Семенюк Дмитрий Юрьевич
    Факультет: «Механический»
    Специальность: «Металлорежущие станки и системы»
    Руководитель:
Гусев Владимир Владиленович д.т.н., проф.
Автореферат по теме магистерской работы:
«Обоснование технологии и разработка технологического оборудования
для обработки сферических поверхностей деталей из керамики»
Содержание:
Актуальность
Цели и задачи магистерской работы
Обзор существующих исследований в данном направлении
Разработка конструкции станка для обработки сферических поверхностей деталей машин
Физическое моделирование и исследование температурного состояния детали и инструмента в процессе
алмазного шлифования шарового клапана
Выводы и перспективы дальнейших исследований
Список использованной литературы
Актуальность
Вопрос обработки деталей машин,
содержащих фасонные (в том числе сферические) поверхности всегда ассоциировался
со специальным инструментом и оборудованием, совершающим сложные движения
формообразования. Детали, имеющие сферические поверхности применяются не только
в машиностроении, но и в медицине, сельском хозяйстве и других отраслях
промышленности (химическая, горно-геологическая, судостроение, приборостроение
и т.д.). Поэтому на сегодняшний день актуален вопрос разработки эффективного
высокопроизводительного станочного оборудования, позволяющего производить
качественную механическую обработку таких деталей. Существует множество
способов получения сферических поверхностей механической обработкой (точение,
шлифование, фрезерование и т.д.), однако особое внимание к себе привлекают
именно способы шлифования, как наиболее производительные процессы финишной
обработки, позволяющие обеспечить не только высокую геометрическую точность, но
и высокое качество поверхностного слоя
обработанной детали.
В настоящее время в мире наблюдается тенденция
производства изделий из неметаллических и композиционных материалов, которые
все шире заменяют металлы во многих отраслях промышленности. Эта тенденция
связана со снижением себестоимости продукции при одновременном повышении их
срока службы, надежности и экологической чистоты. Особое место среди
неметаллических материалов занимает керамика. Физико-механические свойства керамики
по сравнению со всеми видами металлов, которые в настоящее время применяются в
качестве главных материалов для изготовления деталей машин, имеют такие
отличительные черты, как высокая температура плавления, твердость, легкость,
износостойкость, коррозийная стойкость, стойкость против химикатов и т.д. При
этом физико-механические свойства керамики стабильны в большом интервале
температур, что не маловажно при использовании ее в узлах трения и образования
высоких температур. С другой стороны возникает много сложностей с механической
обработкой керамических материалов, т.к. они по сути являются абразивами.
Цели и задачи магистерской работы
В условиях развития
рыночной экономики в Украине важнейшим фактором успешной деятельности
предприятия является снижение себестоимости выпускаемой продукции (за счет
увеличения серийности производства) при обеспечении высоких эксплуатационных
характеристик изделий (за счет применения прогрессивных методов и схем
обработки).
В конструкциях изделий для
электромашиностроения, приборостроения, ядерной энергетики, ракетостроения,
самолетостроения, космической техники и общего машиностроения часто
присутствуют сложные сферические поверхности, которые необходимо обработать с
высокой точностью. Наблюдается тенденция производства изделий из
неметаллических и композиционных материалов, которые все шире заменяют металлы
во многих отраслях промышленности. Одним из материалов, который удовлетворяет
перечисленным требованиям, является керамика. При ее применении снижается
себестоимость изделий при одновременном повышении их срока службы и надежности.
Работы по керамическим материалам во всем мире непрерывно интенсифицируются,
возрастают капиталовложения в их разработку, расширяются области применения
этих материалов. Каждые пять лет производство керамических изделий удваивается.
В данной работе будет рассмотрен вопрос
проектирования специализированного станочного оборудования для шлифования и
хонингования сферической поверхности
детали типа шаровой клапан промышленного крана из конструкционной керамики, а
также притирки пары шар-седло (рис. 1.1)
Рисунок 1.1 – Конструкция шарового крана: 1-шаровый
клапан; 2-полимерные кольца; 3,4-корпус; 5-уплотнения; 6-резиновое кольцо;
7-медное кольцо; 8-винт; 9-винт М4;
10-гайка; 11-ручка.
