К ВОПРОСУ О ПРИМЕНЕНИИ ПЛАЗМЫ ДЛЯ
ЭФФЕКТИВНОГО СЖИГАНИЯ НИЗКОРЕАКЦИОННЫХ УГЛЕЙ
Петров С.В., докт. техн. наук, Литовкин В.В., канд. техн. Наук
Источник: www.rosteplo.ru/Tech_stat/../383
Описание: проведен анализ работ, связанных с методами сокращения использования газа и мазута на
пылеугольных ТЭС, рассмотрена целесообразность использования плазменных систем воспламенения для сжигания низкреакционных углей.
Ключевые слова: плазма, низкореакционные угли, энергетика, топливообеспечение,
розжиг, подсветка, технология сжигания.
На протяжении многих лет стратегия развития отечественной энергетики
базировалась на увеличении доли газа и мазута в топливном балансе. Такая тенденция во
многом определялась технологическими проблемами горения и ценовой политикой.
Сегодня можно говорить, что она себя исчерпала. Прогноз, сделанный в «Энергетической
стратегии России на период до 2020 года» предусматривает достижение равенства цен на
уголь и газ к 2005 году, а к 2020 году выхода на соотношение цен уголь/газ как 1:2 [1]. В
Украине угольная промышленность является основным поставщиком собственного
топлива. Такая ситуация сохранится и в будущем благодаря большим запасам угля.
Однако, несмотря на декларирование о приоритетности развития угольной отрасли
реальных изменений пока не происходит, действенные меры по повышению
эффективности сжигания традиционных видов топлива, в том числе угля, на базе новых
технологий не принимаются. Все это ведёт к тому, что уровень энергобезопасности
Украины остается слишком низким. Основным фактором, который обусловливает такое
положение, является монопольная зависимость от импорта Российского природного газа и
нефти [2]. Доля топлива в общих расходах на производство энергии на электростанциях
Украины достигла 80,5 %, рентабельность составляет 2,2 %. По оценкам экспертов
ожидается тенденция изменения топливного баланса энергетики в сторону повышения
доли угля при ухудшении его качества с упором на малотоксичные технологии сжигания.
А общий рост потребления тепловой и электрической энергии может привести к еще
большему увеличению расхода твердого топлива.
Обеспечение сгорания углеродсодержащих компонентов каменных углей с малым
выходом летучих-горючих веществ было достигнуто благодаря развитию в угольной
электроэнергетике нескольких направлений: камерные топки с жидким шлакоудалением,
циклонные предтопки с пылевидной подачей топлива, вихревые топки с пережимом.
Испытывались различные схемы топливоподготовки и аэродинамические принципы
смесеобразования пылевоздушных потоков. Однако, внедренные в электроэнергетике
котлы с вихревыми горелками для блоков 150, 200, 300, 800 МВт практически
эксплуатировались с большим механическим недожегом топлива: для АШ составляет 20 – 35%, для тощего угля марки Т — 15 – 18%. При пониженных температурах горячего
воздуха и ведении топочного процесса в диапазоне температур 1850 – 2070 К механический
недожег в золе-уносе может быть и больше [3]. .Значительные топочные потери требовали
определенных усилий для организации экономичной работы топок. При энергии
активации для реакции С + О2 = СО2 у коксов твердого топлива (Т, АШ) равной 140 – 146
МДж/кмоль требовалось компенсировать недостаток тепла при сжигании высокозольных,
низко реакционных углей мазутом или газом. Это продолжалось почти полвека и в
золоотвалы было отправлено десятки миллионов тонн недогоревшего углерода.
С 80-х годов ХХ века начавшийся рост цен углеводородного сырья (нефть, газ)
стимулировал поиск новых путей розжига и поддержания устойчивого горения
энергетических углей. А дефицит растопочного топлива (при низких ценах) потребовал
развития альтернативных технологий растопки и создания нового котельно-топочного
оборудования. В СССР после 1985 г. В области горелочной техники развивались два
направления ступенчатого сжигания с термохимической подготовкой (ТХП) угольной
пыли:
— газовые (мазутные) муфельные горелки, встроенные коаксиально в центральную
втулку вихревой пылеугольной горелки (двухулиточные, улиточно-лопаточные);
— горелки, оснащенные плазмотроном и камерой ТХП [4].
