Перспектива истощения природных запасов нефти и газа и связанное с этим увеличение потребления угля обусловило повышенный интерес ученых мира к угольным технологиям. Особое внимание сегодня уделяется изучению специальных процессов обогащения угля, которые открывают новые возможности по переработке низкосортного сырья в кондиционные экологически чистые продукты. [1]
Ежегодно на обогатительных фабриках перерабатывается около 76,2 млн.т. угля (зольностью 38,5 %), выпускается 46,6 млн.т. товарных продуктов (зольностью 15,3 %) и 29,6 млн.т. отходов (зольностью не белее 75 %). Это говорит о том, что в отходах теряется около 1200 тыс.т. угольных фракций в год из-за несовершенного технологического процесса и режимов обогащения. [2]
В настоящее время проблемы экономии топлива и повышение его качества должны решаться в комплексе. Наша страна испытывает острую нехватку качественных коксующихся углей, которые играют немаловажную роль в производстве чугуна, стали, проката. В связи с этим обогатители постоянно и непрерывно ведут поиск рациональных технологий и источников обогащения.
Актуальность темы
Прогнозируемое повышение роли угля в энергетике обусловлено истощением месторождений нефти и газа. Однако вследствие ухудшения горно-геологических условий и несовершенством средств механизации угледобывающих производств ухудшается качественная характеристика углей по зольности, гранулометрическому составу, влажности и сернистости, следовательно, практически весь добываемый уголь требуется подвергать обогащению. В связи с этим быстрыми темпами увеличивается количество отходов на ОФ — шламовых вод, угольных шламов в гидроотвалах, терриконах, илонакопителях.
Недостаток ресурсов теплоносителей в Украине требует изыскания дополнительных источников топлива за счет вовлечения в топливный баланс страны забалансовых шламов и продуктов накопителей, образовавшихся в процессе эксплуатации фабрик. По данным института УкрНИИуглеобогащение на фабриках Минуглепрома Украины хранится в отстойниках и илонакопителях 115 880 тыс. т шламовых продуктов различной зольности. [4]
Поэтому наибольший интерес на сегодня для обогатителей представляет использование вторичного сырья. Помимо того, что эти объекты занимают значительные земельные площади, они еще являются и техногенными источниками энергетического и коксового сырья.
Мелкие классы каменных углей и их шлам накапливаются сегодня в илонакопителях обогатительных фабрик, и дальнейшая их переработка, подготовка к использованию сегодня представляет собой серьезную проблему. Большое количество шламов вместе с водой попадает в водные объекты и загрязняет их. Использование мелких классов углей и шлама после сложного процесса их сушки, в топках и печах малоэффективно из-за значительных расходов этих продуктов в виде просыпей под колосники. Кроме того, мелкие классы при сжигании попадают в воздух и загрязняют атмосферу. Таким образом, весьма актуальным заданием является разработка прогрессивной технологии переработки каменноугольных шламов и мелкого каменного угля для дальнейшего эффективного их использования, а также снижения загрязнения водных объектов и атмосферы. [3]
Зольность горной массы, находящейся в илонакопителе Ясиновского КХЗ, колеблется в пределах 30 — 70 %, а содержание органической массы составляет 30-50 %. Поэтому можно считать, что в силу относительно низкой зольности флотационных отходов, этот илонакопитель является техногенным источником сырья, из которого можно получить не только энергетическое топливо, но и концентрат для коксования.
Качественные показатели шламов колеблется в широких пределах по глубине и площади распределения, что затрудняет их переработку. Поэтому исследование физико-химических свойств твердой массы этого объекта, методов их обогащения и разработка технологии также является актуальной задачей.
Научная значимость работы
Напряженный топливный баланс в Украине и неблагоприятная экологическая обстановка в Донбассе требует разработки эффективных способов использования в топливном комплексе предприятий страны тонкозернистых высокобаластных углесодержащих продуктов из отстойников шахт и илонакопителей, которые занимают значительные земельные площади и ухудшают санитарное состояние воды и атмосферы. [5] В этой связи поиск способов вовлечения в топливный баланс углесодержащих отходов просто необходим.
