Русский
ДонНТУ
Портал магистров ДонНТУ
Реферат | Библиотека | Ссылки |
Отчет о поиске | Индивидуальное задание
Р. Кеннеди, Л. Мацца
Источник: Журнал "Методы менеджмента качества" (№8, 2004)
www.center.ru
Взаимодействие 5S и TPM в системе TPM3
Сегодня системы 5S и TPM рассматриваются в качестве ключевых элементов моделей экономного производства (Lean Manufacturing)
и производства мирового уровня (World Class Manufacturing). Однако лишь в некоторых организациях понимают, что при совместном использовании этих двух
систем можно получить гораздо большие преимущества по сравнению с теми, которые каждая из них может дать в отдельности. К сожалению, во многих компаниях
развертывание этих систем ведут раздельно и не используют их совместный потенциал увеличения производительности, качества продукции, оптимизации поставок
и снижения издержек, а также повышения производственной безопасности и развития корпоративной культуры, что позволяет создать передовое предприятие.
Система TPM была разработана в Японии на рубеже 60-70-х годов на фирме "Ниппон Дэнсо", известном поставщике
электрооборудования для фирмы "Тоёта", как методика повышения эффективности оборудования, в значительной мере в связи со становлением Производственной
системы фирмы "Тоёта" (Toyota Production System). Система 5S была разработана в Японии примерно в то же время как набор принципов поддержания в порядке
рабочих мест. Система TPM оставалась секретной разработкой до 1980 г., когда было опубликовано первое ее авторизованное описание на английском языке. В
начале 90-х годов прошлого столетия TPM в различных вариантах получила распространение во всем мире.
Центр TPM Австралии и Новой Зеландии был основан в 1996 г. с целью создания австралийской версии TPM для машиностроительной
и угольной отраслей промышленности, вспомогательных производств и отраслей услуг путем сопоставления различных версий этой системы (японской, американской,
европейской, южноафриканской, бразильской). В январе 1998 г. была представлена система TPM3 — улучшенная и расширенная австралийская версия системы TPM
третьего поколения, которая до этого была разработана Японской ассоциацией производственного обслуживания (JIPM). Ключевая особенность системы TPM3
состоит в том, что развертывание систем 5S и TPM осуществляется в рамках единой системы мероприятий с учетом специфики персонала на предприятиях Австралии
и Новой Зеландии.
Перед тем как рассмотреть взаимодействие систем 5S и TPM в системе TPM3, обратимся к тому, каким образом японские
специалисты разрабатывали эти две системы, и как была создана австралийская версия системы TPM3.
Системы 5S и TPM
Как можно догадаться из названия, методика 5S включает пять шагов. Они соотносятся с пятью японскими словами в английской
транскрипции1. Эти слова обозначают деятельность по эффективной организации рабочего пространства и стандартизации действий персонала (табл. 1).
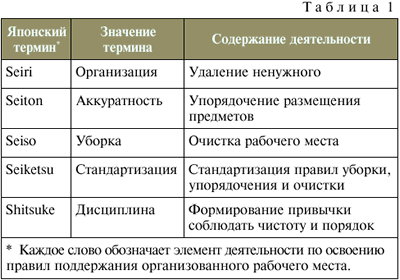
С начала 70-х годов прошлого столетия система TPM претерпела значительные изменения. Изначально существовало пять
направлений деятельности, которые сейчас называют первым поколением системы TPM. Система была нацелена только на повышение эффективности оборудования.
В конце 80-х годов стало понятно, что даже если TPM полностью развернута в производственных подразделениях и ликвидированы потери шести основных видов,
то остаются резервы совершенствования производства за счет ликвидации потерь, обусловленных несбалансированной работой оборудования в составе сложных
технологических линий3 или нарушением производственного графика. Во втором поколении системы TPM упор сделан именно на оптимизацию всего производственного
процесса, поэтому в нее включено дополнительное направление — улучшение работы обеспечивающих подразделений и качества планирования производственной
деятельности.
Позднее разработчики системы TPM пришли к мнению, что налаживание бесперебойной работы оборудования может улучшить
деятельность всей компании, поскольку это ведет к значительному увеличению объемов производства, улучшению качества продукции и повышению производственной
безопасности. Это достигается за счет вовлечения в процесс улучшений обеспечивающих подразделений, а также введения в систему TPM двух дополнительных
направлений: улучшения качества продукции и повышения производственной безопасности. Этим характеризуется третье поколение системы TPM, включающее восемь
направлений деятельности по развертыванию TPM3.
Самостоятельное обслуживание оборудования операторами является ключевым элементом системы TPM, но во многих компаниях,
к сожалению, система TPM сводится лишь к этому элементу, который понимается как выполнение операторами текущего осмотра оборудования и его технического
обслуживания в минимальном объеме.
Правильнее рассматривать TPM в качестве интегрированного подхода к повышению эффективности производственного оборудования
(самостоятельное обслуживание оборудования операторами — это лишь одно из четырех направлений деятельности, выделенных жирным шрифтом в приведенном списке)
и компании в целом.
