|
Artificial neural network based fault identification scheme implementation
for a three-phase induction motor
Sri R. Kolla, Shawn D. Altman
Electronics and Computer Technology Program, Department of Technology Systems, Bowling Green State University, Bowling Green, OH
Источник: http://hinari-gw.who.int
Abstract
This paper presents results from the implementation and testing of a PC based monitoring and fault identification scheme for a three-phase
induction motor using artificial neural networks (ANNs). To accomplish the task, a hardware system is designed and built to acquire threephase
voltages and currents from a 1/3 HP squirrel-cage, three-phase induction motor. A software program is written to read the voltages and
currents, which are first used to train a feed-forward neural network structure using the JavaNNS program. The trained network is placed in a
LabVIEWTM based program formula node that monitors the voltages and currents online and displays the fault conditions and turns the motor
off. The complete system is successfully tested in real time by creating different faults on the motor.
c 2007, ISA. Published by Elsevier Ltd. All rights reserved.
Keywords: Artificial intelligence; Neural networks; Induction motor; Faults; Protection; Relays
1. Introduction
The three-phase induction motor is a workhorse of the
manufacturing industry. This motor may encounter several
fault conditions, which can damage the motor. These
conditions include overload, unbalanced supply voltage, locked
rotor, single phasing, undervoltage, and overvoltage [1].
Microprocessor based protective relays are used to monitor
these motors and disconnect them during faults [2]. The recent
trend in microprocessor based relays is to use artificial neural
network (ANN) based techniques [3].
Elmore and Kramer [4] proposed microprocessor relay
technology for protection of motors. Lacroix and Clegg [5]
used microprocessors to identify the kinds of faults that occur
in three-phase motors. Pandurangavittal, Fakruddin, Rao, and
Parthasarathy [6] designed and built a microcontroller based
three-phase induction motor relay that provides an operator
selectable thermal I –T (current versus time) curve feature.
Farag and Kamel [7] designed and implemented a standalone
microcontroller based digital protection system using an
MC-8031 controller for three-phase induction motors.
et al. applied ANNs for the detection of incipient faults in
single-phase induction motors in the early 90’s [8,9]. They
identified stator winding faults and bearing wear using ANNs.
The motor current and speed were used as inputs. Kolla and
Varatharasa used ANNs for fault identification in a three-phase
induction motor [10]. They used software simulation to produce
data to train an ANN to determine some of the main faults in
an induction motor. Offline testing results for that scheme using
simulated data showed promising results. Different stator fault
monitoring techniques for induction motors are reviewed in a
recent paper by Siddique et al. [11]. An extensive list of 183
references on this topic is given in that paper.
The proposed work in this paper implements the ANN based
fault identification scheme in hardware and tests it in real time.
A 1/3 HP squirrel-cage, three-phase induction motor is used
for this purpose. Section 2 reviews concepts of induction motor
faults and artificial neural networks, and previous methods
of ANN use for fault identification [10]. Details of the
proposed hardware system are described in Section 3. Section 4
describes the training of feed-forward ANNs with threephase
voltages and currents using the JavaNNS program [12].
The development of LabVIEWTM [13] based software for
testing the complete fault identification system is described in
Section 5. Section 6 offers some concluding remarks.
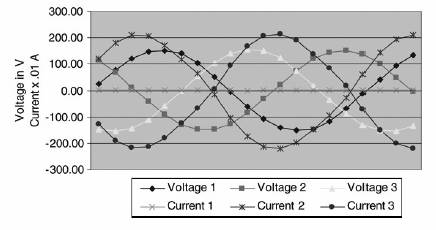
Fig. 1. Three-phase voltages and currents for the single-phasing fault.
2. Induction motor fault identification using an ANN
An induction motor may experience several kinds of faults
during its operation [1]. The main kinds of faults include
overloading, single phasing, unbalanced voltage, locked rotor,
ground fault, undervoltage, and overvoltage. A detailed
discussion of these faults is given in Kolla and Varatharasa [10].
From this information it can be noted that the motor voltages
and currents have distinct characteristics during these faults.
