|
Identifying three-phase induction motor faults using artifical neural networks
Sri Kolla *, Logan Varatharasa
Electronics and Computer Technology Program, Department of Technology Systems, Bowling Green State University, Bowling Green, OH
Источник: http://hinari-gw.who.int
Abstract
This paper presents an arti®cial neural network (ANN) based technique to identify faults in a three-phase induction
motor. The main types of faults considered are overload, single phasing, unbalanced supply voltage, locked rotor, ground
fault, over-voltage and under-voltage. Three-phase currents and voltages from the induction motor are used in the pro-
posed approach.A feedforward layered neural network structure is used. The network is trained using the backpropagation
algorithm. The trained network is tested with simulated fault current and voltage data. Fault detection is attempted in the
no fault to fault transition period. OЂ-line testing results on a 3 HP induction motor model show that the proposed
ANN based method is eЂective in identifying various types of faults. # 2000 Elsevier Science Ltd. All rights reserved. Keywords: Arti®cial intelligence; Industrial computing; Neural networks; Induction motor; Protection; SCADA
1. Introduction
Three-phase induction motors are the most
popular motors used in industrial applications due
to their reliability, low cost and high performance.
These motors often experience several types of
faults. The main types are overload, single phas
ing, unbalanced supply voltage, locked rotor,
ground fault, over-voltage and under-voltage [1].
For high rating motors, protective relays are used
to monitor these faults and disconnect the motors
in case of a faulty situation. The traditional pro
tective relays based on electromechanical and solid
state devices are being replaced by micro-
processor-based relays due to several advantages
[2,3]. Recently ANN is proposed for fault identi®-
cation and other power system applications [4].
Elmore and Kramer proposed microprocessor
relay technology for protection of motors [5].
Lacroix and Clegg used microprocessors to identify
the types of faults occur in motors [6]. Kolla et al.
presented a microprocessor-based protection
scheme for induction motors that used a block
pulse functions based algorithm [7]. Pandurangavittal et al. [8] have designed and built a microcontroller based induction motor relay that
provides an operator selectable thermal I±T curve
feature. The use of ANN for induction motor
fault identi®cation was ®rst proposed by Chow et
al. [9±12]. They have primarily considered incipient faults for single-phase motors. On the other
hand, this paper proposes the use of ANN for
identifying diЂerent types of external faults on
three-phase induction motors.
In an ANN, an optimization technique allows
the network to ``learn'' rules for solving a problem
by processing a set of examples. There are several
types of neural network structures proposed in the
literature, and there are several types of training
algorithms suggested [13]. In this paper, a feed
forward layered neural network structure is used
because of its simplicity and popularity [4]. The
network is trained using the backpropagation
algorithm. The RMS values of three-phase currents
and voltages from the induction motor are used in
the proposed approach. Fault detection is attemp-
ted in the no fault to fault transition period. OЂ-
line testing results on a 3 HP induction motor
model show that the proposed ANN based
method is eЂective in identifying various types of
faults. The fault identi®cation information can be
used for alarm monitoring and protective relaying
purposes.
2. Induction motor faults
A three-phase induction motor may experience
several types of fault conditions which include [1]:
1. Overload
2. Locked rotor
3. Single phasing
4. Unbalanced supply voltage
5. Ground fault
6. Over-voltage
7. Under-voltage
An increased mechanical load on the motor
beyond the rated value results in increased phase
currents, and over heating of the motor. In a tra-
ditional relay protection system, the over current
relay will trip the motor oЂ line. A trip command
is usually given after a speci®ed time depending
upon the magnitude of the current.
The locked rotor condition results in over cur
rent situation. Extreme heating occurs, particu
larly in the rotor. This condition can be tolerated
for only a limited time. Tripping time is deter-
mined according to the inverse time characteristics
in a traditional relay scheme.
When one of the phases of the three-phase motor
is open, single phasing situation occurs. This
results in increased positive and negative sequence
currents, and hence excessive heating. An over
current relay that uses thermal current protects the
motor during this abnormal operating condition.
Unbalanced supply voltage results in negative
sequence voltage. It may also give increased positive
and negative sequence currents. An over current
relay protects the motor during the unbalanced
supply. This situation is also detected by deter-
mining the negative sequence current and voltage.
Ground faults are more prevalent in motors
than other power system devices, because of the
violent manner and frequency with which they are
started. These faults are detected by observing the
zero sequence current. The motor is immediately
disconnected during ground faults.
A reduced supply voltage with a rated mechan-
ical load on the motor results in increased current,
and hence excessive heating of the motor. An over
current relay can protect the motor during this
case. A motor can also be protected against under-
voltages using voltage-time characteristics.
An increased voltage on the motor might have
harmful eЂects on its insulation. A motor can be
protected against over-voltages using voltage-time
characteristics.
