Мешалка
(Журнал фирмы Брюль и Къер"The Monitoring System")
Одной из основных машин является мешалка главного реактора установки. В связи с ее основной ролью в технологическом процессе мешалка была выбрана в качестве одного из узлов, управление состояния которого необходимо производить непрерывно. Эскиз мешалки показан .
Происшедшие в прошлом поломки иызывали значительные убытки (потери производства, повреждения узлов машины и т.п.). После внедрения непрерывной мониторизации механических колебаний, непредвиденных поломок не возникало. Во многих случаях развитие незначительных неполадок- и повреждений в потенциально серьезную аварию удавалось предотвратить, поскольку тревожная сигнализация системы на ранней стадии позволила вовремя принять необходимые меры.
Пример 1
Сразу после установки системы непрерывного управления был зарегистрирован сигнал тревоги, обусловленный превышением заданного предела пиковой энергии сигналом от датчика на узле уплотнения и подшипника в верхней части оси вала мешалки. Данный подшипник обычно не заменяется при текущем ремонте уплотнения.
Показаны тенденции изменений СКЗ и пиковых значений, соответствующие стабильному состоянию (на горизонтальной оси графиков отложено число недель до создания графика тенденций).
показывает долгосрочные тенденции изменений пиковых значений энергии сигнала от упомянутого выше датчика. Эти значения увеличивались до обнаружения неисправности (между 16-ю и 14-ю неделями на оси тенденций).
При прослушивании канала был слышен «тикающий» звук при каждом обороте. Автоматическое сравнение спектров показало увеличение уровня составляющей с частотой 17 Гц. Путем вычисления присущих подшипнику частот увеличение уровня на частоте 17 Гц было диагностициро-вано как дискретный дефект на очень ранней стадии его развития. Наряд на замену подшипника был назначен на ближайший планируемый останов установки. Во время всего периода, предшествующего запланированной остановки установки, обнаруженный дефект подшипника находился под наблюдением, показавшим некоторое увеличение уровня составляющей с частотой 17 Гц.
Во время запланированной остановки установки подшипник и уплотнение были заменены. При осмотре подшипника была замечена изолированная выбоина на внешнем кольце подшипника (см. рис. 8). Неисправность была на такой ранней стадии, что подсчеты показали, что подшипник мог проработать в течение последующих 6 месяцев без важных неполадок.
После установки нового узла уплотнения и подшипника состояние последнего было проверено в обычном порядке. СКЗ и пиковые значения были устойчивы, но пиковые значения энергии имели рассеянный разнос. При прослушивании узла создаваемый им акустический шум имел случайный характер. Причина такого шума, однако, не могла быть определена, предположительно шум создавался трением одной части о другую.
Обычно, при такой ситуации, мешалка была бы остановлена для замены уплотнения. Однако, после наблюдения за уровнями механических колебаний в течение суток было принято решение не останавливать мешалку для замены уплотнения, а продолжать эксплуатацию и использовать график тенденций для периодической проверки ее состояния. На рис. 6 можно видеть результат терпеливого подхода, поскольку график тенденций показывает уменьшение уровня пиковой энергии до нормального значения через некоторое время (приблизительно в промежутке недель -11,5 и -11 на оси времени графика тенденций). На этом участке времени пропал и шум трения.
Если бы система управления с ее способностью проводить анализ тенденций не использовалась, бесполезной остановки оборудования вместе с сопутствующими затратами на потерю производительности, дополнительных расходов на техобслуживание и пр. было бы не избежать.
Пример 2
Несколько позднее, во время ремонта другой машины производственной линии, узел уплотнения и подшипника над баком мешалки был заменен в порядке планового технического обслуживания предприятия. После ввода установки в эксплуатацию было зарегистрировано несколько тревожных сигналов от указанного подшипника в той же точке измерения как и в предыдущем примере 1.
Автоматическое сравнение спектров механических колебаний показало значительное увеличение уровня вибрации в частотном диапазоне от 1 до 10 кГц. Такая картина наблюдалась в течение относительно короткого времени, всего нескольких часов.
Предположительно, неполадка возникла в результате плохой смазки подшипника. Смазка была своевременно подана в подшипник, после чего уровни ненормальной вибрации снизились до нормальных значений. Однако, через несколько минут уровни составляющих с высокими частотами снова увеличились и продолжали повышаться.
Такое повышение уровней высокочастотных составляющих механических колебаний указывало на классические симптомы повреждения подшипника. Было принято решение остановить производство и произвести инспекцию подшипника. Осмотр показал, что ролики деформированы (см. рис. 10), а дальнейшая инспекция выявила, что подшипник был установлен без смазки. Данная ранняя стадия возникновения дефекта была четко видна в спектре механических колебаний.
Подшипник был заменен и эксплуатация возобновилась. Уровни механических колебаний уменьшились до нормы на всех частотах.
