In recent years, neural solutions have been suggested for many industrial systems using either feed-forward or recurrent neural networks. Most of the published papers describe control system applications built around a feed-forward neural network included inside
a traditional feedback control system. The ANN is usually made up of sigmoidal activation function neurones and back propagation is normally used to train the network either online or off-line. Some applications use neurones with a radial base activation function. The ANN may play different roles: plant identification [105], [212], non-linear controller [131], [225], and fault signalling [127], [126]. The neural plant identification technique can be applied to induction motor sensorless speed estimation, for example in [38] where the plant parameter to be identified is the rotor speed.
Typical neural networks used for identification purposes are multilayer feed-forward structures containing neurones with sigmoidal activation function. There are two configurations for plant identification: the forward configuration and the inverse configuration [243]. In case of forward configuration, the neural network receives the same input vector x as the plant, and the plant output provides the reference output Oref during the training (Fig. 4.10(a)). During the identification, the norm of the error vector ||Oref – O|| is minimised using the back-propagation algorithm. As illustrated in Fig.4.10(b), the inverse plant identification employs the plant output y as the network input, while the neural network generates an approximation of the input vector of the plant. The norm of the error vector to be minimised through learning is therefore ||x – O||.
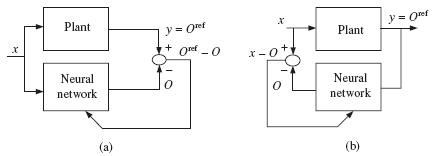
Fig. 4.10 Neural network configuration for plant identification: (a) forward plant identification; (b) inverse plant identification
Feed-forward neural networks generate instantaneous response, thus they can model the steady-state operation of the plant but are not directly capable of modelling its dynamic behaviour. To account for the plant dynamics, the FFANN has to be supplied with a series of past inputs of the plant. Such an approach requires that the neural network is interfaced with a shift register that stores the time series of input vectors (see Fig. 4.11). The shift register is updated at each operation step. An update consists of storing the most recent input vector and discarding the oldest input vector.
An alternative solution is to use recurrent neural networks. This solution is purely neuronal in that it does not require a shift register. However, most of the control systems have used the first solution so far, because the dynamic back-propagation algorithm requires more computation resources than its static counterpart.
Both identification configurations have advantages and disadvantages.
Forward plant identification is always feasible,
but it
does not immediately allow for the construction of the
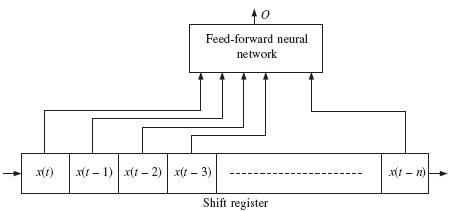
Fig. 4.11 Neural network interfacing for modelling the plant dynamics
plant control. In contrast, plant inverse identification facilitates simple plant control. However, the identification itself is not always feasible because in some cases more than one vector x corresponds to a certain vector y (or series of such vectors).
Figure 4.12 presents a basic control system using a neurocontroller. There are two
alternatives: either the neural network is trained only off-line in an inverse identification
configuration, as presented in Fig. 4.10(b), or it is initially trained off-line but the
training continues on-line in the control system. For training purposes, the back-propagation
algorithm is the most appropriate. Shift registers are used, both during the off-line
identification process and inside the control system, to enable the modelling of the
dynamic plant behaviour. The neurocontroller input consists of the most recent plant
outputs plus the output reference for the current time. Therefore, at each operation
step, it generates a control vector O that causes the plant to produce the expected
output yref.
Fig. 4.12 Basic control system configuration using a feed-forward neurocontroller
The fault signalling applications are part of the larger class of classification
applications. The task of the neural network is to analyse the input data and to generate
information about the operation of the plant: normal operation, or abnormal operation.
In the second case, it may give further details about the abnormality: short circuit,
surpassing voltage or speed limits, etc. The neural network is of the feed-forward type
and is trained off-line using experimental data that reflects all possible operation modes
of the plant.
|