УДК 621.313
МЕТОДИКА ОЦЕНКИ ТЕХНИЧЕСКОГО СОСТОЯНИЯ ТУРБОГЕНЕРАТОРА
Федоренко Григорий Михайлович
Кенсицкий Олег Георгиевич
Сегодня контроль технического состояния
турбогенератора обычно
сводится к контролю температуры наиболее ответственных узлов машины:
обмоток, стали сердечника,
хладагентов и т.д. Реально этот контроль состоит в сравнении текущих
температур с их предельно
допустимыми значениями - "уставками", при достижении которых на щит
управления выдается
предупредительный сигнал. Далее оператор должен принимать решение об
остановке машины,
ограничении нагрузки и т.д. При огромном потоке информации, поступающей
на щит управления от
различных систем, велика вероятность неправильной ее интерпретации и,
как следствие, принятия
оператором ошибочного решения, что может привести к тяжелым авариям и
дорогостоящему ремонту.
Примеров подобных инцидентов в практике эксплуатации мощных
турбогенераторов достаточно.
Вместе с тем проведенные исследования
показывают, что рациональное
использование и целенаправленная обработка оперативной информации,
поступающей от штатных систем
контроля, позволяют объективно оценивать техническое состояние активных
элементов машины,
определять их остаточный ресурс, по реальному состоянию планировать
проведение
ремонтно-восстановительных работ. Это можно рассматривать как первый
этап перехода к
прогрессивной технологии обслуживания и ремонта электротехнического
оборудования энергоблоков
электростанций по его реальному техническому состоянию вместо
применяемой сейчас технологии
планово-предупредительных ремонтов, когда обслуживание оборудования
проводится по временному
графику - по наработке.
Специалистами Института электродинамики НАНУ
разработана методика оценки
технического состояния турбогенератора и его систем, основанная на
целенаправленной обработке
оперативной информации, поступающей от штатных средств контроля машины,
которая позволяет:
- выявлять термометры сопротивления
штатной системы термоконтроля турбогенератора, показания которых по тем
или иным причинам (повреждение термометра, каналов связи и пр.) являются
недостоверными, требующими замены или ремонта;
- оценивать качество работы системы
охлаждения генератора: газоохладителей, теплообменников дистиллята,
системы газового охлаждения в целом;
- оценивать тепловое состояние обмотки
статора турбогенератора;
- выявлять термические дефекты обмотки
статора генератора;
- оценивать тепловое состояние сердечника
статора турбогенератора;
- оценивать тепловое состояние обмотки
ротора турбогенератора;
- проверять качество работы
воздухоохладителей системы охлаждения
Периодическая оценка эксплуатационного состояния
турбогенератора не заменяет функции штатных систем контроля, а
дополняет последние информацией диагностического характера.
Эксплуатационная оценка технического состояния
турбогенератора
выполняется по результатам анализа диагностических параметров и
заключается в сравнении текущих
значений последних с их исходными (базовыми) значениями, полученными на
заведомо исправной машине
при пусконаладочных испытаниях или сразу после последнего капитального
ремонта. Сравнение проводится с учетом принятых нормативов на допустимые
различия текущих и исходных значений.
В качестве диагностических приняты значения
параметров математических моделей, учитывающих реальную конструкцию
элементов и узлов машины, характер протекания в них теплообменных
процессов и описывающих показания термометров штатной системы
термоконтроля турбогенератора в зависимости от режима нагружения машины,
а также температур хладагентов - водорода и дистиллята в пределах
контролируемой зоны:
где Θi - температура, зафиксированная термометром
сопротивления в контролируемой
зоне; U, I - параметры режима нагружения турбогенератора; θг,θд
- температура водорода и дистиллята в контролируемой зоне.
Если же тепловые потери в узле отсутствуют
(газоохладители, теплообменники дистиллята), то математическая модель
представляет собой зависимость между соответствующими температурами
хладагентов.