Анализ работ, связанных с методами сокращения использования газа и мазута на
пылеугольных ТЭС показывает, что практика инженерных методов снижения
потребления дорогих импортных энергоносителей не достигла успехов во внедрении
термохимической подготовки топлива прежде всего из-за ошибочно формируемых
технических заданий. Во-первых, подменялась задача инициирования воспламенения
низко реакционного топлива с незначительным выходом горючих-летучих веществ
задачей компенсации недостаточной калорийности топлива, что на современном этапе
развития горелочной техники ступенчатого сжигания невозможно. Последняя задача
тупиковая для пылеугольных котлов с открытыми и полуоткрытыми топочными камерами
и сохраняющимися горелками первоначальной конструкции. Во-вторых, не учитывалось
изменение механизма реакций. Так при термическом разложении топлива,
активированном повышенной температурой, образуются промежуточные соединения,
которые существенно изменяют механизм реакции по сравнению с условиями
воспламенения рециркулирующими газами с температурой 1500–1700 ºС. В [3] приведены
данные, свидетельствующие о том, что уголь в процессе термической подготовки от 600
ºС до 700 ºС имеет в 2 раза более высокую реакционную способность, чем при
одностадийном доведении до температуры воспламенения в 700 ºС. В-третьих, оставались
несогласованным физические параметры пыли (размер частиц, время пребывания,
концентрация в объеме окислителя) с конструктивным исполнением устройств
термохимической подготовки пылевидного угля.
Ожидаемые тенденции в топливообеспечении энергетики, ориентированные на
повышение роли угля на тепловых станциях, и ужесточение экологических требований
обусловливают необходимость существенных изменений в технологической структуре
производства электроэнергии. В первое время несомненный приоритет в использовании
ограниченных инвестиционных ресурсов получат малозатратные и с коротким
инвестиционным циклом проекты. Увеличение доли угля в топливном балансе за счет
замены газа и мазута может произойти на уже существующих энергетических объектах. К
числу наиболее подготовленных технологий с коротким инвестиционным циклом может
быть отнесена система плазменного розжига и подсветки.
Плазменная техника нашла широкое применение в промышленности, но, к сожалению,
обойдена вниманием электроэнергетикой. Сориентировав полвека тому назад процессы
воспламенения угля на мазуте и газе, ТЭК сегодня не восприимчив к практике
применения плазменных процессов для организации топочных процессов в котлах
большой мощности. Тем не менее для повышения эффективности сжигания угля
создаются новые плазменно-топливные системы. Они являются основным элементом при
реализации плазменно-энергетических технологий. Среди них — пылеугольные горелки,
оснащенные электродуговым плазмотроном и комбинированные плазменные
газификаторы для ТЭС. Плазменно-топливные системы обеспечивают безмазутную
растопку пылеугольных котлов, стабилизацию горения факела и, как следствие,
одновременное снижение мехнедожога топлива, образования оксидов азота и сернистых
соединений.
Плазменно-энергетические технологии основаны на плазменной термохимической
подготовке угля к сжиганию. Она состоит в нагревании электродуговой плазмой
воздушно-топливной смеси (аэросмеси) до температуры выделения летучих угля и
частичной газификации углеродного остатка. Вследствие этого, независимо от качества
угля, из воздушно-угольной смеси получается высокореакционное двухкомпонентное
топливо (горючий газ и коксовый остаток). Когда это топливо подается в топку, то при
смешении со вторичным воздухом, оно воспламеняется и устойчиво горит без сжигания
дополнительных топлив (мазута или природного газа), традиционно используемых для
растопки котлов и стабилизации факела низкосортных энергетических углей.
Плазменно-топливные системы испытаны на 26 энергетических котлах
паропроизводительностью от 75 до 670 т/ч и оборудованных различными типами
пылеугольных горелок (прямоточные, муфельные и вихревые горелки) [5]. При
испытании плазменно-топливных систем сжигались угли всех сортов (бурый, каменный,
антрацит и их смеси). Содержание летучих в них составляло от 4 до 50%, содержание
золы - от 15 до 48%, и теплота сгорания была в интервале от 1600 до 6000 ккал/кг.
