Development and research of automatic control system for ventilation of dead-end mine workings
- Contents
- Introduction
- 1. Relevance of the topic
- 2. Purpose and objectives of the study
- 3. Analysis of the ventilation system of the technological process of ventilation of the preparatory mine workings as an object of automation
- 4. Critical review and analysis of existing automation systems for local ventilation fans
- 5. Development of an automatic ventilation control device for dead-end workings
- Conclusions
- References
Introduction
Due to the limited space and great depth in underground mine workings, there are difficult working conditions for miners. This leads to a deterioration in labor productivity, workers ' health, an increased risk of injuries and accidents, and limits the ability to conduct production processes.
Therefore, one of the most important links of the complex technological system of the mine is the process of ventilation of mine workings, the purpose of which is to maintain a normal atmosphere in the mine – providing the necessary inflow of fresh air, ensuring acceptable concentrations of methane in the mine atmosphere.
The main task of ventilation of dead-end workings is to supply a sufficient amount of air to the face, ensuring the speed of its movement, sufficient for effective ventilation of both the bottom-hole part and the entire development as a whole.
Currently used means of monitoring and controlling the ventilation process do not always provide reliable and effective protection, so the development of an automation system for a ventilation unit with a new device for automatic ventilation of the preparatory work is an urgent topic.
1 Relevance of the topic
The Problem of automation of airing of mines comes down to supply and distribution workings of such a quantity of air, which ensures the desired performance of the Stopes, the requirements of rules of safety and hygiene standards and maintained optimum modes of ventilation installations.
Features of underground mining technology put this task in a number of the most difficult problems of mining.
The difficulties of solving it are due to the following main reasons:
a) significant variability of the topology and parameters of the ventilation networks of mines, as well as the general interdependence of the processes of regulating the air flow through the workings;
b) the complexity and even inconsistency of the dynamic relationships between the input effect of the amount of air entering the face and the set of output parameters of this object to be regulated, the concentrations of methane, carbon dioxide, dust, etc.;
c) the stochastic nature of aerogasic processes and the presence of outliers in random functions of controlled parameters;
d) a large dispersion and a significant number of sensors used to monitor the parameters of the mine atmosphere, which move after the faces, which makes it difficult to obtain reliable and complete information;
e) the complexity of building an automatic fan control system while ensuring the specified high standards of their reliability.
2 Purpose and objectives of the study
The main objective of the design is to increase the efficiency of ventilation of the preparatory workings by developing an automation system for the ventilation unit with an automatic degassing device for the preparatory workings. Under the efficiency of ventilation of the preparatory workings of the mine, we mean timely provision of underground workers with air in sufficient quantities and ensuring high productivity of tunneling machines in safe conditions, which is achieved by stabilizing the methane gas fraction in the mine air at a safe level.
Requirements for the automation system of the ventilation system of the process of ventilation of the preparatory mine workings are as follows:
- Local, remote and automated control of the local ventilation fan in accordance with the algorithm of the installation operation in mine conditions;
- Automatic control of the supply of the local ventilation fan in the appropriate way for the accepted type of fan;
- Automatic degassing of mine workings when it is gassed;
- Automatic control and registration of the main parameters of the mine atmosphere in the preparatory work;
- Automatic protective shutdown of fan for local ventilation in violation of the conditions of its operation, in violation of equipment automation, in case of accidents in the power system installation and other occasions specific to the work situation of fan for local ventilation in coal mine conditions;
- Automatic blocking of the automation system in emergency situations;
- Automatic light and sound alarm in case of emergency situations. Generating warning messages about an airing emergency and failures in the automation system;
- Transfer of all controlled parameters to the dispatcher's personal computer, creation of a database;
- Visualization of the state of the ventilation process and the operation of the local ventilation fan;
- All technical means that are part of the local ventilation fan automation system must meet the conditions of spark and explosion protection.
3 Analysis of the ventilation system of the technological process of ventilation of the preparatory mine workings as an object of automation
In gas mines, the ventilation of dead-end workings is carried out by the injection method of ventilation using a ventilation unit, for example, a VM-6M fan. This method of ventilation in gas mines is mandatory and uniform. Its advantage is that the bottom-hole space is ventilated by a jet of fresh air, which exits the pipeline at a high speed. The technological scheme of the injection method for airing the preparatory workings with the help of a VMP fan is shown in Figure 3.1.
