Главная страница
Электронная библиотека
Аннотированные ссылки
Результаты поиска
Индивидуальное задание
Автореферат магистерской работы
Авраменко Сергея Владимировича
Тема магистерской работы:
"Разработка технологического обеспечения автоматизации сборки конвейерных роликов в условии ОАО "ГОРМАШ""
Руководитель: Богуславский В. А.
факультет: механический
1 Вводная часть
1.1 Актуальность работы
Автоматизация современных производственных процессов является одним из важнейших путей повышения производительности труда и экономической эффективности производства. Любые новые неавтоматизированные технологические процессы и оборудование на современном этапе развития промышленности должны рассматриваться как частное, вынужденное решение, когда в конкретных условиях производство еще не созрели технические и технологические предпосылки для его автоматизации. При современном уровне научно-технического прогресса основной формой производства становится комплексно-автоматизированное и высокомеханизированное оборудование и производство. Одна из основных закономерностей развития техники на современном этапе развития заключается в том, что автоматизация проникла во все отрасли техники, во все звенья производственного процесса, вызвала в них революционные, качественные изменения.
Технологические процессы массового производства имеют ряд особенностей, которые проявляются при проектировании технологий. Среди этих особенностей малая номенклатура выпускаемых изделий, наибольшая программа выпуска, автоматическое достижение точности размеров на настроенных станках. Применение технологических процессов массового производства требует наименьшей себестоимости единицы изделия по сравнению с изготовлением аналогичных изделий в других видах производства. Это достигается за счет применения специальных и специализированных станков и оборудования, технологической оснастки, инструмента; более тщательной проработки технологической документации; широкое применение многостаночного обслуживания.
Повышение нестабильности рынка, усиление конкурентной
борьбы за потребителя между производителями, практически
неограниченные возможности научно-технического прогресса привели к
частой сменяемости продукта. Главным фактором в конкурентной борьбе
стал фактор времени. Фирма, которая может за короткий срок довести
идею до промышленного освоения и предложит потребителю
высококачественный и относительно дешевый товар, становится
победителем.
Быстрая сменяемость продукции и требования ее
дешевизны при высоком качестве приводит к противоречию:
— с
одной стороны, низкие производственные издержки (при прочих равных
условиях) обеспечиваются применением автоматических линий,
специального оборудования;
— но с другой стороны, проектирование
и изготовление такого оборудования нередко превышают 1,5 — 2 года
(даже в настоящих условиях), то есть к моменту начала выпуска
изделия оно уже морально устареет.
Применение же универсального
оборудования (неавтоматического) увеличивает трудоемкость
изготовления, то есть цену, что не приемлется рынком.
Такая
ситуация возникла в 60-х годах нашего столетия и, естественно, перед
станкостроительными фирмами стала задача создания нового
оборудования, которое бы удовлетворяло следующим требованиям:
—
универсальности, то есть легкой переналаживаемости (функциональной
инвариантности);
— автоматизации;
— автоматической
переналаживаемости по команде с управляющей вычислительной машины
(УВМ);
— встраиваемости в автоматические линии и комплексы;
— высокой точности;
— высокой надежности;
—
автоматической подналадки (корректировки) инструмента в процессе
выполнения операции и т.д.
И такое оборудование было создано. К
нему относятся:
— "обрабатывающие центры" механической обработки
с УВМ (с многоинструментальными магазинами (до 100 и более
инструментов), с точностью позицирования изделия относительно
инструмента 0,25 мкм, с "умными супервизорами" функционирования всех
систем, с активным контролем и автоматической подналадкой
инструмента);
— промышленные роботы с программным управлением
как универсальное средство манипулирования деталями,
универсально-транспортные погрузочно-разгрузочные средства, а также
переналаживаемые роботы-маляры, роботы-сварщики, роботы-сборщики и
т.д.;
— лазерные раскройные установки, заменяющие сложнейшие
комплексы холодной штамповки, которые сами определяют оптимальный
раскрой материалов;
— термические многокамерные агрегаты, где в
каждой отдельной камере производится термообработка или
химико-термическая обработка по заданной программе;
—
высокоточные трехкоординатные измерительные машины с программным
управлением (на гранитных станинах, с износостойкими (алмазными,
рубиновыми) измерителями);
— лазерные бесконтактные
измерительные устройства и т.д.