For example, in the case of single phasing, one phase current
is zero and the other two-phase currents have equal magnitude
with a 180_ phase difference while the three-phase voltages
have equal magnitudes with 120_ phase difference between
them, as shown in Fig. 1. The three-phase voltage and current
information is used in identifying faults using ANNs in
this paper. While the applicability of the ANN method for
identifying various simulated faults is demonstrated in [10], the
present work implements the ANN scheme and tests it in real
time for those faults that do not damage the motor.
The ANN tries to mimic the biological brain neural
network in a mathematical model [14]. It is a collection of
simple processing units, mutually interconnected, with weights
assigned to the connections. By modifying these weights
according to a learning rule, the ANN can be trained to
recognize a pattern given the training data. Fig. 2 shows the
simple processing unit in which the process is done by adding
the input signals after multiplying by their link’s weight and the
total is transferred to the transfer function part of the neuron.
There are several transfer functions such as tanh, sigmoid, etc.
There are several kinds of neural network structures proposed in
the literature [15]. A feed-forward network is shown in Fig. 3.
There can be several hidden layers in the network. The figure
shows one hidden layer. In this network, the number of input
nodes and the number of output nodes are determined by the
number of patterns to be identified. The number of nodes in
the hidden layer is selected for an application, generally using
a trial and error method. The neural network has to be trained
so that it can identify the output patterns corresponding to the
input pattern. There are several kinds of training algorithms
suggested in the literature [15]. The back-propagation is one
of the most popularly used algorithms. In this paper a feedforward
network is used, and it is trained with the backpropagation
algorithm. JavaNNS software [12] is used to create
and train the network. While there are many different ANN
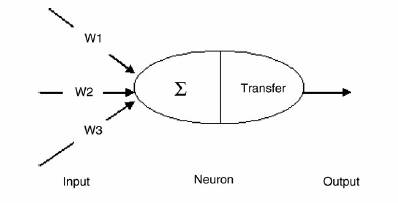
Fig. 2. Simple processing unit.
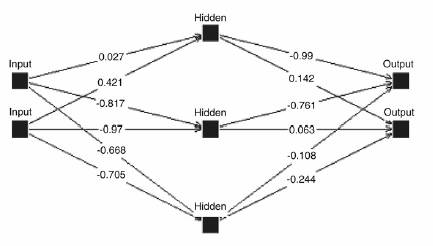
Fig. 3. Feed-forward neural network.
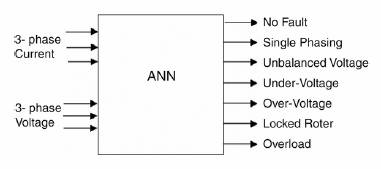
Fig. 4. Inputs and outputs of the ANN.
structures and different training algorithms available in the
literature [14], in the present work a feed-forward network with
back-propagation training is found adequate.
In order to use an ANN for identifying induction motor
fault and no fault conditions, it is necessary to select proper
inputs and outputs of the network, and structure of the
network, and train it with appropriate data. In this study,
inputs are selected as RMS values of three-phase voltages and
currents. Therefore, there are six input neurons. There are seven
outputs corresponding to six faults listed before and a no fault
condition. The output goes to 1 if that particular condition exits;
otherwise it is zero. Therefore, there are seven output neurons.
There is one hidden layer, and the number of neurons in that
layer is varied during training. Fig. 4 illustrates the inputs and
outputs of the ANN.
3. Induction motor fault identification system set-up
The complete hardware system for induction motor fault
identification is developed using the set-up shown in Fig. 5. A
block diagram of this system is shown in Fig. 6. In this system,
the motor is connected to a three-phase supply through three
VARIACS connected in a star fashion. A signal conditioning
circuit that reduces the three-phase voltages and converts threephase
currents into voltages proportional to the currents is
used. The signal conditioner uses a voltage transducer to step
the voltage down, and a circuit is made so that it produces
a voltage proportional to the motor currents. A second-order
active low-pass Butterworth filter is used so that only low
frequency signals are passed to the DAQ board on the National
Instruments SCXI 1000 chassis [13]. The motor used for this
study is a 1/3 HP three-phase squirrel-cage induction motor.
