|
|
«Черные металлы» июнь, 2003
Новая установка вдувания угля для снижения выбросов диоксина на аглофабрике
Бонт Л., Бюттьен К., Фурнель Р., Мершье Г., Питерс М.
Измерения, проведенные в 1996 г. фламандскими органами по охране окружающей среды выявили очень большое содержание диоксина в дымовых (отходящих) газах на агломерационной фабрике завода Sidmar.
Так как в то время не было практически никакой литературы по выбросам диоксина при работе агломерационных установок, то сначала было необходимо провести обширные исследования. Мероприятия, поэтапно внедряемые в процесс, в конечном счете дали простое решение «на конце трубы», позволившее сократить выброс диоксинов в атмосферу более чем на 97 %. Такой результат был достигнут при приемлемых издержках.
В зависимости от масштабов и типа оборудования сталеплавильного производства и эффективности мероприятий по поддержанию чистоты воздушного бассейна агрегаты черной металлургии могут быть главным источником выбросов диоксинов в атмосферу. Было установлено, что процесс агломерации в черной металлургии является основным источником выброса диоксинов.
Предварительные исследования показали, что имеющиеся технические средства для мусоросжигательных установок не могут быть непосредственно применены на агломерационных машинах из-за следующих факторов:
- большие объемные расходы потоков отходящих газов;
- разная температура отходящих газов;
- меняющиеся условия работы во время пуска и остановки;
- высокое удельное электросопротивление пыли
На заводе фирмы ThyssenKrupp Stahl AG была построена демонстрационная установка, включающая реактор для адсорбции диоксинов после электростатического фильтра. В качестве адсорбента (твердого поглотителя) был выбран лигнит (сорт угля). Был испытан также расположенный ниже по потоку окислительный каталитический преобразователь Эксплуатационники одной аглофабрики в Германии образовали проектный консорциум, к которому присоединились фирма Sidmar (Бельгия) и один французский металлургический завод.
Ввиду хорошей степени отделения на демонстрационной установке фирма Sidmar пришла к решению построить промышленную установку для вдувания угля с целью снижения содержания диоксинов в газах за агломашиной № 2. Эта установка имела производительность по агломерату 14400 т за 24 ч. После подтверждения правильности результатов в работу была введена аналогичная установка за агломашиной № 2 (производительность - 5300 т агломерата за 24 ч).
В данной статье рассматриваются технические подробности по двум агломашинам на заводе фирмы Sidmar и результаты обширной кампании измерений, проведенной на обеих установках. Так как к работе были привлечены несколько лабораторий, была достигнута высокая точность и воспроизводимость результатов измерений. Были проанализированы также различные гипотезы, имевшие целью сокращение выброса диоксинов. Первое улучшение в виде снижения выбросов на 85 % было достигнуто благодаря применению обожженной извести и оптимизации процесса. Дальнейшее уменьшение выбросов диоксина было возможно только с применением технологий «на конце трубы». Было принято решение о строительстве промышленной установки по вдуванию угля, основанной на результатах, полученных упомянутым выше проектным консорциумом. Применение адсорбентов, содержащих углерод, влечет за собой риск пожаров и взрывов. До выбора размеров установки были проведены некоторые исследования с целью удержания этой опасности под контролем. Необходимо было также провести измерения по ограничению выброса пыли. В статье обсуждаются и эти измерения, а также дается описание установки для вдувания угля, предназначенной для уменьшения выброса диоксинов.
Техническое описание агломерационных машин
В табл. 1 приводятся наиболее важные технические характеристики двух агломерационных машин на заводе фирмы Sidmar. Машина № 1 имеет суточную производительность 5300 т и машина № 2 - 14400 т агломерата. Годовая производительность составляет 6,84 млн. т. Расход отходящих газов равен 0,5 и 1 млн. м3 в час (при н.у.) соответственно. Охлаждение агломерата обеспечивается прямым обдувом десятью вентиляторами на агломашине № 1 и в циркуляционном цикле на агломашине № 2. На обеих агломашинах в зажигательном горне применяют коксовый газ. Очистка от пыли на сторонах спекания и охлаждения обеспечивается в электрофильтрах. Средняя температура отходящих агломерационных газов составляет около 140 °С.