Обзор существующих исследований в данном направлении
Потребность в точной обработке сферических поверхностей огромного
количества разнообразных деталей с древних времен и до сих пор заставляет
инженеров разрабатывать новые схемы шлифования и совершенствовать старые. В
следствии этого, до нашего времени накопилось много разных способов точной
обработки сферических деталей, однако все они схожи в том, что основаны либо на
использовании фасонного инструмента (что приводит к увеличению затрат на
инструмент), либо требуют «связки» нескольких сложных движений формообразования
(что приводит к усложнению и удорожанию оборудования). Наиболее
производительными методами на сегодняшний день являются методы, представлены на
рисунке 2.1
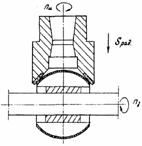
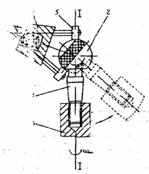
Рисунок
2.1 – Схемы шлифования сферических поверхностей
Проанализировав выше приведенные схемы, можно сделать вывод, что для
наших условий наиболее подходит схема шлифования внутренней конической
поверхностью шлифовального круга (рисунок 2.1,в), т.к. эта схема обеспечивает
высокую производительность и имеет огромный потенциал в области
автоматизированного производства. Образующая конической поверхности
алмазоносного слоя совпадает с касательной к образующей сферы на ее границе с
торцовыми плоскостями, ограничивающими сферу.
Такой процесс шлифования коническим шлифовальным кругом можно отнести к
тем немногим случаям, когда главным движением являются оба вращательных
движения, которые в совокупности определяют необходимую для осуществления
шлифования результирующую скорость резания. Конкретно вопрос должен решаться
целесообразностью того или иного конструктивного решения.
Данный процесс должен обеспечить съем припуска, достаточный для
достижения требуемой точности размера, формы, а так же компенсации погрешностей
базирования. Уменьшая зернистость круга, приближаем процесс шлифования к
чистовому и отделочному. Но тогда целесообразность его осуществления на жестких
осях приспособления и инструмента становится сомнительной. Наоборот, необходимо
освободить один из элементов – шлифовальную головку предоставить ей возможность
самоустанавливаться по обрабатываемой поверхности, что обеспечит процесс
хонингования и доводки или притирки.
Разработка конструкции станка для обработки сферических поверхностей деталей машин
3.1
Выбор схемы обработки
Проведя
анализ существующих схем обработки, мы остановились на схеме, показанной на
рисунке 3.1, т.е. на шлифовании сферы чашечными кругами, но мы будем вести
обработку сразу двумя инструментами.
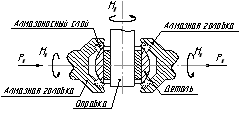
Рисунок 3.1 – Схема шлифования коническим кругом
Данный процесс должен обеспечить съем припуска, достаточный для
достижения требуемой точности размера, формы, а так же компенсации погрешностей
базирования. Данная схема обработки позволяет использовать в качестве
инструмента конические алмазные круги с разной зернистостью, что необходимо при
обработке керамических шаров, поэтому именно такая схема обработки будет
положена в основу специализированного оборудования для производства шаровых
клапанов промышленных кранов.
Еще одним преимуществом является возможность установить вместо
инструмента кольцо-седло крана, а вместо детали – чугунный притир и произвести
обработку кольца, после чего притереть непосредственно шар и седло, применив
мелкодисперсный свободный абразив в виде пасты.
3.2
Расчет режимов резания и сил в зоне резания
Расчет необходимых режимов резания при шлифовании будем проводить исходя
из условий обеспечения необходимого качества поверхности и точности формы
детали. При расчете частоты вращения детали и инструмента будем
использовать расчетную схему (рисунок
3.2)
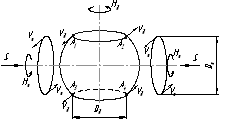
Рисунок 3.2 – Схема шлифования сферической поверхности
Из данной схемы видим, что направления векторов линейных скоростей на
разных точках детали и инструмента отличаются. При этом линейные скорости в
точках А1 и А4 имею одно направление,
поэтому результирующая скорость резания будет определяться разницей окружных
скоростей, и наоборот.
