DonNTU >
Master's portal
Faculty: Ecology and chemical Technologies
Speciality: Chemical technology of fuel and carbonaceous materials
Theme of master's work:
Research of technology of recycling of fluidity waste of chemical-recovery manufactures
Scientific adviser: professor Saranchuk V.I.
About author
Introduction
The task of protecting nature from the harmful effects of emissions of industrial production is now becoming increasingly important. In this regard, there is increasing need to create so-called waste production, free of harmful emissions into the atmosphere and water.
Waste productions occur in the process of acquiring major coking products. Their quantity and quality depend primarily on the applied technology and production conditions.
Good waste management is linked primarily with the fullest use of their valuable properties or substances contained therein. Because the wastes contain significant quantities of product coke production, one of the main directions of their use may return them to the production process - by adding to the charge while coking. This waste coke production can serve as a binding material in obtaining the coal briquettes.
The purpose of the work is to determine briquetted ability and mechanical strength of briquettes from coal of different grades of liquid waste coke production.
Research object is briquettes obtained from the individual grades of coal in a mixture of liquid waste coke production.
The urgency of the work. In coking coal stone a significant amount of waste that have so far not been effectively applied. One of the outputs can be used in part briquetted charge that will provide an opportunity to increase the number of low-caking grades of coal in the coking of liquidactive and recycle waste
The practical value. The use of liquid waste coke production as binders will reduce the amount of waste rock in the coking coals, put in an additional charge low-caking coal components through the use of partially briquetted charge and receive an additional amount of products from processing waste.
CHARACTERISTICS OF Coking Plants WASTE
Fuses of coal
Total quantity of fuses in the solid phase (substances not soluble in toluene)is at 40-50% for the anhydrous mass, the rest is a coal tar pitch. Humidity fusov ranges from 5-11%. Anhydrous mass of fuses has 1,29-1,35 g/cm3 density, ash content varies between 4-6% of total sulfur content of 1,6-2,5%.
Acid pitch of sulfate phase
Acid pitch formed in the saturator sulfate phase after sludge mother water until the content of it has subsided 2.7% 1.3% acidity and hardly soluble in water.
Polymers benzene phase
Polymers obtained in the regeneration of absorption of oil in benzene phase are highly flavored product containing small quantities indenekumaron pitches and higher phenols. Their composition depends on the conditions of the regenerator and can be quite different for individual plants.
General information about the process of briquetting
Briquetting of coal is a process of mechanical processing of coal fines in lump fuel - pellets, having a geometric shape, size and weight.
The essence of briquetting is that crushed to a certain size, coal or natural duff, have been dried and then pressing.
Requirements for briquettes:
a) coal briquettes should have the necessary strength and withstand the mechanical loads of various types;
b) The briquettes should have some moisture resistance;
c) coal briquettes should have heat resistant;
g) pellets produced from the binder should not be in the car and sticks together with long-term storage in a pile in the open air.
The experimental part of work
In order to study selected a sample of coal grades "K", "G", "CC", the factory charge to Makeyevka coking plant. Characteristic marks of coal are shown in the table. 2. Samples of waste production such as fusy, acidic sulfate pitch phase, polymers benzene separation, waste of naphthalene settling precipitation tank were also selected.
Table 1 - Characteristics of Coal
The type of coal |
Wr |
Ad |
Sd |
Vd |
Vdaf |
grade |
---|
+6 |
6-3 |
3-0
|
charge |
9,9 |
7,8 |
1,34 |
31,2 |
33,8 |
21,3 |
17,6 |
61,1 |
à |
9,9 |
7,5 |
1,45 |
34,4 |
37,2 |
- |
- |
- |
ÑÑ |
12,1 |
6,4 |
0,44 |
24,3 |
25,9 |
- |
- |
- |
Ê |
8,2 |
7,9 |
0,75 |
27,1 |
29,5 |
- |
- |
- |
Coal fraction 0-3 mm, as a working moisture content, and analysis was used for researching . Number of relations, which was added to the coal is 10-15%. Pre-weighted links (fus, sour pitch), heated in water bath until its tender, then added SUSPENSION coal and thoroughly mixed until a homogeneous mass (so that there is no clots binder). Heating the mixture of coal with the communications is provided to about 50 ° C in the mixture, which was controlled mercury thermometer. Then the mixture was cooled to room temperature.
Briquetting of coal were carried out on a manual mechanical press, extrusion pressure monitored using a dynamometer. Interval corresponded to 300-1000 atm pressure. The sizes of the briquettes are equal, respectively: the diameter of 16.3 mm in length from 24 to 31 mm (depending on the applied pressure and number of loading matrices pressing). The mass of the briquettes varied between 6-8 g. were investigated on briquetted ability as a separate brand of coal, and their mixture, the same applies to the connecting components.
The strength of the briquettes was determined at the same press, by definition efforts, which stand at crushing cake horizontally and vertically. Compressive force of briquettes were determined as fresh or matured some time.
