Главная | Ссылки |
Библиотека | Табл
поиска
Донецкий
национальный технический университет
Голокоз Ольга Васильевна
Разработка компьютерной
информационной системы управления
производством механизированных крепей
Специальность 8.080401- "Информационные
управляющие системы и технологии"
Автореферат
магистерской
выпускной работы
Научный руководитель: Спорыхин Виктор
Яковлевич
Донецк - 2002 г.
olga_golokoz@ukrtop.com
-
Актуальность тематики выпускной работы. Выпуск в заданные сроки
необходимого количества очистных комплексов для механизации добычи угля определяется
возможностью изготовления механизированных крепей и требует
управляемости их производства
на основе компьютеризации дискретно-непрерывных технологических и информационных процессов.
- Компьютеризация технологического процесса изготовления механизированных крепей представляет
собой сложную научно-техническую проблему, в решении которой принимают участие коллективы
научно-исследовательских, конструкторских, технологических институтов и проектных организаций,
высших учебных заведений, заводов угольного машиностроения, в том числе шахтной автоматики.
- Разработка компьютерной информационной системы управления производством
механизированных крепей позволяет
повысить эффективность производственно-хозяйственной деятельности управляемых объектов за счет
мобилизации их внутренних резервов. Использование математических методов и моделей для
компьютеризации процессов обработки технологической информации на основе новейших
технологических средств и информационных технологий сопровождается изменением
уровня организации и технологии управления, решаются управленческие задачи,
в результате которых повышается синхронизация технологических процессов и снижается время
цикла изготовления лаво-комплекта угледобывающего комплекса.
- Появление новых вычислительных машин и программного обеспечения выдвигают актуальные
исследовательские задачи, связанные с алгоритмизацией управления технологическими процессами,
обоснованием структуры локальных вычислительных систем (ЛВС) в составе интегрированной системы
управления предприятием, развитием методов и средств моделирования технологических процессов,
обеспечением выпуска необходимого количества механизированных крепей в заданные сроки на основе
систем автоматизации управления производством.
-
- Целью работы является интенсификация и повышение эффективности производства
крепей за счет создания компьютерной информационной системы
управления производством на основе
изучения многоуровневой дискретно-непрерывной системы, параметры которой изменяются в
пространстве и времени с использованием теории дискретно-непрерывных систем.
- Для достижения поставленной цели необходимо решить следующие
основные задачи:
- 1. Проведение анализа, обобщение и изучение дискретно-непрерывных информационных процессов изготовления
механизированных крепей как многомерной динамической системы, параметры которой изменяются во времени и пространстве.
- 2. Разработка математической модели
информационной системы управления процессов изготовления секций крепи для обеспечения интенсификации производства и уменьшения времени цикла изготовления лаво-комплекта.
- 3. Исследование
эффективности используемого метода,
получение зависимостей параметров и
режимов работы системы управления
технологическими процессами
изготовления механизированных крепей от
управляющих и возмущающих воздействий,
влияющих на уровень синхронизации
технологических операций.
- Научная новизна
полученных результатов.
- Разработана на
основе теории дискретно-непрерывных
систем с управляемой структурой
математическая модель управления
технологическими
процессами изготовления
механизированных крепей, которая
учитывает модульный принцип, случайный
характер протекания технологического
процесса и связь между
технологическими операциями во
времени и пространстве.
-
- Практическая
ценность.
- -
разработаны алгоритм и программа
системы управления производством
механизированных крепей;
- - построена структурная схема компьютерной системы управления производством механизированных
крепей;
- - разработана компьютерная
информационная система управления
производством механизированных
крепей.
Метод исследования. В работе
использована теория дискретно-непрерывных
систем с управляемой структурой.
Ожидаемые результаты
- построение
математической модели системы управления
технологического процесса
изготовления механизированной крепи с
управляемой структурой на базе дискретно-непрерывной
сети;
-расчет
такта сборочного конвейера в зависимости
от типоразмера секции крепи;
- построение структурной схемы
компьютерной системы управления
производством механизированных крепей
СОДЕРЖАНИЕ РАБОТЫ
Во введении
обоснована актуальность темы, цель и
задачи исследований, методы исследований,
научная новизна полученных результатов.
