Abstract on the topic of graduation work
Content
- Introduction
- 1. Recycling of scrap and waste on an aluminum basis
- 2. Preparation of scrap and waste aluminum for metallurgical processing
- 3. Theoretical foundations of smelting aluminum scrap and waste
- 4. Casting and processing of alloys
- List of sources
Introduction
Aluminum (Al) is a chemical element of the third group of the periodic system of D.I.Mendeleev. Atomic number 13, atomic mass 26.9815. It's silvery white metal, lightweight, low-melting, ductile, easily drawn into wire and foil. The electrical conductivity of aluminum is quite high and is second only to silver (Ag) and copper (Cu) (2.3 times less than copper), belongs to the group of light metals. In nature, there is one stable isotope, 29Al[1].
The density of aluminum is 2699.9 kg/m3 at a temperature of 20 °C, the melting point is 660 °C, and the boiling point is 2452 °C. Aluminum has a cubic face-centered crystal lattice and does not have allotropic transformations. Among metals, aluminum ranks first in terms of prevalence in nature, for practical use - the second (after iron). Clarke of aluminum is 8.05, which is about 15% in terms of Àl2Î3. Aluminum is almost everywhere on the globe, since its oxide (Àl2Î3) is the basis of alumina. For comparison, the iron content in the earth's crust is 4.65%, that is, two times less. In a metallic form, aluminum was first obtained by H.K. Ersted in 1825[1].
1. Recycling of scrap and waste on an aluminum basis
The main raw material for the production of aluminum is alumina - powdered aluminum oxide, consisting of two varieties (modifications) oxides: Àl2Î3 (alpha-alumina) and Àl2Î3 (gamma-alumina). Alpha alumina - the most stable form, occurs naturally as mineral corundum. It has a strong structure, great hardness and chemical resistance: the melting point of corundum is 20...54 °C. Gamma alumina is obtained by dehydration of aluminum hydroxide, it interacts well with solutions of alkalis and acids, has a high hygroscopicity. Even heated to 1000 °C, gamma alumina contains about 1% water, and only a long exposure at 1200 °C completely dehydrates and gamma-alumina turns into corundum. The global aluminum industry includes bauxite mining, production alumina, primary and secondary aluminum, is characterized by a high level of concentration and vertical integration of production. Gain the process of concentration in the global aluminum industry reflects the current state of the world market. This is mainly due to significant growth of aluminum exports from Russia after the collapse of the USSR. Today, Russia accounts for about 20% of world metal exports. For the period 2003-2005. demand for aluminum was very strong. A significant increase in demand for aluminum is mainly due to its use, it is constantly expanding, in the aviation and automotive industry, in the manufacture of packaging materials in the food industry. If in 1992 in Europe for one passenger car the consumption aluminum averaged 72 kg, in Japan - 160 kg, then in 2006 this figure increased to 192 kg and 288 kg, respectively. Average annual consumption growth rate are estimated at 13%, and the actual indicators may differ from the forecast rates by about 200 thousand tons[1].
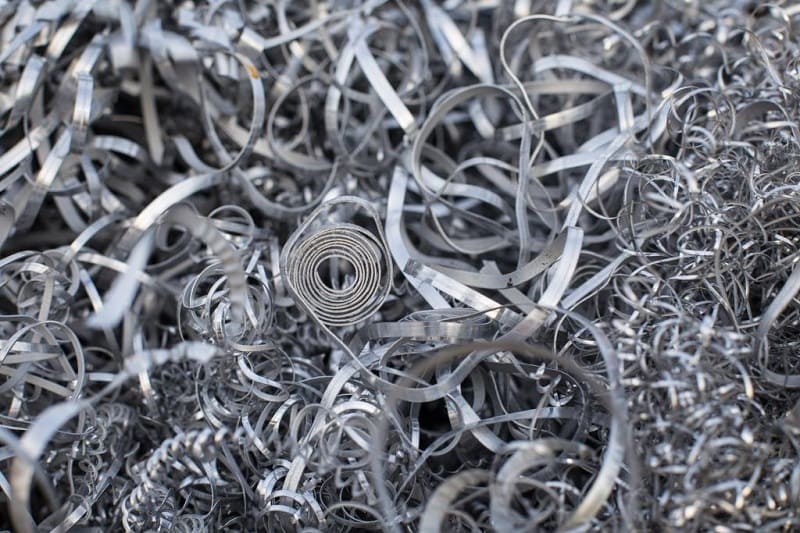
Ðèñóíîê 1 – Aluminum shavings
Aluminum alloys have a low density (2500...3000 kg/m3) combined with very good mechanical properties and satisfactory oxidation stability. Particularly distinguished are aluminum alloys with increased ductility, containing up to 2.8% Mg and up to 2.5% Mn - they have greater strength than pure aluminum, are easy to draw, are close in corrosion resistance to pure aluminum.