Этот список можно продолжать
довольно долго. На базе перечисленного оборудования созданы:
—
вначале гибкие производственные модули ГИМ (обрабатывающий центр,
робот-манипулятор, автоматизированный склад, УВМ);
— затем ГИК —
гибкие интегрированные комплексы и линии;
— гибкие
интегрированные участки, цехи, производства, заводы.
При
создании гибкой производственной системы происходит интеграция:
— всего разнообразия изготовляемых деталей в группы обработки;
—оборудования;
— материальных потоков (заготовок, деталей,
изделий, приспособлений, оснастки, основных и вспомогательных
материалов);
— процессов создания и производства изделий от идеи
до готовой продукции (происходит слияние воедино основных,
вспомогательных и обслуживающих процессов производства);
-
обслуживания за счет слияния всех обслуживающих процессов в единую
систему;
— управления на основе системы УВМ, банков данных,
пакетов прикладных программ, САПР, АСУ;
— потоков информации для
принятия решения по всем подразделениям системы о наличии и
применении материалов, заготовок, изделий, а также средств
отображения информации;
— персонала за счет слияния профессий
(конструктор-технолог-программист-организатор).
В результате
системы ГИП имеют следующие структурные составные части:
—
автоматизированную транспортно-складскую систему (АТСС);
—
автоматическую систему инструментального обеспечения (АСИО);
—
автоматическую систему удаления отходов (АСУО);
—
автоматизированную систему обеспечения качества (АСОК);
—
автоматизированную систему обеспечения надежности (АСОН);
—
автоматизированную систему управления ГПС (АСУ ГПС);
— систему
автоматизированного проектирования (САПР);
— автоматизированную
систему технологической подготовки производства (АСТПП);
—
автоматизированную систему оперативного планирования производства
(АСОПП);
— автоматизированную систему содержания и обслуживания
оборудования (АССОО);
— автоматизированную систему управления
производством (АСУП).
ования (АССОО);
— автоматизированную систему управления производством (АСУП).
НПП «Конвейер»
1.2 Цель и задачи исследований
 Цель работы: повышение эффективности и качества производства роликов, на основе разработки структурного и технологического обеспечения, а также создание нового способа сборки и производства роликов.
Для этого выполняются следующие пункты:
1. Аналитический обзор современного состояния вопроса исследования.
Цель и задачи работы
2. Исследование и разработка технологического процесса производства роликов
2.1 Технологический процесс производства оси
2.1.1Расчет и выбор припусков на механическую обработку
2.1.2 Разработка маршрутного технологического процесса
2.1.3 Разработка операционного технологического процесса
2.1.4 Выбор и анализ выбранного оборудования
2.1.5 Выбор и анализ выбора баз с расчетом погрешности базирования
2.1.6 Выбор и анализ выбора приспособления
2.1.7 Выбор и анализ выбора режущего инструмента
2.2Технологического процесса производства обечайки, стакана, лабиринтных уплотнений
2.3 Выводы
3.Исследование возможности модернизации
фрезерно-центровального станка в технологическом процессе производства оси
3.1 Модернизация станка
3.1.1 Модернизация коробки скоростей
3.1.2 Модернизация коробки подач
3.2 Проектирование специальной оснастки на токарную операцию
3.2.1 Разработка специального зажимного приспособления
3.2.1.1 Разработка конструкции
3.2.1.2 Расчет на точность и прочность
3.2.2 Разработка специальных резцовых головок для токарной обработки
3.2.2.1 Разработка конструкции
3.2.2.2 Расчет на жёсткость и прочность
3.3 Контрольное приспособление
Определение напряженного состояния элементов
конструкции технологического модуля в системе ANSYS
4. Разработка технологического процесса сборки ролика
4.1 Разработка технологического процесса сборки ролика
4.2 Разработка оснастки сборки
4.2.1 Приспособление для держания оси
4.2.2 Приспособление для запрессовки подшипников
5. Выбор конструктивной схемы автоматической линии сборки ролика
5.1 Разработка циклограммы работы автоматической линии
5.2 Выбор манипуляторов и его обоснование
5.3 Определение производительности реальной автоматической линии
5.4 Разработка целевого механизма
6.1 Расчет экономического эффекта внедрения автоматической линии сборки
  Основной проблемой поставленной в данной работе, является решение вопроса автоматизации при реальных условиях нынешней жизни предприятий.
