УДК 622-25
Ваксер Д.Б.
ВЛИЯНИЕ РЕЖИМОВШЛИФОВАНИЯ НА КАЧЕСТВО ПОВЕРХНОСТНОГО СЛОЯ
Как уже упоминалось, под качеством поверхностного слоя при шлифовании понимается не геометрическое состояние поверхности, а те изменения в физико-механических свойствах исходного металла, которые вносятся шлифованием.
В связи с этим качество поверхностного слоя можно оценивать по следующим методикам.
1. Внешний вид шлифованной поверхности наблюдается визуально или по фотографиям. Этим способом наблюдаются видимые поверхностные прижоги, крупные трещины и т. п.
2. Методом цветной дефектоскопии с помощью микроскопа или по микрофотографиям обнаруживаются микротрещины.
3. Микроструктурный анализ.
4. Измерение микротвердости по глубине.
5. Измерение остаточных напряжений и другие методы.
Оценивая тем или иным способом состояние поверхностного слоя после шлифования и сопоставляя его с режимами шлифования, можно сделать заключение о влиянии температурных полей на качество металла.
Расчеты температур позволяют заключить, что при шлифовании закаленных сталей и других твердых материалов температура, как правило, превышает критические точки, и в металле возможны структурные изменения. Глубина и характер этих изменений полностью определяются температурным полем. При наиболее производительных режимах поверхность может нагреваться до температуры плавления металла, а скорости охлаждения могут достигать значений порядка. 10 град/с. Таким образом, металл подвергается своеобразной термической обработке, особенности которой состоят в чрезвычайно высоких скоростях изменения температуры и малой выдержке при высокой температуре. Это своеобразие накладывает свой отпечаток на природу структурных изменений.
Общепринятая точка зрения на природу структурных превращений при шлифовании основана на диаграмме состоянии железо — углерод и сводится к следующим положениям. Если температура металла достаточно высока, но не превышает критической точки А01, то в данном слое мартенсинт может распадаться с образованием троостита и тростомартенсита. Появляются прижоги отпуска, наблюдаемые как темные, хорошо травящиеся участки с пониженной микротвердостью. Если в данном слое температура превышает точку Ас, а скорость охлаждения выше критической, необходимой для закалки скорости, образуется вторичный закаленный слой с образованием, структуры аустенитомартенсита. Появляются прижоги вторичной закалки. Вторично закаленный слой лежит на отпущенном слое металла, переходящем через все стадии отпуска в структуру исходного металла.
По характеру и глубине фазовоструктурных изменений иногда судят о распределении температур по объему изделия после шлифования. При этом обычно ориентируются на известную диаграмму состояния железо — углерод, которая безусловно справедлива лишь для сравнительно медленного нагрева. При скоростях нагрева, характерных для шлифования, происходит образование метастабильных структур, положение критических точек у которых может существенно смещаться по сравнению с известной диаграммой равновесия. Например, увеличение скорости нагрева заявленных сталей приводит к понижению положения критической точки Ас1,. При достижении некоторого предела ее положение стабилизируется. Очевидно, при оценке температур шлифования по характеру и интенсивности фазово-структурных превращений необходимо ориентироваться на эти метастабильные диаграммы, которые не всегда известны. При решении обратной задачи, т. е. при определении структурных превращений по известному температурному полю, нужно также ориентироваться на эти диаграммы.
Фазово-структурные превращения обнаруживаются обычно в результате травления по фотографиям микроструктур. Косвенно судить о наличии этих изменений можно также по изменению микротвердости. Связь между температурами и фазовоструктурными изменениями через изменение микротвердости проявляется вполне отчетливо и может служить основой для формулировки некоторых основных рекомендаций. Ниже приводятся примеры расчета температурных полей для некоторых режимов и их связь с изменениями микротвердости. Для управления качеством необходимо знать влияние различных факторов на температуру и состояние поверхностного слоя. Рассмотрим влияние этих факторов в отдельности.