Таким образом была предотвращена серьезная авария. Сравнение спектров в режиме реального времени привело к тревожной сигнализации задолго упреждением до возникновения серьезной аварии, даже не смотря на то, что ситуация развивалась стремительно. Одновременно, путем сравнения спектров была получена достаточная информация для точного определения характера неполадки.
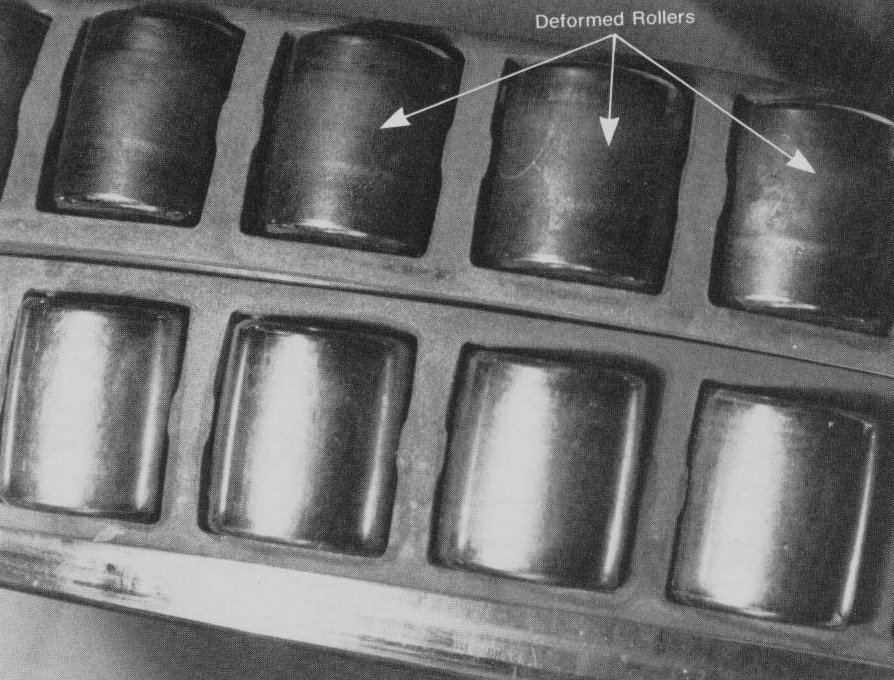
Рисунок 10 Деформация роликов подшипника
Определение малых отклонений
Помимо указанных двух случаев, когда были предотвращены серьезные аварии, имеются также другие полезные аспекты использования системы. Любые отклонения спектров механических колебаний от заданных допусков, независимо от того насколько незачительными они могут выглядеть, автоматически регистрируются и закладываются в память ЭВМ.
Таким образом, даже небольшие изменения состояния оборудования могут регистрироваться и вместе с информацией о других машинах данной технологической линии будут способствовать принятию решений о проведении капитального ремонта оборудования заранее. Так, за исключением показаний серьезного аварийного состояния машин, оборудование может эксплуатироваться с максимальной эффективностью.
Преимущества сравнения спектров перед управлением в широкой полосе частот
Для данного типа подробного управления состоянием применение сравнения спектров является принципиально важным. Мониторизация СКЗ, пиковых и энергетических уровней выявила бы ситуации, в которых имелась бы реальная угроза неминуемой аварии. Однако, небольшие изменения составляющих механических колебаний с относительно низкими уровнями вообще не отражаются на упомянутых параметрах.
Это видно из примера, где определено небольшое изменение состояния, на этот раз используя результаты измерений и анализа механических колебаний редуктора мешалки. Присущие широким частотным полосам значения выглядели устойчивыми на всех точках замера на редукторе (пиковые значения энергии и СКЗ показаны . Однако, изучение накопленных узкополосных спектров механических колебаний показало наличие тенденции увеличения уровней в диапазоне частот 3-10 кГц в дополнение к незначительным изменениям уровней низкочастотных составляющих Эти данные указывают на начало ухудшения состояния подшипников редуктора.
Поскольку эти отклонения не считались значительными, мешалка находилась в эксплуатации. Тщательный контроль за состоянием редуктора будет проводиться в процессе мониторизации, но при нарастании уровней механических колебаний си стема сообщит об изменении состо яния и о надобности технического об служивания.
Другой пример таких малых отклонений может быть показан еще раз на мешалке, на этот раз на ее двигателе показан результат сравне ния спектров механических колеба ний двигателя, указывающий на повышение уровней некоторых высоко частотных составляющих. График тенденций показывает на чало тенденции нарастания в полосе частот 1,6 - 1,8 кГц. Наиболее вероят ной причиной такого нарастания является дефект подшипника в его ранних проявлениях. Однако, поскольку нарастание уровня не рассматривалось как серьезное, подшипники регулярно смазывались для сдерживания нарастаний уровней и двигатель эксплуатировался до планового ремонта. Во время ремонтных работ была проведена инспекция подшипников двигателя и на одном из наружных колец были обнаружены следы точечной коррозии.