Aluminum is one of the most common alloying additives in titanium, magnesium, copper, and zinc alloys. Aluminum is also widely used to obtain various chemical compounds. Thus, aluminum braid [K2SO4%Al2(SO)4%] is used as a mordant for dyeing fabrics and for tanning leather, aluminum oxide (A12O3) - as an abrasive material, adsorbent and catalyst, in the production of refractory materials. In aluminum-based alloys, copper, magnesium, zinc, silicon, manganese, lithium, cadmium, zirconium, chromium and other elements are used as an additive. Aluminum alloys are divided into: those that are deformed - are used for the manufacture of sheets, bars, profiles, forgings by rolling, pressing, forging; foundries - designed for casting; sintered, foamed, and the like. Wrought aluminum alloys make up about 80% of the production volume. The most popular among them are duralumin (Al-Cu-Mg-Mn system) - heat-strengthened alloys widely used in transport and aircraft engineering.
Duralumin - from the French word dur-hard, heavy and aluminum solid aluminum. Duralumin-alloys based on aluminum, contain: 1.4...13% Cu; 0.4...2.8% Mg; 0.2...1.0% Mn; sometimes 0.5...6.0% Si; 5...7% Zn; 0.8...1.8% Fe; 0.02...0.35% Ti, etc. Duralumin are the strongest and least corrosion-resistant of aluminum alloys, subject to intercrystalline corrosion. To protect sheet duralumin from corrosion, its surface is clad with pure aluminum. They are not characterized by good weldability, but due to the rest of their characteristics, they are used wherever strength and lightness are needed. They have found the greatest application in aircraft construction for the manufacture of parts for turbojet engines. Magnalia% named so because of the high content of magnesium (Mg) in them, alloys based on aluminum, containing: 5...13% Mg; 0.2...1.6% Mn; sometimes 3.5...4.5% Zn; 1.75...2.25% Ni; up to 0.15% Be; up to 0.2% Ti; up to 0.2% Zr, etc.
Among casting alloys, the most common are silumins (Al and up to 23% Si-Cu-Mn-Mg). They have relatively high mechanical properties combined with corrosion resistance in humid and marine atmospheres; are used for the manufacture of parts of complex configuration in auto, aircraft and shipbuilding. In addition to silumins, cast aluminum alloys based on Al-Cu systems are used; Al-Cu-Si; Al-Mg% magnalia containing 4...13% magnesium.
Thermal reinforcing alloys also include aircrafts (AlMg-Si-Cu-Mn or Mx), high-strength (Al-Cu-Mg-Zn), heat-resistant (AlMg-Ni-Si) and forging (Al-Cu-Mg-Mn) alloys. Alloys of aluminum with manganese (AMts) and with magnesium - magnalia (Al% 1...7% Mg) are thermally non-reinforcing alloys. They are characterized by medium strength, good ductility and weldability, high corrosion resistance; used in shipbuilding and aircraft construction, in the production of welded tanks, refrigerators, and so on. Magnalia is highly durable and resistant to corrosion in fresh and even seawater. Magnalia is also well resistant to nitric acid HNO3, dilute sulfuric acid H2SO4, orthophosphoric acid H3PO4, as well as in environments containing SO2. They are used as a structural material in aircraft construction, shipbuilding, automobile construction (welded tanks, rivets, gas lines, oil drives), for the manufacture of fittings for building structures, for the manufacture of parts of refrigeration units, for the manufacture of decorative household items, and the like. With a Mg content above 6%, magnalia is susceptible to intergranular corrosion, and has lower casting properties than silumins.
Silumins alloys based on aluminum with a high silicon content (Si). The composition of silumins includes,%: 3...26% Si, 1...4% Cu, 0.2...1.3% Mg, 0.2...0.9% Mn, sometimes 2...4% Zn, 0.8...2.0% Ni, 0.1...0.4% Cr, 0.05...0.3% Ti, etc. With their low strength, silumins have the best casting properties of all aluminum alloys. They are most often used where thin-walled or complex-shaped parts need to be made. In terms of corrosion resistance, they occupy an intermediate position between duralumin and magnalia. Found their main application in aircraft construction, car building, automotive and agricultural machinery construction for the manufacture of crankcases, wheel parts, casings and instrument parts.
