Structural failures of rope-based systems
G. Piskoty, M. Zgraggen, B. Weisse, Ch. Affolter, G. Terrasi
Empa, Swiss Federal Laboratories for Materials Testing and Research, Ueberlandstrasse 129, CH-8600 Duebendorf, Switzerland
Source: Elsevier Science. Engineering Failure Analysis 16 (2009) 1929–1939
Abstract
The aim of this paper was to emphasise the importance of making a broad collection of hypotheses at the beginning of failure investigations as a precondition for efficiency and correct conclusions. For this purpose, two case studies of structural failures are presented, where the failed load carrying structure was based on wire ropes (steel cables) and the incidents occurred despite safety precautions. The investigations are not dealt with in depth – they are merely summaries intended to highlight the failure hypotheses and the procedure in finding the failure causes.
Some generalised conclusions are formulated at the end of each case study. In this way,
the knowledge and experience derived from a failure analysis can be archived in memory and called upon during future investigations – regardless of whether or not a wire rope is present in the failed system.
1. Introduction
When starting a failure analysis it is common practice to compile a catalogue of failure hypotheses and to plan the investigations based on it. The precondition for the success of this approach is that the catalogue of failure hypotheses includes the real failure cause. Otherwise, there is a large likelihood of misinterpretation of the results and delivering incorrect conclusions. Therefore, the goal of the present paper is to emphasise the importance for a broad spectrum of hypotheses and to derive some general ideas for completing hypothesis-catalogues, based on two case studies of structural failures. In all cases the failed load-bearing structure was based on wire ropes and that the incident occurred despite safety precautions.
A brief introduction to rope-based structures is appropriate before the case studies are presented. Ropes are used especially in such structures where high load capacity combined with flexibility of the load carrying element and an inherent redundancy (damage tolerance) are required, such as in ropeways. The reason for these special characteristics is that ropes are made of many single woven wires.
In rope-based systems, the structure and the functional part of the system are often combined. For example, the hauling rope of a chairlift represents the main part of the load carrying structure and also acts as the load transmission element for moving the hangers.
2. Rupture of a rope due to local fatigue
2.1. Introduction
There grips of monocable ropeways [1] can be detachable or fixed. In the first case, the hangers (e.g. chairs, cabins or T-bars) are separated from the rope during the station transit. This allows the passengers to board comfortably at reduced. speed of the hangers. As a positive side-effect, the fatigue of the rope is homogenous, because the location of grips on the rope changes continuously and randomly during operation.
The following accident occurred on a ropeway with fixed grips. In this kind of ropeway, the carriers remain permanently attached to the rope during operation. Therefore, always the same rope segments experience the additional bending and pressure stresses at the grips. In order to avoid an accelerated localised fatigue of the rope, all of the grips have to be relocated by a given distance (approximately 0.5 m) at regular intervals; typically twice a year.
2.2. Accident
During regular operation of the ropeway the hauling rope ruptured close to a grip.
2.3. Investigations
The visual investigation of the rope revealed typical characteristics of fatigue fracture. Many broken wires were found also in the region of almost all the other grips. It seemed obvious that the prescribed relocations of the grips had been neglected. However, the maintenance records showed that the grips were relocated at the specified time intervals and distances in accordance to the manual. The fatigue rupture of the rope was a mystery.
In order to collect some clues, the employees who had relocated the grips were interviewed. It turned out that the grips were relocated by two alternating teams: one team had relocated the grips in the direction of travel, while the other team relocated them in the opposite direction. As a result, the grips alternated between the same two positions (Fig. 1).
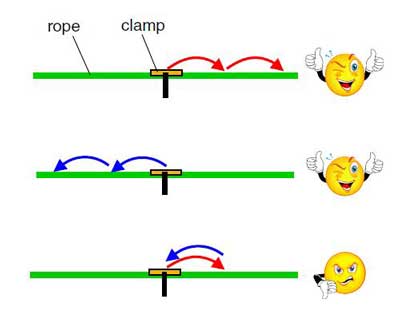
Fig. 1. Possible relocation directions of the grips (the lower region of the hangers is not depicted).
Obviously, the manufacturer did not see the necessity to prescribe a direction for the grip-relocation in the manual, as both possible directions were equivalent.
2.4. Generalized conclusion
3. Rope-detachment from an anchor drum
3.1. Introduction
Anchor drums represent a well-established method for anchoring wire ropes. By this kind of anchorage, the final sequence of the rope is wrapped around a fixed drum with a soft surface, e.g. wood (Fig. 2). The main part of the service load is transmitted between the rope and the drum by friction. Behind the drum, only the small residual force has to be absorbed, using a clamp. The residual force is given by the following equation:
|
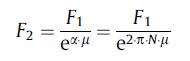 |
(1) |
α: Enlacement angle of the rope around the drum, μ: friction coefficient between the rope and the drum’s surface, N: number of windings.
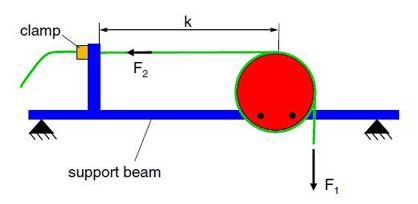
Fig. 2. Construction of the anchor drum.