Для обеспечения необходимого качества обработанной поверхности и
стойкости инструмента, максимальная скорость резания не должна превышать
допустимую для данного обрабатываемого и инструментального материала. В нашем
случае обрабатывается конструкционная керамика на основе оксида алюминия (Al2O3)
алмазным абразивным и инструментом, для которого максимальная скорость резания
составляет 15 – 20 м/с [1]. При этом опыт использования данной схемы обработки
показывает, что наилучшее качество поверхности на одной и той же скорости
резания достигается при соотношении частот вращения детали и инструмента
≈ 1/2.
Шлифование будет проводится по упругой схеме, а нормальное давление на
обрабатываемой поверхности будет составлять PN ≈ 0,05 –
0,1МПа, что обеспечит требуемое качество обработанной поверхности. Для
определения составляющих силы резания воспользуемся расчетной схемой (рисунок
3.3).
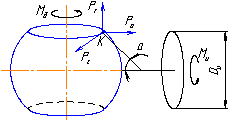
Рисунок 3.3 – Схема разложения сил резания при обработке
Найдем площадь контакта инструмента и детали по которой распространяется
давление с учетом следующих допущений: а) контакт детали и инструмента
непрерывен по всей площади контакта; б) давление на деталь со стороны
инструмента распределяется равномерно по всей площадке контакта.
Проведенные расчеты показали, что эффективная мощность шлифования будет:

3.3 Выбор компоновки
станочной системы
Как видно
из рисунка 3.2 для обработки детали необходимо обеспечить три формообразующих
движения – два вращательных главных движения
и одно поступательное движение подачи. Эти движения (Вz, Ву и Пу)
можно реализовать применив компоновку станка как на рисунке 3.4. Для повышения
производительности и компенсации силовых факторов, мы будем обрабатывать деталь
одновременно с двух сторон двумя инструментами.
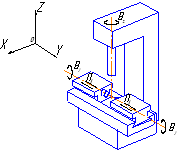
Рисунок 3.4 – Компоновочная схема станочной системы для обработки сферических деталей
3.3 Разработка кинематической схемы
станочной системы
Для
обработки сферических поверхностей деталей на проектируемом оборудовании
необходимо обеспечить три формообразующих движения, следовательно, необходимо
разработать кинематические схемы трех приводов:
а)
Привод вращения детали (рисунок 3.5);
б)
Привод вращения инструмента(рисунок 3.6);
в)
Привод подачи инструмента(рисунок 3.7).
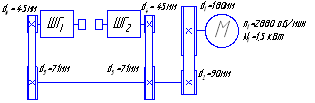
Рисунок 3.5 – Кинематическая схема привода
вращения инструмента
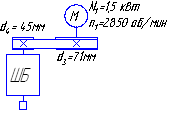
Рисунок 3.6 –
Кинематическая схема привода вращения детали
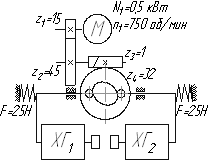
Рисунок
3.7 – Кинематическая схема привода подач инструмента
Общая
мощность станочной системы составила 3,5 кВт.
3.4 Конструкция,
описание и принцип работы станочной системы
Разработанная
станочная система (рис. 3.8) предназначена для шлифования, хонингования или притирки сферических поверхностей. Все
эти процессы могут быть реализованы на одном и том же станке после смены
исполнительного рабочего органа (подвижной инструментальной головки) и
перенастройки на размер. Это не создаст неудобств при эксплуатации станков в
автоматических линиях, но одновременно унификация всех узлов значительно
стоимость производства и ремонта данных станков.
Станок
предназначен для обработки неполных сферических поверхностей диаметром (25…55)
мм деталей из металлов, керамики и других материалов. При определенной
модернизации и настройке механической части и системы управления он может
встраиваться в автоматические линии обработки деталей, содержащих сферические
поверхности.
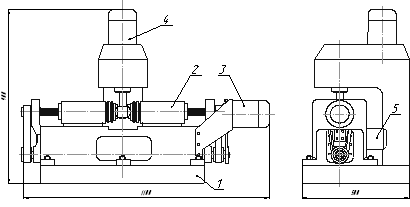
Рисунок
3.8 – Общий вид станка для обработки сферических поверхностей
Основными
узлами системы являются механизмы осуществления вращения и подачи инструмента.
Сборочный чертеж этих механизмов приведен на рисунке 3.9.