Foam aluminum is a relatively new class of ultra-light (100...900 kg/m3) metallic materials, consisting of a large (60...98%) amount of mostly closed elements filled with gas. Foam aluminum has a high ability to damp acoustic and electromagnetic waves, and is also an ideal material for energy absorbers[2].
2. Preparation of scrap and waste aluminum for metallurgical processing
One of the main issues in the reuse of non-ferrous metal waste is the primary preparation of raw materials before metallurgical processing. Primary preparation of scrap and waste of non-ferrous metals includes the following technological processes:
- sorting of raw materials by physical condition, dimensions, name of metals (alloys), removal of ferrous metals and non-metallic materials, by contamination, as well as by other signs;
- fragmentation and fragmentation;
- classification and different types of separation.
Rational primary preparation of secondary non-ferrous metals allows increasing all the main technical and economic indicators of the subsequent metallurgical processing; increase the pulling of non-ferrous metals; to reduce fuel and energy costs for remelting, to reduce the consumption of primary metals, to reduce the melting time, to exclude refining processes. There is nothing more expensive than a cheap metallurgical charge.
In unused types of waste, the return rate of non-ferrous metals in consumer waste is about 50%, in production waste - about 85%, and the overall return rate of non-ferrous metals is 65...70%. Consequently, one third of the consumed non-ferrous metals is not returned to the national economic circulation, but is practically irretrievably lost. Large losses of aluminum with cable waste of consumption. The cable is practically not pulled out in mine workings, from trenches and routes. Aluminum is lost with waste of consumption of ferrous metals in decommissioned machines and mechanisms, in particular in waste of household appliances: refrigerators, washing machines, sewing machines and the like. The development of new technological processes and equipment for the enrichment of scrap and waste of non-ferrous metals is a very urgent national economic task.
Metal obtained from ore or waste, after all, has no chemical and physical differences. However, the energy costs in obtaining metal from ore are much higher (sometimes by an order of magnitude) than when obtaining metal from waste. In the case of open-pit mining, the necessary stripping work, and in the case of underground mining, the construction of mines (mines). And since in most cases non-ferrous metal ores are characterized by a low content of the base metal, it is necessary to build concentration plants. The reserves of natural ores are irreplaceable, the deposits close to the surface of the earth are becoming less and less, therefore the extraction and processing of ores is becoming more and more expensive, which leads to an increase in prices for non-ferrous metals. A significant share of the rise in the cost of production of non-ferrous metals is also due to the need to build environmental structures as well as payments for land occupied by production wastes.
In this regard, the production of non-ferrous metals from production and consumption wastes has long been the second method quite competitive and effective. There is a constant increase in the share of non-ferrous metals from secondary raw materials. So, in industrially developed countries the increase in the production of non-ferrous metals in the 90s of the last century was,%: aluminum - 16 (from secondary raw materials - 13); copper - 6 (from secondary raw materials - 30); lead - 8 (from secondary raw materials - 15); zinc - 9 (from secondary raw materials - 8). Of the aforementioned volume of consumption of aluminum 50 million tons/year, while 26...28 million tons were obtained from primary raw materials, and 22...24 million tons from secondary.
For Ukraine, the way of obtaining non-ferrous metals from scrap and waste of their production became extremely relevant after 1991. This is due to the fact that in Ukraine there is no industrial extraction of ores of aluminum, copper, zinc, lead and a number of other non-ferrous metals. In addition, there are no proven reserves of bauxite for the production of aluminum. And the processing of small reserves of nepheline ores requires the use of new technologies. Species sorting. Sorting should start from the moment the scrap is unloaded. The main part of non-crumbling lump waste based on aluminum is subjected to manual sorting on sorting conveyors and tables. Scrap, sorted by species during unloading, is collected separately and subjected to further processing, depending on its individual characteristics.
Distinctive features of this type of sorting are: color, density, hardness, fracture nature, magnetic properties, product shape. Since the metal surface often has protective coatings (paint, anodizing, varnishing, etc.), the color of the metal should be determined after a cut or break in the metal. Scrap of cast alloys is sorted according to casting characteristics: casting tides, stiffeners, traces of demountable lines, product configuration complexity. Marking. The grade of the alloy is determined with markings made in the form of cast numbers or painted on parts and blanks in accordance with GOST 2171-90.
