Abstract on the topic of graduation work
Contents
- Introduction
- 1. Documentary examination
- 1.1 Materials and research methods
- 2. The main part of the work
- 2.1 Analysis of waste heat losses
- 2.2 Analysis of underburned heat loss
- 2.3 Analysis of heat losses to the environment
- 2.4 Total heat loss analysis
- Conclusions
Introduction
The main harmful substances that pollute the atmosphere as a result of fuel combustion are:
- volatile hydrocarbons (Cx Hy);
- carbon monoxide (CO);
- sulfur oxides (SOx);
- nitrogen oxides (NOx).
In general, the volume and composition of pollutants significantly depends on the type of fuel used, the quality of its combustion, design features of the boiler and burner.
Nitrogen oxides are the only pollutants that cannot be eliminated by changing the type of fuel, as they are most often formed when nitrogen and oxygen combine in the flue gases emitted into the atmosphere. The mechanism of their connection can be different. Under the term "nitric oxide", the NOx formula combines three substances:
NO (nitrogen monoxide);
NO2 (nitrogen dioxide);
N2O (nitrous oxide).
To be more precise, it is NOx that are those substances that prevail inside the boiler (95% or more), while a large amount of NO2 is formed only upon contact with low temperatures, i.e. when exhaust gases are released into the atmosphere. According to its origin, three different mechanisms of NOx formation can be identified.
NOx of thermal origin
These substances are formed from nitrogen present in the air, which is used for fuel combustion at a temperature of 1300 ° C. Their concentration is directly proportional to the flame temperature, the duration of the stay of the flue gases in the high temperature zone, and also depends on the partial pressure of oxygen in this zone.
Ready made NOx
Formed when molecular nitrogen present in the air combines with hydrocarbon fragments formed during the decomposition of fuel in the first stages of combustion. This process especially contributes to the formation of NO. The amount of pollutant emitted is directly proportional to the concentration of oxygen (i.e. its excess) and does not depend on the temperature.
NOx generated from fuel
These substances are formed by the reaction of organic nitrogen compounds contained in fuel with oxygen at a combustion temperature exceeding 1000 ° C. The formation of nitrogen oxides occurs during the combustion of liquid fuel and coal, but there is no methane during combustion, since the latter does not contain nitrogen.
Ways to reduce NOx
The formation of air pollutants (NOx) during fuel combustion depends, first of all, on the time of their stay in the high temperature zone, as well as on stoichiometry, i.e. excess oxygen.
The formed nitrogen oxides enter the atmosphere and combine with it in a rather complex chemical way (reacting with water vapor, as well as photochemically). The mechanism of this reaction has not yet been fully understood.
The number of compounds N 2 O is stable and remains in the atmosphere for many years. This substance, together with carbon dioxide CO 2 and other harmful emissions, contributes to the formation of the greenhouse effect.
By reaction with ozone O3, one nitric oxide NO is rapidly converted to dioxide NO2 and oxygen O2. Later, nitrogen dioxide NO2 is removed from the atmosphere. When oxidized, it transforms into nitrous acid HNO2, and then into nitric acid HNO3, which contributes to the formation of acid rain. It should be remembered that NO2 is a natural and permanent component of the atmosphere (albeit very insignificant). It is mainly formed during the oxidation of ammonia during microbiological reactions in organic substances present in the earth and in water.
The process of forming NOx substances strongly depends on:
- flame temperatures;
- the duration of the presence of combustion products in the high temperature zone;
- the partial pressure of oxygen and its concentration.
To reduce the formation of NOx substances it is necessary:
- lower flame temperature;
- to reduce heat intensity (kW/m3), i.e. set the boiler operating mode below the nominal;
- reduce the residence time of combustion products in the furnace;
- reduce oxygen concentration.
With the introduction of modern low NOx burners, it became possible to further reduce the amount of harmful substances by using:
- recirculation (afterburning) of flue gases, in which part of the flue gases and air used for fuel combustion is taken and, again sent to the furnace, is burned. Thus, the partial pressure of oxygen and the temperature of the flame are reduced;
- reducing the partial pressure of oxygen by reducing excess air.
Additional control over NOx emissions can be achieved by reducing the burner power within the limits of its technical specifications.
Materials from the site EnergoGaz.
1. Documentary examination
The documentary survey was carried out according to the data of the technical reports on the environmental and heat engineering tests of the TVG-8M hot water boilers
A total of 30 results of experimental measurements were analyzed when the boiler was operating in the load range from 2.8 to 7.38 Gcal/hour (from 3.26 to 8.61 MW). When the gas flow rate changes from 390 to 1046, 34 m3/hour.
Analyzed and determined the optimal thermal and environmental indicators and concentrations of harmful components of combustion products.