The SCXI chassis contains simultaneous sampling analog
input module 1140 to collect the voltages and currents, and
eight-channel power relay output module 1161 to simulate
circuit breakers. The chassis communicates with multifunction
I/O card PCI-MIO-16E-1 placed in the PC. A Prony
brake is used to simulate various loading conditions. A
LabVIEWTM program is written to simultaneously acquire the
signal conditioned instantaneous motor voltage and current
data values. The program acquires data at a sampling rate of
1000 scans/s. The program then converts these data values into
RMS values. These signals are used to train and test the ANN
based fault identification scheme.
4. Training of the ANN for fault identification
The ANN structure shown in Fig. 4 is trained with the data
sets obtained from the actual faults created on the induction
motor. This study uses the RMS values of voltages and
currents as inputs to the ANN. A total of 788 input patterns
corresponding to different faults, as described in Table 1,
are used. The no-fault’s 154 patterns represent various load
conditions ranging from no load to full load at selected
increments of load. The single-phasing fault’s 85 patterns
represent each of the three phases removed separately with
different loads. Similarly the remaining fault pattern represent
various possible combinations for each fault.
The JavaNNS program [12] is used to build and train the
ANN structure offline and to determine the appropriate number
Table 1
Number of training patterns per fault
Condition Number of patterns
No fault (NF) 154
Single phasing (SP) 85
Unbalanced voltage (UB) 450
Undervoltage (UV) 49
Overvoltage (OV) 10
Locked rotor (LR) 10
Overload (OL) 30
Total 788
of neurons in the hidden layer. A screen shot of the JavaNNS
program is shown in Fig. 7. The process of constructing the
network involves adding the input layer to the network by
selecting the unit type as input, the height of six for the number
of neurons in the layer, and the sigmoid transfer function, which
is called the logistic function in JavaNNS. Then the hidden
layer is added by selecting the sigmoid function, hidden unit
type, and various numbers for the hidden layer neurons. For
this study, the best results are achieved using eight hidden
layer neurons. As explained in Section 2, selection of the
number of neurons in the hidden layer is a trial and error
process based on achieving the best training of the network.
The last layer is added by selecting the unit type output,
the height of seven for the number of neurons in this layer,
and the sigmoid transfer function. Once the ANN structure is
constructed, the training process involves choosing parameters
for _ (momentum coefficient) and _ (learning coefficient) by
trial and error, when using back-propagation with momentum
algorithm. JavaNNS also includes a maximum non-propagating
error and flat spot eliminator, which worked best when set
to zero in this study. This study tried numbers 0.1–0.9 in
increments of 0.1 for the momentum and learning coefficients
and had the best results with 0.1 for _ and 0.1 for _. After
160,000 training iterations for the ANN structure, the sum of
squared errors (SSE) reduced to 0.013284. The training of the
ANN is performed offline. The number of iterations and the
time it takes for these iterations will not have any effect on the
online identification of faults.
After the network is built and trained it is saved, along with
the biases, weights, and the log file. This file is used as an input
to a program that is written in Visual Basic to change the trained
ANN into a C-program based LabVIEWTM formula node that
is used to determine the current state of the motor based on the
data read into the computer.
5. Testing of ANN based fault identification system
Online testing of the system involves adding the
LabVIEWTM code to read the data in real time and pass the

Fig. 6. Block diagram of complete fault identification system.
values to the formula node. The motor is turned off using the
circuit breaker module on SCXI chassis, shown in Fig. 5, if a
fault is encountered. The LabVIEWTM program used for this
testing is the program shown in Fig. 8. The performance of the
complete system during several faults was verified. Undervoltage,
overvoltage, and unbalanced voltage faults are simulated
by controlling individual phase voltages using three VARIACs.