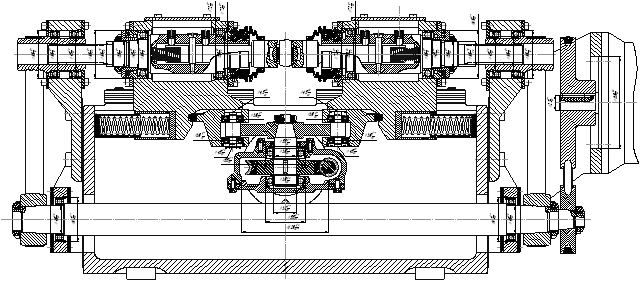
Рисунок 3.9 – Сборка хонинговального модуля
При проектировании был проведен силовой расчет
наиболее ответственных узлов системы, таких как клиноременная передача,
плоскоременная передача, направляющие качения, червячный редуктор, а также
выполнен динамический расчет привода вращения инструмента. Использовалась
литература [2, 3, 4]. Расчеты подтвердили работоспособность основных узлов
входящих в состав станочной системы.
Физическое моделирование и исследование
температурного состояния детали и инструмента в процессе алмазного шлифования шарового клапана
Одним из важнейших параметров функционирования системы резания является
температура, определяющая как работоспособность режущего инструмента, так и
качество поверхностей обрабатываемых деталей. Наряду с экспериментальными
исследованиями, в настоящее время всё большее распространение получают
теоретические методы исследования, позволяющие рассчитать уровень температур на
поверхности и внутри контактирующих тел.
В работе решается задача определения температурного состояния
поверхностного и внутреннего слоя шарового клапана при шлифовании его наружной
сферической поверхности инструментом, оснащенным синтетическим алмазом с целью
разработки рекомендации по назначению
рациональных режимов резания, обеспечивающих требуемое качество обработанной
поверхности.
На начальном
этапе решения задачи была разработана геометрическая 3D модель детали и инструмента (рис.
4.1), а также заданы свойства материала детали (конструкционная оксидная
керамики Al2O3) и оправки
(сталь 45).
После построения геометрической модели детали, была проведена ее разбивка
на сетку конечных элементов (рис.4.2).
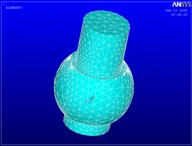
Рисунок 4.2 – Полученная сетка конечных элементов
После этого мы задаем тепловой поток на площадке контакта инструмента и
детали разбитой на 20 отдельных площадок. Тепловой поток предварительно
рассчитан в зависимости от скорости резания и давления на этих площадках
контакта.
После изменения скоростей резания (изменяя частоту вращения шлифовального
круга) и расчета температуры, был построен график зависимости температуры от
скорости резания (рис. 4.3)
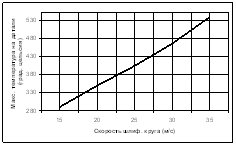
Рисунок
4.3 – График зависимости максимальной температуры на поверхности детали от
скорости вращения шлифовального круга.
Для обеспечения требуемого качества поверхностного слоя детали (по
параметру трещиноватости) необходимо, чтобы температура при обработке не
превышала критически допустимую (300 - 350 °С). На графике видим, что данная
температура образовывается на скорости круга ≈ 25 м/с, поэтому для
обеспечения нормальных условий обработки назначим скорость круга 20 м/с.
Исследуем влияние силы прижима шлифовального круга к детали на
температуру на поверхности детали. По полученным данным построим график
зависимости tmax = f(Ру),
представленный на рисунке 4.4.
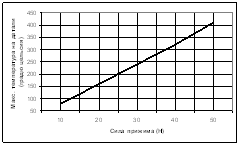
Рисунок
4.4 – График зависимости максимальной температуры на поверхности детали от силы
прижима шлифовального круга.
На построенном графике видим, что для обеспечения качества поверхностного
слоя необходимо, чтобы усилие прижима не превышало 45 Н.
Мы видим, что температура растет с увеличением скорости круга и усилия
прижима инструмента к детали. Есть несколько вариантов возможных режимов,
однако с точки зрения уменьшения шероховатости поверхности нам нужно
увеличивать скорость круга и уменьшать силу прижима инструмента. Поэтому
назначим скорость круга 18 Vкр м/с, а усилие прижима 20 Н и проведем
контрольный опыт. Результаты приведены на рисунке 4.5.