В результате испытаний доказано, что плазменные технологии безмазутной растопки
котлов и стабилизации факела имеют следующие преимущества перед традиционными
технологиями:
• сокращение расхода мазута и газа на ТЭС;
• энергетическая эффективность плазменно-топливных систем в 3 – 4 раза выше, т. к.
относительная электрическая мощность плазмотронов составляет (в зависимости от
типа угля и горелки) лишь 0,5-2% от тепловой мощности пылеугольной горелки;
• замещение стабилизирующего топлива (мазута или природного газа) углем позволяет
снизить образование оксидов азота на 40 – 50% из-за преобразования топливного азота в
молекулярный азот в обедненных кислородом зонах воспламенения и сжигания,
выделения оксидов серы снижается на 30 – 40% (если углем замещается
высокосернистый мазут), а выбросы пятиокиси ванадия подавляются почти
полностью;
• снижение эмиссии диоксида углерода благодаря повышению эффективности процесса
сжигания на пылеугольных котлах в результате уменьшения мехнедожога топлива;
• возможность растопки энергетических блоков ТЭС при потере собственных паровых
нужд станции;
• использование широкой гаммы энергетических углей, лигнита, горючего сланца,
торфа, биомассы и их смесей при сохранении технических, экономических и
экологических показателей энергетических блоков.
Принципиальная проблема, которая сдерживает промышленную реализацию
плазменно-угольной технологии, заключается в необходимости использования
достаточно мощных плазмотронов (свыше 200 кВт). Мощность плазмотрона определяется
минимальными относительными затратами энергии, равными отношению тепловых
мощностей плазмотрона и пылеугольной горелки, для АШ составляет 1,5 – 2,0 %.
Реальный ресурс непрерывной работы таких плазмотронов в лучшем случае составляет
200 – 300 часов (декларируется больший, но никто его не может продемонстрировать).
Сегодня не видны пути существенного повышения ресурса медных электродов. Другие,
способные реально обеспечить значительно больший ресурс, это:
самовосстанавливающийся из газовой фазы катод, вольфрамовый, расходуемый
графитовый — применительно к энергетике не рассматриваются. Скорость эрозии медных
электродов (катода и анода) определяется многими факторами и особенно величиной тока
дуги. Причем, эрозионные характеристики анода и катода могут как полностью совпадать,
так и обнаруживать значительное расхождение — в зависимости от динамики
приэлектродных процессов. В воздушной среде существует критический режим —
значение тока, при превышении которого эрозия материала резко возрастает. Причиной
появления критического режима является потеря устойчивости вращения потока газа в
полости электрода. Поэтому при создании плазмотрона для энергетики к числу основных
вопросов относится обеспечение неизменности уровня удельной эрозии электродов при
длительной работе в диапазоне докритических токов. Эрозия медного полого катода в
воздушной атмосфере составляет порядка ≈ 2 ⋅10 −9 кг/Кл, средний уровень эрозии анода
ниже и составляет ≈ 410−11 кг/Кл. После 50 часов работы в приповерхностном слое
материала электродов появляются растрескивания по границам зерен. Причем, у катода на
более значительную глубину вдвое по сравнению с анодом. Эрозионная поверхность у
анода меньше окисляется, чем катодная. Эрозия медных электродов в основном
определяется плотностью теплового потока и скоростью перемещения приэлектродных
участков дуги. При обеспечении хорошей стабильности работы электродов сегодня можно
говорить о гарантированном ресурсе в воздушной среде катода 200 часов, анода — 1000
часов при токе 200 А и глубине срабатывания материала 6⋅10 −3 м.
Поэтому реальный путь
использования плазмотронной техники в энергетике — это снижение мощности
плазмотронов на порядок (с 300 до 30 кВт), что даст такое же увеличение ресурса
электродов, т.е. составит тысячи часов. Это главное. В дополнение улучшается экономика,
так как тепло от электричества значительно дороже тепла от угля.
В Институте газа НАН Украины разработан новый подход ТХП пылеугольного
топлива, обеспечивающий как улучшенные технико-экономические показатели
плазменной аппаратуры и процесса, так и получение приемлемого для энергетики ресурса
непрерывной работы плазмотронов [6,7]. Выполнены поисковые работы, конечной целью
которых было снижение необходимой мощности плазмотрона (соответственно
установленной мощности электрооборудования) для устойчивого горения пылеугольной
смеси с обеспечением более, чем 10 кратного умножения тепловой мощности струи. Это
достигается благодаря повышению скорости горения низкореакционных углей за счет
использования технологически значимых плазменных эффектов. Дальнейшим развитием
данного подхода является проведение в плазменно-струйном реакторе
высокотемпературной паровой конверсии с получением синтез-газа и высокореакционных
частиц несгоревшего топлива. Исследования проведены на разработанных
комбинированных плазменно-угольных горелочных устройствах для установки на
прямоточные пылеугольные горелки (Рис.1).