Таблица 1 - Техническая характеристика агломерационных машин на заводе фирмы Sidmar
Параметры |
Единицы измерения |
Агломерационная машина |
№ 1 |
№ 2 |
Номинальная производительность |
т/м3 сут. |
33 |
40 |
Годовая производительность |
млн. т/год |
1,9 |
5,0 |
Полезная площадь спекания |
м2 |
175 |
484 |
Длина ленты |
м |
48 |
117 |
Ширина ленты |
м |
3,66 |
4,25 |
Кампания по измерению содержаний диоксина
В табл. 2 показано число измерений, проведенных в 1998-2002 гг. К работам были привлечены три разные лаборатории. Во время «измерительного» дня были организованы одно измерение продолжительностью 6 ч и два измерения по 3 ч. Это объясняет, почему число измерений больше числа «измерительных дней». Очень часто две разные лаборатории вели измерения в одно и то же время, что позволяло оценить точность и воспроизводимость получаемых результатов.
Таблица 2 - Кампания по измерению концентраций диоксина на агломашинах фирмы Sidmar
Год |
1998 |
1999 |
2000 |
2001 |
2002 |
2003 |
Одновременно проводившиеся измерения |
Дни измерений |
67 |
113 |
86 |
65 |
34 |
365 |
85 |
Лаборатория 1 |
128 |
209 |
158 |
61 |
34 |
590 |
- |
Лаборатория 2 |
43 |
11 |
0 |
0 |
0 |
54 |
54 |
Лаборатория 3 |
0 |
34 |
4 |
4 |
0 |
42 |
31 |
Общее число измерений |
171 |
254 |
162 |
65 |
34 |
686 |
- |
На рис. 1 показан разброс результатов измерений содержания диоксина при одинаковых условиях процесса. Для каждого дня измерений регистрировали два значения. Можно видеть, что отношение между максимальным и минимальным значениями составляло - 3. Разброс был типичным и не изменялся в зависимости от абсолютного уровня выбросов диоксина.
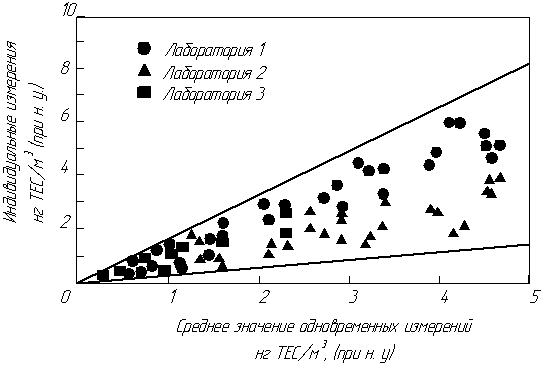
Рисунок 1 - Разброс измеренных значений выбросов диоксинов при одинаковых условиях агломерационного процесса
Различия между результатами измерения разных лабораторий были проверены. Эти данные показаны на рис. 2. Суммарный обзор представлен в табл.3.
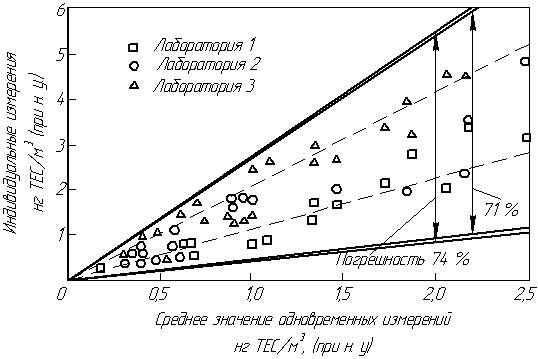
Рисунок 2 - Различия между результатами измерений в различных лабораториях
Таблица 3 - Различия между результатами измерений разными лабораториями
Отношение между лабораториями |
Отношение max/min |
Погрешность результата |
Число измерений |
Лаб. 1 к лаб. 2 |
5,88 |
70,9 % |
2 х 50 |
Лаб. 2 к лаб. 3 |
6,64 |
73,8 % |
2 х 25 |
Лаб. 1 к лаб. 3 |
1,77 |
27,8 % |
2 х 2 |
Расхождение между минимальным и максимальным значениями, полученными в разных лабораториях (отношение), составило ~ 6. Эти данные показывают, что к толкованию полученных показателей следует подходить с большой осторожностью. Ясно также, что различные измерения необходимы и для оценки эффективности мероприятий, предпринятых для уменьшения выброса диоксина в атмосферу.