В первом разделе отмечается,
что ценный
вклад в создание и исследование систем
автоматизации на предприятиях и заводах
угольной промышленности внесли ученные и
специалисты: Борисов А.А., Груба В.И.,
Демченко Н.П., Красик Я.Л., Клубин В.П.,
Лаздынь С.В., Спорыхин В.Я., Фельдман Л.П. и
другие. Вместе с тем, в проведенных
исследованиях недостаточно разработаны
методы создания компьютерной
информационной системы управления
дискретно-непрерывным производством,
параметры которого изменяются
случайным образом в пространстве
и времени.
Приводится
обзор существующих автоматизированных
средств(CASE-средств)
создания компьютерных информационных
систем управления производством - средства
анализа (Upper CASE), средства анализа и
проектирования (Middle CASE), средства
проектирования баз данных, средства
разработки приложений.
В качестве объекта управления(рис. 1) выбран
технологический процесс изготовления
секции крепи, который представляет собой
сложную многосвязную систему и включает:
обработку деталей (поточные линии),
изготовление сборочных единиц (технологические
маршруты), сборку секций крепи (сборочный
конвейер) и термообработку. Изучение
технологии изготовления крепей показало,
что в основном обработка каждой детали (изготовление
сборочной единицы) производится по
самостоятельному, независимому
технологическому маршруту. Это свойство
материальных потоков позволяет
рассматривать единый технологический
процесс изготовления крепи как
совокупность отдельных технологических процессов,
т.е. совокупность некоррелированных
технологических маршрутов, что следует
учитывать при создании компьютерной
информационной системы управления
производством механизированных крепей.
Основной целью построения системы
управления является повышение уровня
синхронизации работ в технологических
маршрутах, обеспечение ритмичной работы
главного конвейера. Для достижения
поставленной цели в работе решаются задачи
исследований, приведенные во введении.
Рис.
1 Структура системы управления
производством механизированных крепей
- В работе рассматривается автоматизация
технологических процессов изготовления механизированных крепей на
примере
Дружковского машзавода как наиболее типичного для данного производства
представителя. Номенклатура выпускаемых заводом механизированных крепей
достаточно широка. Кроме того, в поставляемые конкретному заказчику
лаво-комплекты часто приходится вносить существенные конструктивные
изменения, связанные со спецификой условий эксплуатации на данной шахте.
В условиях рынка отечественным предприятиям приходится выдерживать конкуренцию
с продукцией зарубежных изготовителей и прежде всего - Узловского и
Каменского машзаводов в России и польского завода "КОМАГ". Поэтому производство
крепей должно быть гибким, оперативно реагирующим на конъюнктуру рынка,
экономически выгодным заводу и шахте.
- Изготовление механизированных
крепей производится в блоке цехов данного завода, и является
сложным взаимоувязанным процессом, в котором участвуют 6 самостоятельных
цехов. Этот процесс должен быть организован во времени и в пространстве
таким образом, чтобы выпуск секций крепей и реализации лаво-комплекта
происходили планомерно и в строго установленные заказом сроки. Равномерное
выполнение заказа и реализации выпуска крепей должны быть достигнуты
на основе ритмичной организации производства на всех участках блока
цехов. В технологической последовательности изготовления механизированных
крепей заключительным звеном является узловая и полная сборка секции
крепи на сборочном конвейере с последующим оформлением лаво-комплекта
на заданную длину лавы в шахте. Все изделия поступают на сборочный конвейер
в виде отдельных сборочных единиц и деталей, предварительно прошедших
контроль и сборку.
- В блоке цехов организованы следующие участки:
сборка и испытания гидростоек, сборка перекрытий и буферов. Собранные
и испытанные сборочные единицы и детали, поступают на сборочный конвейер.