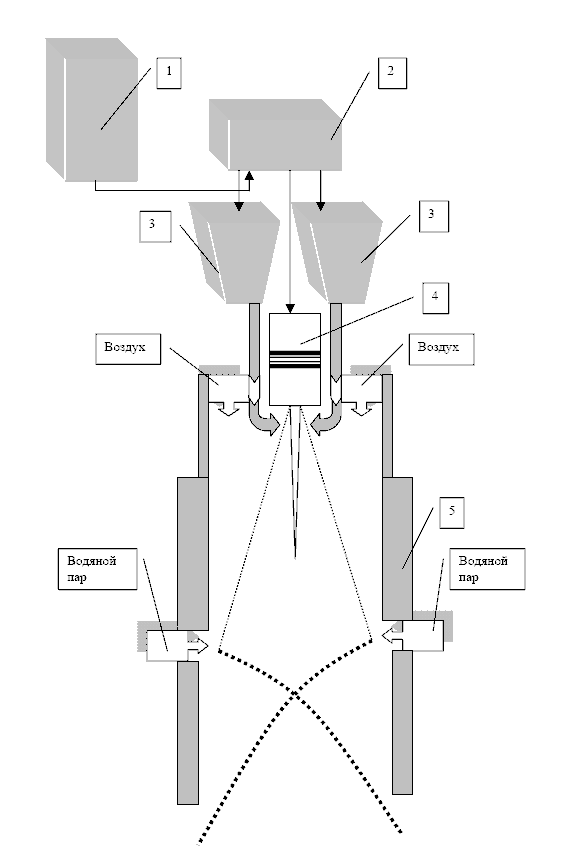
Рисунок 1 — Плазменно-угольное горелочное устройство
1 — источник электропитания, 2 — пульт управления, 3 — питатель-дозатор угольной пыли, 4 — плазмотрон, 5 — муфель
Оценки показывают, что встроенные плазмохимические реакторы в горелки
мощностью 50 ÷ 100 МВт (Рис.2) позволяют применить плазмопиролиз в присутствии
воды или пара (Н2О) и при неполной газификации получить 1,5 ÷ 1,8 нм3/кг синтез-газа с
содержанием СО + Н2 до 95 ÷ 98% при соотношении СО/Н2 как 1/1. Котельная подсветка
плазменным синтез-газом в размере 3000 нм3 эквивалентна расходу электроэнергии до
1,2·103 кВт·ч. Это как раз те летучие-горючие вещества, которые необходимы для
сжигания низкореакционного АШ в указанных горелках.
