Содержание
- Введение
- Обзор состояния вопроса механизации погрузочно-разгрузочных
работ и постановка цели работы
- Теория процесса механизации погрузочно-разгрузочных работ
- Алгоритм и программа расчета
- Исследование влияния интенсивности входящего потока заявок
на характеристики системы
- Практическое применение методики
- Выводы
Введение
Техническое перевооружение современных предприятий, внедрение прогрессивных технологий и технологических схем создают условия для концентрации производства, повышения производственной мощности предприятий, как следствие, повышается трудоемкость производства.
Особенно трудоемкими являются погрузочные, разгрузочные, транспортные и складские процессы, около 70% которых выполняется вручную. Численность трудящихся, занятых на этих процессах, составляет свыше 20% общей численности рабочих. Кроме этого на выполнение погрузочно-разгрузочных работ отвлекаются рабочие основных профессий [10].
Объем погрузочно-разгрузочных работ на предприятиях различных отраслей составляет сотни миллионов тонн различных грузов. Внедрение современных методов выбора в конкретных условиях оптимальных технических решений способствует общему повышению производительности труда, сокращает время простоя транспорта под погрузочно-разгрузочными операциями и этим самым ускоряет его оборот, облегчает условия труда, снижает себестоимость транспортных работ на предприятиях.
1. ОБЗОР СОСТОЯНИЯ ВОПРОСА МЕХАНИЗАЦИИ ПОГРУЗОЧНО-РАЗГРУЗОЧНЫХ РАБОТ И ПОСТАНОВКА ЦЕЛИ РАБОТЫ
1.1 Анализ работ по теории процесса механизации погрузочно-разгрузочных работ
Результаты проведеноого анализа работ по теме Вы можете найти в библиотеке.
1.2 Актуальность темы
Вопросом рационального выбора оборудования для механизации подъемно-транспортных работ начали заниматься еще в 50-е годы т.к. уже тогда было очевидным, что механизация и автоматизация процессов погрузки, разгрузки, транспортирования и складирования приведет к значительному росту производительности производства и сокращению экономических затрат.
Большой вклад в разрешение данной проблемы внес Егоров К.А. В его работах: «Механизация транспорта основных цехов машиностроительных заводов», «Основы механизации погрузочно-разгрузочных работ в металлургии», «Справочник механизатора погрузочно-разгрузочных и транспортных работ» рассматривается вопрос механизации для конкретных производств, предложены методики расчета необходимого парка оборудования, его производительности и определения эксплуатационных расходов.
Работа ученного Аннинского Б.А. «Погрузочно-разгрузочные работы. Проектирование и расчет систем комплексной механизации» стала основой для многих авторов, которые в дальнейшем участвовали в разрешении данной проблемы. Здесь уже поставлен вопрос применения математических методов при проектировании и расчете систем комплексной механизации.
В этом направлении вели разработки и исследования ВНИИПТмаш, НИИтракторосельхозмаш [9], НИИ информации по тяжелому, энергетическому и транспортному машиностроению [11].
На современном этапе определенным вкладом в решение этой проблемы является разработка курса «Техника и технология погрузки, разгрузки, транспортирования и складирования в энергоемких производствах», с участием авторов: Будишевского В.А., Гутаревича В.О., Маценко В.Н. и Сулимы А.А. В нем излагаются основы расчета конструкции основных типов машин промышленного транспорта, применяемых на складах, даны общие методы выбора основных параметров схем механизации погрузочно-разгрузочных работ.
Отсутствие современных методов технико-экономического анализа выбора в конкретных условиях оптимальных технических решений является одной из причин высокой трудоемкости погрузочно-разгрузочных работ.
Механизация и правильная организация вспомогательных работ, в том числе погрузочно-разгрузочных, транспортных и складских, позволяет высвободить большой процент вспомогательных рабочих и, таким образом, значительно повысить общий уровень производительности труда на предприятиях.
На основании вышеизложенного тема настоящей работы является актуальной.