Several microprocessor-based relay schemes that
can protect a motor under all these abnormal
conditions exist in the literature [5±8]. Though
these schemes are eЂective in protecting a motor,
some of them are computationally intense. This
paper, therefore, suggests an ANN based scheme
to identify these faults.
3. Arti®cial neural networks
The ANN tries to mimic the biological brain
neural network into a mathematical model [14]. It
is a collection of simple processing units, mutually
interconnected, with weights assigned to the con-
nections. By modifying these weights according to
some learning rule, the ANN can be trained to
recognize any pattern given the training data.
There are several types of neural network struc-
tures proposed in the literature [13]. A feedfor-
ward layered network is shown in Fig. 1. There
can be several middle layers in the network. The
®g. shows one middle layer. The number of neurons in the input and output layers are governed
by the number of inputs and outputs of the pat-
tern to be recognized. However, the number of
neurons in the middle layer can be selected
depending upon the application. Usually, there is
no processing done in the input neuron.
There are several types of training algorithms
suggested in the literature [13]. The back-
propagation is one of the most popularly used
algorithms.
4. ANN for identifying induction motor faults
In order to use ANN for identifying induction
motor fault and no fault conditions, it is necessary
to select proper inputs and outputs of the net-
work, structure of the network, and train it with
appropriate data. In this study, inputs are selected
as RMS values of three-phase voltages and cur-
rents. Therefore, there are six input neurons.
There are eight outputs corresponding to seven
faults described before and a no fault condition.
The output goes to 1 if that particular condition
exits, otherwise it is zero. Therefore, there are
eight output neurons. There is one middle layer,
and the number of neurons in that layer is varied
during training. Fig. 2 illustrates the inputs and
outputs of the ANN.
To train the network, simulated voltage and
current waveforms representing the seven diЂerent
faults and no fault condition are considered. These
waveforms are obtained using a C-program written
to simulate a 3 HP, 400 V, squirrel cage induction
motor [15]. For example, Fig. 3 shows the wave-
form for a ground fault situation. Similar wave-
forms are given for other faults in Ref. [15]. From
the instantaneous voltage and current values of the
waveform, RMS values are calculated using the dis-
crete fourier transform (DFT) algorithm [2]. The
DFT algorithm ®lters harmonic frequency noise and
extracts fundamental frequency components. These
RMS values are used in the training and testing
process. A total of 201 data sets are used in the
training. They represent various cases as follows:
Unbalanced supply voltage 34
Ground fault 35
Single phasing 7
Locked rotor 50
Overload 34
Over-voltage 14
Under-voltage 21
No fault 6
The network is trained using the backpropagation
algorithm. For this training, Neuralware Inc.'s
Neural Works Professional II/Plus software is
used [16]. In training the network, learning coe.-
cient (_) and the momentum coe.cient (_) are
chosen with diЂerent values each time. Networks
with 6±9±8, 6±10±8 and 6±11±8 input, middle and
output layer neurons are trained. Training was
processed through error convergence criteria [16].
The 6±11±8 network produced the best con-
vergence. For this network, the error convergence
used is 0.01, learning coe.cient (_) used is 0.8 and
the momentum coe.cient (_) used is 0.6. Table 1
gives the 6_11 matrix of trained network weights
and biases from input to middle layer, and Table 2
shows the 11_8 matrix of weights and biases from
middle to output layer.
The trained network is tested with data sets
consisting of trained data of 201 data sets, and a
modi®ed set of data from training set. The mod-
i®ed set of data consisted of changing some of the
trained set data by a _15% variation in RMS
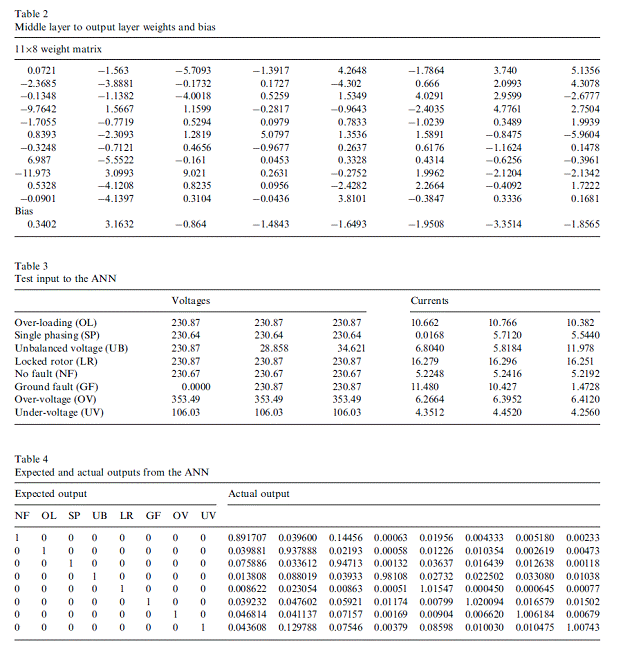
values of three-phase voltages and currents. A
total of 50 additional data sets are generated with
the modi®cation. These test data sets are fed to the
ANN and the results are obtained. One of the data
sets used is shown in Table 3. The table shows the
actual RMS voltages and currents for all the seven
faults and no fault case. The tested results in Table
4 show, for each situation, the expected output
and the magnitudes of actual output from the
ANN. These results are obtained from the Neural
Works program [16]. It is clear from the Table 4
that the ANN has successfully identi®ed the faults.