Исследование гипотезы по возможностям уменьшения выброса диоксина
В 1998 г. было исследовано влияние хлоридов и VOC (летучих органических компонентов). При этом основывались на допущении о том, что концентрацию источников образования диоксинов необходимо сокращать до минимума. Для этого ввод (в аглошихту) загрязненной прокатной окалины, воды с повышенным содержанием хлоридов, пыли из электрофильтров и т.п. значительно сократили. Исследовали некоторые параметры процесса (например, высоту слоя спекаемой шихты, использование обожженной извести и вдувание извести в отходящие газы).
В результате было установлено, что химический состав агломерационной шихты значения не имеет.
В 1999 г. исследования были сосредоточены в основном на допущении того, что диоксины образуются в самом агломерационном процессе.
В окончательном выводе устанавливалось, что применение обожженной извести и оптимизация процесса спекания (например, более точный контроль точки сквозного спекания и улучшение проницаемости спекаемого слоя) могут обеспечить сокращение выбросов диоксина на 85 %.
Дальнейшее снижение выбросов диоксинов могло быть возможным только с применением технологий «на конце трубы». Было решено построить промышленную установку для вдувания угля с целью дальнейшего сокращения выбросов диоксинов.
Мероприятия по сокращению опасности пожара и взрывов и по ограничению выбросов пыли
В табл. 4 полужирным шрифтом выделены концентрации двух различных адсорбентов, которые могут спровоцировать взрыв. В случае адсорбента 1 взрыва можно избежать только добавлением порошкового известняка для создания инертной атмосферы. Такие же исследования были проведены и для оценки риска пожара. Следует отметить, что результаты в значительной степени зависели от специфического качества уловленной пыли агломерата. Их нельзя было распространить на другие агломашины.
Таблица 4 - Исследования взрывоопасности двух адсорбентов
Пыль агломерата |
Адсорбент 1 |
Порошковая известь |
Адсорбент 2 |
70 |
- |
- |
30 |
75 |
- |
- |
25 |
80 |
20 |
- |
20 |
85 |
15 |
- |
- |
40 |
40 |
20 |
- |
35 |
35 |
30 |
- |
30 |
30 |
40 |
- |
Добавление порошкообразной извести увеличивает пылевую нагрузку на электрофильтры. Необходимо оптимизировать работу электрофильтров, потому что на входе в них поступает большое количество пыли. Все электрофильтры были оборудованы периодически действующими зарядными устройствами, которые накладывают пики высокою напряжения (высокочастотные) на основное напряжение постоянного тока. Вследствие более высокого напряжения на электродах возможно более эффективное отделение пыли. Несколько испытаний было проведено для определения влияния типа адсорбента и его количества в сочетании с порошкообразным известняком на выбросы пыли (рис. 3).
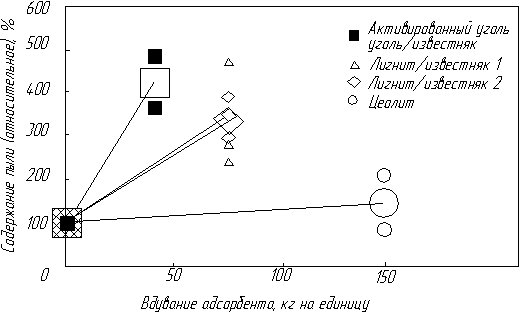
Рисунок 3 - Влияние типа адсорбента и его количества на выброс пыли при комбинировании адсорбента с порошкообразным известняком
Установка для вдування угля на агломашине № 2
В качестве адсорбентов на установке применяют порошкообразный лигнит или активированный уголь. Эти компоненты можно вдувать и одновременно. Установка состоит из двух бункеров вместимостью по 120 м3 каждый для хранения угля и извести, двух стендов для вдувания по 2 м3 каждый и смесительной станции, где адсорбент и уголь смешиваются между собой и транспортируются к точке вдувания в канал отходящих газов. Точка вдувания располагается в газопроводе отходящего газа между агломерационной установкой и электрофильтром, который применяется для электростатического осаждения пыли.