В данном случае, например, модель для
термометров сопротивления, контролирующих температуру стержней обмотки
статора и расположенных между стержнями, представляет собой
регрессионную зависимость вида
| Θi = A1·I2
+ A2
θг + A3θд, | (2) |
а для газоохладителя соответственно
| Θгг - Θхг = B(Θгвг
-
Θхвг), | (3) |
где Θгг, Θхг - температура водорода до и после
газоохладителя;
Θгвг, Θхвг - температура охлаждающей воды на
выводе и на входе
газоохладителя соответственно.
Аналогично модель для термометров сопротивления,
расположенных на дне
паза, вида (2) дополняется составляющей, учитывающей наличие контакта со
сталью (Аi
U2), а для
теплообменника дистиллята имеет вид (3) и связывает температуры
дистиллята на входе и выходе и
температуру охлаждающей воды. При этом принимается, что тепловые потери в
меди обмотки
пропорциональны квадрату тока статора, а потери в стали пакетов
сердечника - квадрату напряжения
на зажимах обмотки.
Таким образом, коэффициенты математических
моделей (2) и (3) Аi
и Bi отражают характер и интенсивность протекания
теплообменных процессов в
контролируемой зоне и являются диагностическими параметрами, анализ
изменения которых позволяет
выявить возникающие нарушения и дефекты, проследить темп их развития.
Значения этих коэффициентов определяются
методами регрессионного анализа
по значениям режимных параметров и показаниям штатной системы
термоконтроля турбогенератора,
зафиксированным в нескольких (не меньше четырех) установившихся по
нагреву режимах нагружения
машины, отличающихся как параметрами нагрузки, так и температурами
хладагентов. Количество
режимов связано с максимальным количеством членов регрессионных
зависимостей, моделирующих
показания термометров штатной системы термоконтроля. В данном случае их
должно быть 6…7 в
диапазоне нагрузки 60…100 % от номинальной с разбросом температур
хладагентов в диапазоне ±10 %
от средних значений.
Указанные диагностические параметры по своей
сути носят интегральный характер, и поэтому для их последующего
определения нет необходимости в точном повторении режимов, при которых
были определены их предыдущие значения.
При выявлении в результате сравнения
диагностических параметров признаков неисправности системы охлаждения
генератора или возбудителя, а также наличия термических дефектов для
исключения ошибки процедуру определения значений соответствующих
параметров необходимо повторить. Если диагноз подтверждается, то
выдается заключение о том, что контролируемый узел или система нуждаются
в ревизии и ремонте и на какие именно моменты необходимо обратить
особое внимание.
Необходимость внеочередной оценки технического
состояния турбогенераторов, включая возбудитель, может возникать при
наличии хотя бы одного из следующих условий:
- эксплуатация турбогенератора после анормальных
режимов (перегрузка по току ротора или статора, перегрев ротора или
статора, работа с повышенным напряжением статора и пр.);
- ухудшение эффективности охлаждения узлов
турбогенератора и возбудителя;
- появление признаков локальных перегревов или
нарушения охлаждения отдельных элементов генератора и возбудителя;
- неизбежность эксплуатации генератора и
возбудителя с отклонениями от заданных допустимых параметров
эксплуатационных режимов;
- продление срока службы генератора сверх
нормативного;
- разборка и сборка газоохладителей
турбогенератора;
- разборка и сборка воздухоохладителей
возбудителя;
- разборка турбогенератора с выводом ротора.
При наличии устойчивого изменения какого-либо
диагностического параметра состояния производится оценка темпов его
изменения и степень опасности зарегистрированного изменения для машины в
целом. По достижению тревожного уровня принимается решение о
необходимости проведения мероприятий по ограничению возможного
отрицательного развития ситуации (то ли ограничение нагрузки, то ли
интенсификация охлаждения и пр.). Достижение же диагностическим
параметром предельного (аварийного) уровня требует немедленной остановки
машины и проведения ремонта. При этом при его приближении к предельному
значению следует проводить внеочередные оценки технического состояния
один раз в смену, а при наличии автоматизированных систем контроля -
один раз в час (и чаще).