Производится разработка автоматической линии сборки которая до нынешнего момента является ручной...
Рисунок 1. Сборка конвейерного ролика в анимации
2 Основная часть
Исследование вопроса расчёта поточной линии
ПОТОЧНЫЕ ЛИНИИ
При проектировании и организации поточных линий
выполняются расчеты показателей, определяющих регламент работы линии
и методы выполнения технологических операций.
Такт поточной
линии — промежуток времени между выпуском изделий (деталей,
сборочных единиц) с последней операции или их запуском на первую
операцию поточной линии.
Исходные данные расчета такта:
- производственное задание на год (месяц, смену);
-
плановый фонд рабочего времени за этот же период;
- планируемые
технологические пооперационные потери.
Такт поточной линии
рассчитывается по формуле
r = Fд / Qвып,
где r —
такт поточной линии (в мин.);
Fд — действительный годовой фонд
времени работы линии в планируемом периоде (мин.);
Qвып —
плановое задание на тот же период времени (шт.).
Fд = Dраб Х
dсм Х Tсм Х kпер Х kрем,
где Dраб — число рабочих дней в
году;
dсм — количество рабочих смен в сутки;
Tсм —
продолжительность смены (в мин.);
kпер — коэффициент,
учитывающий планируемые перерывы;
kрем — коэффициент,
учитывающий время плановых ремонтов.
kпер = (Тсм - Тпер) /
Тсм,
где Тпер — время планируемых внутрисменных перерывов;
kрем — рассчитывается аналогичным способом.
Признаки
поточного производства:
- закрепление одного или
ограниченного числа наименований изделий за определенной группой
рабочих мест;
- ритмическая повторяемость согласованных во
времени технологических и вспомогательных операций;
-
специализация рабочих мест;
- расположение оборудования и
рабочих мест по ходу технологического процесса;
- применение
специальных транспортных средств для межоперационной передачи
изделий.
При поточном производстве реализуются принципы:
- специализации;
- параллельности;
- пропорциональности;
- прямоточности;
- непрерывности;
- ритмичности.
Поточное производство обеспечивает самую высокую
производительность труда, низкую себестоимость продукции, наиболее
короткий производственный цикл.
Основой (первичным звеном)
поточного производства является поточная линия.
Расположение
поточных линий (планировка) должна обеспечить:
-
прямоточность и кратчайший путь движения изделия;
- рациональное
использование производственных площадей;
- условия для
транспортировки материалов и деталей к рабочим местам;
-
удобство подходов для ремонта и обслуживания;
- достаточность
площадей и оргоснастки для хранения требуемых запасов материалов и
готовых деталей;
- возможность легкого удаления отходов
производства.
Основы расчета и организации поточных линий
При проектировании и организации поточных линий выполняются расчеты
показателей, определяющих регламент работы линии и методы выполнения
технологических операций.
Такт поточной линии — промежуток времени между выпуском изделий
(деталей, сборочных единиц) с последней операции или их запуском на первую
операцию поточной линии.