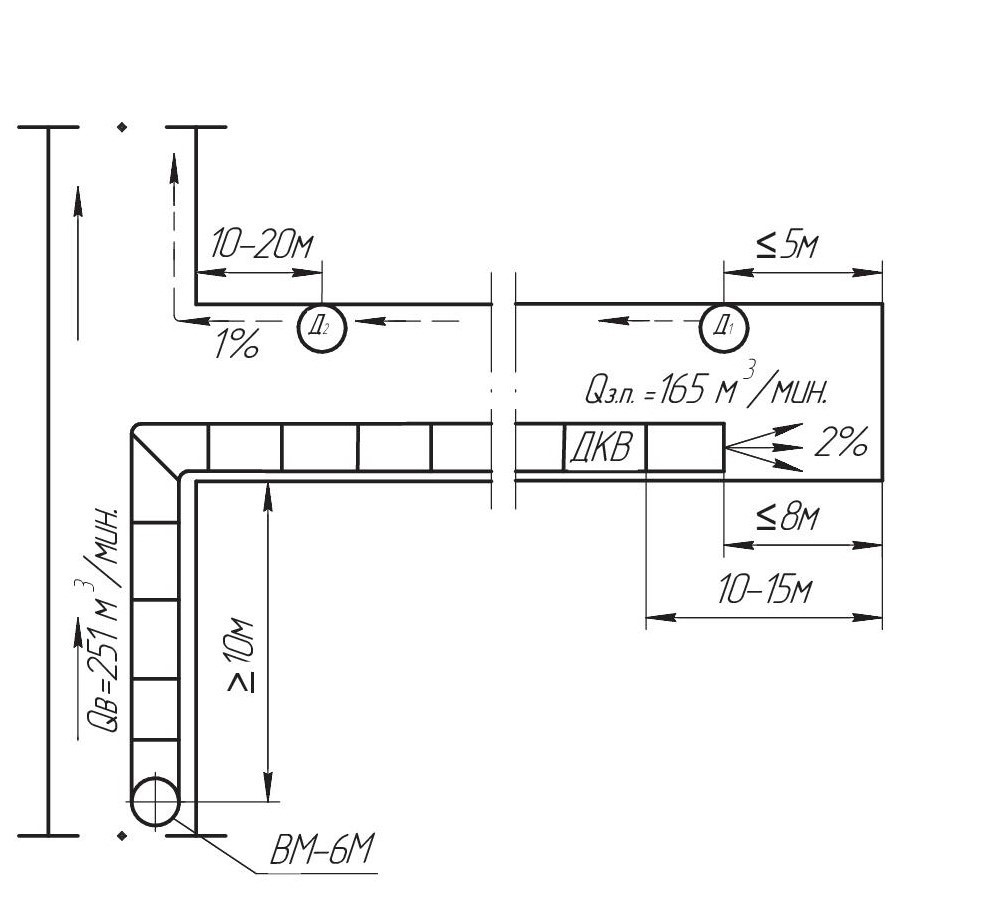
Figure 3.1 – Airing scheme of a dead-end mine
To prevent re-suction using PMF the air that comes out of the preparatory development (recirculation mode) and to prevent concentrations of methane (zagazirovanie) fan VMP is installed in the development, which ventilates the main unit of VGP, at least 10 meters from the mouth of preparatory development. The supply fan VMP should not exceed 70 % air flow in the development in the place of its installation that will provide podsazhivanie the output air flow from the preparatory development phase develop between the VMP and the mouth of preparatory development with the average air velocity not less than 0.15 m/s.
The supply of the VMP fan is calculated depending on the length of the mine, the projected methane release, the number of people who work in the mine, the minimum air velocity in the mine, the minimum air velocity in the bottom hole space, taking into account the temperature, the amount of gases that are formed during blasting operations in the mine face, and the amount of air leaks from the ventilation pipeline. Therefore, when changing these parameters, it is necessary to adjust the supply of the VMP fan accordingly.