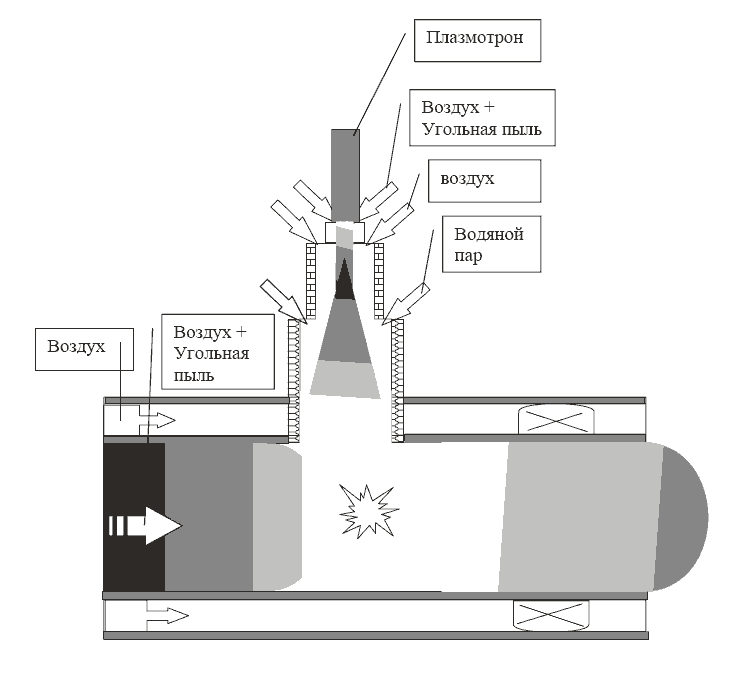
Рисунок 2 — Плазмохимический реактор с прямоточной пылеугольной горелкой
Принципы проектирования плазменно-угольных систем для их последующего
промышленного использования сформулированы в результате расчетов и сопоставления с
экспериментальными данными [8,9]. Математическое моделирование процесса
плазменной переработки угля позволяет не только проверить воздействие отдельных
параметров плазмохимического реактораа форму и характеристики факела, но также
рассчитать влияние различных характеристик топлива на характер воспламенения и
стабильность факела. В экспериментах в качестве топлива использовалась угольная пыль
Донецкого антрацита марки АШ фракцией до 250 мкм. Тепловая мощность плазменной
струи регулировалась в пределах 5 – 50 квт. Угольная пыль, транспортируемая воздухом,
подавалась с одного, двух и трех питателей в воздушную плазменную струю плазменно-
горелочного устройства. Расход угольной пыли через один питатель дозатор составлял 1 –
15 г/сек. Исследовано влияние следующих факторов на повышение скорости окисления
угля:
1) Длина начального участка плазменной струи — изменялась в пределах 3 – 7
калибра при одинаковых среднемассовых параметрах на срезе сопла плазмотрона;
2)
Высокочастотная пульсационная составляющая тока дуги плазмотрона с амплитудой (0,1
– 0,5) Iн;
3) Акустические воздействия;
4) Электрический потенциал плазменно-угольного
факела.
Оценка скорости окисления угольных частиц проводилась по их недожегу на
выходе плазменно-горелочного устройства, Проводилось полное калориметрирование
факела, определялись количество, фракционный состав, зольность угольной пыли на
входе и выходе плазменного горелочного устройства. Также измерялись температура и
скорость частиц, покидающих горелку. Доказано, что с помощью указанных выше
внешних маломощных физических воздействий на высокотемпературную зону горения
угольной пыли можно в 3 – 5 раз увеличить скорость реакций их окисления. При этом резко
повышается количество выгоревшего угля и мощность факела. Практически на такую же
величину можно снизить необходимую тепловую мощность плазмотрона. При работе на
пониженной мощности плазмотрона снятие (например) потенциала с запыленной струи
приводит к затуханию пылеугольного факела и при продувании пыли через раскаленный
муфель.
Умножение мощности пылеугольного факела и плазменная стабилизация горения
несгораемой в данных условиях низкореакционной угольной пыли демонстрируется на
рис.3.
Из экспериментальных исследований (Рис.3) и расчетов (Рис.4) можно сделать
вывод, что факт более чем десятикратного умножения мощности доказан. Кроме того, при
поперечном вдуве пылеугольного факела, инициированного в плазменноугольном
реакторе (Рис.2) в основной поток поджигаемой угольной пыли его эффективность будет
заметно (в несколько раз) выше, чем у плазменной струи той же тепловой мощности.
Поскольку объем и дальнобойность у пылеугольного факела значительно больше,
поэтому соответственно большим у него будет и объем области взаимодействия с
поджигаемой пылью. Кроме того, в факеле содержится достаточно большое количество
нагретых до высокой температуры коксовых частиц крупных фракций. Глубоко проникая
в сносящий поток, эти частицы воспламенятся при контакте с находящимся в нем
кислородом, увеличивая тем самым поджигающий и стабилизирующий горение эффект
факела.
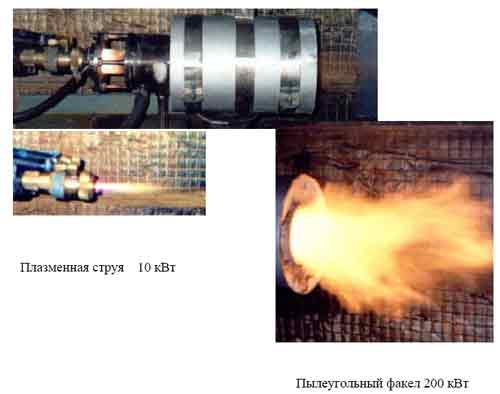
Рисунок 3 — Умножение мощности в плазменноугольном реакторе
Накопленный опыт использования плазменно угольных технологий и выполненные
новые исследования свидетельствуют о том, что какие либо физические запреты или
непреодолимые технические ограничения для промышленной реализации данной
технологии отсутствуют, а польза и преимущества доказаны.