Objectives of documentary survey analysis:
- combustion products in the flue gases of boilers;
- heat losses and gross efficiency of boilers in the operating range of loads;
- specific fuel consumption;
- gross emissions of nitrogen and carbon oxides from the boiler house;
- minimum stable and maximum loads of boilers;
- gross efficiency of boilers in the operating load range.
and measures have been developed to improve the reliability, efficiency of boilers and proposals to reduce emissions of pollutants into the atmosphere.
1.1 Materials and research methods
Hot water boilers TVG-8M with a thermal capacity of 8.63 Gcal/h (10.044 MW) are used as the research material.
Figure 1 shows a diagram of the measuring points.
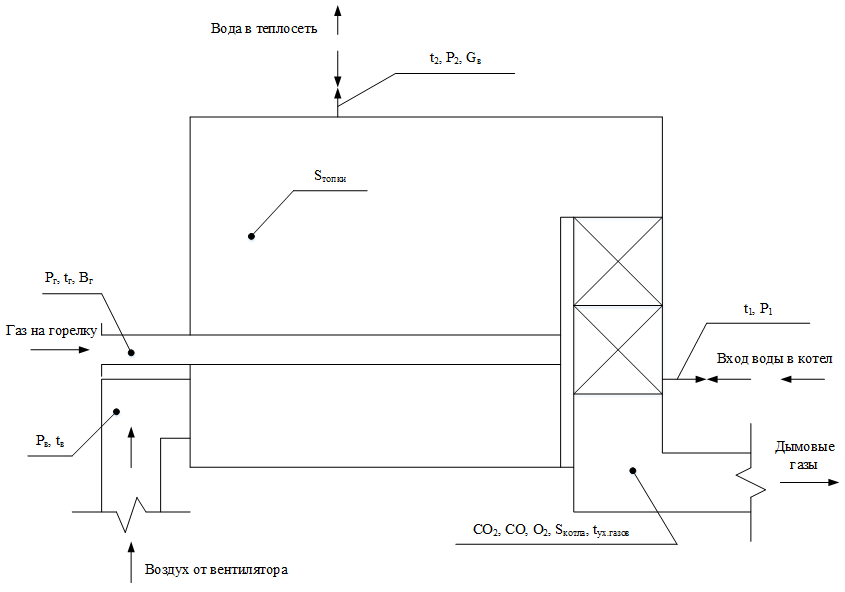
Figure 1 - Measuring points diagram
At a gas pressure on the burner of 1.96 kPa, the heating capacity varies from 2.860 to 3.011 Gcal/h (2 experiments). At a pressure of 2.943 kPa (6 experiments), the heat output changes from 3.47 to 4.58 Gcal/h. With an average value of 3.84 Gcal/hour. At a pressure of 4.905 kPa (7 experiments), the heat output varies from 3.368 to 5.756 Gcal/h. With an average of 4.843 Gcal/hour. At a pressure of 5.886 kPa (2 experiments), the heat output varies from 5.304 to 5.701 Gcal/h. With an average of 5.5 Gcal/hour. At a pressure of 6.867 kPa (2 experiments), the heating capacity varies from 6.206 to 6.477 Gcal/h. With an average of 6.34 Gcal/hour. At a pressure of 7.358 kPa (4 experiments), the heating capacity varies from 5.445 to 7.058 Gcal/h. With an average of 6,016 Gcal/hour. At a pressure of 7.848 kPa (3 experiments), the heat output varies from 6.24 to 7.288 Gcal/h. With an average of 6.687 Gcal/hour. At a pressure of 9.81 kPa (1 experiment), the heating capacity is 6.191 Gcal/hour. At a pressure of 10.791 kPa (1 experiment), the heating capacity is 7.384 Gcal/hour. At a pressure of 11.772 kPa (1 experiment), the heating capacity is 7.189 Gcal/hour.
With an increase in the flue gas temperature from 105 to 188 °C, the boiler efficiency changes from 89.33 to 92.12%.
The dependence of the flue gas temperature on the heating capacity is shown in Figure 2.
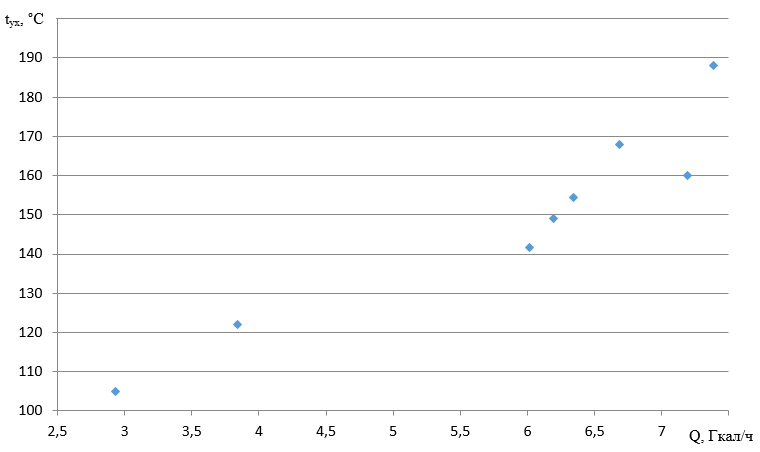
Figure 2 - Change in flue gas temperature from load
2. Most of the work
2.1 Analysis of waste heat losses
Three types of heat loss are considered in the work:
- with waste gases (q2),
- with chemical underburning (q 3),
- to the environment (q5).