4 Critical review and analysis of existing local ventilation fan automation systems
Currently, the following equipment is known for automation of the ventilation system for ventilation of preparatory workings:
– equipment for monitoring the ventilation of dead-end workings of the APTV type (development of OOO Prokopyevsk Electroapparat plant
, Prokopyevsk, Kemerovo region, Russia);
– equipment for airing dead-end workings of the AKTV type (development of WAT Chervoniy metallist
, M. Konotop, Sumy region);
APTV automatic ventilation control equipment performs automatic continuous monitoring of the amount of air entering the face of a dead-end mine through ventilation pipelines, ventilated by local ventilation fans (VMP). The equipment can be used in mines dangerous for gas and dust, and also serves for automatic protective power outage in case of violation of the normal ventilation mode.
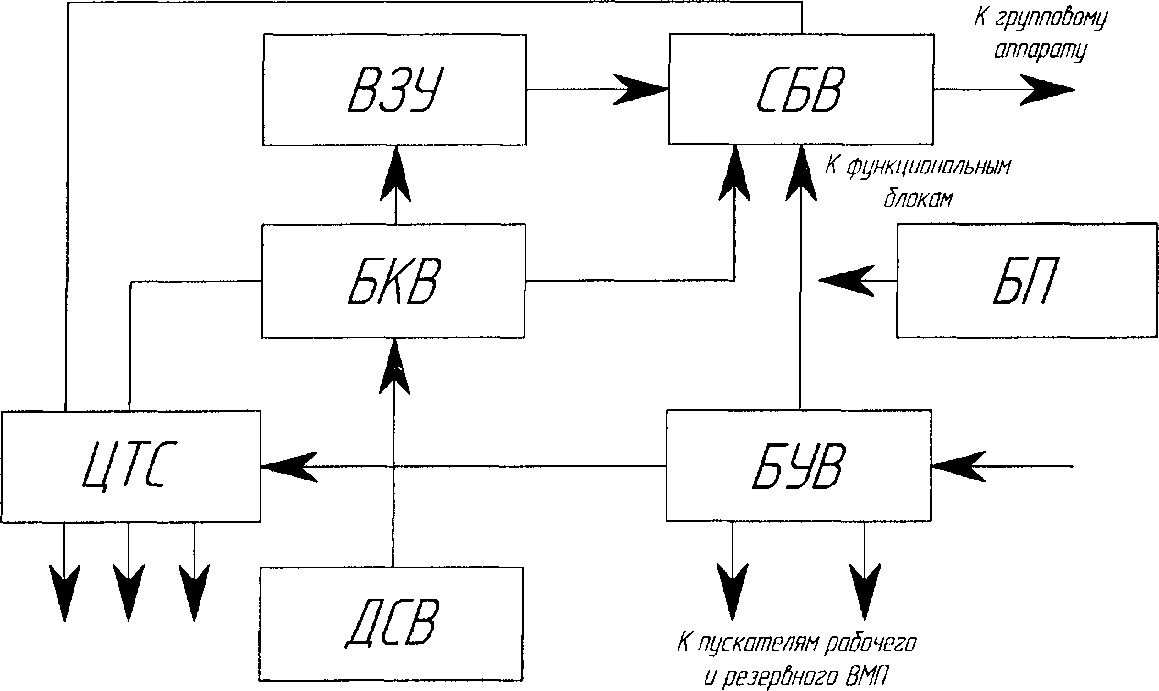
Electrical block diagram of APTV
Equipment for monitoring the ventilation of dead-end workings of the AKTV type is designed for automated local and remote control of VMP local ventilation fans, power off when deviating from the specified mode of ventilation of workings, issuing information to the dispatcher through the telemechanics system about the ventilation of the preparatory workings.
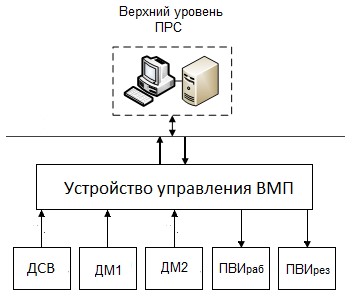
Figure 4.2 – Electrical block diagram of ACTV
5 Development of an automatic ventilation control device for a dead-end mine
To meet all the requirements, it will be advisable to propose the following two-level structure of the fan automation system for local ventilation of the technological process of ventilation of the preparatory mine workings (see Figure 5.1.)
