Методика экспериментальных исследований
Оборудование, материалы, инструмент. Для проведения эксперимента разработан и изготовлен стенд на базе заточного полуавтомата модели 3672, составными частями которого являются: устройство для правки круга свободным абразивом; система для измерения и регистрации составляющих сил шлифования, включающая стол динамический, усилитель низкой частоты модели 8УН4, самописец H33S-4; система записи профиля круга в радиальном сечении; устройство для определения режущей способности шлифовального круга, реализующее схему упругого шлифования эталонных образцов. Шероховатость обработанной поверхности регистрировалась профи-лометром модели 283. Определение линейного износа круга осуществлялось с помощью специального приспособления, оснащенного индикатором часового типа с ценой деления 0,002 мм.
На стенде в процессе проведения экспериментов реализовывалась схема плоского врезного шлифования. Обработке подвергались образцы из технического стекла и хрусталя. Режущая способность алмазного инструмента определялась на эталонных образцах из технического стекла размером 100x50x12 мм.
Для восстановления режущей способности алмазно-абразивного инструмента использовалась абразивная суспензия на основе абразивного порошка карбида кремния черного зернистости №20.
В качестве режущего инструмента использовались алмазные круги типа IAI 200x6x3x75 АС32, зернистости 250/200, 100/80, 65/50 на связке Ml 100$ концентрации алмазов.
В качестве технических сред использовались вода и полярная СОЖ по а. с. №997446, представляющая собой 1% водный раствор ПАВ на основе оксиэтилированных жирных спиртов.
Методика экспериментального определения математических зависимостей технических ограничений от уровня варьируемых параметров.
В процессе экспериментальных: исследований устанавливались следующие зависимости:
Pz=f(V, S, t, W, B, dz);   (1)
Py=f(V, S, t, W, B, dz);   (2)
Vp=f(V, S, t, W, B, dz);   (3)
Q=f(V, S, t, W, B, dz);   (4)
Ra=f(V, S, t, W, B, dz);   (5)
где Pz и Рy - тангенциальная и радиальная составляющие силы шлифования (Н); Vp - радиальный линейный износ круга (мм); Q - коэффициент режущей способности круга, измеряемый отношением производительности шлифования эталонных стеклянных образцов по упругой схеме к величине усилия прижатия образцов к кругу (см3/мин*Н); Ra- уровень шероховатости обработанной поверхности (мкм); V - линейная скорость круга (м/с); S - продольная подача (м/мин); t - глубина шлифования (мм); W- объем сошлифованного материала (см3); В - ширина круга (мм);dz- зернистость круга.
Для решения поставленной задачи использовалась общая методика, согласно которой проведенные эксперименты, необходимые для определения каждой из названных зависимостей, условно можно разбить на несколько этапов. На первом этапе находилась зависимость каждого из аргументов от уровня параметров режима
шлифования при постоянстве значений других варьируемых параметров, в частности при состоянии круга, соответствующем его исходной режущей способности (W=0). Затем определялись математические зависимости аргументов от объема сошлифованного материала. Для различных сочетаний режимов обработки находились коэффициенты этих зависимостей. На следующем этапе путем определенного планирования эксперимента определялась обобщенная зависимость каждого из аргументов от режима шлифования и величины объема сошлифо-ванного материала. На заключительном этапе обобщенная зависимость уточнялась путем введения в нее членов и коэффициентов, учитывающих влияние на исследуемый фактор ширины алмазного круга 8 и его зернистости dz.
Для определения зависимостей Рz(Рy) =f( v, S, t); Vp =f( v, S, t); Q =f( v, S, t); Ra =f( v, S, t)
при W = 0 был реализован полный факторный эксперимент с планом 23(варьирование трех параметров на двух уровнях). Значения верхнего и нижнего уровней режимов шлифования были приняты соответственно для v-32,9 и 18,6 м/с; для S - 6,0 и 2,5 м/мин ,
t -3,6 и 1,3 мм. Значения уровней варьируемых параметров принимались с учетом режимов обработки технического стекла и хрусталя в промышленных условиях.
Для определения зависимостей аргументов от объема сошлифо-ванного материала для всех восьми сочетаний варьируемых параметров режима шлифования осуществлялось шлифование обрабатываемых материалов с периодическим контролем исследуемых параметров (сил, износа круга, его режущей способности, шероховатости образцов) по мере затупления круга" Замеры указанных характеристик процесса шлифования производились при сошлифовании объемов обрабатываемого материала, соответствующих значениям W=0; W= 150 см3; W= 400 см3; W= 700 cм3;W=1OOO см3.
Определение математических зависимостей аргументов (A) от объема сошлифованного материала проводилась с помощью метода наименьших квадратов. При этом к рассмотрению принимались модели, имеющие физический смысл. Наиболее подходящей модели соответствует наименьшая дисперсия адекватности.