For example, if the friction coefficient is 0.2 and the rope is wrapped around the drum four times, the residual force amounts to only 1% of the service load (F2 ≈ F1 / 100). In general, the clamp has to be designed just for a small fraction of the service force in the rope, allowing a smooth clamping, without excessive local pressure on the rope’s surface. This advantage becomes especially important for applications where the rope has to be shifted periodically as in the final case study in
this paper.
3.2. Accident
During regular operation of a ropeway, the end of a hauling rope holding the cabin in position slipped off the clamp of the anchor drum. The rope detached from the cabin and the cabin became free. Fortunately, a safety equipment (track rope break [1]) prevented the crash of the cabin.
3.3. Investigations
The visual inspection of the anchor revealed no apparent anomalies. As an excessive overload during operation could be
excluded, an insufficient load capacity of the anchorage was assumed. This obvious hypothesis had to be proved with a load test. Since the rate of change of the service load in the rope was low, a quasi-static test set-up was built. During the test, the force in the anchored rope was increased gradually up to the triple of the highest service load. However, the clamp did not fail. The hypothesis of insufficient load capacity of the anchor had to be rejected.
At a loss to explain the failure and test result, the disassembly of the test set-up was started. At first, the load in the rope was removed. In doing so, a small amount of slippage was observed between the clamp and the rope. By repeating the loading and unloading cycle, the rope slipped incrementally through the clamp, even when the fluctuating tensile force in the rope remained considerably below the regular operational force. Strangely enough, the slippage took place not during the increase but during the reduction of the load.
The unexpected system behaviour could be explained after a detailed analysis of the process. The service load fluctuated slowly in accordance with the load status, position or acceleration of the cabin etc. within a regular range. If the tensile load increased, the elastic deflection of the support beam became larger. As a consequence, the distance between the drum and the rope clamp decreased (F1 ↑ → k ↓, Fig. 3). Due to the reduced distance, the residual force collapsed (k↓ → F2↓), and therefore the relationship (1) was no longer satisfied. In order to restore the required equilibrium between the forces on the both side of the drum, the rope crept around the drum in a clockwise direction until the residual force increased to the required value again.
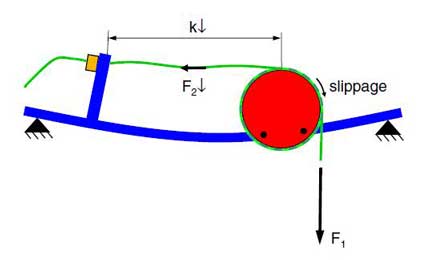
Fig. 3. Disturbed force equilibrium in the rope on both sides of the drum during increased service load (the elastic deformation of the support beam is exaggerated).
When the operational load decreased, the support beam started to flex back into its original position. Therefore, the distance between the drum and the clamp got larger (F1 ↓ → k ↑). Because of the missing rope length between the drum and the clamp, the load started to increase in that rope section. There was no possibility for pulling back the rope over the drum, as it would have required a force several times higher than the current service load (interchanged indices ‘‘1” and ‘‘2” in Eq. (1)). Obviously, the yielding took place at the clamp which was designed just for a small fraction of the service load. During the operation of the ropeway this asymmetric procedure was repeated periodically, until the rope had slid out of the clamp.
3.4. Generalized conclusions
Structures should be analysed also under consideration of fluctuating service loads, even if classical dynamic failure causes – such as vibrations, fatigue or wear – can be excluded.
A failure can be caused by hidden coupling effects in a system.
A simple elastic structure can react to a variable load with asymmetric behaviour. This can lead to the accumulation of small negative effects and finally cause failure.
4. Summary
The generalised conclusions given in this paper represent only some possible examples of how the knowledge of a particular failure analysis can be generalised and collected in order to support future investigations. In this way, the experience made by a failure analysis can be strengthened in one’s memory. Furthermore, it becomes more recallable and applicable for different kinds of failed systems. As a result, the efficiency of the failure analysis procedure increases and the likelihood of incorrect conclusions decreases.
Acknowledgements
The second failure was originally investigated under the leadership of Prof. Dr. G. Oplatka, retired head of the Institute of Ropeway Technology at the Swiss Federal Institute of Technology Zurich (ETH-Z). The authors thank him for providing the background information for this paper.
Literature
- Wallis-Tayler AJ. Aerial or wire rope-ways: their construction and management. Kessinger Publishing, LLC; 2007.
- Eidgenössisches Verkehrs, Energiewirtschaftsdepartement. Pendelbanhnverordnung. Bern: Eidgenössische Drucksachen – und Materialzentrale; 1988.
- Kuron D. Wasserstoff und Korrosion. Kuron Verlag; 2000.
- Lange G. Systematische Beurteilung technischer Schadensfälle. DGM-Verlag; 1993. p. 235 ff.
- Ashby MF, Jones DRH. Eng Mater 1. 3rd ed. Elsevier; 2005.
|