The modern industrial electric drive (ED) - complex system which consists of the whole complete set of interdependent elements: executive power body (electric motor), the power supply (converter), control system ED, including the gauge of parameters ED, setting information devices. All these elements develops, that allows to do more and more progressive ED which provide optimization of industrial operating modes of units or complexes.
Power electronics roughly progresses. A tendency to creation powerful operated power semi-conductor devices (PSD), development of the integrated devices in the form of the finished modules with the structures isolated from the case, began to be shown. Perfection of technology allows to increase constantly power of devices, to raise rapidity and even to produce on one plate devices on bipolar technology.
With the advent of whole operated devices, opens the opportunity of designing of converters with high power parameters and with good compatibility with a network, and also to realize earlier known, but complex in performance, converters with implicitly expressed link of a direct current which differ unitary transformation of energy and supposing a bilateral exchange of energy.
Until recently adjusted ED was carried out mainly based on direct current electric motors. However as PSD improves, a tendency to orientation to adjusted alternating current electric drive , appears.
The new technology of production which is produced on thermogalvanic assembly, demands more rigid technology requirements to ED coiling device. To satisfy those demands it is expedient to apply systems ED with an alternating current motors.
The most simple on a design, a cheap and reliable electric motor is the asynchronous motor (AM) with a short-circuited rotor. Use of such motor in an adjustable drive represents separate interest.
In frequency-adjustable asynchronous ED are used mainly two-links frequency converters (FC) based on of autonomous inverters (AI): with an autonomous link of constant current (the autonomous inverter of a current - AIC) or voltage (the autonomous inverter of a voltage - AIV).
It is known, that ED based on FC AIV with pulse-width modulation (PWM) are more universal, than ED based on FC AIC.
Refer to ED functional diagram based on AIV PWM (figure 1).
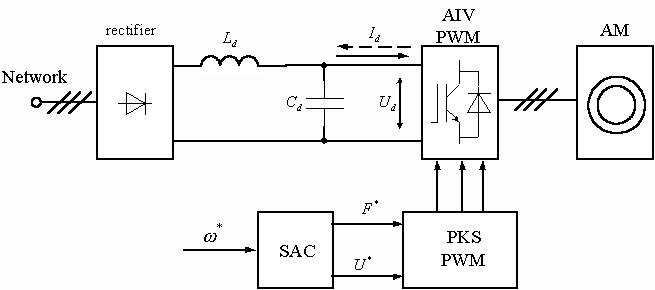
Advantages of analyzed system ED
) in all operating modes;
sinusoidality of an initial current, AM smooth, stepless rotation on speeds close to zero;
the high dynamic parameters ED caused by high rapidity of PWM control.
Necessity of inclusion additional power elements, for realization brake modes, is lack of ED functional diagrams with AIV PWM.
To analysis dynamic parameters, we shall use asynchronous motor block diagram ( figure 2).
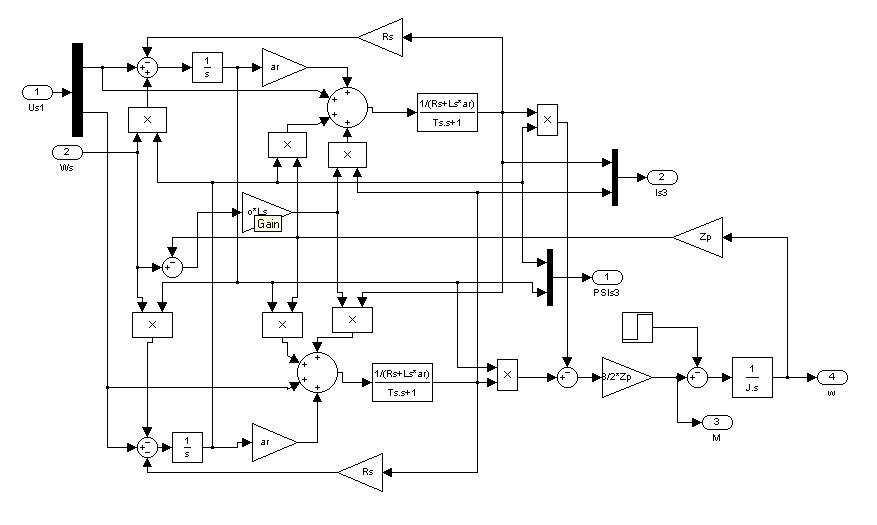
Transfer function of closed current control loop:

Transfer function of closed rate control loop:

Electric drive transiet process illustrated on figure 3

The basic purpose of the given work "Development and research frequency controlled electric drive of the coiling apparatus of thermogalvanic assembly" is to increase technical and economic parameters and functionally-technological abilities of the device.
Demands, shown to the future system of the electric drive, have been based on technological process thermogalvanic processing of steel wire. To satisfy these demands the most suitable system of the electric drive was chosen. After researches of this system, is established, that it has not only entirely provided all technological demands, but also has allowed essentially reduce (in 1.4 times) a current consumption.