В данной работе разработана технологическая схема получения из угольных шламов илонакопителя Ясиновского КХЗ концентрата, пригодного для целей коксования.
Наличие шламов, а также их различие по зольности является результатом несовершенства существующей технологии обогащения угля. Поскольку шламы представляют собой углеродносиликатную массу, физическая сущность метода переработки шламов заключается в разделении их на составляющие: углерод–силикаты, что в полной мере до недавнего времени при существующей технологии не представлялось возможным выполнять достаточно эффективно.[4]
Изучение теоретических аспектов и практики применения традиционных, специальных и новых методов обогащения позволило выделить процесс масляной агрегации среди большинства.
Дело в том, что особенностью складированных в инакопителях отходов флотации является большое содержание ультратонких угольных фракций, неэффективно извлекаемых флотационным методом. В то время как процессы масляной агрегации (агломерация, грануляция) обладают возможностью извлекать широкий класс крупности угольных частиц из высокозольного шлама и способны обеспечить их эффективное обезвоживание на простых аппаратах.[1]
В результате проведенных опытов, получены данные, которые позволили разработать математическую модель процесса обогащения угольных шламов методом масляной агломерации. Базируясь на выявленных закономерностях и установленных зависимостях физико-химических процессов масляной агломерации, проанализированы каналы управления схемы в условиях Ясиновского КХЗ.
Практическая ценность результатов
Разработана технологическая схема обогащения флотационных отходов, складированных в илонакопителе Ясиновского КХЗ, которая позволит улучшить качество конечного продукта, расширить сырьевую базу предприятия, а также позволит эффективно организовать безотходное производство металлургической продукции и значительно укрепит ее позиции на отечественном рынке.
Обзор исследований по теме в ДонНТУ
На базе ДонНТУ были проведены исследования процессов масляной агломерации энергетического угля (СМА-ТЕС), создано ряд перспективных решений по применению масляной агломерации для нужд магистральных гидротранспортных систем (СМАГ-ГТ) и усовершенствован процесс СМА «уголь-золото».
В основу технологии «МГ-ТЕС» был положен «амальгамный» механизм процесса масляной агломерации с учетом режимных параметров. Процесс агломерации осуществляется в специальном аппарате, куда подается подогретая вода, измельченный уголь и кальцинированная сода из расчета 0,01–0,05 мас.%. Аппарат агломерации состоит из двух последовательно расположенных сосудов: в 1-м реализуется этап «амальгамирования», 2-й предназначен для структурообразования и обкатывания гранул. Связующее (мазут при tм = 80 0С) подается на всас насоса, который способствует распределению его по всему объему пульпы. Обезвоживание агломерата осуществляется на стационарном щелевидном сите, оснащенном брызгалами.
Испытание пилотной установки в разных режимах позволили разработать рациональную режимную карту процесса. В результате проведенных опытов были получены следующие результаты: влажность — 14-18 %, средняя крупность гранул — 1,5 мм. После дренирования влажность конечно продукта снизилась до 9-10 %.