When the boiler is operating in the load range from 2.936 to 7.384 Gcal/h, the results of 30 measurements have been analyzed.
Analysis of waste heat losses
In the range of loads of 2.94-7.38 Gcal/h, heat losses with flue gases vary from 4.91 to 8.08%. Average rate of change of the parameter is 0.714%/(Gcal/h).
At low loads in the range of 2.93-3.83 Gcal/h, the rate of change of the parameter is 0.805%/(Gcal/h) and with an increase in the load to 4.84 Gcal/h it changes insignificantly and amounts to 0.32%/(Gcal/h).
A further increase in the load leads to fluctuations in the rate of change of the parameter from 0.69 to 6.1%/(Gcal/h).
Figures 3 and 4 show changes in heat loss with flue gases, boiler efficiency and specific fuel consumption when the load changes in the interval under study.
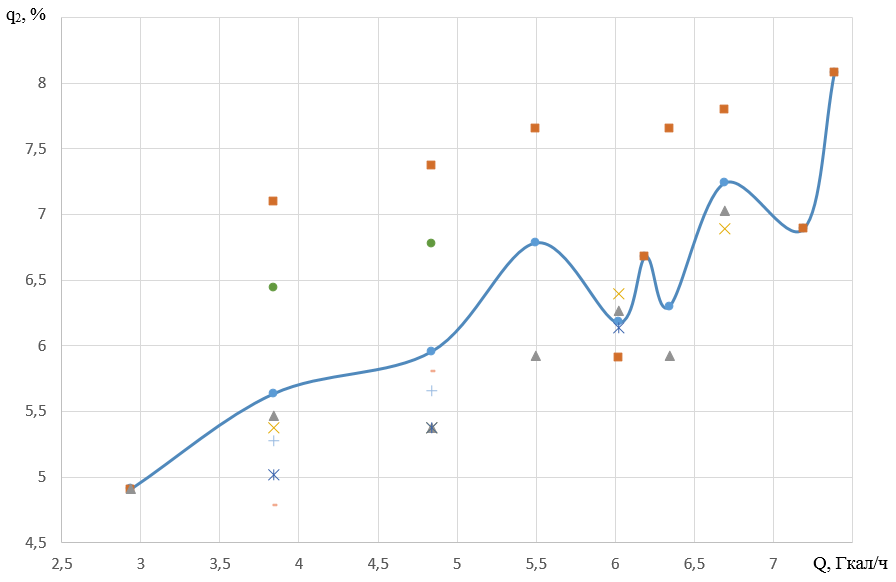
Figure 3 - Dependence of heat losses with waste gases (q 2) on heating capacity
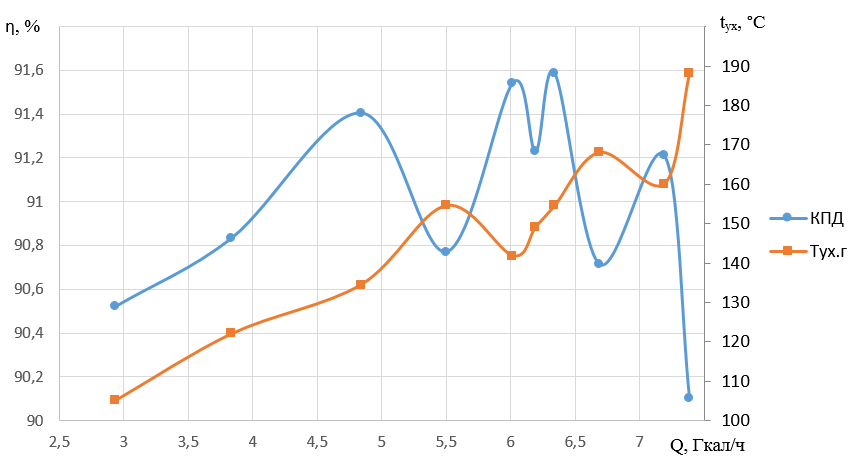
Figure 4 - Dependence of boiler efficiency, flue gas temperature on heating capacity
In the load range from 5 to 7.5 Gcal/h with a step of 0.5 Gcal/h, heat losses with flue gases vary from 5.959 to 8.08%.