Общая сборка секции крепи выполняется поточным методом на толкающем
конвейере периодического действия. Сборка гидравлических стоек производится
поточным методом с применением быстродействующих, пневматических приспособлений
и инструментов. Функционально блок цехов включает в себя следующие цеха:
сборочный цех №17; механический цех №35; термический цех №21; гальванический
цех №32; цех металлоконструкций №19; окрасочный цех; механозаготовительное
отделение №20; общецеховые вспомогательные службы. Эти цехи являются,
с одной стороны, самостоятельными, с другой стороны, объединены общим
производственным процессом, направленным на изготовление готовой продукции
необходимого качества. При этом ритм работы сборочного цеха, как выходного
звена блока цехов, определяет ритм выпуска комплектующих деталей и сборочных
единиц для всех остальных цехов. В блоке цехов выполняются следующие
технологические операции по производству механизированных крепей: -
механическая обработка деталей для гидравлических стоек и гидродомкратов,
предварительная обработка оснований, блоков гидрораспределителей, проходящих
термическую обработку с последующей передачей их на окончательную обработку;
- термическая обработка всех деталей механизированных крепей; - гальваническая
обработка деталей механизированных крепей; - заготовка деталей из листового
и профильного материала с последующей их механической обработкой, сваркой
и окраской; - изготовление сборочных единиц и полная сборка секций крепи
с последующей комплектацией всего комплекса; - окраска деталей механизированных
крепей и покраска секции в сборке. Часть сборочных единиц, деталей и
заготовок поступают в блок цехов по межцеховой кооперации (отливки,
рессоры, гидроблоки, шланги, трубопроводы и др.). Механо-заготовительное
отделение №20 получает детали и заготовки со склада, кузнечного цеха
№5 и обрубного цеха №3 и проводит травление трубных заготовок, их механическую
обработку и их сварку. Продукцией являются следующие детали гидрокрепей:
основания, стаканы, гидроцилиндры, плунжеры, винты, гайки. Эта продукция
направляется в термический цех №21, в механический цех №35 и в окрасочный
цех с последующей передачей на сборку. Механический цех №35 получает
детали по межцеховой кооперации из цеха №20 и из других цехов. Производит
механическую обработку деталей гидростоек: плунжеров, цилиндров, гидродомкратов,
корпусов блоков гидрораспределителей. Всю продукцию отправляют в сборочный
цех №17. Цех металлоконструкций №19 производит заготовку деталей из
листового и профильного материала, их последующую механическую обработку,
сварку. Продукцией цеха №19 являются следующие детали и сборочные единицы
механизированных крепей: перекрытия, защиты, щитки, крышки. Часть продукции
отправляют в окрасочный цех, остальная часть - непосредственно на сборку.
Термический цех №21 производит термическую обработку деталей механизированных
крепей с целью улучшения их механических свойств. Это плунжеры, гайки,
винты, которые передаются в механический цех №35, в сборочный цех №
17. Сборочный цех №17 получает детали и сборочные единицы из цеха №19,
цеха №35, окрасочного цеха, а также из других цехов завода. Производит
узловую и полную сборку секций крепи с последующей комплектацией всего
комплекса.
- Таким образом, в блоке цехов производится большинство деталей
и сборочных единиц секций крепи, а также производится сборка их в изделие.
- В ходе изучения материальных потоков в блоке цехов было установлено,
что работа какого-либо технологического маршрута по обработке своей
детали не зависит от работы остальных технологических маршрутов, поэтому
по своему технологическому маршруту партии деталей движутся к сборочному
цеху независимо от того, как происходит движение партий деталей по другим
технологическим маршрутам. Это свойство материальных потоков позволяет
рассматривать единый производственный процесс в блоке цехов как совокупность
производственных процессов технологических маршрутов.
- Процесс изготовления
механизированных крепей на Дружковском заводе угольного машиностроения
в основном сосредоточен в блоке цехов (БПЦ) 1 и механосборочном цехе
№10. Эти цеха являются, с одной стороны, самостоятельными,
а с другой стороны, объединены общим производственным процессом, направленным
на изготовление крепей необходимого качества в заданные сроки с наименьшими
затратами. При этом ритм работы сборочного конвейера, как выходного
звена блока производственных цехов определяет ритм выпуска комплектующих
деталей и сборочных единиц для всех остальных цехов.
