Abstract Determination of rational technological and design parameters of layered coal gas generators
Content
- Introduction
- 1. Theme urgency
- 2. Goal and tasks of the research
- 3. DKVR boiler device
- Conclusion
- References
Introduction
Stationary steam boilers DKVR (reconstructed double-drum water-tube boilers) are designed to generate saturated steam with pressure up to 13 atmospheres and superheated steam with pressure up to 13 atmospheres and temperatures up to 250 oC. Exists various types of boilers. The first number after the name of the boiler indicates its nominal capacity in tons per hour, the second - working steam pressure in the drum or behind the steam heater in atmospheres, the third is the temperature of the superheated steam, if superheater in degrees Celsius. The estimated efficiency of the boilers is 90-92%. The boiler can operate on solid liquid and gaseous fuels. When the boiler operates on gas or fuel oil, it is possible to increase the steam production by 40-50%.
Initial data in our work:
-Steam capacity = 6.5 t/h.
-Saturated steam, steam working pressure = 13 kgf/cm.
-Fuel coal brand ARSH
-Convective surface 171 m2.
1. Theme urgency
The calculation is made to assess the efficiency and reliability of the unit when operating on a given fuel, the choice auxiliary equipment and obtaining initial data for calculations: aerodynamic, hydraulic, temperatures metal and pipe strength, fly ash intensity, corrosion, etc.
Technologies for the firing of industrial and construction raw materials are used in various industries. Subtle operations thermal processing of materials requires the use of special design solutions. One of them is the boiling oven layer (CS), characterized by a complex structure and versatility.
The disadvantages of this design is that the fluidized bed becomes inhomogeneous, in particular, in the wall space due to the difference in the velocities of the fluidizing agent over the section of the apparatus.
The heterogeneity of the fluidized bed and the presence of gas bubbles impair heat and mass transfer between the walls of the apparatus and the solid phase, as well as the entrainment of the fine fraction of solid material increases, the possibility of adhesion of particles of solid material on the surface of the blinds is not excluded.
The operation of boilers with low-temperature fluidized bed furnaces does not differ from the operation of boilers equipped with serial furnace devices. However, a more dynamic course of the fuel combustion process requires increased attention to it and, as a consequence, the need for its maximum automation. Reliable and economical operation of boiler plants depends on well-organized service, technical condition of equipment and qualifications of personnel.
2. Goal and tasks of the research
The purpose of this work is to determine the rational technological parameters of the NTKS furnace operation.
In this work, a boiler of the DKVR 6.5-13 type was calculated and designed. The DKVR 6.5-13 boiler is designed for the production of saturated and superheated steam for the technological needs of industrial enterprises, in heating, ventilation and hot water supply systems. The appearance of the DKVR boiler is shown in Fig. 1
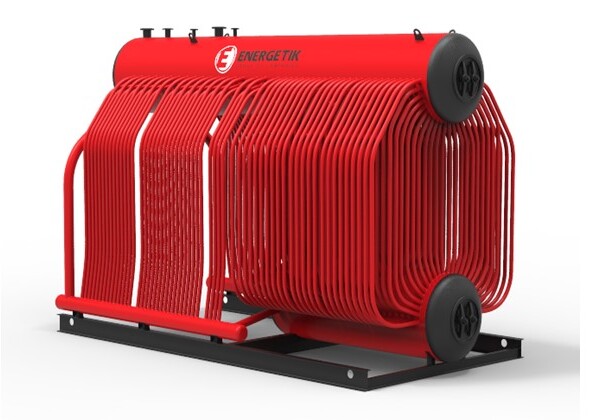
Figure 1-Appearance of the DKVR boiler
Initial data in our work:
-Steam capacity = 6.5 t/h.
-Saturated steam, steam working pressure = 13 kgf/cm.
-Fuel coal brand ARSH
-Convective surface 171 m2.
These boilers are rightfully considered one of the most efficient units. With their high efficiency, steam boilers are economical. There are also unconditional advantages: operation on almost any type of fuel, the unit operation scheme guarantees reliability, high efficiency of work. The devices do not require any special maintenance. The boilers also do not need special conditions for operation.
For firing and disposal of most raw materials and waste products, structures are used, which are based on a cylindrical vertical shaft. Some models have variable cross-section. Average dimensions are 9-12 m in height and 6-8 m in diameter. Itself the shaft is welded on steel sheets with a thickness of up to 12 mm. A typical fine lining is used inside the structure. fireclay bricks. The working base of the fluidized bed furnace is formed by an air distribution hearth (feed panel) with an air box. IN Depending on the specific project, this part can be performed heat-resistant, failure-free and ensuring uniform air flows along the entire internal space of the structure. The fluidized bed apparatus belongs to the field of material processing in a fluidized bed. The disadvantages of this design is that the fluidized bed, inhibited at the periphery of the apparatus by a louver nozzle, becomes non-uniform, in particular, in the wall space due to the difference in the velocities of the fluidizing agent over the section of the apparatus.