1.3 Цель и задачи работы
Цель – разработка и апробация научно обоснованной методики выбора рационального подъемно-транспортного оборудования на базе вероятностного анализа его рабочих процессов на примере мостовых кранов.
Для достижения вышеуказанной цели поставлены следующие задачи:
1. Проанализировать существующие методики выбора оборудования для механизации подъемно-транспортных работ.
2. Разработать расчетные схемы зон обслуживания с одним и несколькими мостовыми кранами.
3. Составить математическую модель, описывающую процесс погрузки-разгрузки.
4. Составить математическую модель для усовершенствованной методики выбора погрузочно-разгрузочного оборудования.
5. Создать программу, с помощью которой определить основные характеристики системы.
6. Построить графики зависимостей, отображающих влияние числа кранов и интенсивности входящего потока на погрузочно-разгрузочный процесс.
7. Разработать алгоритм методики.
8. Показать практическое применение разработанной методики.
2. ТЕОРИЯ ПРОЦЕССА МЕХАНИЗАЦИИ ПОГРУЗОЧНО-РАЗГРУЗОЧНЫХ РАБОТ
2.1 Вступительное замечание
Погрузочно-разгрузочные работы, обеспечивающие технологический процесс механизации перегрузочно-транспортных циклов, в ряде случаев по своему характеру близки к процессам массового обслуживания, что позволяет при расчетах пользоваться вероятностными методами и, в частности, теорией массового обслуживания.
При последующем изложении удобно пользоваться некоторыми распространенными исходными положениями и формулировками теории массового обслуживания.
Поток транспортно-технологических требований (заявок) на обслуживание принято называть входящим потоком заявок, совокупность погрузочно-разгрузочных, транспортных и других установок механизации, обслуживающих заявки - системой обслуживания, продолжительность выполнения операций — временем обслуживания.
Входящий поток заявок формируется случайным образом, поэтому применяются аналитические методы определения средней длины очереди и среднего времени ожидания.
Исходя из вышеизложенного, склад можно представить как систему массового обслуживания (рис. 1):
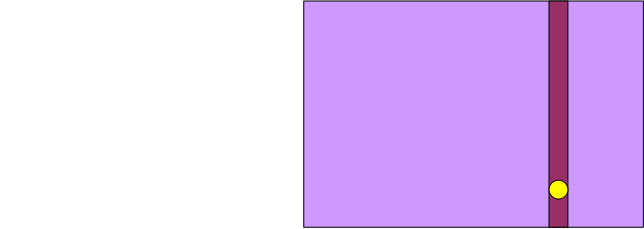
Рис.1 Склад как система массового обслуживания
В работе [3] предлагается рассматривать входящий поток заявок на погрузочно-разгрузочные работы как поток случайных событий с пуассоновским распределением частоты поступления требований. В этом случае вероятность поступления k заявок в систему за время t может быть рассчитана по следующей формуле:
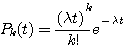
где – среднее число заявок в единицу времени, т.е. интенсивность входящего потока заявок.
Однако, для практического применения подхода, изложенного в работе [3], при обосновании погрузочно-разгрузочного оборудования складского хозяйства следует учесть возможность варьирования положения начальных и конечных точек маршрутов перемещения грузов по территории склада. В первом приближении эти точки могут быть рассмотрены как случайные.
2.2 Расчетная схема склада
Для составления математической модели погрузочно-разгрузочного процесса, с учетом вышеизложенного материала разработана расчетная схема зоны обслуживания с одним мостовым краном (рис.2a):
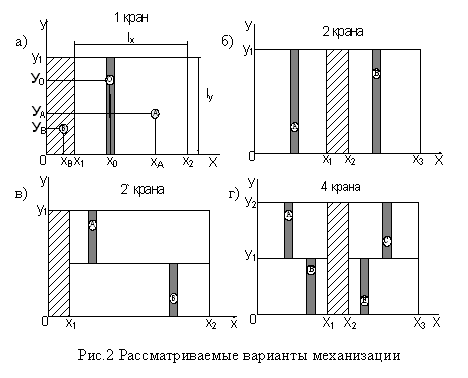
Склад в данном случае делится на две зоны: зона хранения с координатами (х1, х2, у1, у2) и погрузочно-разгрузочная зона с координатами (0, х1, у1). Начальное положение крана определяется точка О с координатами (х0, у0). Груз транспортируется из точка А (ха, уа) в точка В(хв, ув). Такая схема очень удобна т.к. учитывает изменение параметров. Процесс погрузки описывается математической моделью, которая позволяет определить время выполнения одной операции при различных координатах точек О, А и В.