A Prony brake is used to simulate overload and locked rotor
conditions. Disconnecting a phase power line simulates a
single-phasing fault. The results for a few example cases are
collected and reported in Table 2. This table shows the inputs
and outputs for the ANN structure. The output of the ANN for
a particular fault is close to 1.0 while the other outputs are close
to 0.0 when that fault is present. In the final implementation of
the scheme, a 5% threshold is allowed around these values in
identifying the faults. The input voltage and current waveforms
used to obtain results in Table 2 for the single-phasing case are
shown in Fig. 9. The actual fault indication for the fault case
is also depicted on the same LabVIEWTM panels shown in the
screen shots in Fig. 9. The input voltage and current waveforms
along with the fault indication for the unbalanced supply voltage
case are shown in Fig. 10. The results for other faults can
be found in reference [16]. It is clear from these results that the
ANN based scheme has successfully identified the faults for a
three-phase induction motor.
6. Conclusions
This paper described the implementation and testing of a PC
based fault identification scheme for a three-phase induction
motor using the ANN. To accomplish this, a hardware system
was designed and built to acquire three-phase voltages and
currents from an induction motor. A 1/3 HP squirrel-cage
three-phase induction motor was used to create faults and
collect data for training and testing the ANN based system. A
LabVIEWTM program was written that read the voltages and
voltage representation of the currents. These voltages were first
used to train an ANN structure using the JavaNNS program.
The trained network was placed in the LabVIEWTM program
formula node that monitored the voltages and currents online
and displayed the fault conditions and turned the motor off. The
complete system was successfully tested in real time by creating
different faults for the three-phase induction motor. This study
shows an example of how the theories behind neural networks
work accurately in a real world application.
Acknowledgements
The authors thank Drs. David Border and Erik Mayer of the
Electronics and Computer Technology Program, Department of
Technology Systems, Bowling Green State University, for their
helpful suggestions on this work.
References
[1] ABB Relaying Division. Protective relaying: Theory and application. New
York (NY): Marcel Dekker, Inc.; 1994.
[2] Phadke AG, Thorp JS. Computer relaying for power systems. New York
(NY): John Wiley & Sons; 1988.
[3] Sachdev MS. (Coordinator), Advancements in microprocessor based
protection and communication. IEEE tutorial course text. Publication no.
97TP120-0, New York (NY); 1997.
[4] Elmore WA, Kramer CA. Complete motor protection by microprocessor
relay. In: Proceedings of Georgia tech protective relaying conference.
1987. p. 1–13.
[5] Lacroix B, Clegg D. Microprocessor motor protection relay. In:
Proceedings of 4th international conference on developments in power
system protection. IEE Pub. No. 302. 1989. p. 235–8.
[6] Pandurangavittal K, Fakruddin DB, Rao IR, Parthasarathy K. Microcontroller
based three-phase induction motor protection relay with operator
selectable thermal I –T curve feature. Electric Machines and Power Systems
1998;26:13–26.
[7] Farag WA, Kamel MI. Microprocessor-based protection system for threephase
induction motor. Electric Machines and Power Systems 1999;27:
453–64.
[8] Chow M-Y, Yee S-O. Using neural networks to detect incipient faults in
induction motors. Journal of Neural Network Computing 1991;2:26–32.
[9] Chow M-Y, Sharpe RN, Hung JC. On the application and design of
artificial neural networks for motor fault detection. IEEE Transactions on
Industrial Electronics 1993;40:181–96.
[10] Kolla SR, Varatharasa L. Identifying three-phase induction motor faults
using artificial neural networks. ISA Transactions 2000;39:433–9.
[11] Siddique A, Yadava GS, Singh B. A review of stator fault monitoring
techniques of induction motors. IEEE Transactions on Energy Conversion
2005;20:106–14.
[12] Fischer I, Hennecke F, Bannes C, Zell A. JavaNNS. http://www-ra.
informatik.unituebingen.de/JavaNNS/, 2001.
[13] National instruments, LabVIEW requirements. www.ni.com/labview/
requiremts/, 2003.
[14] Lau C, editor. Neural networks: Theoretical foundations and analysis.
New York (NY): IEEE Press; 1992.
[15] Caudill M, Butler C. Understanding neural networks: Computer
explorations. Cambridge (MA): MIT Press; 1992.
[16] Altman SD. Real-time implementation of a fault identification scheme
for a three-phase induction motor using artificial neural networks. M.I.T.
thesis. Bowling Green (OH): College of Technology, Bowling Green State
University; 2004.
|