RUS | UKR | ENG ||
ДонНТУ >
Портал магистров ДонНТУ
Хрящева Мария Сергеевна
Факультет физико-металлургический
Специальность: Термическая обработка
Тема выпускной работы:
Исследование структуры твердых сплавов на основе карбида титана полученных методом горячего вакуумного пресования
Научный руководитель: Пашинский Владимир Викторович
Материалы по теме выпускной работы:
Об авторе | Библиотека | Ссылки |
Сведения о руководителе | | Индивидуальный раздел
Реферат по теме выпускной работы
Развитие порошковой металлургии началось в результате нехватки новых материалах, невозможность их получения и обработки с помощью традиционных методов. Для твердосплавного производства используются следующие основные виды карбидов: вольфрама, титана, тантала, ниобия, ванадия, циркония, хрома и гафния. Чаще всего применяют карбид вольфрама при его изготовлении в большинстве случаев применяют порошок вольфрама, однако его запасы являются относительно дефицитными и на сегодняшний день некоторые виды изделий, изготавливавшихся на основе карбида вольфрама, можно изготовить с использованием карбида титана.
Рост объемов производства спеченных материалов и обработки металлов резанием требует изыскание и создание новых материалов для армирования пресс-форм и лезвийного инструмента, а также быстроизнашивающихся деталей и механизмов, равноценных или превосходящих по свойствам стандартные твердые сплавы на основе карбида вольфрама, который является относительно дефицитным, поскольку запасы вольфрамового сырья ограничены.
Как основу безвольфрамовых твердых сплавов целесообразно использовать карбид титана. Последний обладает более высокой, чем WC, температурой плавления, твердостью и окалиностойкостью, однако несколько уступает карбиду вольфрама по модулю упругости и теплопроводности.
Полная замена карбида вольфрама в составе твердых сплавов карбидом титана требует разработки и применение таких металлических связок, которые наряду с высокой твердостью и прочностью обладали бы повышенной пластичностью.
Сплавы на основе карбида титана с никелевой и железной связкой являются перспективными для изготовления прокатных валков, в первую очередь благодаря экономичности по сравнения с другими твердыми сплавами и в то же время достаточно высоким комплексом прочностных свойств. К перечисленному выше можно добавить, что в Украине работает завод по производству чистого титана, что дает возможность в последствии получить более дешевое и доступное сырья отечественного производителя. В отличие от вольфрама, который Украинские потребители вынуждены импортировать.
В связи с этим были проведены исследования структуры и свойств твердых сплавов на основе карбида титана с металлической железо-никилиевой связкой.
Исследования проводились на образцах сплавов Т50Н10Ж и Т50Н40Ж, Т35Н19Ж46, которые имеют следующий химический состав:
Т50Н10Ж: TiC=50%; Ni=10%; остальное железо;
Т50Н40Ж: TiC=50%; Ni=40%; остальное железо;
Т35Н19Ж46: TiC=35%; Ni=19%; Fe=46%.
Опытные образцы были изготовлены методом горячего вакуумного прессования. При этом методе используется гидравлический пресс, а формовка и спекание происходят в пресс-форме. Благодаря этому способу обеспечивается высокая точность изготовления заготовки, что снижает потери материала при механической обработке и сокращает ее длительность.
На образцах были приготовлены шлифы с помощью полировки алмазной пастой на деревянной подложке. Также шлифы подверглись последовательному травлению в насыщенном водном растворе FeCl3 и смеси 10% растворов красной кровяной соли и едкого натра. Микроструктурный анализ проведен на микроскопе “Neophot-21”, после чего производилась количественная обработка полученных микроструктур образцов Т50Н40Ж и Т35Н19Ж46 с использованием программ “Image Tool” и “Statistica”.
По полученным микроструктурам было определено, что в обоих сплавах карбиды и связка достаточно равномерно распределены по сечению, не наблюдается скоплений карбида или неравномерного распределения связки.
По полученным результатам с гистограммы (рисунок 1) видно, что размер карбидной фазы в сплаве Т50Н40Ж на 40-50% больше чем у сплава Т35Н19Ж46, при этом размеры участков связки также у сплава Т50Н40Ж больше чем у сплава Т35Н19Ж46. Поэтому можно отметить, что укрупнению зерна способствует большее количество никеля в сплаве Т50Н40Ж.
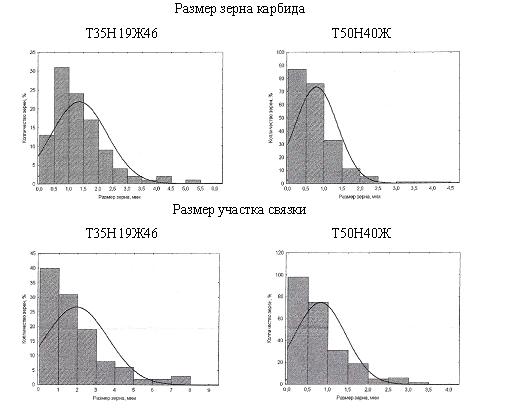
Рисунок 1 – Результаты количественная обработка образцов Т35Н19Ж46 и Т50Н40Ж после травления
На предложенных образцах были смоделированы предполагаемые температурные условия работы валков трайб-аппаратов из этих материалов.