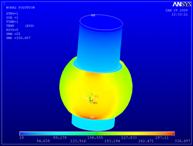
Рисунок 4.5 – Тепловое состояние шарового клапана при обработке на
следующих режимах: Py = 20 Н,
Vкр = 18 м/с, Vд = 7 м/с.
Как показал проведенный опыт (рис.
4.5), обработка детали на принятых режимах обеспечат требуемое качество
поверхностного слоя детали т.к. максимальная температура на поверхности детали
(336 °С) не превышает допустимой (350 °С).
Выводы и перспективы дальнейших исследований
В результате проведенной работы был спроектирован специализированный
станок для обработки сферических поверхностей деталей машин. В качестве примера
детали, был взят шаровой клапан промышленного крана. В работе был проведен
анализ существующих методов и схем обработки неполных сферических поверхностей
и выбран наиболее производительный (шлифование внутренней поверхностью
конического шлифовального круга). Для выбранной схемы обработки были рассчитаны
скорости резания на различных участках площадки контакта. Для обеспечения
необходимых движений формообразования была разработана компоновочная схема
станка. На следующем этапе были разработаны кинематические схемы приводов
вращения детали и инструмента, а также привода подачи шлифовального круга, для
которых были рассчитаны мощности электродвигателей. В конструкторской части
работы были разработаны конструкции привода вращения детали и подачи
инструмента, для которых были выполнены необходимые силовые расчеты
ответственных узлов и деталей.
Для назначения режимов резания, обеспечивающих
отсутствие образования дефектов обработки под воздействием температурного
фактора, был проведен температурный анализ состояния детали при ее
обработке. Для этой цели был использован
программный пакет ANSYS. Проведенные расчеты показали, что максимальная
температура в зоне контакта не превышает допустимых значений.
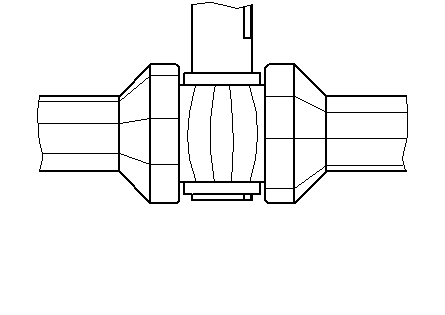
Рисунок 5. - Анимированное изображение процесса обработки сферической поверхности на спроектированном станке (89 кБ, 21 кадр, 10 циклов повторения)
Список использованной литературы
     1. Абразивная и алмазная обработка материалов. Справоч¬ник. Под ред. д-ра техн. наук проф. А. Н. Резникова. M. «Маши построение», 1977 – 391с.
     2. Кочергин А. И. Конструирование и расчет металлорежущих станков и станочных комплексов. Курсовое проектирование: Уч. пособие для вузов. – Минск: Высш. шк., 1991 – 382с.
     3. Детали и механизмы металлорежущих станков: в 2-х т., Т.1. под ред. Д.Н. Решетова. М.: Машиностроение, 1972 – 664с.
     4. Расчет динамических характеристик металлорежущих станков : учебное пособие / В.А. Ванин, А.Н. Колодин, Ю.В. Кулешов, Л.Х. Никитина. – Тамбов : Изд-во Тамб. гос. техн. ун-та, 2007. – 104 с.
     5. Гусев В.В. Назначение режимов резания при алмазном шлифовании конструкционной керамики/Наукові праці ДонНТУ. Серія: Машинобудування і машинознавство. Випуск 110. Донецк: ДонНТУ, 2006. С. – 6 - 16.
     6. Братан С.М., Каинов Д.А. Сазонов С.Е. Оценка параметров качества поверхности при доводке свободным абразивом/ Наукові праці ДонНТУ. Серія: Машинобудування і машинознавство. Випуск 124. Донецк: ДонНТУ, 2007. С. – 9 - 15.
     7. Дитиненко С.А., Снисаренко И.Н., Машко А.А., Черненко А.В. Условия уменьшения шероховатости обработки при шлифовании / Наукові праці ДонНТУ. Серія: Машинобудування і машинознавство. Випуск 139. Донецк: ДонНТУ, 2008. С. – 16 - 23.
ДонНТУ |
Портал магистров ДонНТУ |
Реферат |
Библиотека |
Ссылки |
Отчет о поиске |
Индивидуальное задание
|