 |
страничка студента
|
|
|
|
НИРС
Процесс перемешивания жидкости в замкнутом объеме является сложным физическим явлением. Для того, чтобы проанализировать это явление относительно конкретной технологической задачи представляется целесообразным использование определенных критериев, которые позволяют выполнить сравнительные оценки на макро- и микроуровнях. В рамках оценки эффективности перемешивания определенного объема жидкости наиболее часто используются интегрированный показатель «интенсивность перемешивания».
Интенсивность перемешивания металла в ковше представляется очень важным технологическим показателем при обработке стали на установке ковш-печь. Во-первых, интенсивность перемешивания металла определяет длительность некоторых этапов обработки, в том числе гомогенизации металла по химическому составу и температуре или процессу рафинирования металла шлаком. Во-вторых, процесс перемешивания металла газом происходит достаточно сложно, и в жидкой ванне образуются как зоны интенсивной циркуляции, так и «застойные области», проявление которых может негативно отражаться на конечных показателях обработки в целом. В-третьих, использование аргона как субстанция, которая обеспечивает процесс перемешивания, допускает дополнительные расходы на обработку и соответственно уменьшение количества аргона их, что используется, снижает.
Основные задачи физического моделирования относительно настоящей работы можно сформировать таким образом:
- изучение особенностей перемешивания жидкости в ковше при ее продувке газом через пористые блоки, установленные в днище;
- изучение возможности оптимизации основных рабочих параметров вдувания газа (интенсивность, количество продувных блоков, расположения продувных блоков и т.п.) для обеспечения процесса перемешивания рациональной интенсивности;
- изучение особенностей перемешивания металла с шлаком в процессе продувки металла газом.
Физическое моделирование
Физическое моделирование процессов перемешивания жидкости наиболее преимущественно при сохранении одинаковых геометрических размеров исследуемого агрегата и модели. Однако, объем основной массы сталеразливочних ковшей, которые используются в металлургическом производстве, составляет 10-45 м3 (при массе металла 80-350 т), что делает очень затруднительной технику моделирования с сохранением геометрических размеров, поскольку это связано с большой трудоемкостью исследовательских работ и не всегда гарантирует получение абсолютно надежных данных по физическому моделированию.
Учитывая тот факт, что при вдувании газа в жидкость весьма важными представляются процессы, что происходят под действием сил тяжести, которые определяют всплытие волдырьков газа, и сил инерции, которые определяют развитие системы циркуляционных потоков в жидкой ванне ковша, в настоящей работе как базовые критерии подобия был принят критерий Фруда и критерий гомохронности.
Физическое моделирование процесса перемешивания расплава инертным газом в ковше выполнено на прозрачной модели, что позволяет визуализировать все основные процессы, которые происходят при продувке жидкости. Геометрические размеры вместимости, которая имитирует сталеразливочний ковш, были выбраны следующими: диаметр - 0,24 м, высота - 0,40 м. При этом предусматривалась, что выбранная вместимость обеспечит моделирование процессов перемешивания для ковшей разной конструкции (в первую очередь, отношения высоты налива металла к диаметру ковша). При этом как моделирующая жидкость использовали воду при температуре 18-25оС. Выбор у воды как моделирующая жидкость объясняется тем фактом, что значения вязкости воды и стали в области температур внепечной обработки достаточно близки друг к другу. Перемешивания жидкости осуществляли сжатым воздухом.
Для имитации шлака, расположенного на поверхности металла, использовали масло силикона, которое, как известно, имеет высокие значения поверхностного натяжения, а вязкость может варьироваться в достаточно широких границах в зависимости от его температуры. Плотность выбранного масла силикона составила 965 кг/м3.
Геометрический масштаб физических моделей определялся с учетом критериев подобия Фруда и гомохроности и составил 1:8 и 1:12 по отношению к выбранному моделируемому объекту - установка ковш-печь вместимостью 60т и 110т соответственно. Для визуального наблюдения газожидкостных потоков стенки моделей выполняли из прозрачного стекла, а воду подкрашивали специальным индикатором для цветового отличия от масла силикона. Наблюдаемые картины перемешивания фиксировали с помощью цифровой видеокамеры. Экспериментальные установки позволили регулировать затрату газа и изменять положение продувных устройств относительно вертикальной оси сосуда. В процессе исследования было снято около 250 фотографий процесса перемешивания для разных значений расходов и скоростей вдуваемого газа, которые изменяются в интервале 0,1-0,8 м/с.
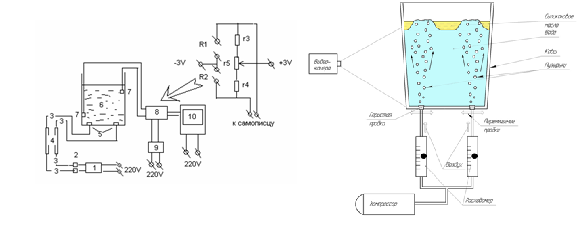
Рис.1 - Схемы физических моделей для изучения процесса перемешивания: а - для визуализации процессов перемешивания; бы - для оценки интенсивности перемешивания в ходе продувки: 1 - компрессор, 2 - узел регуляции подачи воздуха, 3 - трубопровод, 4 - блок измерения параметров вдуваемого воздуха (затрата, давление),5 - продувочные узлы, 6 - модель ковша, 7 - датчики измерения электропроводимости воды, 8 - мостовая схема, 9 -стабилизированный блок питания, 10 - самописец
Таким образом, на основании выполненных наблюдений характера движения потоков в верхней части ковша основные гидродинамические потоки можно условно классифицировать на 5 интегрированных подобластей с одинаковыми условиями (направление векторов скоростей, величина скорости, интенсивность турбулентности)
область восходящего газожидкостного потока, проникающего через слоя масла (шлаку);
область выхода вдуваемого газа в атмосферу, включая разбрызгивание шлака и металла (то есть область пятна выхода газа на поверхность ковша);
область нисходящих потоков металла, которые скользят вдоль слоя шлака сверху вниз;
область горизонтальных потоков металла (с некоторым количеством волдырьков газа), которые двигаются вдоль поверхности шлака по направлению от восходящего потока к периферии ковша;
область формирования смеси металла, шлака и волдырьков вдуваемого газа, которая формируется под шлаковым слоем в зоне движения восходящих потоков.
Развитие и размеры той или другой из выделенных подобластей зависят от ряда факторов, главной из которых является затрата вдуваемого газа, количество продувных узлов и их расположения, а также вязкость шлака, какое разное на разных этапах внепечной обработки.
|
|