Drip method. The method is based on the reaction between alloy elements and reagents applied in the form of drops. In this case, a spot or sediment with a certain color is formed, indicating the presence of one or another component in the alloy. To separate aluminum alloys from magnesium and zinc alloys, a reagent is used: CdSO4+NaCl+HCl. On aluminum alloys, after applying a drop of the specified solution, surface coloring does not occur, but on magnesium and zinc alloys% a black color appears. The main disadvantages of manual sorting of scrap and waste of non-ferrous metals are significant labor intensity, low productivity of the process, the impossibility of sorting by visual signs of similar in composition groups of alloys. The greatest difficulty is high-quality sorting of small pieces of scrap and waste less than 100 mm in size, the amount of which in the raw material reaches 50...55%. The main guarantee of high-quality, reliable waste sorting is the high qualification and experience of the sorter, as well as the maximum use of different devices and special tools and devices[2].
3. Theoretical foundations of smelting aluminum scrap and waste
The main purpose of smelting is to obtain alloys that meet the requirements of standards in terms of chemical composition, physicochemical and mechanical properties. Modern smelting technology ensures minimal heat and metal losses with optimal energy and labor costs. Melting is carried out in furnaces at atmospheric pressure. Heating, melting, overheating are accompanied by accompanying metallurgical processes: oxidation of aluminum and alloying elements, gas contamination of melts, dissolution, evaporation of components, interaction of liquid metal with fluxes and furnace lining. Some of the listed processes are necessary and useful, others are undesirable, negatively affecting the quality of the alloys obtained.
The mutual arrangement of atoms in the crystal lattice of a solid metal is absolutely the same in all three dimensions. This constancy of the arrangement of atoms in crystalline substances is called long-range order. When melted, the vibration amplitude of each atom of the crystal lattice increases significantly, the atoms acquire the ability to translate. As a result, long-range order is violated. The arrangement of atoms in a molten metal strongly overheated from the melting point, which is characteristic of the crystalline state, is retained only in microvolumes of the melt. These areas are called "clusters". The arrangement of atoms in these volumes is called short-range order. With a further increase in temperature, the remnants of the crystal-like structure are completely destroyed. The short-range order disappears and the melt passes into a structureless state.
Some properties of metallic melts. In production conditions, in most cases, they work not with pure aluminum, but with aluminum alloys, crystallizing in a certain temperature range. When melting secondary raw materials, consisting of various grades of aluminum alloys, processes occur that are determined by the thermophysical and physicochemical properties of aluminum. These are the heat of fusion, melting point and specific heat capacity, which determine the amount of heat required to melt a given metal. Aluminum has a relatively high heat of fusion, equal to 385.2 J/g, and higher than many other metals, the heat capacity, which at the melting point is 1.143 J/(g). The values of the specific heat for most metals in the liquid state are calculated by the formula: C = 7.15/A, J/(kg × Deg). The specific heat capacity of some metals is given in table. 6.5. Alloying components slightly change the above-mentioned characteristics in comparison with pure aluminum, therefore their presence in the alloy is not taken into account when choosing the design and power of the melting furnace, to determine its productivity, heating mode, permissible overheating of the alloy. These characteristics are very different from those for other pure metals.
The high heat capacity of aluminum and aluminum alloys provides certain technological advantages. For example, technologists do not have to worry too much about the casting speed of a 6 or 10 t ladle mold. The metal in the ladle is stored in a liquid state for 1...2 hours. But for some other technological processes where it is required to provide an increased cooling rate, this property of aluminum alloys creates certain production difficulties. The dependence of the temperature of liquid aluminum on the duration of standing in ladles with a capacity of 3 tons and the temperature of the ambient air are given in table. 6.6. In the continuous mode of casting metal from the furnace, the average proofing time is determined by the capacity of the furnace.
For the melting of aluminum-containing scrap and waste, furnaces of various designs are used: flame chops, rotating shaft, rotating rotary, electric induction, as well as combinations of these types. The choice of the furnace is due to the technical and economic feasibility of melting a certain type of raw material. For example, induction or rotary crucible furnaces are suitable for smelting clean waste (die-cutting, shavings) and scrap without iron burn-in. Fiery chop furnaces are adapted for smelting bulky scrap with iron burn-in. When choosing furnaces, the capacity of the furnace is of great importance, which must correspond to the volume of production, which guarantees the uninterrupted operation of the unit, as well as heating methods. Particular attention is paid to the cost of energy sources in the area of construction of a workshop (plant).
Secondary raw materials in many cases contain a high percentage of contamination, which includes oxides, non-metallic materials, objects from other metals mechanically connected to aluminum (cast iron, steel, titanium, etc.). The methods used for preparing the charge before melting do not provide complete purification of raw materials from impurities. For such raw materials, furnaces are used, the designs of which make it possible to simply, economically, effectively separate these impurities from aluminum during the melting period. The cost and payback period of the installed melting units are of great importance. And, finally, the amount of damage to the environment caused to one degree or another by the operation of the furnaces is taken into account. Factories located within the boundaries of large settlements should mainly be equipped with electric ovens. Fire chop ovens should be installed subject to effective gas cleaning. When choosing a melting unit, in addition to the specified characteristics, the thermal efficiency of the furnace is taken into account.