The heterogeneity of the fluidized bed and the presence of gas bubbles impair heat and mass transfer between the walls of the apparatus and the solid phase, as well as the entrainment of the fine fraction of solid material increases, the possibility of adhesion of particles of solid material on the surface of the blinds is not excluded.
When gas bubbles rise, forces arise that cause intense transverse vibration of the vertical rods.
The disadvantages of vertical inserts is that it is impossible to regulate the amplitude of their oscillations at different numbers of fluidization, which does not allow achieving maximum vibration, in addition, there is a possibility of vibration transmission to the device body, leading to its destruction.
3. DKVR boiler device
The DKVR boiler consists of two horizontally located drums: upper and lower. The lower drum is shortened so much that it does not fall within the furnaces. This increases the reliability of the boiler, since there is no need to protect the part of the drum facing the firebox from the flame radiation. In steamseparation devices are located in the upper drum space. In the water space of the upper drum there is a feed tube and pipe for continuous blowdown. The lower drum contains a perforated pipe for periodic blowdown and a heating device drum when kindling. For boilers with a capacity of 6.5 tons per hour and above, the upper and lower drums are connected to each other pipes rolled into the upper and lower drums. The rear boiler pipes are downcomers, and the front ones are lifting ones. All together they form a convective boiler heating surface or a convective bundle. On the side walls of the furnace, there are screen pipes. They form the radiation heating surface of the boiler. The upper ends of the wall tubes are rolled in the upper drum, and the lower ends are welded to the collectors. To create a circulation loop, the collectors are connected to the upper drum by water-lowering pipes and connected to the lower drum water transfer pipes. The DKVR 10-13 boiler is structurally different from boilers of lower capacity: it has a raised lower drum under which is a manhole in the boiler furnace. The boiler has additional front and rear screens.
Conclusion
Units with fluidized bed support have many advantages due to their high performance, functionality and flexibility in restructuring. Especially the latest models are convenient for the possibilities of modular layout, which allows with minimal costs integrate the kiln station into the infrastructure of the enterprises with individual design. As for the operation process itself, then the advantages of firing in fluidized bed furnaces are low fuel consumption, the possibility of using fine raw materials (0.6-2 mm) and technical reliability. The high quality of the finished product is also noted, but this applies only to certain materials. If we talk about the disadvantages of KS furnaces, then the main thing will be the high coefficient of dust entrainment of the charge. The dust carried away from the heating units constitutes 25% of the total issue.
This calculation was carried out for the combustion of ARSh coals with an ash content of 22.9% (previously coal T with an ash content of 16.1% was burned in an amount BT = 1747 t/year, CT = 5700 rubles/t).
Thanks to our economic calculations, we have determined that we need Kрек = 3,000,000 rubles for reconstruction, while the period the payback is 6.3 years and the annual economic effect is 114,600 rubles/year.
References
- File archive of students "StudFiles" [Electronic resource] // Energy: website. - URL: https://studfiles.net/preview/1191872/
- Chernetchenko G.B. , Plevako A.P. Ecology Energy [Electronic resource]: article. / G.B. Chernetchenko. - Electronic data. - Pavlodar: Bulletin of the Innovative University of Eurasia, 2011. URL: https://articlekz.com/article/13579
- Combustion of coal in a fluidized bed and utilization of its waste / Zh.V. Viskin and V.I. Sheludchenko, A.I. Ivanov, V.V. Kravtsov. - Donetsk "New World", 1997. - 284 p.
- Calculations of fluidized bed apparatus: reference book / A. P. Baskakov; [A.P. Baskakov and others]; ed. I.P. Mukhlenova and others - L.: Chemistry, Leningrad. dep, 1986 .-- 350s.
- Study of mathematical models of the processes of dehydration of enriched coal by the "fluidized bed" method / V. N. Pavlysh [et al.]// Development of ancestors 2015 [Electronic resource] = Mining of mineral despots: a good scientific and technical collection / DVNZ "National State University" and in. ; editorial board: V. Bondarenko (editor-in-chief) and ін. - Dnipropetrovsk: Litograf, 2015. - P.163-166.
- Research of mine heat-and-power processes and creation of control systems: research report (intermediate): N-21-2000 / Donetsk National Technical University; DonNTU; hands. B.V. Gavrilenko; executed by: Ogolobchenko A.S. [and etc.]. - Donetsk, 2003 .-- 115 p.
- Research and development of furnaces and fluidized-bed baths for heat treatment of small-sized products: author. dis. ... Cand. tech. Sciences: 05.14.04 / Yu. I. Alekseev; Alekseev Yuri Ivanovich; Uralsk. polytechnic. in-t them. CM. Kirov. - Sverdlovsk, 1980 .-- 22 p.