Разработанная методика учитывает возможность использования нескольких обслуживающих агрегатов. При этом изменяются расчетные схемы зон обслуживания. На рис.2 показаны рассматриваемые варианты механизации с одним (2а), двумя (2б,в) и четырьмя (2г) мостовыми кранами.
2.3 Математическая модель погрузочно-разгрузочного процесса
Начальными данными для математической модели являются размеры зоны хранения (lx, ly) и погрузочно-разгрузочной зоны, скорости передвижения крана (Vk) и тележки (Vt), скорость подъема груза (Vp), а также высота, на которую поднимается (Hp) и опускается (Ho) груз.
Время выполнения операции – это сумма времени на выполнение отдельных частей операции. Движение крана считаем простым. Погрузочная операция состоит из следующих частей:
- перемещение крана из начального положения (точки О) к грузу, который требуется погрузить. На передвижение крана вдоль оси x затрачивается время t1;
- на передвижение тележки вдоль оси y до точки А затрачивается время t2.
- опускание крюка и подъем груза выполняется за время t3.
- перемещение груза из точки А в точку В. Передвижение крана вдоль оси х выполняется за время t4.
- на передвижение тележки вдоль оси y до точки В затрачивается время t5.
- опускание груза в точку В происходит за время t6.
При этом случайным образом генерируются различные координаты точек О, А и В.
Таким образом, математическая модель времени выполнения операции погрузки выглядит следующим образом:



Склад как система массового обслуживания может иметь различные характеристики, отражающие эффективность ее работы. Для того чтобы рассчитать эти характеристики необходимо определить математическое ожидание времени обслуживания. Эта величина, в отличие от среднеарифметической, дает возможность получить более точные значения, что в последствии влияет на точность результатов. Математическое ожидание времени выполнения одной операции определяем по формуле:
, c
Вероятность того, что одновременно на выполнении требований будут заняты п обслуживающих агрегатов, характеризующая долю времени, когда все п агрегатов загружены одновременно, равна:

где - вероятность того, что поступит количество требований равное количеству обслуживающих агрегатов:
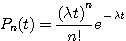
- вероятность поступления количества требований меньшего, чем количество обслуживающих агрегатов.
На погрузочно-разгрузочных операциях могут образовываться очереди при определенной интенсивности поступления заявок. Вероятность образования очереди на обслуживание, т.е. вероятность поступления количества заявок превышающего количество обслуживающих агрегатов выражается формулой:

Анализируя полученные значения характеристик можно принимать решения о введении дополнительных единиц обслуживающих агрегатов либо об их выводе в связи с нецелесообразностью использования.
2.4 Разработка усовершенствованной методики выбора погрузочно-разгрузочного оборудования с учетом сложной конфигурации зон обслуживания
Склад с одним мостовым краном (рис. 3) может быть разделен на три зоны: погрузочно-разгрузочную, зону хранения и зону проходов. Конфигурация этих зон может быть различной и определяется планировкой склада. Зоны представляют собой плоскости, в которых происходит движение точек. груз транспортируется из точки А, которая принадлежит зоне хранения Т, в точку В, которая принадлежит зоне погрузки-разгрузки. Начальное положение крана определяется координатами точки О, которая принадлежит и зоне хранения и погрузочно-разгрузочной зоне.