Для определения обобщенной зависимости аргументов от v , S , t и W также реализовывался полный факторный эксперимент с планом 23. Варьируемыми параметрами являлись режимы обработки. В качестве функции отклика принимались коэффициенты в уравнениях зависимостей Аi=f(W),
Все этапы исследований сопровождались статистическим анализом результатов эксперимента при доверительной вероятности 95%.
Методика восстановления режущей способности инструмента. Для восстановления режущей способности алмазных кругов был применен метод правки свободным абразивом. Процесс правки осуществлялся непосредственно на станке при вращении круга с рабочей скоростью. Подача абразивной суспензии составляла 180 -200 смэ/мин. Подача притира была равна 0,69 мм/мин. Длительность правки круга, которым предварительно был сошлифован объем материала W * 1000 см3, составляла 3-4 мин. Критерием окончания правки являлась величина коэффициента режущей способности, которая для заправленного круга зернистости 250/200 находилась в пределах Q=0,45-0,60 см3/мин Н. Радиальный износ круга в процессе правки не превышал 20% размера зерна основной фракции и для круга зернистости 250/200 равнялся 30-40 мкм.
Результаты экспериментальных исследований влияния режимов обработки и правки на процесс шлифования стеклоизделий
Экспериментальные исследования были проведены с целью определения аналитических зависимостей технологических и технических ограничений ( Pz , Рy , Q , Vp и Ra ) от режимов шлифования и других параметров процесса шлифования, которые необходимы для решения задачи оптимизации технологического процесса механической обработки стеклоизделий.
Экспериментальные исследования силовых зависимостей плоского врезного шлифования технического стекла. Эксперименты проводились в соответствии с изложенной выше методикой. В качестве математической модели, описывающей связь тангенциальной и радиальной составляющих силы шлифования с режимами обработки была принята степенная зависимость.
Pz(y)=CPz(y).VnPz(y).SyPz(y).txPz(y);   (6)
где Срz(y) - коэффициенты, учитывающие условия обработки, в
частности, активность используемой СОЖ;
n , y , x - показатели степени при варьируемом параметре.
Уравнение регрессии, позволяющее оценить значения Ср, n , y , X , имеет вид:
y = b0 + b1x1 + b2x2 + b3x3 + b13x1x3 + b23x2x3 + b123x1x2x3;   (7)
где y - логарифм исследуемого параметра;
b0 - свободный член, определяющий коэффициент в зависимостях(6);
bi - коэффициенты регрессии, определяющие показатели степени в зависимостях (6);
xi- безразмерные варьируемые параметры, представляющие собой логарифмы V, S , t.
В соответствии с матрицей планирования полного факторного эксперимента с планом 23 были выполнены экспериментальные исследования. В результате статистической обработки полученных данных, после отбрасывания незначимых коэффициентов регрессии и преобразования уравнений, зависимость составляющих силы шлифования от режимов обработки для исходного состояния круга примет вид:
Pz=45.7.V-0.62.S0.82.t1.13;   (8)
Py=77.6.V-0.49.S0.78.t1.13;   (9)
Проверка гипотезы адекватности полученных математических моделей по F - критерию Фишера показала их адекватность.
Предварительные эксперименты, имеющие целью изучить характер изменения составляющих силы шлифования по мере затупления круга, показали, что зависимость составляющих силы шлифования от объема сошлифованного материала может быть описана уравнением вида:
Pz(y)=Pzo(yo)+bek/w;    (10)
где Pzo(yo)- значение соответствующей составляющей силы шлифования при W = 0;
b - прирост силы шлифования ;
коэффициент К характеризует скорость наростания силы по мере удаления припуска;
W - объем соллифованного материала.
Коэффициенты b и K зависят от режимов обработки. Для всех восьми сочетаний режимов обработки производилось затупление круга в процессе сошлифования объемов обрабатываемого материала до W = 1000 см3. Для каждого сочетания v, S, t методом наименьших квадратов определялись значения коэффициентов К и & . Анализ результатов определения коэффициентов K и b показал, что значения коэффициентов находятся в зависимости от режима обработки. Для получения зависимости коэффициентов К и b от v, S и t использовался метод планирования эксперимента с планом 23, в котором варьируемыми параметрами выступают режимы обработки, исследуемыми - коэффициенты К и b .