- Компьютерная информационная
система управления должна увязывать объемы производства крепей с пространственным
закреплением, разбивку задания на более короткие периоды, доведение
их до непосредственных исполнителей и управления их выполнения. Общая
сборка секций крепи выполняется поточным методом на рамном шагающем
конвейере периодического действия. Для контроля и типовых испытаний
секций крепей функционирует испытательная станция, стенды которой соединены
транспортным конвейером. Сборочные единицы и детали (стойки, гидродомкраты)
на главный сборочный конвейер транспортируются на тележках. Основания,
стаканы, конструкции подаются в сборочный цех с помощью подвесного толкающего
конвейера. Подача их непосредственно на рабочие места сборщиков главного
конвейера производится с помощью крана, электротельферов и пневматических
подъемников. Для изготовления сборочных единиц организованы участки
сборки и испытания гидростоек, сборки перекрытий и буферов, окраски
цилиндров стоек. Гидравлические стойки собирают поточным способом с
применением быстродействующих пневматических приспособлений и инструментов.
Каждый участок выпускает собранные и испытанные сборочные единицы и
детали, поступающие на главный сборочный конвейер. Сборочный цех 17
является выпускающим цехом в производстве механизированных крепей в
БПЦ 1 и, в общем, характеризует производственную мощность блока цехов
в изготовлении готовых элементов секции крепи.
- Равномерное выполнение
плана выпуска и реализации крепей может быть достигнуто только на основе
ритмично организованного производства на всех участках БПЦ с использованием
средств автоматизации и современных компьютеров.
- Ритмичность производства
- это согласованная во времени работа отдельных цехов, производственных
участков, рабочих мест. Отсюда следует, что необходима увязка работы
главного конвейера с работой цехов-поставщиков сборочных единиц и деталей
(в том числе стандартных, используемых в различных типах крепей),
а именно: достижение единства ритма на всех стадиях и операциях; ритм
работы линий, изготовляющих комплектующие изделия, должен быть равен
или кратен ритму сборки секций крепи (как основному ритму выпуска элементов
секции крепи), а ритм отдельных операций внутри линий механической обработки
равен или кратен ритму поточной линии. Научно обоснованный и заранее
установленный ритм сборочного конвейера (с учетом заданий) на основе
компьютерных информационных технологий является организующим фактором,
способствующим обеспечению непрерывной и равномерной подачи комплектующих
изделий на сборку.
- В основу
организации управления поточно-конвейерной
сборки положены следующие принципы:
разделение всего процесса сборки на
операции с одинаковой длительностью;
специализация рабочих на выполнении
постоянно закрепленных операций;
поступление на главный конвейер полностью
собранных, испытанных и окрашенных
сборочных единиц и деталей.
- Ритм сборки секций
крепи определяется тактом поточной линии (конвейера).
Такт поточной линии представляет собой
расчетный промежуток времени между
выпуском с нее последовательно идущих по
потоку экземпляров изделий.
- Такт
сборочного конвейера определяется на
основании задания из выражения:
,
где
t - расчетный такт
сборочного конвейера;
- календарный фонд
времени работы в смену;
- регламентированный перерыв для отдыха;
- число рабочих смен в сутки;
- процент
технологических потерь;
- число рабочих
дней в году;
- программа выпуска
секций крепи на год, шт.
Такт является основой расчета числа
рабочих мест по сборочным операциям. Необходимое
число рабочих мест на i-той
группе операций определяется по формуле:
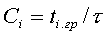
где
- продолжительность i-той
группы операций, мин.
Число рабочих мест на i-той
группе операций определяют путем
округления расчетного числа до ближайшего
целого числа. Коэффициент загрузки
рабочего на i-той
группе операций:
,
где
- проектное число рабочих мест
- Важнейшим условием высокопроизводительной работы сборочного цеха является
правильное распределение сборочных операций на рабочих местах, обоснованный
выбор потребного числа сборщиков для выполнения заданного объема сборочных
работ при обеспечении допустимого коэффициента загрузки рабочих мест.
Указанные операции должны быть компьютеризированы с использованием современных
ЭВМ.