Большинство энергоблоков украинских ТЭС
вводились в эксплуатацию в 70…80-х годах прошлого века, и большинство из
них, в лучшем случае, оснащены автоматизированной системой контроля
параметров режима (АСКР). А блоки, пущенные ранее, не имеют и ее.
То есть внедрение диагностического комплекса,
реализующего разработанную методику, на большинстве энергоблоков
возможно только в результате проведения коренной реконструкции в составе
вновь созданной современной автоматизированной системы управления
технологическим процессом (АСУ ТП). Кроме того, внедрение
интеллектуализированного метода обработки эксплуатационной информации
требует определенного уровня квалификации и подготовки персонала, что
также представляет некоторую проблему для эксплуатации.
В этих условиях на первоначальном этапе
внедрения разработки в эксплуатацию целесообразным является создание
единого центра сбора и обработки оперативной информации. Этим
обеспечивается "единообразие" подхода к диагностическим процедурам,
необходимый уровень специалистов-аналитиков. При современном уровне
развития информационных технологий исходная информация от любой ТЭС
может быть беспрепятственно и в кратчайшие сроки передана в центр и
обработана. Таким же
образом персоналом ТЭС может быть получено заключение о техническом
состоянии конкретного турбогенератора, что может быть использовано при
определении сроков проведения и необходимых объемов ближайшего
планово-предупредительного ремонта или для оптимизации, в зависимости от
состояния, режимов работы конкретного оборудования.
При наличии АСУ ТП (или хотя бы АСКР) процедура
сбора и передачи оперативной информации в диагностический центр не
представляет сложности. Хуже обстоит дело с энергоблоками постройки 60-х
годов. Там все эти процедуры придется выполнять вручную. Тем не менее,
если машина проработала более 200 тыс. часов, это необходимо. Вне всяких
сомнений, затраты себя оправдают.
На сегодняшний день методика оценки технического
состояния турбогенератора адаптирована для турбогенераторов типа
ТВВ-1000-4У3 (8 энергоблоков украинских АЭС). Проводятся работы по
адаптации методики для турбогенераторов ТВВ-1000-2У3 (5 энергоблоков
АЭС), ТГВ-300 (42 энергоблока ТЭС), ТГВ-200 (34 энергоблока), ТГВ-200М
(5 энергоблоков).
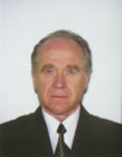 |
Федоренко Григорий Михайлович
Федоренко Григорий Михайлович Ведущий научный сотрудник отдела №10 ИЭД
НАН Украины. Родился в 1939 г. Окончил Киевский политехнический институт
в 1962 г. В 1990 г. защитил докторскую диссертацию по специальности
"Электрические машины и аппараты". Лауреат Государственной премии
Украины в области науки и техники (2002 г.). Основные научные интересы:
надежность и нагрузочная способность турбо- и гидрогенераторов ТЭС, ГЭС,
АЭС и жидкостно-заполненных электромашин специального назначения.Тел./
факс (044) 454-24-16; E-mail: gmf@ied.org.ua
|
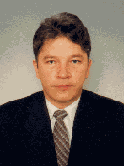 |
Кенсицкий Олег Георгиевич
Родился в 1958 г. В Институте электродинамики работает с 1982 г. после
окончания Киевского политехнического института. В 1992 г. защитил
диссертацию на соискание ученой степени кандидата технических наук по
специальности "Электрические машины и аппараты". С 1994 г. - старший
научный сотрудник отдела № 10.Область научных интересов: исследование
электромагнитных и тепловых процессов в крупных электрических машинах
общепромышленного и специального назначения, разработка и исследование
систем контроля, диагностики и прогнозирования ресурса крупных
машин.Тел.: 454-25-23, (067) 422-39-15, E-mail: snl@ied.org.ua
|