The maximum increase in losses with an increase in the load from 7.189 to 7.384 Gcal/h, which corresponds to a decrease in boiler efficiency by 0.4% and increases the specific fuel consumption to 141.7 m3/Gcal. That is, this load interval is undesirable.
Based on the analysis, the preferable load is 7.189 Gcal/h, providing heat loss with exhaust gases of 6.89%. At the same time, the boiler efficiency is 91.21%, and the specific fuel consumption is 138.43 m3/Gcal at a loss rate of 0.69%/(Gcal/h) with an increase in load from 6.68 to 7,189 Gcal/h.
At the proposed load, the flue gas temperature is 160 ° C, which is lower than the maximum possible.
2.2 Analysis of heat loss with chemical underburning
Heat losses with chemical underburning are insignificant and do not affect the technological mode of operation of the boiler unit. Therefore, their influence can be ignored when choosing the optimal operating mode.
2.3 Analysis of heat losses to the environment
Figure 4 shows the changes in heat loss to the environment when the load changes in the range of 2.94 - 7.38 Gcal/h.
In the range of loads of 2.94 - 7.38 Gcal/h, heat losses to the environment change in the range of 4.91 - 1.8%, the average rate of change of the parameter is 0.533%/(Gcal/h).
At low loads, heat losses to the environment are higher, since when the load decreases, the boiler efficiency also decreases. At a load of 2.9 Gcal/h and a boiler efficiency of 90.52%, the highest value of heat loss with flue gases is observed - 4.57%.
At the previously selected optimum load of 7.189 Gcal/h, heat losses to the environment are 1.89%, while the boiler efficiency is 91.21%.
The presence of heat losses to the environment forces us to provide stricter insulation control.
At a selected load of 7.189 Gcal/h, heat loss to the environment is 1.89%.
The graph of the dependence of heat losses to the environment on heating capacity is shown in Figure 5.
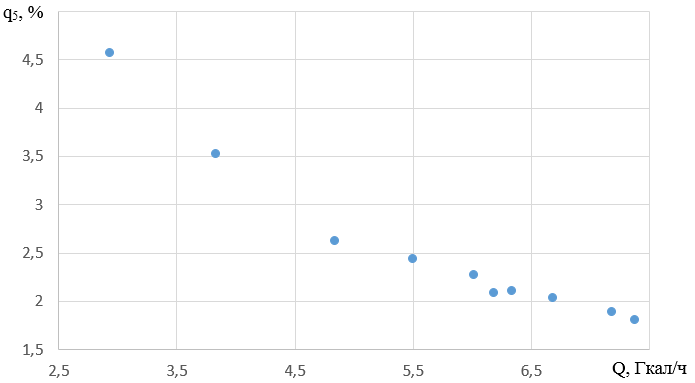
Figure 5 - Graph of the dependence of losses in the environment on heat output
2.4 Analysis of total heat loss
When the boiler is operating under the investigated loads, the total heat losses are from 7.26 to 10.67%. At all loads, most of these are waste heat losses. Their percentage in total losses is from 50.88 to 81.61%.
The rate of change in total losses varies from 0.358 to 5.684%/(Gcal/h). The average rate of change is 1.8569%/(Gcal/h).
With the proposed load of 7.189 Gcal/h, the total losses are 8.79%. The graph of changes in the total losses from heating capacity is shown in Figure 6.
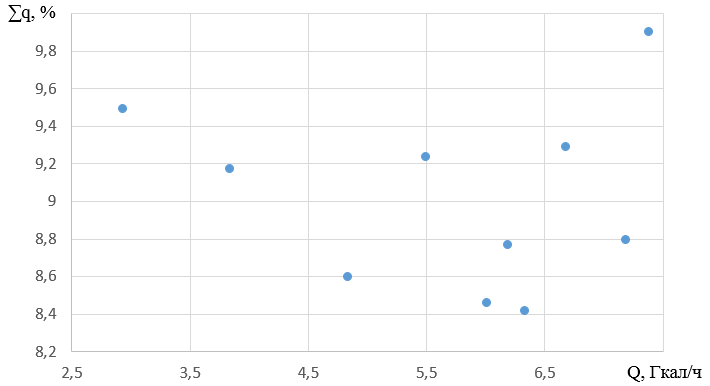
Figure 6 - Graph of changes in total heat losses
Conclusions
In the future, in order to reduce NOx emissions and improve the performance of the boiler unit, the slotted bottom burner will be replaced with a burner with two-stage combustion.
When writing this essay, the master's work has not yet been completed. Final completion: June 2021. The full text of the work and materials on the topic can be obtained from the author or his manager after that date.