Possibility of using lean production for ukrainian enterprises
Introduction
The interest to quality management has seriously increased in Ukraine in recent years.
The managers has created many new concepts and methods of management recently. This is a business process reengineering (BPR), Total Quality Management (TQM), Statistical Process control (SPC), coaching, a model of international standards ISO 9000, ISO 14000, HACCP, “Five S”, “Six Sigma” and others. Unfortunately, the post-Soviet countries do not have their own development in this industry. There is no traditions, schools, the experience of predecessors, there is no established management systems. Therefore, the Ukrainian managers need to learn a lot from foreign techniques in order to remain competitive.
The concept is one of the most advanced proposals for management.
Specialists of quality management believe that the concept of Lean production is an important factor for the improvement of the production system for Ukrainian enterprises.
The aim of this work is the revealing of the essence of the concept of lean production; analysis of the possible application of lean production in Ukraine.
The history of the system
“Lean production” is a Japanese technology management. This is the philosophy of the buisiness organization, which includes many aspects of the company, including strategic development and marketing management.
Taiichi Ohno (1912 - 1990) is considered to be the founder of lean production. He joined the Toyota Motor Corporation in 1943. In mid-1950's, he introduced a system for TPS (Toyota Production System). This system became known as Lean production, Lean manufacturing, Lean.
The concept of “lean production” is the elimination of all types of losses and maximization of resource efficiency. The peculiarity of the concept of “lean production” is constant improvement of all business processes of the organization to improve customer satisfaction.
The essence of the concept of lean production
The main idea of this concept is as follows: action, operation or process that does not add to the value of the product are treated as losses. All losses are divided into two categories.
Loss of the first order is something that can not be eliminated. For example, calculation of wage employees. This process does not add to the value of the product. But without it, it is impossible to maintain efficiency of the company. It can not be removed, it can be only improved.
Loss of the second order can be eliminated. They are classified as follows in the company “Toyota”:
1. Overproduction. The result of overproduction is:
- Premature consumption of raw materials;
- Not optimal use of manpower;
- The need to purchase additional equipment;
- An increase of space;
- Percent increase in payments (property tax);
- Excessive increase in stocks;
- Increase in transportation and administrative costs.
2. Excess reserves. Raw materials, finished and unfinished products, which are stored in a warehouse, do not add the value of the product from the standpoint of the client. Company “Toyota” solved this problem by using a system of relations with suppliers Just-in-Time. Finished products are also sent to customers directly from the shop.
Most Ukrainian companies consider stock to be protection against uncertainties. Therefore, companies will not eliminate stocks. The question is, what the optimal number of stocks should be in the company and in what form. The task of management is to achieve a balance between units.
3. Defects. The losses, which require the material and human resources. The philosophy of Lean said that the need to build such a system in which any deviation from the norm will be noticeable.
4. The unnecessary operations and movements in the workplace. If an employee is looking for a long document or instrument, it also does not add to the value of the product from the perspective of the client. To avoid this type of loss, you need a place to organize workplaces.
5. Excessive handling. The attempt to set more stringent tolerances increases the possibility of a defects and often requires the use of more expensive tools and a more highly skilled workers.
6. Downtime. Waiting time after arrival of the previous phase of the production process. They often arise in the performance imbalance between the production sites and shops. Delays also occur because of breakdowns of equipment. To reduce the negative consequences of such situations, it is necessary to create reserves of unfinished products.
7. The unnecessary displacement. Transportation and movement is an important part of the production process. But from the perspective of the customer, internal displacement, and transport do not add the value of the product. At some plants the length of the flow may be several kilometers. Reducing the length of the flow can lead to significant results in reducing overall production time, reduce losses from damage due to transportation, reduce stockpiles and production facilities. All this greatly affects the overall financial results of the company.
8. Loss of staff creativity. This is a serious type of loss, which affects the overall position of the company. If a person is indifferent to the work, he will not feel accountable for results and the quality of his work.
Technology of introducing the Lean production
The technology of lean production involves five sequential steps, which at first glance seem quite simple. They are:
- determination of the value that the client wants;
-creation process of obtaining this value;
-organization of the continuous movement of the process;
-introduction of the principle of stretching (rather than pushing);
-continuous improvement of all elements of the system.
The steps of introducing the lean production are presented at figure 1.
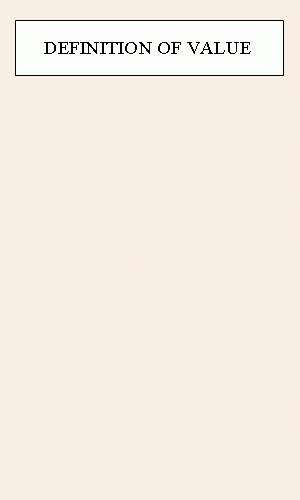
Figure 1 – The steps of introducing the lean production (animation: volume – 53 kB;
size – 500x300 pixels; amount of shots – 9; delay between shots – 100 ms;
delay between the last and first shot – 200 ms; amount of cycles of reiteration – 7)
Lean production in Ukraine
The concept of lean production has already been widely disseminated in Russia.
In Ukraine, the principles of Lean has had little popularity. But it should be noted that today some of the Ukrainian companies have already begun to introduce elements of lean production. Today Machine-Building Plant “Chervona zirka” (Kirovohrad), soft drinks plant “Panda” (Vinnytsa) are in implementing lean production. Just the first stages of Lean technology show high positive results.
Conclusions
Concept of Lean production allows the company to get a lot of advantages. This release of resources, improvment production flow, the interest of staff, trouble-free operation of equipment, etc. Therefore, the introduction of Lean in Ukrainian enterprises is very important to their operation and maintenance of competitiveness.
We can say that in our country a real opportunity to apply the concept of lean production has emerged. Some companies are already implementing Lean production. However, the spread of the concept of Lean is limited to financial problems of firms and incomplete knowledge of the importance of the system. Some managers try to implement only certain elements of the system. But it is not possible to get significant results. Some of them monitor the implementation of Lean not too responsibly and carefully, and because of this they suffer financial losses.
We can conclude that the management company should be very serious about innovation, set goals for continuous improvement, interest in the experience of such domestic and foreign enterprises. Only in this case using the principles of lean production will give significant results.
List of literature:
1. Вумек Дж. П., Джонс Д. Т. Бережливое производство. Как избавиться от потерь и добиться процветания вашей компании. – М.: Альпина Бизнес Букс, 2004. – 473 с.
2. Wikipedia: http://ru.wikipedia.org/wiki/Бережливое_производство
3. Морской В. Lean Thinking: решение проблем в производственной логистике: http://www.iteam.ru/publications/logistics/section_74/article_2483/
4. Адлер Ю. Бережливого Бог бережет. По материалам конференции «Созвездие качества'2004». Сборник тезисов докладов. – К.: Украинская ассоциация качества, Межотраслевой центр качества «Прирост», 2004. – 204 с.
5. Шехватов Д., Воронин А. Бережливое производство как элемент стратегий Кайдзен: http://www.cfin.ru/management/manufact/lean_as_kaizen.shtml
6. Куприянова Т.М., Растимешин В.Е. Как выращивается Бережливое производство: http://www.tpm-centre.ru/page.php?pageId=98&menuItemTreeCode=0810
7. Бушуев А. Стратегия, Маркетинг и Бережливое Производство: http://www.leancor.ru/article2/10011
8. Булгакова М.В. Особенности национального внедрения Lean // Методы менеджмента качества. – 2006, №10. – С. 4-9.
9. Гагарский В. Бережливое производство – ответ на вызовы кризиса: http://www.orgprom.ru/go/obj0069098568/obj0021380748/obj0011864948
10. Фомичев С.К., Скрябина Н.И., Уразлина О.Ю. «Бережливое управление»: управление потоком создания ценности // Методы менеджмента качества. – 2004, №7. – С. 5-11.
11. Цыганов И.Ю. Экономное производство – первоочередная необходимость // Методы менеджмента качества. – 2004, №4. – С. 3-6.
|