Таким образом, результаты исследований, проведенных ДонНТУ подтверждают теоретические выкладки и свидетельствуют о том, что:
- Качественные показатели продуктов агломерации практически не зависят от зольности исходного угля;
- Расходы мазута на единицу массы исходного угля снижаются при увеличении его зольности;
- Зольность отходов процесса СМА значительно превышает уровень при обогащении традиционными методами углей тонких классов, что позволяет использовать их в промышленности строительных материалов;
- Гранулированный концентрат хорошо обезвоживается на стационарном сите, что исключает необходимость применения центрифуг и термической сушки;
- Аппараты агломерации конструктивно просты и могут быть использованы на базе серийно выпускаемых флотационных машин;
- Включение процесса СМА в пылеприготовительный цикл ТЭС открывает перспективу перехода от сухого измельчения угля на более производительное — мокрое и снижает взрыво- и пожароопасность цеха измельчения на ТЭС.[1]
Группой научных работников ДонНТУ и Научно- производственного объединения «Гаймек» было исследовано шесть основных технологических вариантов «гидротранспорт-агломерация» угля:
- Перемешивание угля на главном терминале гидротранспортной системы (МГТС) в гранулы 1 типа (пленочные) — трубопроводний транспорт гранулята в потоке воды — обезвоживание и обесзолевание в осадительных центрифугах конечного терминала;
- Перемешивание угля на главном терминале в гранулы 2 типа (менисковый) — гидравлический транспорт гранулята — обезвоживание и обесзолевание в фильтрующих центрифугах конечного терминала;
- Перемешивание на главном терминале части угля в гранулы 2 типа — транспортировка по трубам смеси «уголь-гранулят» — обезвоживание в фильтрующих или осадительных центрифугах конечного терминала;
- Перемешивание угля в гранулы 1 типа непосредственно в трубопроводе с последующим обезвоживанием и обесзоливанием гранулята на осадительных центрифугах;
- Обезвоживание транспортируемого МГТС угля на конечном терминале в центрифугах с последующим перемешиванием угля из фугата центрифуг в гранулы 1 типа — обезвоживание и обесзоливание гранулята на осадительных центрифугах;
- Гидротранспортирование угля — обезвоживание центрифугированием на конечном терминале с последующим перемешиванием угля из фугата центрифуг в гранулы 2 типа — обезвоживание и обесзоливание гранул на ситах и в смеси с углем на центрифугах.
Исследования проводили на энергетическом и коксовом угле при добавлении мазута М100 и М40. Анализ и обобщение результатов позволили сделать вывод о бессомнительном преимуществе технологии «гидротранспорт-агломерация».
Положительные результаты экспериментов дают основания полагать, что комбинирование гидравлического транспортаугля с процессом его масляной агломерации обеспечивает возможность создания МГТС нового поколения, способных транспортировать каменные и бурые угли разных марок и модификаций без существенных изменений их физико-химических характеристик с соблюдением требований экологической чистоты.[1]
Существующие технологии процессов СМА «уголь-золото» обеспечивают извлечение золота крупностью 5-500 мкм на уровне 79-99 %. Исследования ДонНТУ и Института биоколлоидной химии НАН Украины показали, что этот процесс возможно усовершенствовать за счет модификации поверхности углемасляных гранул специальными веществами и таким образом расширить область применения процесса, обеспечив извлечение зерен крупностью менее 5 мкм. В результате рационального подбора компонент гранул и их модификации можно существенно улучшить эффективность адгезионного обогащения золота.
Обзор исследований по теме в Украине
Кроме вышеуказанных исследований в Украине были проведены эксперименты по селективной масляной агрегации высокозольных углесодержащих продуктов ОФ. Этот метод был назван «ОВЗУМС». Этот процесс рекомендуется использовать для переработки энергетических углей с глубиной обогащения выше 1-3 мм.
Характерной особенностью процесса является интенсивное и недлительное перемешивание углевмещающей суспензии со связующим при небольших его расходах. В результате такой обработки возникают микрофлокулы, а гидрофильные частицы породы остаются в воде. Для выделения сфлокулированного концентрата используется осадительная центрифуга либо флотационная машина. Как связующее могут использоваться каменноугольные смолы. Наибольшую эффективность имеют масло для омасления шихты (МОШ), впитывающее масло, полимеры бензольного отделения коксохимпроизводства.
Первый вариант этого процесса был реализован на углеобогатительной фабрике Авдеевского КХЗ. Установка для реализации процесса создана на базе флотационной машины МФУ-50. Первая камера была переоборудована как турбулизатор, на валу которого установлено две мешалки: верхняя четырехлопасная, крестовидная, нижняя — стандартный импеллер флотомашины. Аэрационная труба со статором, пеносъем были демонтированы.