Процесс освоения самостоятельного обслуживания оборудования операторами состоит из семи шагов (табл. 2), направленных на то,
чтобы они научились выполнять базовое техническое обслуживание (или ремонт) оборудования и приобрели навыки выявления его дефектов до того, как они
приведут к поломке или выпуску брака. По словам вице-президента JIPM, С. Накадзимы, система TPM позволяет выпускать бездефектную продукцию с
использованием методики "точно вовремя" при стремлении к нулю поломок оборудования и высоком уровне автоматизации производства. Без системы TPM
производственная система фирмы "Тоёта", возможно, не смогла бы развиться. Это подтверждается тем, что смежники фирмы "Тоёта" динамично осваивают систему
TPM.
Система TPM3 — новое поколение TPM
На предприятиях Австралии и Новой Зеландии, где производственная культура довольно сильно отличается от производственной
культуры предприятий Японии, разработана TPM3 (улучшенная и расширенная австралийская версия третьего поколения системы TPM). Для этого потребовалось
расширить область отдельных улучшений таким образом, что теперь она охватывает как само оборудование, так и процессы: на макроуровне, когда рассматривают
все производство с целью установления причин потерь и планирования бюджета времени для улучшений, и на микроуровне, когда оценивают величину отдельных
видов потерь для решения сложных проблем. В систему TPM3 введены дополнительные направления деятельности по формированию производственной среды и
улучшению системы управления персоналом, чтобы отразить потребность в переходе от деятельности по аналогии к последовательным улучшениям, которые являются
фундаментом TPM.
Мы считаем, что целесообразно обозначить названия некоторых направлений TPM терминами, наиболее полно отражающими
деятельность по улучшению производственной среды, и изменить порядок реализации некоторых направлений, например, присвоить направлению обеспечения
безопасности номер 1 вместо 8. Концептуальная модель, показывающая, как эти 10 направлений TPM взаимосвязаны, представлена на схеме 1 (С — основные,
S — поддерживающие и D — развивающие направления).
По нашим наблюдениям, на большинстве заводов Австралии и Новой Зеландии пользуются простым языком, а не научными терминами.
С этой точки зрения производственная среда может быть разделена на рабочую площадь, т. е. все, что окружает оборудование, и
само оборудование.
Деятельность по обустройству рабочей площади предусматривает использование первых двух элементов системы 5S и входит в
освоение самостоятельного обслуживания оборудования операторами по типовой процедуре, состоящей из семи элементов (где первые пять шагов включают три
оставшихся элемента системы 5S). Это меняет смысл работы, называемой "очисткой": происходит переход от простой чистки оборудования к глубокой "очистке,
совмещенной с проверкой", позволяющей идентифицировать многие скрытые дефекты оборудования, которые могли бы привести к серьезным проблемам (поломкам или
снижению качества продукции).
Важный вопрос, касающийся терминологии, связан со значением словосочетания "самостоятельное обслуживание оборудования
операторами". Многие догадываются, что существует различие между трактовкой этого словосочетания в Японии ("техническое обслуживание оборудования") и
в Австралии и Новой Зеландии ("ремонт оборудования"). В связи с этим зачастую тратится много времени и средств, чтобы научить операторов самостоятельно
ремонтировать оборудование, что не является целью развертывания системы TPM. Самостоятельное обслуживание касается обучения операторов навыкам раннего
выявления дефектов и передачи знаний о том, как функционирует оборудование (но не как оно устроено), чтобы операторы могли как можно быстрее выявлять
проблемы, связанные с оборудованием и качеством продукции. Поэтому мы пользуемся более точным термином "самостоятельное обслуживание оборудования
операторами".
Система TPM3, как и первоначальная версия TPM, основана на предположении, что наиболее эффективно рабочее пространство
могут использовать малые группы из четырех-восьми работников, которые четко знают цели деятельности, регулярно получают сведения о результатах
производственной деятельности и поддерживают связь с обеспечивающим персоналом (ремонтными и техническими службами). Поэтому формирование производственной
среды и самостоятельное обслуживание оборудования операторами являются ключевыми направлениями системы TPM3, ориентированными на развитие деятельности
малых групп.
Формирование производственной среды
Направление развертывания системы TPM3 по улучшению производственной среды было введено с целью обеспечить участие всего
персонала в освоении этой системы, отвечая на ключевой вопрос: "Тратится ли время впустую, когда персонал выполняет ту или иную работу?" При этом
требуется, чтобы все занятые на рассматриваемой площади работали сообща и улучшали функционирование предприятия по всем направлениям развертывания
системы TPM.
Генеральной целью является инициирование и улучшение деятельности малых групп путем закрепления за ними участков рабочего
пространства. Малые группы затем посредством своей деятельности создают "места, где все на своем месте", проводят внутренние аудиты, чтобы оценить
результаты собственных усилий по улучшению безопасности, производительности и моральных факторов. С того момента как малые группы приступают к улучшениям
на своих рабочих местах, значительно уменьшаются потери времени на поиск предметов и улучшается горизонтальная связь между командами. Малые группы также
ведут подготовку и внедрение системы самостоятельного обслуживания оборудования операторами.
