Анализ существующих автоматических роторных линий сборки
показал, что наиболее распространёнными и относительно простыми являются те
линии, в которых на вход обычно подаётся набор (комплект) деталей или изделий,
хотя это уменьшает число струй роторной линии и снижает производительность на
выходе роторных машин по сравнению с производительностью первого ротора. Более
разнообразные схемы характерны для сборки (монтажа), при которой на вход линии
подаётся поток базовых деталей, разделяемый на U струй, а собираемые детали
поступают в технологически установленной последовательности. Детали различных
номенклатур могут подаваться также поштучно или порциями (например, при
изготовлении армированных изделий из пластмасс).
Сборочные роторные машины (рис.1) предназначены для
механического объединения нескольких элементов в единое целое, т.е. для
сопряжения (навивка, ввинчивание, обмотка, вставка, заливка и т.д.) и крепление
элементов деталей (сварка, связывание, сшивание, завальцовка, обжим, пайка,
клёпка, гибка и др.) с обеспечением требуемой точности, надёжности соединения,
определённого взаимного расположения деталей. Такие машины имеют несколько
входов и один выход.
Рисунок 1 - Типовая единичная группа автоматической роторной
линии для сборки двух деталей:
а-схема, б-проекция движения потока предметов
труда на горизонтальную плоскость.
1 - блок нижней системы привода сборочного ротора; 2 - ползуны
нижнего привода; 3 - нижний шток инструментального блока; 4 - нижний диск
транспортного (загрузочного) ротора; 5 - собираемые элементы; 6 - клещевые
захваты; 7 - верхний диск транспортного (загрузочного) ротора; 8 - вал
транспортного ротора;9 - блок верхней системы привода сборочного ротора; 10 -
зубчатая передача транспортного вращения роторов; 11 - верхняя часть станины; 12
- торцовый кулачок верхней системы привода; 13 - ползун верхней системы
привода;14 - пазовый кулачок верхней системы привода; 15 - блокодержатели; 16 -
собранные детали;17 - инструментальный блок; 18 - нижняя часть станины;19 -
основной вал сборочного ротора.
Сборочные машины, предназначенные для объединения нескольких
одинаковых деталей или элементов в едином корпусе или упаковке, т.е. для
выполнения операций комплектации, также имеют несколько входов и один выход.
Наличие подпотоков влияет на плотность потока комплектуемой продукции. При
пропусках наблюдаются недоукомплектованные потоки.
По основному технологическому назначению различают сборочные
роторы: для выполнения сборочных операций, требующих вращательного и
поступательного осевого движения (навивка, ввинчивание и т.п.); для выполнения
сборочных операций, требующих вращательного и поступательного радиального
движения (обмотка, завальцовка и т.п.); для выполнения сборочных операций,
требующих одного поступательного движения (запрессовка, клёпка, гибка, вставка и
т.п.).
По числу позиций в одном инструментальном блоке сборочные
роторы могут иметь одну сборочную (комплектующую) позицию или две и более
позиций.
2.2 Разработка технологического процесса сборки гидрозамка
В гидросистемах и гидропередачах широко распространены
гидрозамки, служащие для запирания поршней гидроцилиндров в фиксированном
положении при отсутствии подачи жидкости от питающей установки. Гидрозамки
одностороннего действия чаще всего применяют в горной практике для запирания
поршневых полостей стоек гидрокрепей при распоре их между почвой и кровлей
выработки и для отпирания при загрузке. При повышении давления в одной из
внешних гидролиний управляющий поршень смещается в сторону меньшего давления и
открывает клапан, обеспечивающий слив жидкости из полости гидроцилиндра, в
сторону которой должен начать смещаться его поршень. Таким образом, блокировка
гидроцилиндра снимается.
Рассмотрим автоматизацию сборки
гидрозамка КГУ3.020ПР-01,
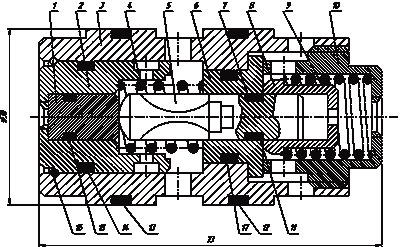
Рисунок 2 - Сборочный чертёж гидрозамка
КГУ3.020ПР-01
используемого в секциях шахтных крепей КМТ, 1КД80, на
автоматической роторной линии. В настоящее время сборка данного гидрозамка
осуществляется с помощью частично механизированного и частично
автоматизированного ручного труда. Так, автоматизированной частью сборки
гидрозамка является сборка резинового кольцевого уплотнения 5 и цилиндрической
детали - толкателя 10[8].