Исходный продукт подавали с помощью насоса, подключенного к хвостовому карману соседней флотомашины. Связующее подавали дозировочным шестеренным насосом. Для создания требуемого рН среды подается водный раствор NaOH. Продукт перемешивания из турбулизатора самотеком переходил во вторую камеру флотационной машины. Эта камера (камера разделения) была оборудована стандартным блок-импеллером с уменьшенной в два раза скоростью вращения. Для снижения интенсивности турбулентных потоков в этой камере над статором была установлена «успокоительная» решетка.
Концентрат масляной селекции обезвоживали вместе с флотоконцентратом на барабанных фильтрах и присаживали к шихте, которая шла на коксование.
В случае необходимости перечистки основного концентрата ОВЗУМС использовали метод масляной грануляции. Смесь всплывшего продукта и высоковязкого связующего поступала в гранулятор с приводом, где при высоких скоростях происходит вторичное обогащение и образование низкозольных углесвязующих гранул.
Второй вариант этого процесса был реализован на ЦОФ «Россия» в 1984-86 гг. Переработке подлежал высокозольный шлам энергетического угля. В лабораторных экспериментах уголь класса 1-13 мм отделяли от общего сырья, поступающего в аппарат ОВЗУМС. Крупные зерна использовались в качестве зародышеобразователей (активных центров) углемасляных флокул концентрата, способствующих его лучшему разделению от минеральной компоненты при центрифугировании.
Установка ОВЗУМС состояла из трех аппаратов масляной сепарации, которые представляют собой цилиндроконические емкости. В середине эти емкости оборудованы консольным валом, закрепленным в обойме подшипниками. Обойма крепится к крышке бака. На валу расположено три импеллера турбинного типа с уменьшающимся по высоте вала диаметром. Аппараты масляной селекции устанавливаются последовательно с небольшим перепадом высот, что обеспечивает транспортировку пульпы самотеком.
Обзор исследований по теме в мире
Опыт работы многих как отечественных, так и зарубежных фабрик показывает эффективность процессов масляной агломерации при обогащении ультратонкого угля. Поскольку опыт зарубежных обогатительных предприятий намного больше, то целесообразнее отобразить результаты мировых исследований в виде таблицы 1.
Наименование метода | Страна, вид установки, произв-ть | Этапы процесса | Реагент, расход, % | Хар-ка исходного материала | Кач-во конечного продукта |
«Трент-процесс» | США, промышленная, 20 т/ч |
Смешивание, грохочение | Печное масло, нефть, бензол, 25-35 | dи = 0-100 мкм, Аи = 10-35% |
dг = 3-6 мм, Ак = 4-26 %, Wг = 10-20 % |
«Конвертоль» | ФРГ, полупромышленная, 5 т/ч |
Смешивание, центрифугирование | Тяжелый мазут, 10-15 | dи = 0-1 мм, Аи = 15-20% |
Ак = 2-9,5 %, Wг = 10-15,5 % |
«Олифлок» | ФРГ, промышленная, 30 т/ч |
1 вариант — Смешивание, грохочение, центрифугирование | Легкие фракции мазута, 10-18 | dи = 0-1 мм | dг = 0,5 мм, Wг = 15-20 % |
2 вариант — Смешивание, центрифугирование, грохочение, флотация | Легкие фракции мазута, 10-18 | dи = 0-1 мм, Аи = 33 % |
dг = 0,5 мм, Ак = 8-9 %, Wг = 15 % |
||
Польша, опытная | 3 вариант — Смешивание, грохочение | Дизельное масло, 16 | dи = 0-0,05 мм, Аи = 10-21% |
dг = 1 мм, Ак = 6-9 %, Wг = 15-20 % |
|
Масляная агломерация (CFRI) | Индия, опытная | Кондиционирование, смешивание, грохочение, окомкование | Легкое масло, 6-12 | dи = 0-100 мкм, Аи = 12-40 % |