- На основании вышеописанных параметров, заданий по выпуску секций
механизированных крепей и нормированного времени элементарных сборочных
операций должны составляться с помощью ЭВМ графики сборки секций крепи
всех видов и определяется потребное число рабочих-сборщиков для выполнения
процесса сборки. Для правильной комплектации рабочих позиций конвейера
большое значение имеет степень унификации сборочных единиц и деталей
различных типов крепей. Запасы комплектующих изделий, которые являются
унифицированными для всех типов крепи, должны находиться на рабочих
местах постоянно. Запасы специализированных деталей готовят за смену
до начала выпуска крепи, в которую они входят, и по окончании изготовления
соответствующего типа крепи используют полностью для освобождения площадей
под комплектующие изделия следующего типа секций крепи. Анализ выпускаемых
элементов секции крепи блоком цехов показывает, что у конструкторов
завода имеются значительные резервы для унификации элементов выпускаемых
секций крепи. Это позволит уменьшить объемы конструкторской работы,
технологической подготовки производства, значительно снизить себестоимость
и повысить качество выпускаемых крепей выемочных комплексов.
-
- Во втором разделе
строится математическая модель
системы управления. При
этом производится анализ существующих
методов.
- К основным видам математических моделей для исследуемого технологического
процесса можно отнести имитационное моделирование, которое представляет
собой воспроизведение процессов, объектов, явлений с имитацией случайными
величинами и случайными процессами звеньев оригинала, которые не удается
представить определенными математическими моделями. Имитационное моделирование
рассматривают так же, как управляемый эксперимент, проводимый на ЭВМ.
В таком эксперименте определенные математическими моделями части объекта
моделирования взаимодействуют с имитирующими возмущающие воздействия
и некоторые звенья САУ генераторами случайных величин. Это взаимодействие
проводится по определенным в эксперименте правилам, а результаты моделирования
подвергаются статистической обработке.
- Полунатурное моделирование (моделирование
с реальной аппаратурой) заключается в исследовании элементов реальной
аппаратуры совместно с моделью остальной части системы, реализованной
на ЭВМ. Применение такого метода становится необходимым в тех случаях,
когда не удается описать работу некоторых элементов системы математически.
- Методы теории массового обслуживания. Моделирование на основе СМО предусматривает,
в основном, исследование зависимости количественных показателей обслуживания
от характеристик потока заявок и параметров ИПК (инженерно-производственный
комплекс), производительности ИПК, количества ресурсов определенного
класса и т. д. При этом возникают трудности, связанные с размерностью
задачи. Кроме того, модель, построенная методами СМО, не отражает параллельность
протекающих процессов, конкурирующих в доступе к совместно используемому
ресурсу, поэтому эти методы дают упрощенное описание динамики реального
ИПК. Их можно использовать для предварительной оценки альтернативных
вариантов построения моделей ИПК.
- Другим распространенным методом математического
описания технологических процессов является метод вероятностного автомата
(ВА). Вероятностный автомат - это система М= (X, Y, А,
μ
(а', у/а, х)).
Здесь Х={х1, х2, . . . ,хm}- конечное множество входных сигналов ВА,
Y={y1, y2, . . . yn } - конечное множество выходных сигналов, А={ a1,
. . .,ak } -конечное множество состояний. Через
μ((а', у/а, х) обозначена
условная вероятность того, что ВА M, получив на вход символ х, находясь
в состоянии а, перейдет в новое состояние
а'
и выдаст на выходе сигнал
у. Наглядно ВА можно представить в виде "черного ящика", который имеет
вход, выход и память. Память "черного ящика" проявляется в том, что
он может находиться в различных состояниях. Для изучения свойств дискретных
систем и развития методов их конструирования, успешно применяются, также,
методы теории графов и сетей. Следует отметить, что не все графовые
модели, в частности, конечные автоматы, адекватно описывают реальные
производственные системы с параллельно функционирующими и асинхронно
взаимодействующими компонентами.