Скорость круга. Скорость резания, в данном случае скорость. круга, выступает как чисто количественный фактор, определяющий масштаб температурного поля. Изменение скорости круга изменяет мощность тепловыделения в зоне шлифования, что приводит к изменению температур во всех точках шлифуемого изделия в одинаковое число раз. При сохранении всех факторов. режима скорость круга влияет на мощность источника тепла в соответствии с формулой
Это соотношение получается в результате того, что увеличение скорости круга приводит к некоторому уменьшению сил резания Рz в соответствии с формулой
Поскольку мощность тепловыделения, а вместе с ней и температура, растут со скоростью не очень быстро увеличение скорости крута должно быть рекомендовано почти во всех случаях для металлов, не очень чувствительных к большим неоднородностям температур. Высокие скорости резания позволяют производить шлифование с большими продольными подачами. В этом случае, несмотря на высокие температуры поверхности, глубина проникновения высоких температур будет невелика, дефектный слой будет мал и может быть устранен на суперфинише.
Скорость продольной подачи. Температура поверхности и распределение температур по глубине сложным образом зависят от скорости продольной подач (скорости изделия). При фиксированной плотности теплового потока с увеличением скорости происходит уменьшение максимальной температуры. В этом случае зависимость температуры от скорости определяется функцией вида
для скоростей, характерных при шлифовании. Кроме этой зависимости па поведение температуры при изменении скорости определенное влияние будет оказывать изменение мощности с изменением скорости. Например, при плоском шлифовании в диапазоне скоростей продольных подач от З до 12 м/мин зависимость плотности теплового потока от скорости можно считать линейной. В этом случае, если пренебречь влиянием других, менее существенных причин, зависимость температуры поверхности от скорости подачи имеет вид
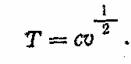
При других схемах шлифования (или в другом диапазоне скоростей) возможна иная зависимость плотности теплового потока от скорости подачи. Тогда и зависимость температуры от скорости может быть иной. В частности, если Рz или q зависят от скорости подачи.
Тенденция к увеличению скорости продольной подачи наблюдается почти у всех исследователей. Часто эта мера рекомендуется, как средство, позволяющее уменьшить вероятность появления шлифовочных прижогов и трещин; чем меньше скорость детали, тем выше опасность прижогов и больше глубины измененного слоя, и наоборот, для снижения опасности возникновения трещин при шлифовании деталей из жаропрочных сплавов рекомендуется повышать скорости детали до 70 м/мин. В основе этих рекомендаций обычно лежит простое соображение, заключающееся в том, что чем больше скорость детали, тем меньше время контакта круга с деталью и меньше время воздействия на шлифуемую поверхность высоких температур. Изложенные в настоящей книге результаты исследования позволяют заключить, что теплофизическая ситуация в зоне контакта абразивного крута с деталью много сложнее, и рекомендовать в качестве радиальной меры борьбы со шлифовочными прижогами и особенно трещинами увеличение скорости продольной подачи не всегда целесообразно. Основной причиной, приводящей к возникновению шлифовочных трещин, являются термические напряжения, превышающие предел прочности металла. Эти напряжения возникают наиболее вероятно в том случае, когда температурное поле характеризуется большими градиентами и большими скоростями нагрева и охлаждения. Эти особенности как раз и имеют место при больших скоростях детали, Для выбора оптимального режима шлифования, который мог бы обеспечить необходимое качество, следует учитывать весь комплекс технологических характеристик процесса с учетом их взаимных связей.
ЛИТЕРАТУРА
1. Яшерицын П.И., Зайцев А.Г. Повышение качества шлифованных поверхностей и режущих свойств алмазно-абразивных инструмента. Минск, Наука и техника, 1972, с.478.
2. Ваксер Д.Б., Иванов В.А. Алмазная обработка технической керамики. Л., Машиностроение, 1976,160 с.
3. Балкевич В.Л. Техническая керамика. М., Стройиздат, 1968. 230 с.
НАЗАД
|