Ак = 5-21 % |
США, промышленная, 250 кг/ч |
Смешивание, грохочение (+центрифугирование), сушка | Легк масло, 0,5-3, Тяжелое, 8-12 | dи = 0-0,1 мм, Аи = 17-40 % |
dг = 2 мм, Ак = 10-21 %, Wг = 7 % |
|
Индия, полупромышленная, 2 т/ч |
Кондиционирование, смешивание, грохочение, окомкование | Легкое масло,1-2, Тяжелое, 10-18 | dи = 0-0,5 мм, Аи = 17-41% |
dг = 2-8 мм, Ак = 9-22 %, Wг = 10 % |
|
Сферическая агломерация (NRCC) | Канада, опытная, 5 кг/ч |
Кондиционирование, смешивание, грохочение, гранулирование | Дизельное топливо, 5, Мазут, 20-70 | dи = 0-0,015 мм, Аи = 15-20% |
dг = 6-10 мм, Ак = 5-8 %, Wг = 5 % |
Селективная агломерация (ВНР) | Австралия, полупромышленная, 5 т/ч |
Смешивание, грохочение | Легкое масло, 8 - 14 | dи = 0-0,1 мм | dг = 2-5 мм, Ак = 7-9 %, Wг = 12 % |
«IPTACCS» | Австралия, полупромышленная, 30-50 т/ч |
Смешивание, гидротранспорт, грохочение | Продукты коксования, 10-15 | dи = 0-0,5 мм, Аи = 23-26 % |
dг = 1 мм, Ак = 10-13 % |
Аи — зольность исходного, Ак — зольность концентрата, dг — крупность гранул,dи - крупность исходного, Wг — влажность гранулированного концентрата |
Содержание работы
Результаты исследований свойств отходов флотации, складированных в илонакопителе ЯКХЗ, позволили составить гранулометрический и фракционный анализ объединенной технологической пробы массой 100 кг. В табл. 2 — 3 приведен гранулометрический и фракционный состав объединенной пробы отходов флотации.
Класс крупности, мм | Выход, % | Зольность, % | Содержание серы, % | Суммарный выход надрешетного продукта | Суммарный выход подрешетного продукта | ||||
Выход, % | Зольность, % | Содержание серы, % | Выход, % | Зольность, % | Содержание серы, % | ||||
> 1,0 | 1,19 | 5,18 | 1,35 | 1,19 | 5,18 | 1,35 | 100,00 | 42,25 | 1,51 |
0,5-1,0 | 6,19 | 10,27 | 1,32 | 7,37 | 9,45 | 1,32 | 98,81 | 42,69 | 1,51 |
0,3-0,5 | 9,19 | 15,23 | 1,40 | 16,56 | 12,66 | 1,37 | 92,63 | 44,85 | 1,52 |
0,1-0,3 | 26,07 | 27,14 | 1,45 | 42,64 | 21,51 | 1,42 | 83,44 | 48,12 | 1,54 |
0,044-0,1 | 25,71 | 48,50 | 1,45 | 68,34 | 31,67 | 1,43 | 57,36 | 57,65 | 1,58 |
0,0-0,044 | 31,66 | 65,09 | 1,68 | 100,00 | 42,25 | 1,51 | 31,66 | 65,09 | 1,68 |
Итого | 100,00 | 42,25 | 1,51 | - | - | - | - | - | - |
Плотность разделения, кг/м3 | Выход, % | Зольность, % | Содержание серы, % | Суммарный выход надрешетного продукта | Суммарный выход подрешетного продукта | ||||
Выход, % | Зольность, % | Содержание серы, % | Выход, % | Зольность, % | Содержание серы, % | ||||
<1500 | 73,60 | 5,34 | 1,57 | 73,60 | 5,34 | 1,57 | 100,00 | 21,44 | 1,60 |
1500-1600 | 2,30 | 26,36 | 1,57 | 75,90 | 5,98 | 1,57 | 26,40 | 66,33 | 1,69 |
1600-1800 | 4,80 | 46,17 | 1,68 | 80,70 | 8,37 | 1,57 | 24,10 | 70,15 | 1,70 |
1800-2000 | 6,10 | 73,01 | 1,70 | 86,80 | 12,91 | 1,58 | 19,30 | 76,11 | 1,70 |
>2000 | 13,20 | 77,55 | 1,70 | 100,00 | 21,44 | 1,60 | 13,20 | 77,55 | 1,70 |
Итого | 100,00 | 21,44 | 1,60 | - | - | - | - | - | - |
Исходя из полученных результатов гранулометрического и фракционного анализов можно сделать вывод, что даже при простой классификации шлама по зерну 0,1 мм можно выделить 15–20 % топлива с зольностью до 16 %. Таким образом, можно предположить о технической возможности обогащения вторичного топлива крупностью более 0,1 мм гравитационным методом.