Гидрозамок односторонний состоит из таких деталей, как
корпус, поршень, толкатель, втулка и золотник, комплектуемые совместно с
прокладками и кольцами, также в состав изделия входит 2 цилиндрические пружины,
втулка (без уплотнительного кольца) и гайка. Перед сборкой все детали необходимо
промыть, чтобы их чистота соответствовала требованиям. К гидрозамку
предъявляются высокие требования, следовательно, необходимо соблюдать такие
положения, как: резиновые и защитные кольца и место их установки необходимо
смазывать маслом И-20А ГОСТ 20799-75, не допускается их перекручивание и
повреждение; при сборке гайку заворачивать моментом не менее 50Нм до
упора.
Сборка данного изделия производится в следующем порядке. В
корпус 4, на который одеты два резиновых кольца 17, вставляется предварительно
собранный сборочный узел, состоящий из поршня 1 с уплотнительным кольцом 16 и
толкателя 10 с кольцом; в канавку между корпусом и поршнем вставляется стопорное
кольцо 2. Далее производится вставка в полученную сборочную единицу пружины 8.
Втулка 11 совместно с кольцом 15 устанавливается в корпус до упора, а потом
золотник 6 совместно с резиновым кольцом 14 и прокладкой 5 устанавливается в
данный сборочный узел до резинового кольца. Затем последовательно вставляется
втулка 7, пружина 12 и закручивается гайка 9 до упора.
Рисунок 3- Процесс сборки гидрозамка КГУ3.020.ПР-1
(Для просмотра анимации подведите к рисунку курсор мыши)
Технологический процесс сборки представляется в виде графа (рис 4):
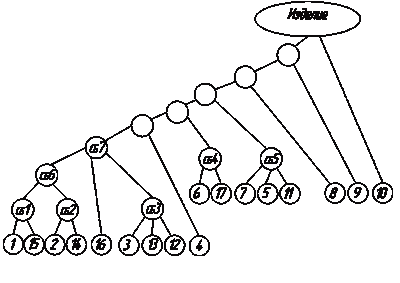
Рисунок 4 - Технологический процесс сборки гидрозамка
На основании данного технологического процесса сборки
составлена автоматическая роторная линия сборки данного изделия согласно
принципам [1,7](рис.3).

Рисунок 5 - Схема автоматической роторной линии сборки
гидрозамка:
ЗР - ротор загрузки; ТР - технологический ротор; ТрР -
транспортный ротор
2.3 Разработка приспособления для вставки стопорного кольца в корпус
Главной задачей данной магистерской работы является
проектирование роторной машины для реализации автоматической сборки
металлического стопорного кольца и корпуса гидроцилиндра. На данный момент
конструкция самой роторной машины ещё в стадии доработки, но она будет
реализована на основании существующих принципов построения роторов (см. типовую
конструкцию сборочных роторов). Но мною уже разработан новый способ сборки
кольца и корпуса и схема инструментального блока технологического ротора (см.
рисунок 6).
