-протокола для организации обмена информацией во взрывоопасных средах. Как видно из рисунка 3, использование системы Profibus позволяет создавать системы управления на трех уровнях – уровне технологического оборудования, уровне процесса, уровне цеха.
Выводы.
1. Показано, что повышение эффективности управления конвейерным транспортом угольной шахты возможно при использовании комплексной системы автоматизированного управления, реализованной с использованием многоуровневого подхода построения систем.
2. Выполненный анализ условий функционирования системы конвейерного транспорта шахты показал, что наиболее целесообразным является построение трехуровневой системы управления, которая включает уровень конвейерного транспорта, уровень неразветвленной конвейерной линии, уровень отдельного конвейера.
3. Распределенная реализация многоуровневой системы управления конвейерным транспортом шахты возможна при использовании специализированных телекоммуникационных сетей, в частности, системы Profibus и Industrial Ethernet.
4. Система Profibus позволяет создавать системы управления во взрывоопасных и пожароопасных условиях, комплекс технических средств которой охватывает все три уровня управления: уровень конвейерного транспорта, уровень неразветвленной конвейерной линии, уровень отдельного конвейера и тем самым является наиболее предпочтительным при построении многоуровневой системы управления конвейерным транспортом угольной шахты.
Литература
- Автоматизация процессов подземных горных работ. // Под общей ред. Иванова А. А. – Киев; Донецк: Вища шк., 1987. – 327 с.
- Толпежников Л. И. Автоматическое управление процессами шахт и рудников: Учебное пособие для вузов. – 2-е изд., перераб. и доп. – М.: Недра, 1985. – 352 с.
- Звягинцев А. М., Красников А. Л., Курносов Н. М., Долинин И. В., Скрыпников С. Н. Полевые шины fieldbus – новая перспектива в автоматизации управления технологическими процессами // Датчики и системы. – 1999. – № 7–8. – С. 61–73.
- Олссон Г., Пиани Дж. Цифровые системы автоматизации и управления: СПб.: Невский диалект, 2001г. – 557 с.