Самостоятельное обслуживание оборудования операторами
Освоение системы самостоятельного обслуживания оборудования операторами расширяет деятельность малых групп, смещая фокус
приложения усилий с рабочей площади на само оборудование. Цель освоения системы — подготовка ответственных и компетентных специалистов, а также создание
надежных и безопасных рабочих мест. Это достигается путем приведения оборудования в желательное состояние при соблюдении требований эксплуатационных
нормативов (затяжка креплений, чистка, смазка), обучения операторов принципам функционирования оборудования (чтобы они лучше диагностировали проблемы),
внесения в устройство и порядок использования оборудования отдельных улучшений, предупреждения преждевременного износа оборудования путем ежедневных
проверок и правильной его эксплуатации, установления необходимых условий для обеспечения правильного использования оборудования.
Освоение системы самостоятельного обслуживания операторами показано в табл. 2.
Взаимосвязь 5S и TPM3
Первые два элемента в системе 5S (Seiri ? Seiton) нацелены на освобождение рабочего пространства от нежелательных или
ненужных предметов и упорядочение оставшихся предметов. Деятельность по организации рабочего пространства непосредственно соответствует этим двум шагам
в 5S (создание "рабочих мест, где все на своем месте"), кроме этого, используется концепция закрепления площадей за малыми группами. Деятельность по
улучшению производственной среды также способствует установлению связей между малыми группами, что является условием улучшения работы многих предприятий
Австралии и Новой Зеландии.
Интеграция 5S в TPM3 через улучшение производственной среды и пять шагов самостоятельного обслуживания операторами
показаны в табл. 3.
Шаг 1 процедуры освоения системы самостоятельного обслуживания оборудования операторами и шаг 2 сфокусированы на
регулярной чистке и проверке оборудования для определения источников проблем и дефектов. Третий элемент системы 5S — очистка рабочего пространства —
необходим, поскольку без него уборка производственных помещений превращается в рутинное удаление мусора, и загрязнения внутри машин остаются источниками
дефектов и поломок.
Таким образом, TPM3 не только включает третий элемент системы 5S (регулярная уборка для поддержания порядка на рабочих
местах), но и развивает эту деятельность в направлении восстановления оборудования для достижения его желательного состояния путем создания "базовых
условий" (предотвращения загрязнения и ослабления креплений и проведения смазки), для того чтобы продлить срок службы узлов и агрегатов машин.
Четвертый элемент системы 5S — стандартизация — включает установление и обеспечение наилучших методов формирования
производственной среды, чтобы обеспечить постоянство выполнения требований первых трех элементов системы 5S. На шаге 3 освоения системы (разработка
стандартов для чистки и проверки) не только устанавливаются стандартизованные процедуры для выполнения работ на шагах 1 и 2, но и проводится обучение
операторов тому, как осуществлять техническое обслуживание оборудования, принимая на себя ответственность за смазку оборудования.
Ключевым условием обеспечения постоянства деятельности в системе 5S является пятый и последний элемент — дисциплина. На
шагах 4 и 5 осуществляется постоянное ознакомление операторов с принципами функционирования оборудования наряду с установлением стандартов его технического
обслуживания. В результате операторы заинтересованы в поддержании хорошего состояния оборудования.
Следует также обратить внимание на ключевую роль третьего элемента системы 5S — уборка рабочего места. Чтобы стимулировать
деятельность малых групп, отвечающих за содержание участков рабочего пространства, нужно чтобы их участники осознавали степень своей ответственности за
обеспечение требуемого санитарного состояния производственных помещений и его постоянное улучшение. Если этого не происходит, то нередко участники групп
заботятся лишь о своей области деятельности и не обращают внимания на то, что происходит по соседству. Это преодолевается введением системы TPM3, в
которой проводится различие между простой чисткой и "чисткой, совмещенной с проверкой", которая значит гораздо больше, чем простая уборка помещений.
Выводы
Интегрируя 5S в TPM3, мы смогли успешно развернуть системы 5S и TPM на ряде предприятий Австралии и Новой Зеландии,
встречая поддержку и одобрение персонала этих предприятий вместо обычной пассивности и неприятия. Мы также убедились в том, что можно соблюсти
реалистичные сроки освоения системы самостоятельного обслуживания оборудования операторами — 24 месяца (TPM3 основана на 12-недельных циклах улучшений,
которые основаны на последовательной оценке результатов осуществленных мероприятий).
Другое важное достоинство методики TPM3 состоит в том, что она позволяет создать малые группы с частично перекрывающимися
областями деятельности, которые ведут работу, направленную на значительное увеличение объемов выпуска продукции, повышение производительности, улучшение
качества, соблюдение условий поставок, безопасности и улучшения морально-психологического климата в компаниях, нацеленных на освоение и совершенствование
этой системы.
ДонНТУ>
Портал магистров ДонНТУ>
Реферат | Библиотека | Ссылки |
Отчет о поиске | Индивидуальное задание