Зависимость коэффициентов b и k от V, S и t была принята в виде
b=Cв.Vnв.Syв.txв;   (11)
k =k0 + k1V +k2S + k3t;   (12)
Статическая обработка результатов экспериментов позволила получить обобщение зависимости составляющих силы шлифования от режима шлифования и объема сошлифованного материала
Pz=45.7.V-0.62.S0.82.t1.13 + 8371.V-2.26.S1.21ln V-2.92.t1.2e(331-9.4V-42S-110t)/w ;   (13)
Py=77.6.V-0.49.S0.78.t0.97 + 94.5.V-0.4.S1.12-0.57ln t.t1.16e(-78.6-9.8S-31.6t-7.4St)/w ;   (14)
На рис.1 приведены графики зависимостей Pz и Рy для различных режимов обработки.
Проведя серию экспериментов аналогичных приведенным выше, при вариации ширины алмазного круга и его зернистости были получены дополнительные данные, позволившие уточнить обобщенные зависимости (13) и (14), введя в них характеристики алмазного инструмента.
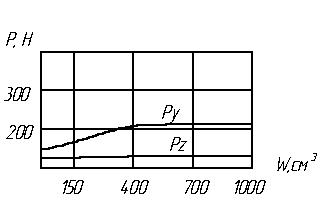
Рисунок 1.-Зависимости составляющих силы шлифования от объема сошлифованного материала.Шлифование технического стекла кругом АС32 250-200-MI - 4 с режимами: I - v = 18,6 м/с; s =6,0 м/мин; t = 3,6 мм; 2 - v= 32,9 м/с; S = 2,5 м/мин t = 1,3 мм
Экспериментальные исследования режущей способности инструмента. Режущая способность алмазно-абразивного инструмента характеризует возможность инструмента обеспечить необходимый уровень выходных параметров процесса шлифования, а именно производительность процесса, силы шлифования, качество обработанной поверхности и т.д. Режущая способность инструмента оценивалась коэффициентом режущей способности Q . Предварительные исследования зависимости коэффициента режущей способности от объема сошлифован-ного материала показали, что эта зависимость может быть описана уравнением
Q = aen(w)1/2;   (16)
где a - постоянный коэффициент, значение которого соответствует значению коэффициента режущей способности круга в исходном состоянии, коэффициент n характеризует скорость падения режущей способности по мере сошлифовывания припуска.
Для каждого сочетания режимов обработки v, s, t (интервалы варьирования прежние) определялось значение a и n методом наименьших квадратов. Можно предположить, что режимы обработки оказывают влияние только на величину коэффициента n, так, как значение коэффициента a определяется способом восстановления режущей способности инструмента. Поэтому зависимость (17) можно представить в виде
Q = Qисх.e(-0,0227-0,00074V-0.0044S-0.0045t+0.0025St)(w)1/2;   (17)
где Qисх- значение коэффициента режущей способности в исходном состоянии инструмента.
Для определения зависимости n от режимов обработки v, S , t был применен метод статистической обработки полного факторного эксперимента. В качестве математической модели принята зависимость
n = n0 +n1x1 + n2x2 + n3x3 + n12x1x2 + n13x1x3 + n23x2x3 + n123x1x2x3;   (19)
После определения коэффициентов регрессии ni в уравнении (19) и оценки их значимости была установлена зависимость коэффициента режущей способности алмазного инструмента и объема сошлифованного материала:
Q = Qисх.en(w)1/2;   (20)
Исследование качественных показателей обработанной поверхности по параметру шероховатости. Эксплуатационные характеристики изделий из технического стекла и хрусталя во многом определяются показателями качества обработанной поверхности. На данном этапе качество формируемой поверхности оценивалось уровнем ее шероховатости Ra. Экспериментально исследовалось влияние режимов обработки и объема сошлифованного материала на параметр Rа. Для этой цели использовался статистический метод планирования эксперимента. Варьируемые параметры и их значения принимались такими же, как и в предыдущих исследованиях. В качестве математической модели, описывающей связь шероховатости с режимами обработкиt принята зависимость
Ra = A + BV + CS + Dt ; (22)
где А - значение шероховатости при v, S, t, равных 1; B, С, D - коэффициенты при варьируемых параметрах.
Эта зависимость может быть представлена уравнением регрессии в виде полинома
y = b0 + b1x1 + b2x2 + b3x3 + b12x1x2 + b13x1x3 + b23x2x3 + b123x1x2x3;(23)
где b0 - значение шероховатости при кодированных параметрах X1, X2, X3, равных 0.
bi- коэффициенты регрессии при варьируемых параметрах.
В результате обработки экспериментальных данных было установлено, что все коэффициенты регрессии за исключением 4 оказались незначимыми.
Зависимость (22) приобретает вид
Ra = b0;
b0 зависит от зернистости алмазного круга, так для круга зернистости 250/200
Ra = 5,1 мкм .
Для проверки полученного результата была принята другая математическая модель шероховатости обработанной поверхности
Ra=CRa.VnRa.SyRa.txRa;(25)
В результате вычисления коэффициентов, оказалось, что зависимость Ra от S , v, t принимает вид (24), т.е. режимы шлифования не оказывают практического влияния на шероховатость обработанной поверхности. Гипотеза адекватности моделей подтверждена результатами статистической обработки данных эксперимента.
