Content
- Introduction
- 1. Devices for the implementation of the air cooling operation and the basics of heat treatment
- 2. Types of chamber type furnaces
- 3. Fundamentals of creating mathematical and physical models for studying thermophysical processes of air cooling of metal in furnaces
- 4. Mathematical modeling of the air cooling process
- Conclusions
- The list of sources
Introduction
The technology of production of metal products generally includes three main elements: metallurgy – production of metal of a given composition and its casting; mechanical technology-production from metal products of a given external shape; heat treatment-obtaining the specified properties by changing the structure of the metal. One of the important steps in this chain is heat treatment products, which allows you to level a number of defects in the structure of metals obtained during the the first and second stages of production of products, as well as give a number of new properties. In this regard, in In mechanical engineering, thermal energy is widely used to control the structure and properties of steel products. processing. This type of processing is able to change the structurally sensitive properties of metals, which in the total mass of properties, they occupy a large share.
The process of air cooling during the heat treatment of steel products is carried out in thermal furnaces. actions that impose a number of requirements on this process, such as ensuring a given speed and reducing the cooling time. This leads to an overexpenditure of energy resources and an increase in the residence time of the material in the furnace due to insufficient research of the influence of various design and technological parameters on the process of removing heat from metal. The choice of a rational air flow rate is hindered by insufficient knowledge of the working process. the cooling process in real conditions, the lack of sufficiently simple and reliable methods of its design calculation etc. To meet the requirements, it is necessary to develop a mathematical model for determining the thermal state of the metal.
1. Devices for the implementation of the operation of air cooling and the basis of heat treatment
The chamber furnace often acts as a heating, or even a thermal furnace operating for certain periods. One of the integral parts is the working space, thanks to which it is possible to evenly distribute the necessary indicators of the temperature field. Chamber furnaces are best demonstrated in the chamber mode, since it is in such conditions that it is possible to achieve the highest performance performance. A photo of the heat treatment furnace is shown below in Figure 1.1.
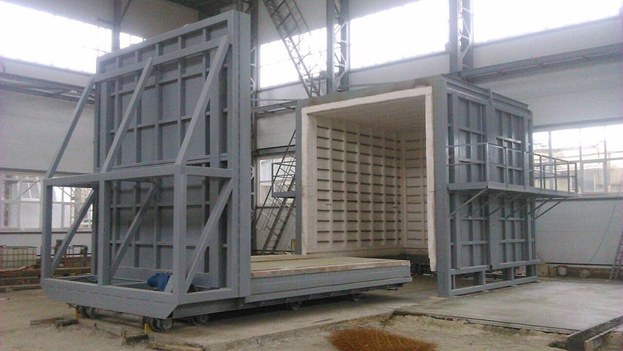
Figure 1.1 - Furnace with a roll-out hearth for heat treatment of products
A chamber furnace is a unit whose functionality looks the widest possible way. To the number of functions such chambers include a variety of types of treatments, starting from heating, ending with calcination. It is worth noting that chamber furnaces demonstrate themselves equally well in all directions, giving out consistently high performance indicators in any of the areas.
As for the temperature indicators in the chamber furnace, it changes periodically and this happens due to the constant movement of the heating process, with the help of fixed parts. Don't miss out either the fact that chamber furnaces are usually divided into categories according to the principle of operation, which can be very different from each other.
Chamber furnaces, according to the principle of operation, are divided into two categories:
• Electric chamber furnace
• Fuel chamber furnace
As for the most practical and convenient option, you should choose chamber furnaces with a retractable hearth. This variation of the chamber allows you to significantly simplify the process of loading and unloading material, which is why many prefer to buy such a furnace.
Chamber type furnaces are a category of vacuum equipment that boasts a fairly wide range of products. But it is worth noting at once that often such cameras are designed to perform a single task. A photo of the heat treatment furnace is shown below in Figure 1.2.
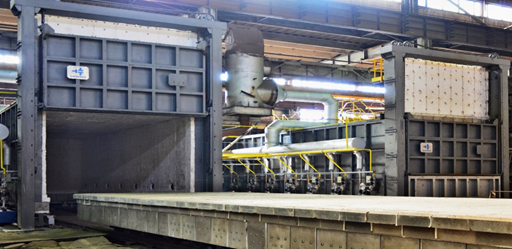
Figure 1.2 - Furnace with a roll-out hearth for heat treatment of products
2. Types of chamber type furnaces
There are several types of chamber type furnaces, namely:
• Release camera
• Heating chamber
• Annealing chamber
• Tempering chamber
• Calcination chamber
This is only a part of the types of chamber furnaces that are most often used in various enterprises. Such a large range of chamber furnaces allows the user to think carefully in order to finally decide and take the unit that he needs.