Бункер для хранения адсорбента выдерживает внутреннее давление 3 бар и снабжен предохранительными клапанами для защиты от взрыва. Наружный диаметр бункера составляет 4500 мм. Бункер для хранения извести имеет такие же размеры; он рассчитан на максимальное давление 40 мбар (изб.). Оба бункера рассчитаны и на разрежение 10 мбар (ниже атмосферного). В каждом бункере предусмотрены короба для взвешивания материалов.
Наружный диаметр бункеров для вдувания составляет 1300 мм. Они рассчитаны на внутреннее давление 2,5 бар, и в каждом предусмотрены три короба для взвешивания. В каждом бункере для вдувания имеются два дозирующих винта (шнека) - по одному для каждого дымохода с отходящими газами. Дозирующие винты транспортируют адсорбент и известь в смесительные камеры, откуда смесь всасывается в точку вдувания в канале отходящего газа. Фактический расход транспортирующего воздуха составляет 400 м3 в час (при н. у.) для каждой агломашины.
Обзор результатов
На рис. 4 показана динамика выброса диоксинов в 1997-2002 гг. Фактическая величина выбросов изменяется в пределах от 0,1 до 0,6 нг/м3 (при н. у.).
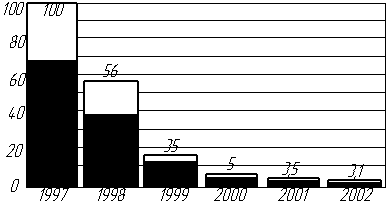
Рисунок 4 - Динамика выбросов диоксинов с 1997 по 2002 гг. (%)
На рис. 5 представлены результаты проведенных индивидуальных измерений. Ввод обожженной извести в сочетании с оптимизацией процесса обеспечил сокращение выбросов диоксинов на 85 %.
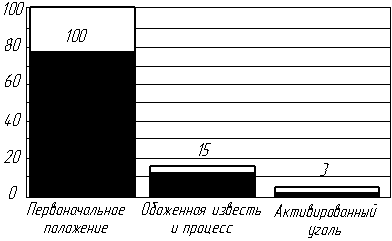
Рисунок 5 - Влияние отдельных мероприятий на уменьшение выбросов диоксинов (%)
Дальнейшее снижение выбросов на 80 % было достигнуто благодаря вводу в действие установки для вдувания угля. Все работы (принятие решения, инжиниринг и сооружение) на агломашине № 2 были выполнены в течение 6 месяцев. После оценки результатов в 2000 г. было принято решение о строительстве второй установки для вдувания и на агломашине № 1. Новая установка была введена в эксплуатацию во второй половине 2000 г.
Выводы и перспективы
Имеющиеся технические средства для мусоросжигательных установок не могут быть непосредственно применены на аглофабриках ввиду некоторых фундаментальных различий.
В 1998 и 1999 гг. на аглофабрике завода Sidmar была проведена обширная кампания по измерению содержания диоксинов в отходящих газах. Было выполнено более 400 измерений. Работали три разные лаборатории одновременно и по отдельности, что позволило оценить точность результатов и их воспроизводимость. Наиболее важный вывод заключался в том, что химический состав аглошихты в условиях аглофабрики завода Sidmar в отношении влияния на выброс диоксинов значения не имеет.
Были проверены несколько гипотез образования диоксинов и адсорбентов для их поглощения с целью снижения выброса диоксинов в атмосферу. Усовершенствование управления процессом и использование обожженной извести обеспечили сокращение выбросов на 85 %. Для дальнейшего сокращения выбросов было решено построить на аглофабрике промышленную установку для вдувания порошкообразного угля. Первая такая установка была введена в действие 8 декабря 1999 г. за агломашиной № 2. После получения хороших результатов в 2000 г. была пущена аналогичная установка и за агломашиной № 1. В итоге выбросы фактически сократились на 97 % (в 30 раз).
|