Исходные данные расчета такта:
- производственное задание на год (месяц, смену);
- плановый фонд
рабочего времени за этот же период;
- планируемые технологические
пооперационные потери.
Такт поточной линии рассчитывается по формуле
r = Fд / Qвып,
где r — такт поточной линии (в мин.);
Fд — действительный
годовой фонд времени работы линии в планируемом периоде
(мин.);
Qвып — плановое задание на тот же период времени
(шт.).
Fд = Dраб Ч
dсм Ч Tсм Ч kпер Ч
kрем,
где Dраб — число рабочих дней в году;
dсм —
количество рабочих смен в сутки;
Tсм — продолжительность
смены (в мин.);
kпер — коэффициент, учитывающий планируемые
перерывы;
kрем — коэффициент, учитывающий время плановых
ремонтов.
kпер = (Тсм - Тпер) /
Тсм,
где Тпер — время планируемых внутрисменных
перерывов;
kрем — рассчитывается аналогичным способом.
Классификация поточных линий приведена в табл. 7.4
Таблица 7.4
Классификация поточных линий
№ п/п |
Признак |
Характеристика |
1 |
Степень механизации технологических операций |
1.1. Механизированные 1.2.
Комплексно-механизированные 1.3. Полуавтоматические 1.4.
Автоматические 1.5. Гибкие интегрированные |
2 |
Количество типов одновременно обрабатываемых и
собираемых изделий |
2.1. Однономенклатурные (обработка изделия одного
наименования) 2.2. Многономенклатурные (обработка изделий
нескольких наименований одновременно или последовательно) |
3 |
Характер движения изделий по операциям производственного
процесса |
3.1. Непрерывно-поточные (все операции синхронизированы во
времени, т.е. равны или кратны такту линий) 3.2.
Прерывно-поточные (перерывы в ходе производственного процесса и
невозможность синхронизировать технологические операции во времени)
|
4 |
Характер работы конвейера |
4.1. С рабочим конвейером, когда операции выполняются без снятия
изделия с конвейера 4.2. С распределительным конвейером, когда
конвейер осуществляет доставку изделия на рабочее место, а операция
выполняется со снятием изделия с конвейера 4.3. С непрерывно
движущимся конвейером 4.4. С пульсирующим конвейером
|
При неизбежных технологических потерях (планируемом выходе годных),
такт r рассчитывается по формуле
r = Fд / Qзап,
где Qзап — количество изделий, запускаемых на поточную линию
в планируемом периоде (шт):
Qзап = Qвып Ч kзап,
где kзап — коэффициент запуска изделий на поточную линию,
равный величине, обратной коэффициенту выхода годных изделий (a); kзап = 1/a.
Выход годных изделий в целом по поточной линии определяется как
произведение коэффициентов выхода годных по всем операциям линии
a = a1
Ч a2 Ч ... Ч an.
Ритм — это количество изделий, выпускаемых поточной линией в
единицу времени.
Расчет количества оборудования поточной линии ведется по каждой операции технологического процесса:
или
,
где
— расчетное количество оборудования (рабочих мест) на i-й операции
поточной линии;
tштi — норма штучного времени на i-ую
операцию (в мин);
kзапi — коэффициент запуска детали на i-ю
операцию.
Принятое количество оборудования или рабочих мест на каждой
операции Wпi определяется путем округления расчетного их
количества
до ближайшего большего целого числа.
Коэффициент загрузки оборудования (рабочих мест) определяется как
.
Количество оборудования (рабочих мест) на всей поточной линии
,
где чоп — число операций технологического процесса.
Явочное количество рабочих (Ряв) равно количеству
рабочих мест на поточной линии с учетом многостаночного обслуживания:
,
где kмо — коэффициент многостаночного обслуживания;
,
где S Рi — численность рабочих
участка.