- Широкое применение в различных областях
науки и техники в настоящее время получили различные графовые методы
исследования параллельных процессов. Наиболее известными и широко применяемыми
графовыми методами алгоритмического описания являются: графы состояний
(автоматы); управляющие графы; графсхемы алгоритмов. Существуют и другие
графовые методы алгоритмического описания, такие как системы суммарных
векторов, параллельные программные схемы и др. Но они не получили достаточно
широкого применения для моделирования технологических процессов.
- В последние
годы в Украине и независимо во Франции появились работы, где описывались
системы, состоящие из параллельно функционирующих и асинхронно взаимодействующих
непрерывных и дискретных компонентов. В Украине такие графические и
математические средства были названы ДН-сетями, а во Франции - гибридными
сетями Петри (гибридные СП). Языковые средства ДН-сетей включают в себя
непрерывную и дискретную позиции, непрерывный, дискретный и структурно-управляемый
переходы, спецификацию, в соответствии с которой непрерывные и структурно-управляемые
переходы помечаются операторами, например, интегрирования, дифференцирования,
передаточной функцией, коэффициентом усиления, непрерывные позиции -
непрерывными переменными. Непрерывные позиции маркируются вещественны
числом. Структурно-управляемые переходы реализуют функцию "включить-выключить"
машину, аппарат связь между компонентами системы.
- Гибридные СП являются
расширением сетей Петри: в их основу положены непрерывные сети Петри.
Последние являются эквивалентом тактируемых дискретных сетей Петри с
определенным временем срабатывания перехода. Гибридные СП имеют непрерывные
и дискретные позиции, а также непрерывные и дискретные переходы. Так
как позиции непрерывной сети Петри маркируются вещественным (положительным)
числом, которое не длиннее целого, то, по признанию самих авторов, непрерывные
сети Петри позволяют моделировать лишь некоторые непрерывные системы.
Эти же ограничения перенесены и на гибридные сети Петри. Ограничения,
присущие гибридным СП, маркирование непрерывных позиций вещественным
положительным числом дают возможность описывать только процессы массового
расхода физических потоков (химических компонентов) и обработки информации.
Возможность маркировать непрерывные позиции вещественными числами позволяет
описывать языком ДН-сетей сложные технологические системы, в которых
происходят процессы тепломассопреобразования и обработки информации.
- Обращение к
графическим языковым средствам связано с тем, что графические методы
в проектировании и программировании получают все большее распространение
в связи с широкими возможностями графических терминалов.
- В технологическом
процессе изготовления механизированных крепей можно выделить дискретно-непрерывные
процессы, состоящие из подпроцессов, которые функционируют как непрерывно,
так и дискретно. Повышение экономической эффективности такого процесса
требует применения более современных методов. Поэтому, задачу управления
такой сложной системой будем решать методом дискретно-непрерывных сетей.
- В
третьем разделе на основе
полученных теоретических и экспериментальных
результатов исследования объекта
управления разработаны технические
требования к создаваемой
компьютерной информационной системе
управления. В соответствии с
требованиями построена
принципиальная схема системы
управления изготовления крепей(рис.
2),
которая включает в себя два уровня
управления. На первом уровне
расположены технические средства
автоматизации дискретных и
непрерывных технологических
процессов изготовления крепей. Для
управления дискретными процессами
разработана локальная
вычислительная сеть (ЛВС)
автоматизации управления
технологическими маршрутами.
Управление осуществляется планово-диспечерским
отделом(ПДО), который с помощью АРМов
выдаёт и корректирует задание цехам с
дискретным производством.
- Заказ на изготовление лаво-комплекта
крепи инженерными службами завода(верхний
уровень управления) с помощью АРМов
обрабатывается соответствующим образом и
передаётся по каналам связи в ПДО, который
с учетом разработанных в работе
алгоритмов и программ(используя и другие
программы) разрабатывает сменно-суточные
задания цехам, производственным участкам,
поточным линиям, технологическим
маршрутам. На последующие сутки сменно-суточные
задания из файл сервера ПДО по каналам
связи с помощью мостов и модемов
передаются в файл сервер ЛВС
автоматизации управления
технологическими маршрутами (правая часть
нижнего уровня управления) и файл сервер
САУ режимами термических печей (левая
часть нижнего уровня). Далее информация о
сменно-суточных заданиях по каналам связи
передаётся в АРМы планово-распределительных
бюро(ПРБ) цехов, где разрабатываются
сменные задания на каждое рабочее место.