Briquettes from factory conditions for the study were selected. They have a cylindrical shape with a diameter of 30 mm and a length of 150 mm. Also, the samples were selected from the batch of charge which were not briquettes. Briquetting is carried out through the extruder. Schematic diagram of the extruder is shown in Fig. 1
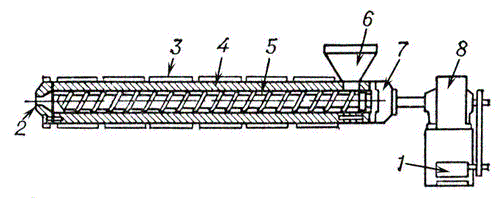
1 - motor drive, 2 - a form of the device, 3 - heating element, 4 - sleeve, 5 - screw, 6 - boot bunker, 7 - thrust bearing; 8 - reducer
Figure 1 - Extruder
Calculate the compression pressure in the extruder to which a coal - is complexity. Therefore, the pressure molding was evaluated approximately from the density of the briquettes. Density of briquette factory was 1.17 g/cm3, which corresponds to approximately 300-400 atm pressure. On the mechanical strength of briquettes were made about the length of 5-7 cm Their strength was 500-700 success units.
Analyzing the charge with a binder which were not succeed as factory briquettes should be noted that there is quite a large number of relatively large (visible) inclusions binder. This suggests a poor mixture of binder with the charge. In laboratory conditions the mixing of charge was improved and then briquettes were formed from this charge. The dependence of the density of the applied pressure is shown in Fig. 4.2
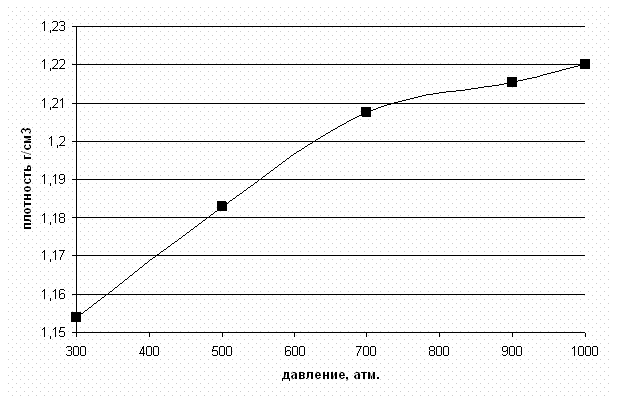
Figure 2 - Changes in the density of the briquettes from the pressure of pressing
At small pressures pressing the density varies linearly in proportion depending on the pressure, at a pressure higher than 700 atm. these changes are slow. The particles of coal converge very close to each other, and raises tensions in the briquettes, which impede the significant increase in density. Further increases in pressure (> 1000 atm) to change the density practically does not result, gradually approaching the density of carbon in the cast - about 1,29 g/cm3.
Samples of briquettes tested immediately after preparation and after aging in a day distinguished by the strength in 5-17%. In the extracts of samples obviously their polymerization takes place, the partial evaporation of moisture and grip sticks, what makes it more durable. For briquettes made of a fresh charge and the binder this hardening is to 45% depending on the binder and make charcoal.
Briquettes, which were obtained by thorough mixing with the permanent heating were the strongest. This hardening was about 30% (Table 4.2). From this we can conclude that the existing technology of briquetting factory in need of adjustment. That is an additional heating of charge and equipment for its mixing with the binder.
Table 2 – The characteristics of briquettes which are made of plant residue charge with binder
Terms of briquetting |
The strength of the briquettes at a pressure |
300 |
500 |
700 |
900 |
1000 |
Cold briquetting batch |
248 |
298 |
337 |
310 |
377 |
Warming the charge up to 40 ° C |
260 |
393 |
445 |
475 |
445 |
Warming up the charge with thorough mixing |
295 |
435 |
470 |
490 |
460 |
In some experiments the observed decrease in the strength of the briquettes at 1000 atm. compared to 900 atm., while the density of the briquettes virtually doesn’t change. This may be due to the fact that in this appendix binding particles of coal approach fairly close to each other and further increase in pressure leads only to an increase in tension within the briquette and the crushing of coal particles.
Analyzing the mixture, which is obtained from the factory, should be noted that quite strong briquettes can got, but it needs a greater homogenization.
These pellets will be used to coking in the coke ovens. This would provide several advantages. There is waste coke production, which at that time sold almost for a song (that is not bad, if no other options are left, because the waste and their disposal should be paid). Their use in the form of sticks, rather than simply mixing with the charge of watering by conveyor belt to remove contamination of conveyor belts, bins, coke ovens. Because the briquetted blinds are not producing all of the elements of pollution. And besides coke comes out in a homogeneous type of thorough mixing and homogeneity from the mixture . Briquetting allows no deterioration in the quality of uncaking coal enter grades, lower quality, given the increasing density of the download. In the result the wastes provide the increase of coke and the use of payback to the cost of their disposal.
Conclusion
Significant quantities of waste coke production require a rational approach to their use. One of the main directions for their use - may be adding their charge. Fus, sour pitch, polymers, as demonstrated by the study are a good binder material and can be used for briquetting of coal. These briquettes have sufficient strength, which allows their delivery into the chamber coking.
The paper examined the characteristics of the waste production and disposal of existing methods, the theoretical basis of the briquetting of coal with binder material, and test methods of the briquettes. The results of the study of samples from the plant charge with blind materials and recommendations for improving the process of briquetting are given in this work. The main reason for receiving bad quality briquette is a lack of homogenization of coal with binder material. Good homogenization cannot be achieved at normal temperature and mixing in the extruder. It requires additional heating of charge and blinder and a mixer as equipment.
©
DonNTU Shvets Mariya 2009
|