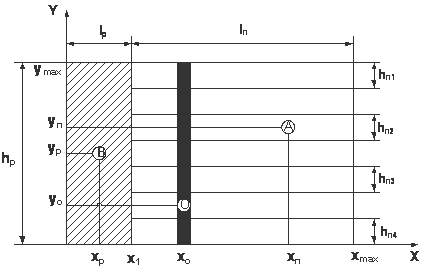
Рисунок 3 - Расчетная схема скла
Для описания процесса погрузки разработана следующая математическая модель.
Точка . Погрузочно-разгрузочная зона описывается следующим уравнением:

Точка .
Зона погрузки:

Точка .
Если время передвижения тележки больше времени передвижения моста, то общее время выполнения операции вычисляем по формуле: 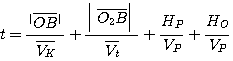
Если же время передвижения тележки меньше времени передвижения моста, то
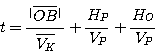
Таким образом, временем выполнения операции будет максимальное из двух вышеперечисленных:
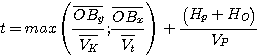
3. АЛГОРИТМ И ПРОГРАММА РАСЧЕТА
З.1 Алгоритм методики
Основываясь на вышесказанном, была разработана методика выбора рационального оборудования.
Начальными данными, как отмечалось ранее, являются размеры зоны хранения и погрузочно-разгрузочной зоны (Х1, Х2, У1), скорости передвижения крана (Vk) и тележки (Vt), скорость подъема груза (Vp), а также высота, на которую поднимается (Hp) и опускается (Ho) груз. Начальные данные во многом зависят от принятой расчетной схемы, поэтому ее разработку также лучше осуществлять на данном этапе. Таким образом, методика учитывает различные габариты складской и погрузочно-разгрузочной зон, а также использование обслуживающих агрегатов с различными характеристиками.
Следующим этапом является составление математической модели системы. Этот процесс подробно описан в пункте 2.3. Разработанная математическая модель позволяет определить время выполнения одной операции при различных координатах точек О, А и В, что выполняется на третьем этапе.
В четвертом блоке определяем основные характеристики системы. Математическое ожидание времени обслуживания, которое показывает средне время выполнения заявки. Вероятность того, что все агрегаты будут загружены одновременно, которая равна отношению вероятности поступления количества требований равному количеству агрегатов к вероятности поступления количества требований меньше, чем количество агрегатов. Вероятность того, что поступит количество заявок, превышающее число обслуживающих агрегатов.
Методика учитывает возможность использования нескольких обслуживающих агрегатов. При этом изменяются расчетные схемы зон обслуживания и, соответственно, значения основных характеристик системы. Эти изменения отображают графики зависимостей основных характеристик от интенсивности потока заявок. Построение этих графиков является заключительным этапом методики, а их анализ позволяет выбрать рациональный вариант механизации погрузочно-разгрузочных работ.
3.2 Программа расчета
Для выполнения расчетов было выбрано программное средство Mathcad 11. Он содержит обширный набор инструментов для реализации графических, аналитических и численных методов решения математических задач на компьютере. В среде Mathcad доступны сотни операторов и логистических функций, предназначенных для численного и символьного решения технических проблем различной сложности.
При расчетах использовались характеристики мостового двухбалочного крана харьковского экспериментального завода грузоподъемностью 10т.
Следуя разработанному алгоритму, была написана программа. Она позволяет увидеть не только конечный результат, но промежуточные расчеты.