Figure 5.1 indicates: UUVMP – device for controlling fans of local ventilation; PVI rab, PVIres – starters of the working and backup fan; DM1, DM2 – methane sensors in the bottom and mouth of the preparatory work; DSV – air flow rate sensor.
The scheme is implemented on the basis of two levels of control. The upper level (operator level) is represented by an industrial workstation. This is the control level of the local ventilation fan. This level performs the following functions: start and stop of the working and backup VMP; degassing of the preparatory work; archiving of data.
Industrial workstation (ORS) is an individual set of technical and software tools designed to automate the professional work of a specialist and provide preparation, editing, search and display on the screen and print the necessary documents and data. The automated workplace provides the operator with all the tools necessary to perform certain functions.
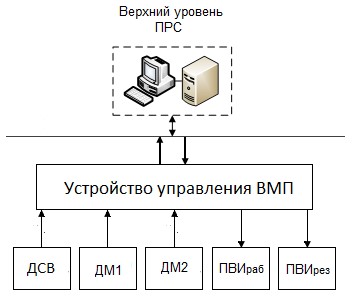
Figure 5.1 – Block diagram of the automation system of the technological process of ventilation of the preparatory mine workings
On the lower level there are sources of technological information-methane sensors for monitoring the methane content in the air, an air flow rate sensor, as well as actuators-starters of the working and backup fan.
To implement the effective operation of this system, a control algorithm was developed, which is shown in Fig.5.2.
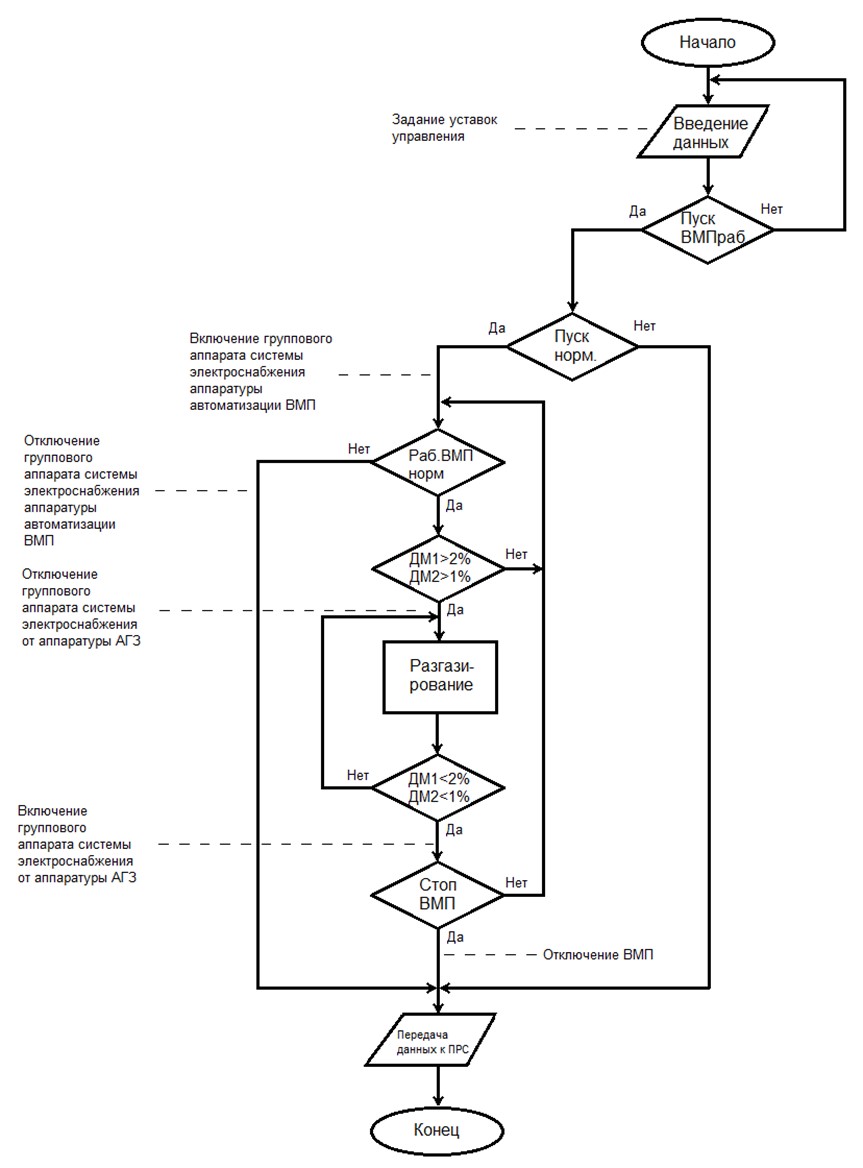
Figure 5.2 – Block diagram of the algorithm for automatic control of ventilation of the mine preparatory work
At the first stage of control, before the start of ventilation, the values of the control settings are determined and set in the corresponding devices of the automatic control system. When the command Start
is received, the VMP fan is started. The VMP fan turns on. When establishing a normal ventilation mode (Vtek.> Vust., where Vtek. – current air velocity in the ventilation pipeline), a command is formed to work out the time delay of 5-20 minutes. (set by the setpoint) to turn on the group apparatus of the power supply system for consumers of the preparatory production. After working out the set time delay of 5-20 minutes, if the airing mode is normal, a permit is formed to turn on the group apparatus of the power supply system for consumers of the preparatory production. Next, the ventilation mode of the preparatory workings of Vtek is controlled. > Vust.