The output of the ANN for a particular fault is
close to 1.0 while the other outputs are close to 0.0
when that fault is present. The closeness is within
_12% in worst case situation. Though the results
are satisfactory for the cases considered, further
improvements can be obtained if more data points
are used in training.
5. Conclusions
This paper described an application of ANN for
identi®cation of external faults on a three-phase
induction motor. A feedforward layered ANN
structure was used, and trained using the back-
propagation algorithm. The paper gave details of
diЂerent parameters used in the backpropagation
training algorithm. It provided oЂ-line testing
results using simulated fault data. The paper used
RMS values of voltages and currents. Other sig-
nals that may be tried are instantaneous values of
voltages and currents, and symmetrical compo-
nents of voltages and currents. To increase the
accuracy of fault identi®cation, the training set
should have a larger data with more fault situa-
tions. The present paper did not test the method
against any other noisy data. Work is underway to
test the proposed scheme using real-time signals
from an operating three-phase induction motor.
References
[1] ABB Relaying Division, Protective Relaying: Theory and
Application, Marcel Dekker, Inc., New York, 1994.
[2] A.G. Phadke, J.S. Thorp, Computer relaying for power
systems, John Wiley & Sons, New York, 1988.
[3] M.S. Sachdev (Coordinator), Advancements in Micro-
processor Based Protection and Communication, IEEE
Tutorial Course Text, Publication No. 97TP120-0, IEEE,
New York, 1997.
[4] M.A. El-Sharkawi, D. Niebur (Eds.), A Tutorial Course
on Arti®cial Neural Networks with Applications to Power
Systems, IEEE Tutorial Course Text, Publication No.
96TP112-0, IEEE, New York, 1996.
[5] W.A. Elmore, C.A. Kramer, Complete motor protection
by microprocessor relay, in: Proceedings of Georgia Tech
Protective Relaying Conference, Atlanta, GA, April 1987,
pp. 1±13.
[6] B. Lacroix, D. Clegg, Microprocessor motor protection
relay, in: Proceedings of 4th International Conference on
Developments in Power System Protection, IEE Pub. No.
302, 1989, pp. 235±238.
[7] S.R. Kolla, D.V. Gedeon, Microprocessor-based protec-
tion scheme for induction motor, in: Proceedings of Elec-
trical Manufacturing and Coil Winding Association
Conference, Chicago, IL, September 1994, pp. 119±123.
[8] K. Pandurangavittal, D.B. Fakruddin, I.R. Rao, K. Par-
thasarathy, Microcontroller based three-phase induction
motor protection relay with operator selectable thermal I±
T curve feature, Electric Machines and Power Systems 26
(1998) 13±26.
[9] M.-Y. Chow, S.O. Yee, Using neural networks to detect
incipient faults in Induction motors, Journal of Neural
Network Computing 2 (1991) 26±32.
[10] M.-Y. Chow, S.O. Yee, Methodology for on-line incipient
fault detection in single-phase squirrel-cage induction
motors using arti®cial neural networks, IEEE Transac-
tions on Energy Conversion 6 (1991) 536±545.
[11] M.-Y. Chow, R.N. Sharpe, J.C. Hung, On the application
and design of arti®cial neural networks for motor fault
detection, IEEE Transactions on Industrial Electronics 40
(1993) 181±196.
[12] P.V. Goode, M.-Y. Chow, Using a neural/fuzzy system to
extract heuristic knowledge of incipient faults in induction
motors, IEEE Transactions on Industrial Electronics 42
(1995) 131±146.
[13] C. Lau (Ed.), Neural Networks: Theoretical Foundations
and Analysis, IEEE Press, New York, 1992.
[14] M. Caudill, C. Butler, Understanding Neural Networks:
Computer Explorations, MIT Press, Cambridge, MA,
1992.
[15] L. Varatharasa, Application of Arti®cial Neural Networks
for Identi®cation of Simulated Faults in Induction
Motors, M.I.T. Project Report, College of Technology,
Bowling Green State University, Bowling Green, OH,
1998.
[16] Anon. Using Neural Works . A Tutorial for Neural
Works professional II/plus and neural works explorer,
Neuralware Inc, Pittsburgh, PA, 1993.
|