С помощью написанной программы определяем время выполнения погрузочно-разгрузочной операции и строим график закона его распределения (рис.4):
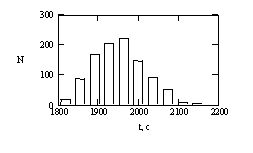
Рисунок 4 - Диаграмма распределения времени выполнения операции
Среднее время выполнения одной операции для данного крана и расчетной схемы с одним мостовым краном равно:
c
Вероятность одновременной загруженности всех агрегатов при интенсивности входящего потока заявок з/ч равна Еn=0,729. Эта зависимость отображена на графике (рис.5):
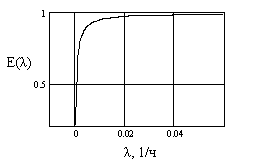
Рисунок 5 - График зависимости одновременной загруженности всех агрегатов от интенсивности входящего потока заявок
Вероятность образования очереди в этом случае равна Dn=0,748. Зависимость вероятности образования очереди на обслуживание от интенсивности входящего потока имеет вид (рис.6):
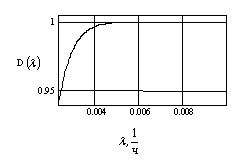
Рисунок 6 - График зависимости вероятности образования очереди от интенсивности входящего потока заявок
В результате произведенных расчетов можно сделать вывод о неэффективности использования этой модели мостового крана при данных исходных параметрах т.к. скорость выполнения требований не достаточна для обслуживания такого количества заявок, что приводит к 75% вероятности образования очереди на обслуживание.
Таким образом, написанная программа реализовывает математическую часть разработанной методики. Дает возможность получить количественные значения величин, а также проследить характер их зависимостей.
4. ИССЛЕДОВАНИЕ ВЛИЯНИЯ ИНТЕНСИВНОСТИ ВХОДЯЩЕГО ПОТОКА ЗАЯВОК НА ХАРАКТЕРИСТИКИ СИСТЕМЫ
Склад представленный в виде системы массового обслуживания является открытой системой. Как всякая открытая система она имеет входные и выходные параметры. Входящей величиной для нашей системы является поток требований на обслуживание. Продуктивность работы системы во многом зависит от количества обслуживающих агрегатов и от их характеристик. Таким образом, интенсивность входящего потока и число обслуживающих агрегатов – это два основных фактора влияющих на работу системы и на ее характеристики.
Зависимость основных характеристик системы от этих факторов отображают следующие графики (рис.7):
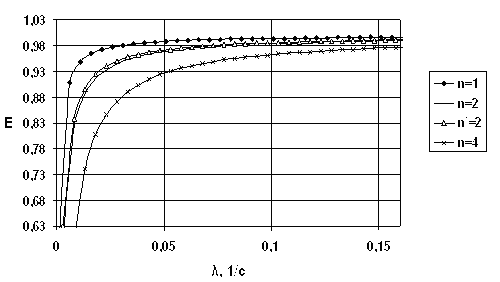
Рисунок 7 - Зависимость одновременной загруженности всех агрегатов от интенсивности потока
График зависимости вероятности одновременной загруженности всех агрегатов от интенсивности потока показывает, что при одинаковом потоке входящих заявок одновременная загруженность всех агрегатов уменьшается с увеличением числа агрегатов. Это дает возможность проследить, при какой величине входящего потока требуется увеличивать количество погрузочно-разгрузочного оборудования (рис.8):
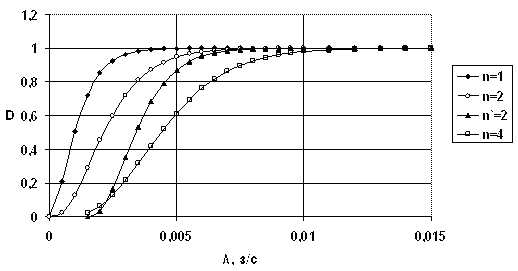
Рисунок 8 - Зависимость вероятности образования очереди на обслуживание от интенсивности потока заявок
График зависимости вероятности поступления количества заявок большего, чем обслуживающих агрегатов от плотности потока заявок дает возможность увидеть, при какой плотности потока заявок возникает очередь на обслуживание для каждого количества обслуживающих агрегатов.
Из графиков видно, что в случае с двумя кранами, изменение расчетной схемы незначительно влияет на величину вероятности одновременной загруженности всех агрегатов и в то же время существенно влияет на вероятность образования очереди.
Из зависимостей Е( ) и D( ) видно, что D( )=0,8:
для 1 крана при =0,0015, а Е( )=0,75;
для 2 кранов при =0,002, а Е( )=0,6;
для 2` кранов при =0,002, а Е( )=0,6;
для 4 кранов при =0,035, а Е( )=0,5.
