гибкая.
Эти этапы взаимосвязаны и неотделимы между собой. В общем случае сборка- это часть технологического процесса изготовления изделия, которым заканчиваются работы по соединению отдельных деталей в узлы [2,3,4,5]. Однако теоретических основ их применения для большинства сборочных операций не существует для разработки таких основ необходимо исследовать общие характеристики сборочного процесса и его трудоемкость.
Доля сборочных работ разная (рис. 1) в различных отраслях машиностроения и ее можно представить в виде следующей диаграммы (в процентах от общей трудоемкости изготовления машин и приборов).
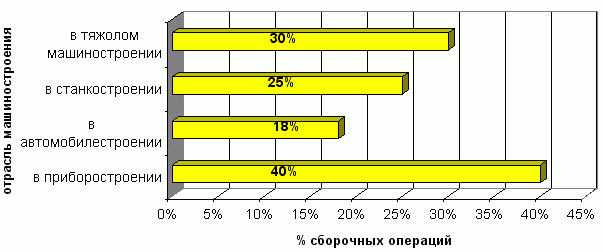
Рисунок 1 – Диаграмма распределения трудоемкости по типам производства [5]
Трудоемкость сборочных работ в машиностроении занимает второе место после механической обработки и составляет в среднем от 20-70% [3,5,6] от трудоемкости изготовления изделий. В настоящее время увеличиваются трудозатраты на сборку [1] , это объясняется общими трудностями и проблемами экономического развития Украины, а также специфическими особенностями механизации и автоматизации сборочных процессов. Например. В машиностроении механизировано, как и 20 лет назад , только около 25% [7] сборочных операций и значительно менее 6% [6,7] автоматизировано. Весьма эффективным путем снижения трудоемкости сборочных работ для массового и крупносерийного производства является применение технологической оснастки на основе агрегатирования сборочного оборудования [6,7]. Пользуясь этим принципом, удается создавать самые разнообразные сборочные приспособления.
Таким образом, тип производства оказывает решающее влияние на организацию сборочных работ, на разработку технологических процессов.
Основная часть сборочных работ выполняется на общей сборке и лишь малая их доля осуществляется над отдельными сборочными единицами с увеличением серийного производства сборочные работы все больше раздробляются по отдельным сборочным единицам, объем узловой сборки становиться равной общей сборки, что способствует механизации и автоматизации сборочных работ [4].
Для условий единичного и мелкосерийного производства, доля продукции которого в общем, объеме выпуска машиностроительных изделий наибольшая, а уровень механизации слесарных работ весьма низкий. В качестве примера на рис. 2 представлена трудоемкость слесарно-сборочных работ по различным видам производимого оборудования на предприятиях тяжелого машиностроения [8].
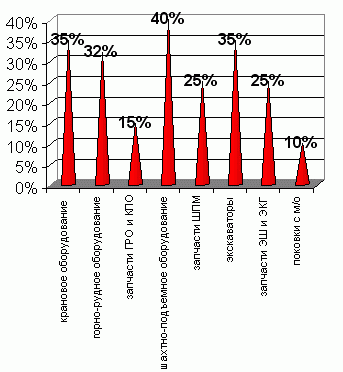
Рисунок 2 – Диаграмма распределения трудоемкости сборочных работ
Специфика сборки машин, из-за частой смены номенклатуры изделий, характеризуется трудностями механизации и автоматизации, и это требует применение широкоуниверсальных технологических средств. Однако при их применении на конкретных технологических операциях реализуется небольшой процент их технологических и технических возможностей. Для производства в условиях рыночной экономики номенклатуры деталей изготовляемых на протяжении календарного года, предприятие вынуждено иметь заведомо избыточный набор технологических средств, некоторая часть которых может оказаться невостребованной. Таким образом, необходимость изготовления деталей широкой номенклатуры небольшими по размерам партиями и определенная непредсказуемость номенклатуры деталей вынуждает предприятие иметь большое разнообразие технологических средств заведомо избыточных как по составу и количеству, так и по технологическим и техническим возможностям [9]. Недостаточная специализация низкий уровень унификации и стандартизации, малая изученность процесса приводит к низкой собираемости сборочных единиц –явлению, когда сборка сопровождается весьма значительным объемом пригоночно-доделочных работ, трудоемкость которых превышает трудоемкость собственно сборочных операций.
Сложившуюся структуру сборочного процесса изделий единичного и мелкосерийного производства целесообразно представить на основе группирования по видам работ, объединяющим слесарно-сборочные операции выполнение которых определяется однородностью и однотипностью решаемых технологических задач[8]:
1) слесарно-доделочные работы (зачистка заусенцев, опыливание, сверление отверстий, нарезание резьбы и пр.);
2) пригоночно-поводочные работы (пригонка поверхностей, непредусмотренная технологическим процессом сборки, а также «нормальные» пригоночно-доводочные операции, предусмотренная ТУ на сборку;
3) слесарно-вспомогательные работы (изготовление прокладок, пружин, шайб и других деталей);
4) балансировка деталей и сборочных единиц;
5) собственно-сборочные работы;
6) обкатка и испытание сборочных единиц и изделий;
7) разборка и демонтаж изделия;
8) консервация и упаковка.
Доля трудоемкости сборки прокатного оборудования по сравнению с механической обработкой возросла в полтора раза. Это свидетельствует об относительно низких темпах совершенствования сборочных процессов, который определяется недостаточными масштабами проектирования и внедрения прогрессивных технологических процессов, механизации и автоматизации, методов размерной отработки конструкции сборочных единиц и рациональной организации сборки изделий. В этих условиях особую актуальность приобретают вопросы анализа и оценки технического уровня сборочного производства, а также на основе количественной оценки значимости основных факторов наметить комплекс мероприятий по совершенствованию процессов сборки и сокращению трудоемкости сборочных работ. А разработать такой комплекс можно, изучив особенности классификации видов сборки различных соединений. По сохранению целостности при сборке соединения подразделяются на разъемные и неразъемные [2,3,4,5]. Количество разъемных соединений в современных машинах и механизмах составляет 65-85% от всех соединений. Для общего машиностроения число соединений указанных видов можно выделить соотношением: