A PERMANENT MAGNET GENERATOR FOR SMALL SCALE WIND TURBINES
J. R. Bumby, N. Stannard and R. Martin
Abstract—This paper describes the development of a permanent magnet generator for small scale wind turbines. The generator has been designed for ease of manufacture so that it can be made by small mechanical engineering companies with limited electrical engineering knowledge. The generator has also been designed to have no cogging torque so that it can be used with all horizontal and vertical axis turbine designs. The generator is efficiency is very high, particularly at part load. Typical efficiency values are 93-94%.
Index Terms—Wind power; Permanent magnet generators.
INTRODUCTION
Small scale wind turbines (less than 20 kW) are typically designed and manufactured by relatively small mechanical engineering companies. One component that causes particular problems is the electrical generator as suitable generators are not always readily available. In the case of mains-connected turbines the manufacturer is sometimes forced down the route of using a gearbox and standard 4-pole induction machine. For smaller turbines the manufacturer is inevitably looking at a specially built generator such as those described in [1] and [2]. Many of these turbine developers would like to employ a direct drive generator (no gearbox) whilst having a generator design that is mechanically simple, so enabling them to build their own if necessary. The generator must also be mechanically robust, cheap to make and easily integrated into the turbine system. It must also be easily modified for mains-connection operation, battery charge operation or for resistance heating. In addition it should produce no cogging torque to avoid any self-starting issues associated with some types of wind turbine.
THEORY
The generator consists of two rotor discs mounted either side of a non-magnetic, non-conducting stator, Fig. 3. The magnets are mounted in a N-S-N-S arrangement circumferentially round each rotor plate with the N magnet on one plate facing a S magnet on the other. The flux travels directly across the “air” space between the rotor discs before turning circumferentially in the rotor disc and travelling one pole pitch before returning back across the air-gap. A non-magnetic, non-conducting stator holds a number of circular bobbin wound armature coils positioned circumferentially round the stator. Although generators can readily be designed for any number of phases the generators described in this paper are all three phase machines with 16 magnets per disc and 12 armature coils. This combination gives a 240° phase shift between adjacent armature coils and provides for 4 coils per phase. By using simple bobbin wound armature coils it is straightforward to connect the four armature coils per phase in an appropriate series/parallel arrangement so that the generator is suitable for either mains-connect or battery charging. Alternatively, armature coils with a different number of turns can be used, the manufacturer simply selecting the appropriate coils for the application.
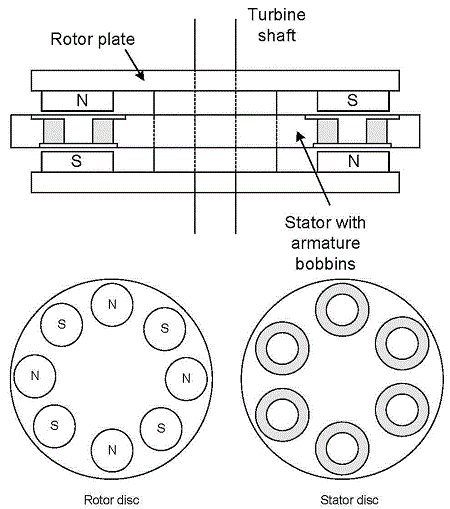
Figure 1 – Generator topology
The magnetic field distribution from the 16 magnets for the 1 kW generator is shown in Fig. 2. The flux density distribution is approximately sinusoidal in both the radial and circumferential directions so that the flux density profile over a magnet pitch can be thought of as a “sinusoidal hill” described by [3]
  (1)
where (2) - is the magnet equivalent current density.[6]
The assumption of the magnetic flux density forming a “sinusoidal hill” implies an axi-symmetric flux density distribution around each magnet with x being the radial distance from the centre of the magnet. This flux density profile can now be used to derive the flux between the centre of the armature coil and the radius raas
  (3)
If it is assumed that the armature coil is concentrated at its mean axial position, but that the coil is divided into three segments a, b and c in the radial direction, with the turns in each of these segments concentrated at the mean radius of that segment, then the total flux linkage is given by
  (4)
and the coil emf by
  (5)
In equation (4) a flux enhancement factor k1 is introduced (k1>1) to compensate for the fact that the flux calculated in the outer coil segment will be slightly less than actual. This is because the analysis assumes the flux density to be sinusoidally distributed in all directions round the magnet. However, this is only strictly true in the generator circumferential direction and not the radial as in this direction the flux density simply reduces to zero. Thus the flux calculated for the outer coil segment will be a slight underestimate. Typically k1=1.05 is used to compensate for this.
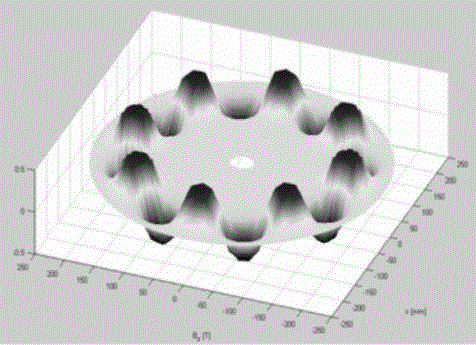
Figure 2 – Flux density distribution at the axial centre of a 12/16 generator
A similar approach can be taken in calculating the coil inductance but now the flux profile is assumed to conical with a trapezoidal cross section. The inductance of an armature coil is then given by [3]
  (6)
with the coil flux linkage given by
  (7)
Full details of this analysis can be found in [3].
The three phase generator output can be dissipated in a three phase resistor bank or, more usually, the output is rectified and used either to charge batteries or used directly as the dc link voltage to supply a grid tie inverter such as the SMA Windy Boy[7] as shown in Fig. 3.
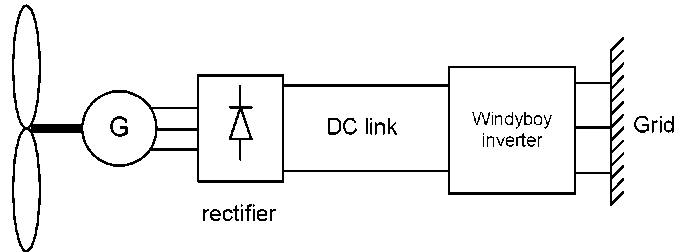
Figure 3 – Connection of Windy Boy to mains
In either case the generator and rectifier are conveniently represented by an equivalent circuit viewed from the dc side of the rectifier. Such an equivalent circuit is shown in Fig. 4 for battery charge applications. The battery is simply represented by its internal resistance and open circuit emf whilst the generator is modeled by its open circuit emf, its equivalent resistance and the equivalent overlap resistance [8]. If required an additional voltage is easily included to represent the diode volt drop in the rectifier.
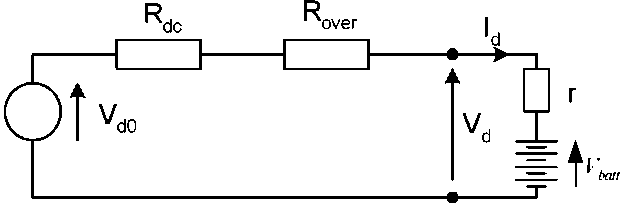
Figure 4 – Equivalent dc circuit for battery charging.
For a three-phase, 6–pulse, rectifier the effective armature resistance is approximately twice the phase resistance i.e.
  (8)
The overlap resistance is given by
  (9)
and the open circuit emf is related to the phase voltage by
  (10)
Simple circuit analysis gives the current as
  (11)
And the battery terminal voltage as
  (12)
The power supplied to the battery is now readily calculated as
  (13)
For mains connect applications through the grid-tie inverter the battery is simply replaced by the dc link capacitance and the mains connect inverter is modeled by its power transfer characteristics, Fig. 5. In the case of the SMA Windy Boy the power transfer characteristic is a linear function that depends on the dc link voltage [7]. As the generator used is a PM generator, then, to a first approximation, the power transfer is a direct function of turbine speed (neglecting voltage drops in the armature resistance and overlap resistance).
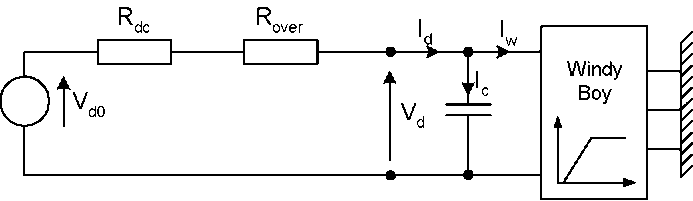
Figure 5 – Windy Boy equivalent circuit
For the Windy Boy to operate there must be a dc voltage of at least 260V. The dc link voltage that will correspond to maximum power transfer can be set at any voltage up to 600V. If set at, say, 450V then the inverter would transfer power as a linear function of voltage between 260 and 450V and above 450V would keep the power constant until the over-voltage cut-off condition is reached. This must be below 600V. The analysis is similar to before except now the power transfer through the inverter determines the current Iwas
  (14)
With the remaining equations being
  (15)
  (16)
  (17)
If feeding a resistive load the generator is simply represented by its per phase equivalent circuit shown in Fig. 6. Analysis of this circuit is straight-forward and gives the terminal power per phase as
  (15)
where k is the machine constant and w the rotational speed in rad/s. Provided the load resistance is significantly greater than the generator resistance and reactance (normal), then the final approximation relating power output to generator speed and load resistance holds.
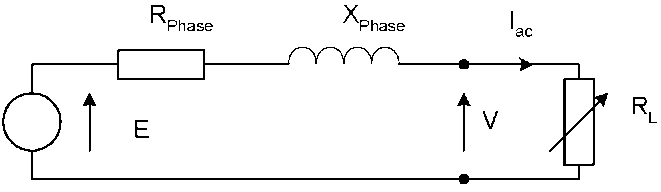
Figure 6 – A.C. equivalent circuit for a resistive load
CONCLUSION
This paper had described the design, manufacture and performance of a permanent magnet generator for use with small scale wind turbine. The generator is also ideally suitable for use with small water turbines. It is also easy to manufacture and with materials easily separated for reclamation at the end of its life. The generator produces no cogging torque and has an efficiency of typically 93-94%. Part load efficiency is particularly good. The modular winding design allows different coil arrangements and armature voltages to be readily accommodated. Predicted and measured performance, both at ac, and when operating through a rectifier, are in excellent agreement, with a maximum difference of 5%.
REFERENCES
Polinder, H.; “Design of a PM generator for the Turby, a wind turbine generator for the built environment”, 16th International Conference on Electrical Machines, Cracow, Poland, 5-8th September 2004, paper OS13-6.
Chalmers, B.J., Wu, W. and Spooner, E., “An axial flux permanent magnet generator for a gearless wind energy system”, IEEE Trans. On Energy Conversion, Vol. 14, No. 3, June 1999, pp 749-753
Bumby, J.R. and Martin, R. ”Axial-flux permanent-magnet air-cored generator for small-scale wind turbines”, Proc. IEE – Electrical Power Applications, Vol. 152, No. 5, September 2005, pp 1065-1075
Bumby, J.R. British Patent Application No 0412085.3 “Axial-flux, Permanent Magnet Electrical Machine”, 29 May, 2004
Carbon Concepts, Vertical axis-wind turbine and generator, http://www.carbonconcepts.co.uk/, 29 June, 2006
Bumby, J.R., Martin, R., Spooner, E., Brown, N.L. and Chalmers, B.J. ”Electromagnetic design of axial flux permanent magnet machines”, Proc. IEE – Electrical Power Applications, Vol. 151, No. 2, March 2004, pp 151-160
Windy Boy Grid Connect Inverter, http://www.sma-america.com/windyboy.html#2500, November 30th, 2004
Mohan, N., Underland, T.M. and Robbins W.P “Power Electronics – Converters, Applications and Design”, John Wiley and Sons, Third Edition, 2003, ISBN 0-471-429078-2.