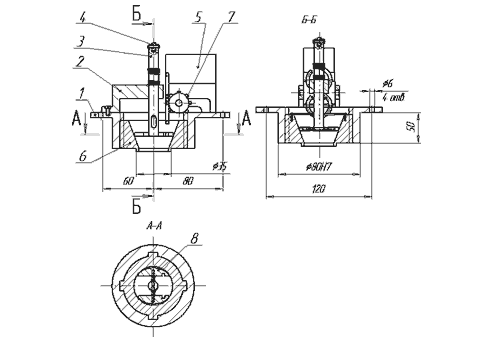
Рисунок 6 - Схема приспособления для вставки стопорного кольца в корпус
Приспособление состоит из:
1. Корпус
2. Стойка
3. Толкатель
4. Ролик
5. Магазин с кольцаци
6. коническая матрица
7. Шаговый податчик колец
8. Разрезной пуансон
Процесс сборки происходит следующим образом . В приспособ роторе коническая
матрица 6 закреплена подвижно с толкателем посредстров пластинчатой пружины, что дает им в какой-то степени возможность независимо двигаться.Шаговым податчиком выдается из магазина кольцо, оно попадая в прорезь между разрезным пуансоном попадает в коническую матрицу под определенным углом (Силы тяжести кольца разворачивают его по отношению к нормали конуса матрицы на прямой угол).Ролик 4 двигаясь по копиру двигает толкатель, а он в свою очередь пуансон и кольцо. Кольцо двигаясь вместе с матрицей подходит к корпусу. После того как матрица упрется в корпус начинает сжиматься кольцо, до тех пор пока не выйдет из приспособления и не установится в корпусе. После этого толкатель вместе с матрицей поднимается и процесс повторяется.
3. Заключение
3.1 Обзор основных результатов
В работе проведён анализ структуры автоматической роторной
линии, сборочных операций и условий их осуществления на роторных машинах.
Изучены конструктивные элементы сборочных роторных машин и линий, особенности их
компоновки.
Проанализирована конструкция и служебное назначение
гидрозамка одностороннего типа КГУ3.020ПР-01. Разработан технологический процесс
сборки гидрозамка и автоматическая роторная линия для его осуществления, которая
позволяет увеличить производительность в 9-10 раз, снизить трудоёмкость сборки
изделия в 3 раза, что приведёт к снижению себестоимости сборки. В состав данной
линии входят загрузочные, транспортные и технологические (сборочные)
роторы.
3.2 Перспективы исследований
В дальнейшей своей работе над магистерской диссертацией
планируется усовершенствовать автоматическую роторную линию для сборки гидрозамка в
целом, а также в частности спроектировать роторную машину для установки
стопорящего кольца в корпус с перспективой её дальнейшего внедрения и
использования в машиностроительном производстве.Для этого планируется
исследование напряжённого состояния металлического стопорящего кольца,
конической матрицы и цангового толкателя непосредственно в процессе вставки
кольца в корпус. Планируется исследование особенностей уплотнений, их сборки с
деталями гидрозамка.
Итак, главной задачей стоит дальнейшее совершенствование
способов сборки на автоматической роторной линии на примере гидрозамка
одностороннего типа КГУ3.020ПР-01.
Список используемой литературы
1.Клусов И.А.
Проектирование роторных машин и линий: Учеб. пособие для студентов
машиностроит.
спец. вузов - М.: Машиностроение, 1990 - 320
с.
2.Кошкин Л.Н. Роторные и роторно-конвейерные линии - М.: Машиностроение,
1982 - 236 с.
3.Прейс В.В. Технологические роторные машины вчера, сегодня,
завтра - М.: Машиностроение, 1986 - 128 с.
4.Клусов И.А. и др.
Автоматизация сборочных процессов на роторных линиях - Киев, 1967 - 48
с.
5.Кошкин Л.Н. Комплексная автоматизация производства на базе роторных
линий - М.: Машинострое- ние, 1972 - 258 с.
6.Клусов И.А. и
др. Автоматические роторные линии - М.: Машиностроение, 1987 - 256
с.
7.Кошкин Л.Н. Автоматические линии роторного типа: Конструкции, расчёт и
проектирование/ А.Н. Кошкин, И.А. Клусов, В.В. Прейс - Тула, ЦБТИ,
1961 - 198 с.
8.Ищенко А.Л. Разработка технологического и структурного
обеспечения проектирования высокопроиз- водительных процессов и
систем сборки непрерывного действия. Дис. на соис...канд. техн. наук
-
Донецк, 1999 - 200 с.
9.Новиков М.П. Основы технологии
сборки машин и механизмов - М.: Машиностроение, 1980 - 532 с.
10.Муценюк К.Я.
Автоматизация сборочных процессов - Л.: Машиностроение, 1969 - 107 с.
11.
Михайлов А. Н. Основы синтеза поточно-пространственных технологических систем. -
Донецк:
ДонНТУ, 2002. - 379 с.
12.Волкевич П.И. - Курс лекций по дисциплине "Автоматизация производственных процессов в машиностроении"