В качестве сравнительного образца использовался сплав на основе карбида вольфрама, титана, тантала и кобальтовой связки, а именно образец резца марки ТТК, который использовался при обработке круглой заготовки. Исследования проводились на образце именно из этой группы сплавов, т. к. эти сплавы являются «универсальными», и инструмент из них применяют как для обработки стали, так и чугуна благодаря их свойствам.
Резец, из которого был взят материал образца, работал в условиях тяжелого чернового точения стальных поковок, при наличии различных неметаллических включений и ударов. В частности производилось точение углеродистых, высокоуглеродистых и легированных сталей. В соответствии с условиями работы резца по ГОСТ 3882-74 «Сплавы твердые спеченные. Марки», был выбран сплав ТТ7К12, который имеет следующий химический состав:
WC=81%; TiC=4%; ТаС=3%; Co=12%.
На образце ТТ7К12 был приготовлен шлиф с помощью полировки алмазной пастой на деревянной подложке. После чего производилось тепловое травление в соответствие с ГОСТ 9391-80 «Сплавы твердые спеченые. Метод определения пористости и микроструктуры». Нагрев производился до температуры 530-540°С и продолжался в течение 15 минут. На полученных шлифах изучалась микроструктура. При спекании карбиды титана и тантала растворяются в части карбида вольфрама, также на микроструктуре можно было обнаружить белые частички свободного карбида вольфрама, серые – растворенный титан и тантал в карбиде вольфрама и черные – связка кобальта.
Микроструктурный анализ проведен на микроскопе “Neophot-21”, после чего производилась количественная обработка полученных микроструктур с использованием программы “Image Tool”.
Количественная обработка показала, что количество сложного карбида, полученного в результате растворения карбидов титана и тантала в карбиде вольфрама составляет около 10,3% занимаемой поверхности.
Т.к. в процессе работы резца марки ТТ7К12 происходит его интенсивный нагрев, в лабораторных условиях было установлено при каких температурах начинается его окисление. Исследования осуществлялись визуально. Нагрев производился в камерной печи до температур 600°С и 700°С. Уже после часа выдержки при температуре 600°С на образце отмечалось потемнение полированной поверхности. При температуре 700°С и выдержке 30 минут на резце было обнаружено появление желто-зеленой пленки в местах полировки, после продолжения выдержки при этой же температуре в течении еще 30 минут, обнаруженная ранее пленка образовалась равномерно по всей рабочей поверхности образца. Это может говорить о том, что началось интенсивное окисление. После 2х часовой выдержки и травления при температуре 530-540°С в течение 15 минут был сделан снимок микроструктуры (рисунок 2а).
Следовательно можно сделать вывод, что одной из причин выхода из строя резцов типа ТТК во время продолжительной работы является интенсивное окисление уже при 700 °С.
Основываясь на полученных данных такому же испытанию подверглись и опытные образцы Т50Н10Ж, Т50Н40Ж, Т35Н19Ж46. Нагрев производился до 600°С, 700°С, 800°С и 900°С. Длительность выдержки составила 2 часа при каждой температуре. После выдержки на 700°С на образцах Т50Н10Ж и Т35Н19Ж46 было обнаружено равномерное потемнение поверхности по всему объему, тогда как на образце Т50Н40Ж лишь неравномерные темные пятна. Видимые результаты были достигнуты лишь при нагреве до 900°С, тогда на всех трех образцах образовалась заметная плотная пленка окислов.
На образцах были приготовлены шлифы с помощью полировки алмазной пастой на деревянной подложке, затем производилось тепловое травление: Т50Н10Ж – при 570-580°С в течение 30 мин. (рисунок 2б), Т50Н40Ж - при 750-760°С в течение 30 мин. (рисунок 2в), Т35Н19Ж46 - при 570-580°С в течение 15 мин. (рисунок 2г).
Рисунок 2 – Микроструктуры образцов при увеличение 1000
По полученным данным можно сделать следующий вывод:
1. Проведенная сравнительная оценка образца сплава ТТК и опытных образцов Т50Н10Ж, Т50Н40Ж, Т35Н19Ж46 показала явное преимущество последних; при длительной работе уже при 700°С резец начинает интенсивно окисляться.
2. По полученным микроструктурам видно, что наиболее интенсивному окислению подвергается сплав Т35Н19Ж46 в сравнении с Т50Н10Ж и Т50Н40Ж, это говорит о том, что первой начинает окисляться железная связка и исследование этого сплава при длительной работе при 900°С не является перспективным.
3. Т50Н10Ж в сравнении с Т35Н19Ж46 имеет практически одинаковое количество железа, однако не так интенсивно подвергается газовой коррозии. Это происходит, т. к. в структуре находится больше карбидов титана, которые в свою очередь являются «барьерами» для окисления.
4. Из представленных материалов следует, что наибольшим сопротивлением к окислению обладает сплав Т50Н40Ж, так как в его составе мало железной связки и много никеля.
Также немало важный интерес представляет колличественная обработка полученных результатов, т.е на сколько процентов по массе уменьшился бы валок из твердого сплава на основе карбида титана при определенных температурах и длительности работы.
|