Исследования данного объекта показали, что зольность шлама не превышает 65 %. Гранулометрический анализ проб показал возможность обогащения класса крупнее 1 мм гравитационным методом, и менее этой крупности — методом масляной агломерации.
Изучение теоретических аспектов и практики применения традиционных, специальных и новых методов обогащения позволило выделить процесс масляной агрегации среди большинства. Он основан на избирательном смачивании углеродных частиц специальным реагентом и выделении их из всего объема углемасляной суспензии.
Этот процесс обладает многими преимуществами, основными из них являются:
- обогащение тонкодисперсного угля с зольностью до 60–70 %;
- эффективное обезвоживание угля с применением простых обезвоживающих аппаратов;
- агрегация угольных зерен во флокулы и агрегаты нужной крупности и зольности.
Единственным недостатком является большой расход масляного реагента [6]. Однако и эту проблему можно решить путем использования отходов коксохимического производства, где углеводородные продукты после технологической переработки оказываются непригодными для дальнейшего использования.
Большие масштабы производства кокса обуславливают получение значительного количества жидких и газообразных продуктов коксования, которые исчисляются миллионами тонн в год. Наравне с коксом, выход которого составляет около 70–80 %, образуются и летучие продукты. Значительный удельный вес при производстве кокса занимает выход газа, в котором содержится огромное количество (табл. 4) ценных компонентов, подлежащих извлечению и переработке.
Продукт | Выход, % на сухой уголь | |||
из газового | из жирного | из коксового | из отощенно-спекающегося | |
кокс | 72,57 | 75,03 | 81,41 | 85,86 |
пирогенетическая вода | 5,27 | 5,10 | 2,87 | 1,70 |
смола | 4,83 | 4,41 | 3,07 | 1,85 |
Сырой бензол | 1,37 | 1,05 | 0,8 | 0,38 |
газ | 14,74 | 13,0 | 10,85 | 9,9 |
аммиак | 0,22 | 0,22 | 0,26 | 0,20 |
диоксид углерода и сероводород | 1,0 | 1,19 | 0,74 | 0,11 |
Хотя содержание указанных продуктов сравнительно небольшое, однако при больших масштабах коксохимического производства на основе соединений, которые изымаются из коксового газа, производится более 100 видов промышленной продукции.
Характеристика основных промышленных отходов коксохимических заводов приведена в таблице 5 [11].
№ | Наименование отходов | Класс токсичности | Тип (органический или неорганический) | Пожароопасность | Агрегатное состояние |
1 | Порода (отходы углеобогащения) | 4 | органический | негорючий | твердое |
2 | Хвосты флотации | 4 | органический | негорючий | Суспензия |
3 | Фусы каменноугольные | 2 | смешанный | горючий | смолистая масса |
4 | Кислая смолка сульфатного отделения | 2 | смешанный | негорючий | вязкая смолистая масса |
5 | Полимеры бензольных отделений | 3 | смешанный | горючий | жидкое |
6 | Смола и масла | 2 | смешанный | горючий | жидкое |
7 | Отработанный раствор сероочисток | 2 | смешанный | негорючий | жидкое |
8 | Отработанная H2 SO4 | 2 | неорганический | негорючий | жидкое |
9 | Кубовые остатки фталевого ангидрида | 2 | смешанный | горючий | твердое |
В результате исследования сырьевой базы коксохимического завода, а также анализа работы многих предприятий в этой области были обнаружены такие альтернативные реагенты как — кислая смолка, полимеры бензольных отделений, отработанные масла и мазуты, кубовые остатки фталевого ангидрида.
