Increasing of the social production volume is a character of scientific and
technological process. Problem of use of heavy tonnage industrial wastes
in national economy becomes more critical at intensive rising of capacity
of the mining enterprises. Now the volume of overburdens and waste rock
exceeds 3 mlrd. m3, cleaning rejects are near 1 mlrd. m3.
The variety of composition and properties of the overburdens
and waste rock determines a range of their utilization at different fields of the industry of
building materials. The overburdens of many deposits are qualitative raw materials for production of
extensive list of building materials: a lime-sand brick, a ceramic brick, a ceramics, a glass, etc.
The purpose of the present work is the research of the possibility of use
of the co-products made at the production of some materials from the natural raw materials
and other wastes for production of the ceramic glazes.
The main research object is a nephelinic syenite the reject
of zirconium concentrate located at the territory of Donetsk chemical-and-metallurgical plant at
Donskoye settlement of Volnovakha district. Nephelinic syenite is the co-product made as a result of
extraction and wet cleaning of zircon ores. Nepheline is at dump in quantity of some million tons.
The tasks are:
- -to develop a composition of the ceramic glazes;
- - to select the optimal firing temperature;
- - to make decision about possibility of use of the technogenic waste
as one of the main components for production of the ceramic glazes on the grounds of received results;
- -getting of necessary ratio of coefficient of thermal linear expansion of the crock and coverage;
- -selection of a coloring agent for coloration of the glaze layer;
- - utilization of the technogenic waste.
2 EXPERIMENTAL PART
2.1Specification of raw materials
Nepheline-containing raw materials are the alkaline aluminum silicates;
the main ones are the nepheline, feldspars and colored minerals. Chemical composition of studied
nepheline-containing waste is characterized by the following containing of the components (%):
SiO2 39.3; Al2O3 32.87; Na2O 16.3;
K2O 5.93; CaO 1.53; Fe2O3 1.01; MgO 0.61;
TiO2 0.28; ZrO2 0.1; ignition loss 2.04.
Although nepheline belongs to the heat-resistant minerals it generates
low-melt eutectics with quartz, feldspars, melilite, pyroxenes.
It was a reason of the nepheline using as a component of ceramic glaze.
Glaze is a thin coat of vitreous coating laid on the
surface of ceramic products with following firing.
The purpose of the glazes is to cover a porous crock by dense
and smooth bed, to substantiate the products with crock and to give a good form, to
increase the chemical stability, to guarantee the electrical properties, to protect intraglaze
and underglaze decor against mechanical and chemical effect, to be a picturesque element
as well as the bottom layer for overglaze and intraglaze decor.
Alkali-containing removal of Kostyantynivka chemical plant of the following chemical composition (%):
CaO 64.63; BaO 22;
SrO3 11.23; SO3 2.03; ignition loss 0,11;
breakage of bottle glass; semiacid kaolin of The White Gully collected at the dumps as the
overburdens of the following composition (%):
SiO2 61; Al2O3 23,5;
Na2O 0,45; K2O 2,35; CaO 0,4; Fe2O3 1,1;
MgO 0,6;TiO2 1,5; ignition loss 9,1 were used in this work as other components of the glaze.
The compositions stated in the table 1 below were investigated for production of επσ unfritted glaze.
Table 1 - Composition of glazes.
Ή Composition of glaze |
Components |
Nepheline |
Breakage of bottle glass |
Alkali-containing removal |
Clay CY-3 |
Semiacid kaolin
|
Soda |
Boric acid |
Silicate block |
1. |
- |
- |
- |
- |
- |
- |
- |
- |
1.1 |
40 |
40 |
- |
20 |
- |
- |
- |
- |
1.2 |
40 |
40 |
- |
- |
20 |
- |
- |
- |
1.3 |
40 |
50 |
- |
- |
10 |
- |
- |
- |
1.3 |
40 |
55 |
- |
- |
5 |
- |
- |
- |
2. |
- |
- |
- |
- |
- |
- |
- |
- |
2.1 |
40 |
- |
40 |
20 |
- |
- |
- |
- |
2.2 |
40 |
- |
40 |
- |
20 |
- |
- |
- |
2.3 |
40 |
- |
50 |
- |
10 |
- |
- |
- |
2.4 |
40 |
- |
55 |
- |
5 |
- |
- |
- |
2.5 |
30 |
- |
50 |
- |
20 |
- |
- |
- |
2.6 |
50 |
- |
30 |
- |
20 |
- |
- |
- |
3. |
- |
- |
- |
- |
- |
- |
- |
- |
3.1 |
40 |
- |
- |
- |
20 |
40 |
- |
- |
3.2 |
40 |
- |
- |
- |
10 |
50 |
- |
- |
3.3 |
40 |
- |
- |
- |
5 |
55 |
- |
- |
4. |
- |
- |
- |
- |
- |
- |
- |
- |
4.1 |
40 |
- |
- |
- |
20 |
- |
40 |
- |
4.2 |
40 |
- |
- |
- |
10 |
- |
50 |
- |
4.3 |
40 |
- |
- |
- |
5 |
- |
55 |
- |
5. |
- |
- |
- |
- |
- |
- |
- |
- |
5.1 |
40 |
- |
- |
- |
20 |
- |
- |
40 |
5.2 |
40 |
- |
- |
- |
10 |
- |
- |
50 |
5.3 |
40 |
- |
- |
- |
5 |
- |
- |
55 |
For preparation of mixture initial components have been weighed
on analytical weights, then crushed before passage through a sieve 02 and mixed in the ratio
corresponding to the composition of glaze and shut by the distilled water. Mass was carefully
mixed and inflicted on the preliminary moistened ceramic burnt and burned at the temperature 1000 and 1100°C.
CONCLUSIONS
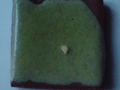 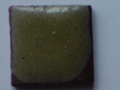 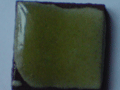
The following conclusions are made as a result of research. The studied wastes can be
used as basic components of ceramic glaze. The temperature of 1100 °C is optimum for the poured burning, transparent glassy coverage being produced.
© DonNTU 2008 Oberemok
|