В частности, кроме оговоренного выше, целесообразно отметить следующее. В
стремительно развивающейся Европейской интеграции и стоящего на повестке дня
порядка выполнения ратифицированного Киотского протокола энергокомпании
столкнутся с фактом платежей до 100 Евро/т твердых выбросов. Плазменная технология
приближает качество золы ТЭС к Евро стандарту EN450 (С ≤ 6%), а ТЭС к порогу
максимальной коммерческой выгоды от продажи минеральных отходов промышленности.
Известны оценки плазмохимически обработанного угольного сырья как полупродукта
получения цемента — 40дол/т, цемент из энергетического сырья — 70 дол/т. Во многих
странах ЕС промышленные комплексы создаются по каскадному проекту, где отходы,
образующиеся на одном предприятии, служат сырьем для другого.
Желающие освоить плазменные технологии необоснованно пугаются стартовых
капиталовложений в плазменное электротехническое оборудование. Но без инвестиций в такое
оборудование, которое является основным средством производства с длительным сроком
безремонтной эксплуатации, нельзя приступить к отработке оптимальных схем
плазмохимической обработки, тем более, что приобретаемая техника выполнит как
эксплуатационные, так и ремонтные задачи. При незначительном дооснащении
плазменной установки она может использоваться в ремонте для плазменной резки и
напыления защитных покрытий.
Никто не обсуждает отношение стоимости блочного трансформатора к стоимости
блока, без которого оборудование стоимостью в 150 млн. долларов просто склад техники,
а стоимость плазменного технологического комплекса окупается за счет ценовой разницы
производства электроэнергии на газе и на угле, а это для 1 МВт·ч не менее 8 долларов. В
зависимости от используемых углей срок возврата инвестиций на реализацию системы
плазменного розжига и подсветки топлива может находиться в пределах от нескольких
месяцев до нескольких лет.
Список литературы
1. Чурашев В.Н., Чернова Г.В. Региональные особенности топливообеспечения
енергетики России // сб. Докл. Конференции „Модернизация электростанций,
использующих низкореакционные угли в странах СНГ”, Москва, Россия, 21 – 22
апреля 2004. — с. 1 – 13.
2. Куцан Ю.Г., Білодід В.Д. Щодо проєкту концепції енергетичної політики України
на період до 2003 року. Энергетики и электрификация. 2001.№3. — с. 2 – 11.
3. Литовкин В.В. О неиспользованных резервах повышения эффективности сжиганиянизкореакционных топлив в пылеугольных котлах.//Енергетика и электрификация,
№5, 1995г. —с.1–3.
4. Жуков М.Ф., Карпенко Е.И., Перегудов И.С. Плазменная безмазутная растопка котлов и стабилизация горения пылеугольного факела. Новосибирск: Наука, 1996. —
304 с.
5. Мессерле В., Сакипов З., Ибраев Ш. Электротермохимическая подготовка угля к
сжиганию. — Алматы: Наука. — 1993. — 259с.
6. Петров С.В., Сааков А.Г. Плазма продуктов сгорания в инженерии поверхности.
ТОПАС, Киев: 2000. — 218 с.
7. Петров С.В. Плазменная обработка низкореакционных углей// Вісник
східноукраїнського національного університету імені Володимира Даля, №11 [63],
2003.— с.71 — 80.
8. Петров С.В., Сааков А.Г., Котляров О.Л., Яценко В.П. К проблеме снижения
энергозатрат на плазменный розжиг и стабилизацию горения пылеугольного
факела// Технічна електродинаміка, 2004, №3, с. 84 – 87.
9. Petrov S.V., Saakov A.G. Plasma — catalyst of combustion of low-reactive coals// 16th
International Symposium on Plasma Chemistry. Taormina — Italy. June 21 – 27, 2003. P.
346 – 356. |