Исследования зависимости шероховатости обработанной поверхности от степени затупления круга, определяемой объемом сошлифо-ванного материала, показали, что она может быть описана уравнением
Ra = Raoekw (26)
где Ra0 - шероховатость обработанной поверхности в исходном состоянии круга;
К - коэффициент, характеризующий скорость уменьшения шероховатости по мере затупления круга.
Как показано выше, Ra0 не зависит от режимов обработки, а определяется зернистостью алмазно-абразивного инструмента. Можно предположить, что коэффициент К будет изменяться в зависимости от значений V , S и t . Для всех сочетаний варьируемых параметров V, S и t (план 23) по мере затупления круга измерялась шероховатость обработанной поверхности. Для каждого цикла затупления методом наименьших квадратов определялись Ra0 и К . Для получения зависимости коэффициента К от режимов обработки использовался метод планирования эксперимента. Оценка полученных коэффициентов регрессии показала, что все они за исключением b0 незначимы. Таким образом, зависимость шероховатости обработанной поверхности от объема сошлифованного материала в исследуемом диапазоне режимов обработки может быть описана уравнением
Ra = b0e-4.04*10-4w(27)
Зависимость Ra=f(W) графически представлена на рис..
Экспериментально установлено, что изменение ширины шлифовального круга несущественно сказывается на величине Rа . Зернистость шлифовального круга влияет на величину коэффициента b0, величина которого уменьшается с уменьшением размера зерна алмазов.
Технологическая среда практически не влияет на значение шероховатости обработанной поверхности.
Экспериментальное исследование износа алмазно-абразивного инструмента. Износ алмазного инструмента в процессе шлифования, скорость изменения этого выходного параметра технологического процесса во времени свидетельствует об условиях протекания
процесса обработки, являясь поэтому важным показателем его эффективности.
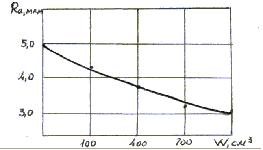
Рисунок 3.- Зависимость шероховатости обработанной поверхности от объема сошлифованного материала припуска. Шлифование технического стекла кругом зернистости 250/200 с режимами шлифования v=32,9 м/с,S=2,5 м/мин, t=1.3 мин
В процессе экспериментальных исследований определялась зависимость износа алмазных кругов (Vp) от объема сошлифованного материала (W) для условия установившегося износа. При этом было сделано предположение, что зависимость Vp=f(W) имеет линейный характер и может быть описана уравнением
Vp=AW +C,    (28)
где С - коэффициент, учитывающий величину износа круга к моменту наступления установившегося характера износа, то есть, по окнчании периода приработки круга после его правки; A- коэффициент, характеризующий скорость роста износа инструмента в зависимости от величины съемов.
При вариации режимов шлифования на уровнях, идентичных описанным ранее, измерялся линейный износ алмазного круга в зависимости от величины объемов сошлифованного материала и для каждого сочетания режимов обработки v, S, t определялись значения коэффициентов А и С. Экспериментально было доказано, что характер полученных зависимостей совпадает с прогнозируемым. На рис. 2.3 представлена одна из экспериментально полученных зависимостей Vp=f(W) o Износ инструмента берется на радиус круга.
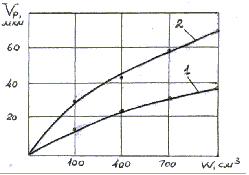
Рисунок 4.- Зависимость износа алмазно-абразивного инструмента от величины съема сошлифованного материала. Шлифование технического стекла кругом зернистости 25/200 с режимами: 1- v= 18,6 м/с; s= 6,0 м/мин;
t= 1,3 мм; 2 - v= 18,6 м/с; s=2,5 м/мин;
t = 3,6 мм
С использованием статистических методов обработки результатов факторного эксперимента была найдена зависимость коэффициентов Д и С от режимов шлифования. На основании обобщения полученных данных была выведена комплексная зависимость (2.2,9), учитывающая влияние на величину износа алмазно-абразивного инструмента таких параметров процесса шлифования, как режимы шлифования, объем сошлифованного материала, ширина и зернистость инструмента
Формула (29 ) получена для условий шлифования технического стекла в среде воды. Влияние поверхностно-активной СОЖ на величину износа может быть учтена величиной постоянного коэффициента. Поверхностно-активные СОЖ, изменяя физико-механические характеристики материала, облегчают условия его диспергирования, что приводит к снижению износа инструмента. В среднем, за счет использования активных сред величина износа снижается на 20%. Приведенная формула для подобных условий примет вид