If we talk about the simplest types of chamber furnaces, then undoubtedly it is a heating chamber. Such cameras are the most practical and simple in terms of design. As for the most expensive and complex furnaces in terms of design , there is no doubt that these are chamber calcining furnaces .
3. Fundamentals of creating mathematical and physical models for studying thermophysical processes air cooling of metal in furnaces
The mathematical model should be implemented in the automated process control system of the heat treatment shop in this regard, it has the following requirements: high resistance to thermal and physical loads; performance.
4. Mathematical modeling of the air cooling process
Depending on the construction, mathematical models can be divided into two groups: deterministic a mathematical model and an empirical mathematical model.
When considering the problems of heat treatment of materials in furnaces, the most widely used method is mathematical modeling. modeling of thermophysical processes according to the first method, i.e. a deterministic mathematical model is created, which is based on the solution of the differential equation of non-stationary thermal conductivity. The features of the simulated object are taken into account by setting unambiguity conditions. In many ways, such a mathematical model it is universal and it is quite easy to apply for this kind of processes, adjusting the conditions uniqueness.
In this paper, the section of air cooling of the heat treatment process of steel cylindrical pipes is considered. blanks. The test blanks are loaded into a chamber heat treatment furnace with a roll-out hearth with the shape of the inner chamber in the form of a rectangular parallelepiped. The purpose of heat treatment is to improve the properties of products, relieve stress and prepare the structure for further processing. The oven is usually loaded with several workpieces at once, placing them according to a special scheme on stands. A schematic representation of the arrangement of workpieces and linings in the heat treatment furnace is shown in Figure 4.1.
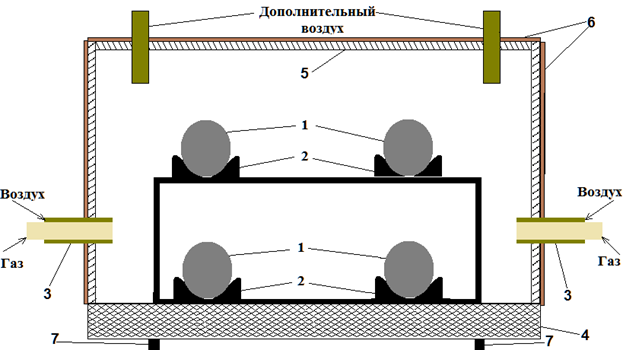
1 – workpieces to be processed; 2-workpieces supports; 3-gas burners; 4-podina from fireclay bricks; 5-ceramic fiber of walls and arch; 6-metal structures of walls and arch; 7 – rollers for the rolling out of the hearth.
Figure 4.1-Schematic representation of the placement of workpieces in the furnace
Conclusions
1. In this work, the types of chamber furnaces were considered, and a chamber furnace with a roll-out hearth was chosen. The main problems associated with the significant influence of air cooling on the properties of the product were identified metal in the heat treatment cycle.
2. A mathematical model for studying the process of convective heat transfer in chamber furnaces is considered. The mathematical model is based on the solution of the differential equation of non-stationary thermal conductivity with differential consideration of lining sections, mutual heat exchange of metal with lining elements, and determining the temperature of the air flow on the body on the basis of the theory of turbulent jets, taking into account the mixing of fresh air with the gas environment of the furnace chamber, taking into account the share of the convective and radiant components in the total amount of heat removed from the metal. The model allows you to calculate faster than the real-time rate by using a one-dimensional problem statement with guaranteed achievement of a given level of accuracy.
3. Using a mathematical model, the proportion of the convective component in the total amount was calculated heat output at different air flow rates.
The list of sources
- Voskoboynikov V. G. General metallurgy: textbook for universities / V. G. Voskoboynikov, V. A. Kudrin, A.M. Yakushev; pererab. Moscow: ICC Akademkniga, 2005. - 768 p.: 253 ill.
- Tikhonov, A. S. Thermocyclic treatment of steels, alloys and composite materials [ Text] / A. S. Tikhonov, V. V. Belov, I. G. Leushin. - M.: Nauka, 1984 – - 187 p.