An urgency of job
The review of existing decisions
Statement of a problem
The account of influence of the previous zones of burning of fuel on optimum value of factor of the charge of air
in a considered zone
The description of results and plans for the future
Literature
An urgency of job
Automation of management by technological processes and manufacture plays the important role in continuous increase in output in our country. The intensification and complication of technological processes, growth of individual capacity of units and increase of requirements to quality of finished goods according to the international standards do impossible management of units without systems of automation.
Now complex automation at which on automatic control are translated as the basic, and auxiliary processes, units, sites of the enterprise is made.
In our country the great value is given to theoretical and practical questions of automation of productions. New opportunities for highly effective automation of technological processes in metallurgy open introductions of the newest devices and means of the automation, the automated control systems of technological processes (ACSTP), application of microprocessors, the micro-computer, robotics. Therefore for wide introduction of automatics the knowledge of bases of automation of technological processes is necessary.
The review of existing decisions
Now on the majority of heating furnaces about temperature of the metal which is being the furnace, in most cases judge on temperature of working space of zones. Often in one zone mount some sensitive elements of gauges of temperature with the purpose of the control of uniformity of temperature of a zone or reception of separate signals for measurement and regulations.
Regulation of temperature is carried out by change of thermal loading of a zone. Thus in one systems of regulation of temperature of a zone the regulator of temperature operates submission of fuel, and in others – submission of air. In the first case proportion of quantities of fuel and air it is reached by influence of a regulator of a parity on submission of fuel, in the second – on submission of air.
One of effective and accessible ways of decrease in specific expenses of thermal energy in metallurgical manufacture is perfection of management by process of burning of fuel in working space of furnaces.
Systems of regulation of a parity of fuel known now and air share on opened and closed.
The opened systems providing regulation of a mode burning of fuel on the basis of the information on charges of fuel and air, brought to the furnace, have a number of the lacks connected with impossibility of the account knockout of air from air lines on sites, located after the measuring device; impossibility of the account backlashes in a joint of adjusting body with the executive mechanism.
The systems of automatic control closed on adjustable size provide higher quality of management in comparison with the opened systems since in them automatic indemnification of all indignations is provided and there is an opportunity to estimate result of drawing of operating influences.
One of real opportunities of construction of the closed control system of a mode of burning of fuel is use of automatic gas analyzers for the control of structure of products of burning of fuel.
Essential feature of devices of the automatic gas analysis is their significant detention lag. For this reason dynamic characteristics of the closed systems are defined of detention lag of the gas analysis and mismatch dynamics of a mode of burning of fuel.
For multizone heating ardent furnaces construction of the closed system of regulation by process of burning of fuel becomes complicated that these objects have uniform system of removal of products of burning from all zones and it is rather difficult to define on structure of departing products of combustion in what of zones there was an infringement of burning.
Alongside with the systems incorporating a gas analyzer, attempts of creation of the closed systems of extreme regulation have been undertaken. The theoretical precondition for realization of such systems is extreme dependence of temperature of a torch on factor of the charge of air in working space of a zone of the furnace. However practical approbation of such system has found out its unfitness for operation of that automatic optimizer did not provide allocation of a useful signal about change of average temperature of a torch on a background of casual fluctuations of radiation of a torch and the measured values of its temperature have appeared commensurable with average change of temperature of the torch, the caused maximum deviation of a parity between charges of fuel and air.
By virtue of the listed factors, the closed systems of automatic control by a mode of burning of fuel in working space of ardent heating furnaces of a wide circulation have not received. Now the cores are the opened control systems of a mode of burning of fuel which are effectively enough used on the heating furnaces equipped by two-wire torches of type « a pipe in a pipe ». The basic condition of use of the opened control systems are the exact account and indemnification of all external indignations. First, it is necessary to reduce to a minimum backlash in joint adjusting body with the executive mechanism or to provide the algorithms, allowing them to consider. Secondly, it is necessary to enter amendments into indications of flowmeters for reduction of the measured sizes normal conditions at a deviation of values of pressure and temperatures of gas and air. At performance of these conditions to become obvious known advantages of the opened systems, the system of automation, its reliability and efficiency becomes simpler. The satisfactory decision of such problem became possible only at use of means of digital computer facilities.
Now have received a wide circulation of system with realization of direct digital management of technological parameters. Use of such management raises accuracy of realization of operating influences, promotes improvement of quality of regulation and reduces material inputs on creation of technical maintenance.
Statement of a problem
The problem of optimum control of technological objects consists in maintenance of such conducting technological process which allows to receive production of demanded quality at the minimal specific expenses. However this problem is not considered in full, that speaks difficulty and bulkiness of strict mathematical statement which becomes complicated also that a number of the important parameters influencing a course of technological process, are random variables. With reference to a problem of management a mode of burning of fuel in ardent heating furnaces a random variable is, for example, time of stay of metal in working space, i.e. time of heating..