При D( )>0,8 для всех случаев Е( ) находится в пределах 0,5…0,75, что свидетельствует о недоиспользовании оборудования [3]. Таким образом показатели Е и D являются противоречивыми. Для систем, допускающих наличие очереди на погрузочно-разгрузочных работах без существенных издержек, следует использовать критерий Е. В то же время выбор оборудования в системах, для которых недопустима задержка выполнения погрузочно-разгрузочных работ, более значим показатель D.
Таким образом, построенные графики являются завершающим этапом разработанной методики и позволяют увидеть характер влияния интенсивности потока заявок на работу системы для каждого варианта механизации.
5. ПРАКТИЧЕСКОЕ ПРИМЕНЕНИЕ МЕТОДИКИ
На практике данную методику можно применять при выборе средств механизации, в частности, мостовых кранов. Она позволяет сделать рациональный выбор среди множества моделей мостовых кранов, применимых в конкретных условиях.
Ниже приведена сравнительная таблица (табл.1), показывающая эффективность применения трех различных моделей мостовых кранов в условиях разработанной расчетной схемы: Х1 = 50 м, Х2 = 100 м, У1 = 32 м, Нр = 10 м.
В качестве первой модели был взят мостовой двухбалочный кран Харьковского экспериментального завода грузоподъемностью 10т.
Вторая модель КМ10(3К) – двухбалочный мостовой кран Бурейского кранового завода. Третья модель является модификацией этой модели, она имеет более высокие скоростные характеристики (табл.1):
Таблица 1 - Сравнительная характеристика
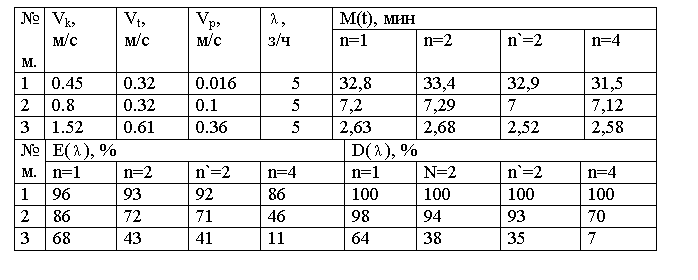
Таким образом, видно, что среднее время выполнения заявки второй модели в 4,5 раза превышает среднее время выполнения заявки первой модели, а вероятность образования очереди при этом сокращается на 2 – 30 %. Из таблицы также видно, что при использовании четырех агрегатов вместо одного время выполнения одной заявки уменьшается в среднем на 0,7 мин. В сумме выигрыш во времени в час составляет 3,5 мин при данном потоке заявок.
Вероятность одновременной загруженности всех агрегатов при использовании третьей модели меньше на 30 – 75 %, в зависимости от числа обслуживающих машин, чем при использовании первой модели. Но из таблицы также видно, что использование четырех агрегатов третьей модели будет не рациональным т.к. будет иметь место простой кранов.
Таким образом, видно, что показатели эффективности у трех рассматриваемых моделей существенно отличаются. Поэтому разработанная методика может иметь широкое применение при выборе средств механизации погрузочно-разгрузочного оборудования, так как полученные с помощью нее результаты позволяют принять обоснованное и рациональное решение.
ВЫВОДЫ
1. Проведенный обзор литературы показал (11 источников), что большинство источников содержит множество рекомендаций по применению различного погрузочно-разгрузочного оборудования и методики, основанные на критериях экономичности и производительности. В одном из источников рассмотрен вопрос применения теории массового обслуживания для описания погрузочно-разгрузочных работ. Однако большинство из них не учитывают тот факт, что погрузочно-разгрузочные работы по своему характеру близки к процессам массового обслуживания. Вследствие нерационального выбора оборудования для механизации погрузочно-разгрузочных работ увеличиваются затраты связанные с простоями основного производственного оборудования либо к завышенной стоимости последнего.
2. Разработаны расчетные схемы зон обслуживания для различного количества обслуживающих агрегатов, а именно с одним, с двумя и с четырьмя мостовыми кранами.