Общее число рабочих на поточных линиях определяется как
среднесписочное:
,
где Рсп — среднесписочное число рабочих поточной
линии;
d — процент потерь рабочего времени
(отпуска, болезни и т.д.);
dсм — количество смен.
Скорость движения конвейера (V):
- при непрерывном движении конвейера V=L / r;
- при пульсирующем
движении конвейера V= L/ tтp,
где L — расстояние между центрами двух смежных рабочих мест, то есть
шаг конвейера (м);
tтp — время транспортировки изделия с
одной операции на другую.
Задел — производственный запас материалов, заготовок или
составных частей изделия для обеспечения бесперебойного протекания
производственных процессов на поточных линиях.
Различают следующие виды заделов:
- технологический;
- транспортный;
- резервный (страховой);
-
оборотный межоперационный.
Технологический задел (Zт) — детали (сборочные
единицы, изделия), находящиеся непосредственно в процессе обработки:
,
где
— число рабочих мест на каждой операции;
ni — количество
деталей, одновременно обслуживаемых на i-м рабочем месте.
Транспортный задел (Zтр) — количество деталей,
находящихся в процессе перемещения между операциями и расположенных в
транспортных устройствах.
При непрерывном движении конвейера
Zтр =LркР / V,
где Lрк — длина рабочей части конвейера (м);
V — скорость
движения конвейера (м/мин);
Р — количество изделий в операционной
партии (шт).
При периодической транспортировке
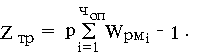
Транспортный технологический заделы зависят от параметров оборудования,
тех. процессов.
Резервный (страховой) задел создается для нейтрализации
последствий, связанных со случайным характером выхода изделия в брак,
перебоев в работе оборудования и др.
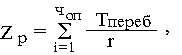
где Тпереб — время возможного перебоя поступления изделий с
данной операции на операцию, подлежащую страхованию (мин);
r — такт
поточной линии (мин).
Оборотный межоперационный задел на линии — количество заготовок
(деталей, сборочных единиц), находящихся между операциями линии и
образующихся вследствие различной производительности смежных рабочих мест
для выравнивания работы линий. Размер межоперационного задела постоянно
колеблется от максимума до нуля и наоборот. Максимальная величина
межоперационного оборотного задела определяется разностью
производительностей смежных операций:
,
где Тсовм — время совместной работы оборудования на обеих
операциях (в мин);
— количество оборудования на подающих и потребляющих смежных операциях,
работающего в период Тсовм (шт);
tштi — норма
времени выполнения операции.
Синхронизация — процесс выравнивания длительности операции
технологического процесса согласно такту поточной линии. Время выполнения
операции должно быть равно такту линии или кратно ему.
Методы синхронизации:
- дифференциация операций;
- концентрация операций;
- установка
дополнительного оборудования;
- интенсификация работы оборудования
(увеличение режимов обработки);
- применение прогрессивного инструмента
и оснастки;
- улучшение организации обслуживания рабочих мест и
т.д.
3 Заключение
Таким образом, раскрыта тема магистерской работы, приведены её цели и основные задачи, а также показана актуальность магистерской работы. Произведен обзор существующих исследований и разработок. Приведены результаты некоторых теоретических исследований по вопросам повышения эффективности и качества автоматизированной сборки.
ПЕРЕЧЕНЬ ССЫЛОК
1. Буда Я.,Гановский В. Автоматизация процессов машиностроения. - М.: Машиностроение, 1991.
2. Ковальчук Е.Р., Косов М.Г. Основы автоматизации машиностроительного производства. - М.: Машиностроение, 1999.
3. Лебедовский М. С., Вейц В. Л., Федотов А. И. Научные основы автоматической сборки. - Л.: Машиностроение, 1985. - 316 с.
4. НПП «Конвейер»
5.Непомнящий Е_Г_ Экономика и управление предприятием Производственный процесс и типы производств