Proceeding from that the developed subsystem of management will work as a mode of burning of fuel in structure of ACSTP a site of heating furnaces principles of optimization of management in the given work are not considered by a temperature mode of furnaces. Only imitating model of heating of metal for reception of necessary parameters of heating for the further calculations is used. Also it is necessary, that distribution of a thermal stream along working space of the furnace is optimum, and change of temperature of a surface of heated up preparations corresponds to this distribution.
Management of a mode of burning of fuel is usual reduce to the decision of a problem on its full burning in zones of the furnace, and quality of this process estimate on power parameters: to temperature of the gas environment, a thermal stream on metal or heat absorption metal, proceeding from that dependence of these parameters on factor of the charge of air (
) has extreme character. I.e. the theoretical maximum of the characteristic is necessary on the value equal 1.0, corresponding full burning of fuel. As show researches, the maximal temperature in zones of the furnace, at burning gaseous fuel, is reached at the values equal 1.05-1.15, because of various conditions of mixture of fuel and air in torches of various type and because of different theoretical quantity of air, necessary for full burning various kinds of gaseous fuel. On the other hand, at space of zones of the furnace there is the superfluous atmospheric air getting from an environment through windows ïîñàäà and delivery (in forwardflow-counterflow furnaces these sites of working space are characterized by the lowered value of internal pressure), and also through an element of a laying. Therefore it is considered, that in real conditions full burning of fuel is reached at , equal 1.0, that corresponds to theoretical value.
However the factor of the charge of air influences not only heat exchange, but also on mass exchange in furnaces: change of size
is accompanied by change of an oven atmosphere. At
in the furnace the regenerative atmosphere is created, and at
- oxidizing which leads to the raised oxidation of metal and essential deterioration of economic parameters of work of the unit. Practical value is represented only with that statement of a problem of optimum control which considers oxidation metal though not always losses from generation of scale surpass expenses for fuel. It is obvious, that there is the best combination of managements (i.e. charges of fuel and air on zones) at which the set temperature mode of heating is observed and expenses for fuel and generation of scale are minimized.
The account of influence of the previous zones of burning of fuel on optimum value of factor of the charge of air
in a considered zone
By consideration of values
in a real course of technological process, it is necessary to consider structure and quantity of products of the burning acting in the considered zone from previous or the previous zones, since values
for various zones are various.
The described correction is convenient for spending to sequences, return to a course of technological process (since tap of products of burning of fuel is carried out in an interval between methodical and the first welding zones). Convenience consists that products of burning of the fuel, leaving a soaking zone, consist of products of burning of the fuel brought only in it a zone. It is obvious, that by consideration of a soaking zone correction is not required. By consideration of processes in the second welding it is visible, that the products of burning leaving it will consist of the sum of products of burning of gas of this zone and products of burning of the gas, acting of a soaking zone.
And their quantity will be equal to their sum, and the chemical compound will depend on value of factor of the charge of air sold in these zones. Thus, that the total structure of products of burning of fuel being space of the second welding to a zone would correspond to the structure received at realization of value
for this zone, it is necessary to correct this value in view of quantity and structure of products of the burning acting from previous (in this case, soaking) zones.
For correction of value
in a considered zone it is necessary to know a chemical compound of fuel and structure of products of combustion at various factors of the charge of air.
The algorithm of calculation of corrected value of factor of the charge of air
looks as follows:
-definition of value
In a considered zone (as an example, the second welding zones);
-on the basis of this value and sizes of the charge of gas in a considered zone define specific quantity of products of burning of fuel and absolute value of this size -
;
-on the basis of this value and size of the charge of gas in the previous zone and value
, we define specific quantity of products of burning of fuel
;
-we work out the equation of material balance in the form of:
(1)
Thus there is an error since the quantity of products of burning of fuel formed in a considered zone at optimum value of factor of the charge of air is accepted equal to quantity of products of burning of the fuel, formed in the same zone at the corrected value of factor of the charge of air. This error can be reduced a method consecutive ïðèáëèæåíèé. Already on the second step of iterations it does not exceed 1 %;
-we define the corrected value
from the equation (1):
The same value is used as the first approach an iterative method, and after the second step is accepted as demanded value, at realization which in working space of the second welding zones, in it will be established such chemical compound of products of burning of fuel which would correspond to realization
by independent consideration of the processes proceeding in it.
Passing to the first welding it is necessary for zone to consider, that the quantity of products of burning leaving it is equal to the sum of products of burning this zone and to total receipt from the second welding and soaking zones.
Value of size
is corrected here to similarly above described algorithm. The given algorithm of correction of value
can function in a subsystem of management of a mode of burning of fuel in real time.
The description of results and plans for the future
In the object-oriented environment of programming Borland C ++ Builder 6.0 the program which provides calculation of structure of products of full/incomplete combustion of fuel, heating of metal, components thermal and exergical of the furnace has been made.
Calculation was made proceeding from technical characteristics ñåìèçîííîé the methodical furnace with walking beams Open Societies «ÌÌP by Ilyich». The factor of the charge of air changed in ranges 0,7..0,9 and 1,0..1,2 with step 0,05, and in a range 0,9..1,0 with step 0,01.