При выборе нужного реагента руководствовались, прежде всего, безопасностью выбираемого вещества и агрегатным состоянием (табл. 5). Оптимальным вариантом в этом случае является полимер бензольного отделения.
Кроме того, эти соединения не находят квалифицированного применения: основное количество полимеров сжигается или используется на утилизационных установках для подачи в качестве добавки в угольную шихту. Следует обратить также внимание, что эта группа продуктов коксохимических производств имеет и ограниченный сбыт.[12]
В результате применения полимеров бензольного отделения процесс селективной агломерации протекает быстрее и качественнее, это показали и наши исследования. Используя опыт работы аналогичных фабрик, принят расход полимерного связующего в пределах 15–20 %. Анализы экспериментов показывают, что промышленный процесс агломерирования на первом этапе целесообразно вести в концентрированных суспензиях, что значительно увеличивает его производительность без заметного ухудшения качества.
Учитывая опыт работы фабрик-аналогов и некоторых особенностей ЯКХЗ, следует использовать процессы смешивания, агломерации и обезвоживания.
Целесообразным будет использование модифицированной флотационной машины для операции смешивания и агломерирования. Изменяя режим работы флотационной машины МФУ, регулируем крупность углемаслянного агрегата.
Для обезвоживания углемасляного гранулята используются простые обезвоживающие аппараты механического действия: дуговые сита.
Однако, фракционный анализ угля крупностью более 0,1 мм показывает, что зоны №6 и №7 имеют очень трудную категорию обогатимости, а остальные — среднюю. Определение категории обогатимости осуществляется в соответствии показателем обогатимости по ГОСТу 10100-84:
Тобщ=(100*6,1)/(100-13,2)=7,02
Т6=100*(5,1+14,75)/(100-19,25)=24,58
Т7= 100*(10,07+10,93)/(100-19,9)=26,21
Значение категории обогатимости характеризует наличие сростков в зонах № 6 и № 7. Для их раскрытия предусматриваем операцию измельчения по крупности 0,1 мм с добавкой связующего. Это обеспечивает срыв окси-пленки с поверхности угольных частиц.
Обогащение остальных зон, имеющих среднюю категорию обогатимости производим на установках гравитационного действия — винтовых сепараторах с предварительной гидравлической классификацией и последующими операциями осаждения и фильтрования.
С целью повторного использования связующего гранулят подвергают обезмасливанию. Регенерацию масляной фазы из суспензии осуществляют за счет отстаивания суспензии в сгустителях при температуре в пределах 10–20 оС.
Проведенные совместно с Авдеевским КХЗ испытания по использования гранулированного концентрата, полученного из органической части отходов, показали целесообразность присадки его к основной коксовой шихте (массовая доля до 5–10 %). Достаточно хороший кокс образуется на основе 100 %-ного гранулята, полученного с этим связующим. [10]
Принципиальная схема обогащения флотоотходов Ясиновского КХЗ представлена на рис.2
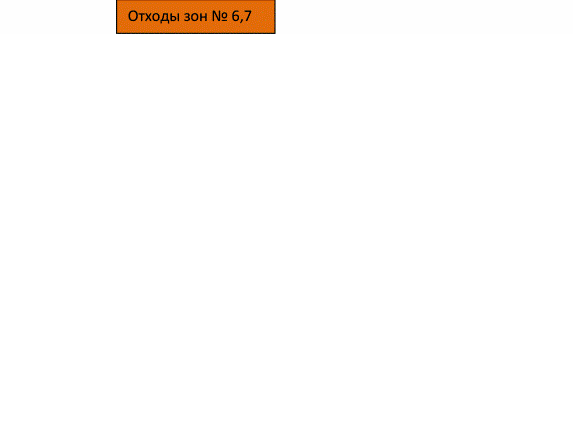
(Размер анимации 36 Кб, разрешение 580х430, количество циклов 8, количество кадров 34)
Рис.1 — Принципиальная схема обогащения продуктов илонакопителя ЯКХЗ
Заключение
Предложенная схема позволяет получить агломераты размером 0,5-5 см, влажностью в пределах 10-14 % и зольностью до 16 %. Следует указать, что полученные гранулы отличаются хорошей спекающейся способностью и могут служить дополнительным сырьем коксохимического производства.