After preliminary preparation, scrap and waste of aluminum is processed in smelting units. By the heating method, melting units can be divided into two main groups: fuel and electric. Does the first group include stoves heated with gas or liquid fuel, and the second% are heated by electricity. Approximately 2/3 of the volume of aluminum alloys is carried out in fiery reflective furnaces, which are similar in design and principle of operation to open-hearth furnaces.
Fiery oven chops. The most widespread are universal fiery chop furnaces, in which any raw material is melted: shavings, sawn-off sawdust, aircraft and lump scrap with iron running-in, and the like. They have high performance and are easy to maintain. The metal charge of reflective furnaces for melting secondary aluminum raw materials is diverse and consists of cuttings, scrap and waste of foundry and deformed alloys, briquettes, shavings, slag and waste of own production, dry crushed shavings, preparatory alloys, etc. The use of one or another type of metal charge in smelting depends on the furnace unit, the specified alloy grade.
Metallic silicon, copper, zinc and primary aluminum are used to bring the molten charge of a given alloy composition. In order to save primary materials, some of them are sometimes replaced with scrap or waste of a known composition. To obtain high quality alloys, the initial metal raw material must undergo a certain preparation before forming the charge, which is the most important stage in the processing of secondary raw materials. The tasks of preparing raw materials for reflective melting include sorting by types and groups of alloy grades, enrichment and removal of harmful impurities (moisture, non-metallic inclusions, iron-containing running-in, etc.), increasing the bulk weight and reducing the size of the pieces to convenient for loading conditions when cutting, crushing or pressing and briquetting. Grinding raw materials facilitates the separation of other materials as well as parts from various aluminum alloys[3].
4. Casting and processing of alloys
At most enterprises of secondary non-ferrous metallurgy, metal is cast into molds of a conveyor-type casting machine to obtain ingots weighing up to 15 kg. In cases where secondary alloys are close in chemical composition or correspond to alloys that are prepared from primary metal, they are cast not only into ingots, but also into a billet of round or rectangular solid or hollow sections.
Round ingots are used to produce profiles, rods, forgings and stampings, pipes and wires. For the outer diameter, the assortment of cast ingots is conventionally divided into four groups: up to 200; 200...400; 400...800 and more than 800mm. They strive to bring the length of cast ingots to the maximum possible in order to increase the yield. Flat ingots-slabs are used mainly for rolling sheets. Slab thickness is usually 200...400 mm and width 900...2100 mm. For the deoxidation of steel, aluminum alloys are used, which are poured into granules. In this case, a stream of liquid aluminum is directed into water, and then the granules are dried and sent to consumers. It is possible to obtain granules by spraying liquid metal with air or inert gas. Aluminum ingots weighing up to 15 kg are produced on technological lines consisting of a mixer (furnace), a device for filtration and non-oxidative casting of metal into molds of a casting conveyor, an installation for cooling ingots, a pig-laying machine and a bag strapping section.
Ingots of various sections (hollow and solid round, rectangular) are cast by the method on the floor of continuous or continuous casting, the essence of which is the continuous supply of liquid metal to a special water-cooled crystallizer. When casting round and flat ingots, molds of various designs are widely used, consisting of a cooler body and a mold sleeve, made of aluminum alloys. Casting ingots into electromagnetic crystallizers is also used. Casting with the formation of an ingot by an electromagnetic field completely eliminates mechanical interaction between the ingot and the mold, which ensures a high surface quality. The combined processes of continuous casting and rolling of metals are becoming more widespread in the world. Work in this direction was started in the 30s of the last century in the USA and the USSR both for non-ferrous metals and their alloys[3].
List of sources
- Bredikhin V.N., Shevelev A.I. Modern technologies for the processing of non-ferrous metal waste. -M .: TsNIIEITsM, V.1; 1991.
- Fetisov M.F., Kushnerov V.Yu., Bredikhin V.N. and others. The modern method of controlling the basicity of the agglomerate, Sat. scientific. Proceedings of DonNTU, Metallurgy series, No. 1 (16) - 2 (17), 2013.
- Kolobov G.A., Bredikhin V.N., Chernobaev V.M. Collection and processing of secondary raw materials of non-ferrous metals -M .: Metallurgy, 1992.