3. На основе разработанных схем составлена математическая модель погрузочно-разгрузочной операции, которая учитывает возможность использования одного либо нескольких обслуживающих кранов. Разработанная математическая модель позволяет определить время выполнения одной операции при различных координатах точек О, А и В, описывающих начальное положение крана, груза и места погрузки.
4. Для возможности многостороннего обоснования выбора погрузочно-разгрузочного оборудования, в работе предложена еще одна методика подбора оборудования, учитывающая сложную конфигурацию зон обслуживания. Разработана усовершенствованная расчетная схема зон обслуживания и составлена к ней математическая модель.
5. Разработана программа, выполняющая расчет времени выполнения одной операции, среднего времени выполнении операции, вероятности одновременной загруженности всех агрегатов и вероятности образования очереди на обслуживание в системе Mathcad 11. Программа позволяет получить диаграмму распределения времени выполнения одной операции и графики зависимостей вероятностей от интенсивности потока заявок.
6. Используя результаты расчетов программы, построены обобщенные графики зависимостей вероятностей от интенсивности потока заявок для различного количества обслуживающих агрегатов, из которых видно при какой величине входящего потока заявок требуется увеличивать либо уменьшать число кранов для повышения эффективности работы всей системы.
7. С использованием разработанной методики был выполнен сравнительный анализ работы кранов трех моделей в расчетных условиях эксплуатации и показано, что значения величин, характеризующих эффективность работы системы, значительно отличаются. В частности время выполнения операции второй модели в 4,5 раза меньше чем у первой, а вероятность образования очереди при этом сокращается на 30 %.
Таким образом, разработанная методика может иметь широкое применение при выборе средств механизации погрузочно-разгрузочного оборудования, так как полученные с помощью нее результаты позволяют принять обоснованное и рациональное решение.
Работа была доложена на 7й международной научно-технической конференции «Горная энергомеханика и автоматизация» 23 ноября 2007г., а также на студенческой научной конференции «День науки» 17 мая 2007г.
ПЕРЕЧЕНЬ ИСПОЛЬЗУЕМОЙ ЛИТЕРАТУРЫ
- Абрамович И.И. и др. Грузоподъемные краны промышленных пред-приятий: Справочник/И.И. Абрамович, В.Н. Березин, А.Г. Яуре. – М.: Машиностроение, 1989. – 360с.
- Аннинский Ю.А. Погрузочно-разгрузочные работы. Проектирование и расчет систем комплексной механизации. - Л.: Машиностроение, 1975. – 344с.
- Вентцель А.Д. Курс теории случайных процессов. 2-е изд., доп. – М.: Наука. Физматлит, 1996.
- Граничин О.Н. Введение в методы стохастической оптимизации и оценивания: Учеб. пособие. – СПб.: Издательство С.-Петербургского Университета, 2003. – 131с.
- Егоров К.А. Механизация транспорта основных цехов машинострои-тельных заводов. – М., Л., 1949.
- Егоров К.А. Основы механизации погрузочно-разгрузочных работ в металлургии. 2-е изд. – М., 1952.
- Егоров К.А. Справочник механизатора погрузочно-разгрузочных и транспортных работ. – Л., 1979.
- Промышленный транспорт/Под ред. А.С. Гельмана, С.Д. Чубарова. – 3-е изд., перераб. и доп. – М.: Стройиздат, 1984. – 415с., ил. – (Спра-вочник проектировщика).
- Средства механизации подъемно-транспортных операций и погрузоч-но-разгрузочных работ. Таблицы применяемости и рекомендации по выбору подъемно-транспортных и погрузочно-разгрузочных средств. – М., 1963.
- Техника и технология погрузки, разгрузки, транспортирования и скла-дирования в энергоемких производствах. Под ред. В.А. Будишевского, А.А. Сулимы. – Донецк, 2000. – 350с.
- Шестаков К.М, Попов Ю.И. Механизация складов металла на маши-ностроительных заводах. – М., 1966.
|