Эти задания начальником цеха, старшими
мастерами, мастерами доводятся в начале
смены исполнителям.
-
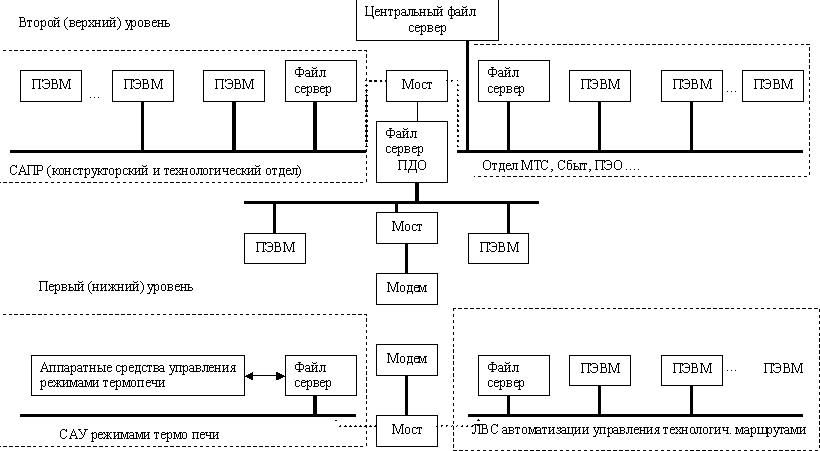
-
- Рис 2. Принципиальная схема системы
управления изготовления крепей; ПЭО -
планово-экономический отдел; МТС - отдел
материально-технического снабжения
-
В заключении сформулированы
научные результаты, практическая
значимость и область использования
выполненной выпускной магистерской
работы.
-
- Список литературы
- Згуровский М.З., Денисенко В.А. Дискретно-непрерывные
системы с управляемой структурой. - К.:Наукова
думка 1998
- Питерсон Дж. Теория сетей Петри и моделирования систем: Пер. с англ. -М.: Мир, 1984. -264 с., ил.
Тадао Мурата. Сети Петри: Свойства, анализ, приложения. ТИИЭР, т. 77, № 4, апрель,
1989
Цанов В.А., Ташев Т.Д. Вопросы перехода от SDL-схем к сетям Петри при проектировании распределенных информационно-управляющих систем. // Сб.: Управление ресурсами в интегральных сетях. -М.: Наука, 1991.
Черняев В.Г. Вопросы композиции сетей Петри. I // Сб.: Управление ресурсами в интегральных сетях. -М.: Наука, 1991.
Закревский А.Д. О корректности параллельных алгоритмов логического управления. // Техническая кибернетика, 1987, № 4,
Кириллов В.Ю. Об автоматной интерпретации сетей Петри. // Техническая кибернети-ка,
1987.
Беликов В.К., Рутнер Я.Ф. матричное задание и анализ раскрашенных сетей Петри. // Техническая кибернетика, 1987, №
5 Халимон В.И., Савина Е.В. Система преобразования модели периодического технологического процесса в сеть Петри. // Математические методы в технике и технологиях. Сб. трудов 13 междун. науч. конф. ММТТ-2000. Т. 6. Секции 11, 12, 13. -СПб. 2000.
Веревкин А.П., Муртазин Т.М. Моделирование процессов принятия решений в сложных системах управления. // Проблемы нефтегазового комплекса России. / Материалы международной конференции, УГНТУ.- Уфа, 1998.
Васильев В.В. и др. Система специального математического обеспечения для моделирования параллельных процессов. // Управляющие системы и машины, 1987, № 5.
Юдицкий С.А. Технология целевого моделирования бизнес-систем. // Приборы и Системы. Управление, контроль, диагностика, 2000, № 10.
-
Главная | Ссылки |
Библиотека | Табл
поиска
Created: May 20, 2002