Литература
- Белецкий В.С., Сергеев П.В., Папушин Ю.Л. Теория и практика селективной масляной агрегации углей. — Донецк, 1996
- Использование отходов обогащения путем их сжигания в топках с псевдоожиженным слоем/ А.А. Рандел, Д.В. Гоулл и др.// Новое в теории и практике псевдоожижения. — М.: Недра, 1980
- Лурий В.Г., Михеев О.В., Никишечев Б.Г. Новый способ окускования шламов и мелких классов каменных углей/Московский горный институт, М.:1993
- В.П. Надутый, А.М. Эрперт, А.И. Шевченко «Метод оценки качества шламов из илонакопителей» / Геотехнічна механіка: Міжвід. зб. наук. праць // Ін-т геотехнічної механіки ім. М.С. Полякова НАН України. — Дніпропетровськ, 2005. — Вип. 61
- Папушин Ю.Л. Энергетическое использование высокозольных шламов Донбасса// Матеріали науково-практичної конференції "Донбас — 2020: Наука і техніка — виробництву"— 2002
- Елишевич А.Т., Оглоблин Н.Д., Белецкий В.С., Папушин Ю.Л. Обогащение ультратонких углей — Донецк: Донбасс, 1985
- Диденко В.Е. Технология приготовления угольных шихт для коксования. — К.: «Вища школа. Головное изд-во», 1989
- Шендрик Т.Г., Белецкий В.С. Исследование межфазных взаимодействий в процессе масляной агломерации соленых углей// Экотехнологии и ресурсосбережение. — №1, 1995
- Папушин Ю.Л. Особенности извлечения масляной агрегацией коксующейся угольной фракции из илонакопителей// Научные труды ДонНТУ — Выпуск 15(131) — [Электронный ресурс] — режим доступа: http://www.nbuv.gov.ua/portal/natural/Npdntu/Gir/2008_15/S22.pdf
- XuMuK.ru/Сайт о химии./Коксование/[Электронный ресурс] — режим доступа: http://www.xumuk.ru/encyklopedia/2055.html
- Борисенко А.Л. Термическое обезвреживание в коксовых печах отходов коксохимических предприятий/УХИН/[Электронный ресурс] — режим доступа: http://www.nbuv.gov.ua/portal/natural/ukhj/2009_5-6/11.pdf
- Власов Г.А., Саранчук В.И., Чуищев В.М. Утилизация промышленных отходов на ОАО «Авдеевский коксохимический завод»/Экология окружающей среды/[Электронный ресурс] — режим доступа: http://www.eco-mir.net/show/352/
- Тесаловская Т.М.; Жиляев Ю.А.; Андрейков Е.И.; Степанова Л.А.; Акулов П.В.; Мальков Н.Н.(патент РФ)/Ru-Patent.info/Способ получения высокотемпературного пека для производства пекового кокса/[Электронный ресурс] — режим доступа: http://ru-patent.info/21/75-79/2176657.html
- Сергеев П.В., Белецкий В.С., Елишевич А.Т. Способ обогащения и обезвоживания угля «ОВЗУМС»/А.с. СССР №15584473// Открытия. Изобретения. — 1990, №15
- Офенгенден М.Е. Исследование повышения селективности флотации тонких угольных шламов:дис.кан.техн.наук — Сталино, 1952