AC-AC CONVERTER WITH LOAD POWER ESTIMATOR Marian
Gaiceanu ”Dunarea de Jos” University of Galati, Department of
Electrical Engineering, Domneasca Street, 111, 6200 Galati-
ROMANIA
Key words: PWM ac-ac converter, power balance,
rotor field oriented control.
Abstract In this paper a three-phase
quasi-direct ac-ac converter system by means of pulse-width modulation
(PWM) is reported. The control of the source converter is based on the
minor current loop in a synchronous rotating-frame with a feed forward
load current component added in the reference, completed with the dc
voltage control loop in a cascaded manner. The synchronous rotor based
reference frame was used for the field-oriented controllers involved in
the load side. Two control boards, based on the dSMC (digital Smart Motion
Controller) 30 MIPS 32-bit fixed-point digital signal processor (DSP),
were involved in the ac-ac system driving. By using the power balance
control, the DC link voltage variation at the load changes can be reduced.
In this way a small DC link capacitor is required to handle the dc voltage
error control. In order to obtain the feed-forward current component, the
load power must to be known. In this paper the load power is estimated
from the dc link, indirectly, through a dc load current estimator. In this
way the author overcomes the use of the serial communication between
control boards in order to deliver the load power information from the
inverter side. The load current estimator is based on the DC link voltage
and on the load current of the supply converter. By a proper control
sinusoidal input current, a nearly unity power factor (0,998),
bi-directional power flow, small (up to 5%) ripple in the dc-link voltage
in any operated conditions high quality balanced three-phase output
voltages were obtained. The performances of the ac-ac converter system
were shown through the experimental results.
Introduction The use of the force-commutated
[1] PWM source converters is related to attaining of the bi-directional
power flow and unity power factor, respectively. The first approaches in
the ac/ac conversion with PWM modulators were done in [2]-[4]. The ac-ac
converters are spited in indirect ac-dc-ac and quasi-direct ac-ac
converters, respectively. The quasi ac-ac converter system has the
advantage of the systems energy storage devices reduction. The load
feed-forward current component was introduced to force the converter power
to match the power [5] required by the inverter. By controlling the power
flow in ac-ac converter system, the unidirectional DC-link voltage can be
kept at the constant value. Reversing the flow direction of the dc-link
current ensures the reversibility of the power. The ac-ac converter is
used in drives that require regenerating power capability like elevators,
crane, centrifuge, wind turbine and so on. The PWM ac-ac converter system
is mainly used in industrial ac drive systems, where control of the ac
voltage and frequency at the induction machine terminals are needed.
The ac-ac converter The block control diagram
of the ac-ac system is shown in the Fig.1. On the basis of a DC voltage
reference V*dc, dc voltage feedback signal (Vdc), current feedback signals
(Ia, Ib for supply converter, and Iu, Iv for the load converter),
reference and the feedback speed, flux reference and the magnetizing
current, and load power signal (obtained through the load power
estimator), the software operates the ac-ac control (voltage, current,
flux and speed) system and generates the firing gate signals to the
corresponding PWM modulator. The input boost inductor is designed from
the THD (Total Harmonic Distortion) factor point of view. Therefore, the
input current THD factor is constrained to be less than 5% at the full
load. The boost inductor limits the peak switching currents to an
acceptable value and smoothing the line current. The dc link capacitor
design is carried out under the assumption that the ripple currents
generated by the supply converter and load converter are equal in
magnitude and are phase shifted by 180˚. The DC link capacitor provides a
decoupling function between the grid side and load side, respectively.
Thus, the dc capacitor provides a reduced value for the ripple current
generated by both converters and maintains a controllable dc link voltage.
The phase-locked loop (PLL) is necessary for the proper current
controllers decoupling, and for d-q axes synchronization with the grid
reference voltage, respectively. The PLL tracks the grid frequency.
Because of the system stability limit [6], [7] the proportional feedback
gain of the PI dc voltage controller must be small according to [8]. In
order to obtain a sinusoidal ac current shape, in motoring mode operation,
the dc link voltage is regulated at a higher level than the peak of the
incoming line such that the IGBTs can control the current.
Control of the voltage source converter The
detailed design methodology for the ac-ac converter system regulators is
presented in [9]. In ac drive a unity power factor is necessary. This
implies a proper orientation of the reference frame and a zero reference
value for d-axis line current, Id:

Low overshoot and fast response are the design criteria.
Voltage controller By model linearizing through
the small perturbation method around the equilibrium point the parameters
of the dc-voltage controller were derived [9]. The main task of the
voltage controller is to maintain the dc link voltage to a certain value.
Another task is to control the power flow of the voltage converter.
Current controllers The internal (current)
loops with wide bandwidth are needed to regulate the reactive power in
order to achieve unity power factor, and to regulate the active power such
that low dc voltage variation is ensured. At the same time, the ac input
current is regulated to be sinusoidal. The proportional integral (PI)
controllers were used in [9]. By using a decoupling method the cross
coupling between the d and q axes due to boost inductance was compensated.
Thus, by decoupling the d and q axes of the synchronous reference frame
model, the current control loop is obtained. The feed-forward current
component was added to the reference. Their value is provided from the
power balance equation, i.e. the power converter must meet the load power
requirements. Therefore,
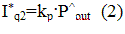
in which the proportional constant (considering that the
supply voltage has the constant value) is given by:
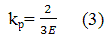
Through the feed-forward component the power flow is
controlled indirectly by the reference current. The output dc link power
is estimated as:
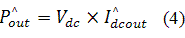
The estimated dc link current is given by:
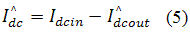
Mathematical model of the three-phase load converter
side By aligning the rotor flux vector to the d-axis and setting
the rotor flux linkage to be constant when the motor is operating in its
constant-torque region, the following equations are available:

in which ψqr (ψdr): q-axis (d-axis) rotor flux linkage.
The d-q model of the induction machine in the rotor field oriented frame
is :
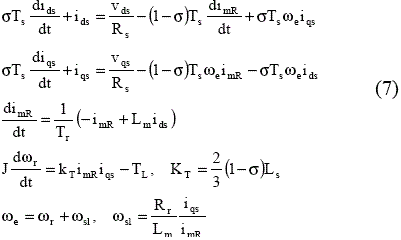 Rs - the stator resistance
per phase. ωe - the synchronous rotating frame angular speed. ωr -
the rotor angular speed. ωsl - the slip angular speed. Ids (Iqs) -
the d-axis (q-axis) stator current. V*ds (V*qs) - the d-axis (q-axis)
stator voltage commands. Ls (Lr) - the stator (rotor) inductance. Lm
- the mutual inductance. Ts=Ls/Rs - the time constant of the stator
circuit. σ - the total leakage factor. TL - the total load
torque. Tr=Lr/Rr - the time constant of the rotor circuit. KT - the
torque constant. J - the moment of inertia. p - the number of poles
pairs.
In the stator voltage equations, the d and q axes
components are coupled. They can be decoupled by introducing the
corresponding coupling compensation terms and the back-EMF feedforward
voltages, Ed and Eq, in the d-q axes voltage commands (V*ds, V*qs)
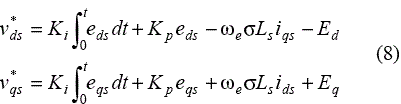

where eds= i*ds- ids, eqs= i*qs- iqs denote the d-q axes
current errors, and i*ds, i*qs the d-q axes current commands,
respectively. Kp and Ki denote the proportional gain and the integral
gain, respectively.
REFERENCES
- T.,Kataoka, K., Mizumachi, and S., Miyairi: «A pulsewidth controlled
ac to dc converter to improve power factor and waveform of the ac line
current,» IEEE Trans. Ind. Appl., vol. IA-15, pp. 670-675, Nov/Dec, 1979
- E. P. Weichmann, P.D. Ziogas, and V.R. Stefanovic: «A novel
bilateral power conversions scheme for variable frequency static power
supplies» IEEE Trans on Ind. Appl., vol IA-21, pp. 1225-1233,
Sept./Oct, 1985
- P.D.Ziogas, Y.G.Kang, and V. Stefanovic: «Rectifierinverter
frequency changers with suppressed dc link components» IEEE Trans. on
Industry Appl., vol. IA-22, no.6, pp. 1027-1036, Nov.-Dec. 1986
- P.D.Ziogas, Y.G.Kang, and V. Stefanovic: «PWM control techniques for
rectifier filter minimization» IEEE Trans. on Industry Appl., vol.
IA-21, pp. 1206-1213, Sep../Oct. 1985
- Ooi, B.T., Dixon J. W., Kulkarni A. B., Nishimoto, M. (1988). An
integrated AC Drive system Using a Controlled-Current PWM
Rectifier/Inverter Link, IEEE Trans on Power Electronics, vol.3, pp.
64-71, Jan/Feb.
- B. T. Ooi, Y.Guo, X.Wang, H.C. Lee, H.L. Nakra, J.W. Dixon,
«Stability of PWM HVDC Voltage Regulator Based on Proportional-Integral
Feedback» EPE Firenze’91, pp.3-076-3-081
- M. Nishimoto, J.W. Dixon, A.B. Kulkarni and B.T. Ooi, «An integrated
controlled-current PWM rectifier chopper link for sliding mode position
control» IEEE, Ind. Appl. Soc. Annual Meeting, pp. 752-757, October,
1996
- Y. Guo, X. Wang, H.C. Lee, and B.T.Ooi, «Poleplacement control of
voltage-regulated PWM rectifiers through real-time multiprocessing»
IEEE Trans. on Ind. Engineering, vol. 41, no. 2, pp. 224- 230,
March/April 1994
- Gaiceanu M., (2004). AC-AC converter system, PEMD’04, IEE,
Edinburgh, UK, 31st March-2nd April, 2004
- Leonhard, W.: Control of electrical drives, Springer-Verlag, Berlin
1996
|