In case of violation of ventilation (Vtek. & lt; Vust.) for a time of more than 30 – 120 s. (setpoint of the setpoint), a command is formed to turn off the group apparatus of the power supply system for consumers of the preparatory production. In case of failure or shutdown of the working VMP fan, a command is formed to automatically switch on the backup VMP fan in constant operation. During normal operation of the VMP fan, the current values of methane concentration in the bottom and mouth of the mine are monitored. If the set values of methane concentration are exceeded (the production is gassed), a command is formed to turn off the group apparatus of the power supply system for consumers of the preparatory production. Next, the degassing of the preparatory work begins. After degassing of the production, a permit is formed to turn on the group apparatus of the power supply system for consumers of the preparatory production.
When the VMP fan stop command is received, the fan stops.
For all ventilation modes, information should be generated about the operation of the VMP fan, the state of ventilation of the preparatory work, the concentration of methane, the possibility of applying voltage to the current collectors of the preparatory work, and the presence of voltage in the backup power supply network.
Conclusions
The technological process of airing a dead-end mine as an object of automation was analyzed and the requirements for the control system were formed. Its trouble-free operation requires constant monitoring of parameters such as methane concentration and air flow rate. As a result, a computer-integrated microprocessor control system for the process of ventilation of a dead-end mine was developed. Its algorithm allows for automatic continuous monitoring of the amount of air entering the face of a dead-end mine, and automatically turn off electricity when the normal ventilation mode is violated with the implementation of degassing of the mine if necessary.
References
- Братченко, Б.Ф. Стационарные установки шахт/ Под общей ред. Б.Ф.Братченко. –М.: Недра, 1977. – 440с.
- Бабак, Г.А. Шахтные вентиляторные установки главного проветривания/ К.П. Бочаров, А.Т. Волохов. –М.:Недра,1982. – 295с.
- Богопольский, Б.Х. Автоматизация шахтных вентиляторных установок/ М.А. Левин, и др. Изд. 2–е, перераб. и доп. М.: Недра, 1976. – 232с.
- Волотковский, С.А Электрификация стационарных установок шахт/ С.А Волотковский, Д.К. Крюков., Разумный Ю.Т. Справочное пособие/ Под.общей ред. Г.Г. Пивняка –М.: Недра,1990 – 390с.
- Батицкий, В.А. Автоматизация производственных процессов и АСУ ТП в горной промышленности: учебник [для студентов вузов]./ Батицкий В.А., Куроедов В.И. Рыжков А.А. –М.: Недра, 1991. – 303с.
- Пучков, Л.А. Методы и алгоритмы автоматического управления проветриванием/ Л.А. Пучков, Л.А. Бахвалов – М.: Радио и связь,1992. – 228.
- Бедняк, Г.И. Автоматизация производства на угольных шахтах/ Г.И. Бедняк, В.А., Ульшин, В.П. Довженко и др. – К.: Техника, 1989. – 272с.
- Толпежников, Л.И. Автоматическое управление процессами шахт и рудников/ Л. И. Толпежников. – Москва: Недра, 1985. – 352 с.