Results of calculation of one-dimensional bilateral model of heating of metal are resulted in figure 1.
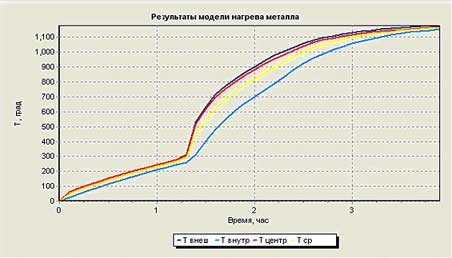
Figure 1 – Results of calculation of model of heating
Calculation of components thermal and exergical balances is made for zones of the methodical furnace. We shall consider results of modelling on an example of the first welding zones. For it in table 1 are compared power and exergic balances at factor of the charge of air 0,98.
Table 1 – Power and exergical balances (
)
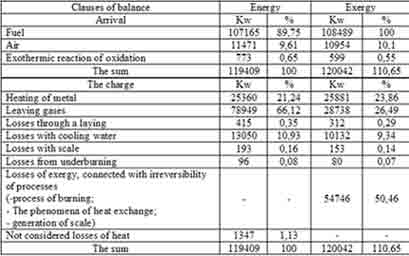
In figure 2 the graphic representation of the given balance made in conformity with table 1 is given.
Comparison of two balances allows to draw a conclusion, that in exergical balance the estimation of separate components essentially differs from a corresponding estimation of components in power balance. First of all we shall note, that in exergical balance products of burning are presented by smaller sizes, than in power. Energy, transferable a stream of products of burning, quantitatively is much less, than chemical energy of fuel.
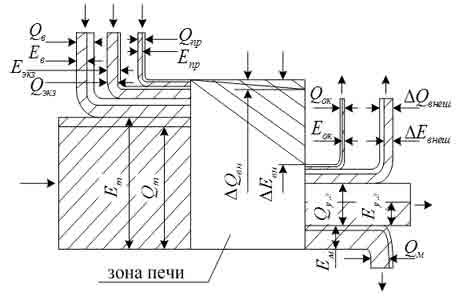
Figure 2 – Comparative balance energy- exergy for the first welding zones of the methodical furnace
In power balance it is not visible influences of many factors reducing perfection of process. In particular, in clause of the charge losses of exergy, connected with irreversibility of processes are rather essential. Careful exergical the analysis allows to find out sources of these losses and ways of their downturn.
So, for example, exergy products of combustion leaving the furnace it is possible to reduce due to recuperation (owing to recuperation the temperature of leaving products of combustion decreases), losses of exergy at irreversible burning can be reduced by enrichment of air by oxygen and heating of components (at heating of air the quantity of products of combustion due to reduction of quantity of fuel decreases).
In exergical balance as well as in power, it is not visible, directly the big influence which having warmed up air renders on the charge of fuel.
In work have been carried out some comparative experiments for research of dependence of exergical losses and the charge of fuel from temperature of heating of air. Results are resulted in figures 3 and 4.
From figure 3 it is visible, that with increase in temperature of warmed up air the charge of the fuel submitted on a zone, decreases, that allows to save it. As a result of heating of air decreases not only temperature of products of the burning leaving in an environment, but also and their quantity (owing to reduction of quantity of fuel).
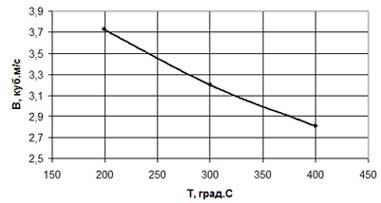
Figure 3 – Dependence of the charge of fuel on temperature for the first welding zones of the methodical furnace
At exergical the analysis the additional useful effect, namely, reduction of losses exergy, caused is shown by irreversibility of burning that is brightly reflected in figure 4.
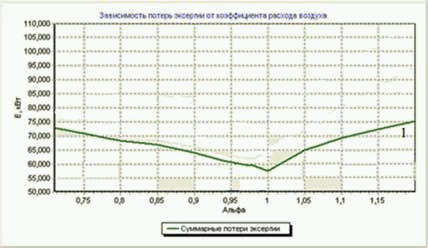
Figure 4 – Dependence of total losses exergy from factor of the charge of air at various temperatures of heating of air (1 - 400 C, 2 - 300 C, 3 - 200 C).
However, exergy is size thermodynamic, instead of economic. Therefore at the analysis of work of technological objects it is necessary to estimate losses, both with thermodynamic, and from the economic point of view. In this connection, it is necessary to make exergical economic function which considers costs of fuel and metal heated up in the furnace, a cost measure of damage from oxidation of metal and loss exergy, and to carry out its minimization. The result of drawing up of the given function will be displayed by the schedule.
Literature
1. Automation methodological furnaces. Buglack L., 1981.
2. Glinckov G.M., Makovskiy V.A., ACSTP in the sintering and steel-smelting shops., 1981.
3. Designing systems of control and automatic regulation of the metallurgical process. Glinkov G.M., Makovskiy V.A., 1986.