Перспектива вичерпання природних запасів нафти і газу та пов'язане з цим збільшення споживання вугілля зумовило підвищений інтерес науковців світу до вугільних технологій. Особлива увага сьогодні приділяється вивченню спеціальних процесів збагачення вугілля, які відкривають нові можливості по переробці низькосортної сировини в кондиційні екологічно чисті продукти. [1]
Щорічно на збагачувальних фабриках переробляється близько 76,2 млн.т. вугілля (зольністю 38,5%), випускається 46,6 млн.т. товарних продуктів (зольністю 15,3%) та 29,6 млн.т. відходів (зольністю не біліше 75%). Це говорить про те, що у відходах втрачається близько 1200 тис.т. вугільних фракцій на рік через недосконалість технологічного процесу та режимів збагачення. [2]
В даний час проблеми економії палива та підвищення його якості повинні вирішуватися в комплексі. Наша країна гостро відчуває нестачу якісного коксівного вугілля, яке має важливу роль у виробництві чавуну, сталі, прокату. У зв'язку з цим збагачувачі постійно і безперервно ведуть пошук раціональних технологій і джерел збагачення.
Актуальність теми
Прогнозоване підвищення ролі вугілля в енергетиці обумовлено вичерпанням родовищ нафти і газу. Однак внаслідок погіршення гірничо-геологічних умов і недосконалість засобів механізації вугледобувних виробництв погіршується якісна характеристика вугілля по зольності, гранулометричному складу, вологості і сірки, отже, практично усе вугілля, що добувається потрібно піддавати збагаченню. У зв'язку з цим швидкими темпами збільшується кількість відходів на ОФ — шламових вод, вугільних шламів у гідровідвалах, териконах, мулонакопичувачах.
Недолік ресурсів теплоносіїв в Україні вимагає пошуку додаткових джерел за рахунок залучення в паливний баланс країни забалансових шламів та продуктів мулонакопичувачів, що утворилися в процесі експлуатації фабрик. За даними інституту «УкрНИИуглеобогащение» на фабриках Мінвуглепрому України зберігається у відстійниках і мулонакопичувачах 115880 тис. т шламових продуктів різної зольності. [4]
Тому найбільший інтерес для збагачувачів представляє використання вторинної сировини. Крім того, що ці об'єкти займають значні земельні площі, вони ще є і техногенними джерелами енергетичної та коксівної сировини.
Дрібні класи кам'яного вугілля та їх шлам накопичуються в мулонакопичувачах збагачувальних фабрик, і подальша їх переробка, підготовка до використання сьогодні являє собою серйозну проблему. Велика кількість шламів разом з водою потрапляє у водні об'єкти і забруднює їх. Використання дрібних класів вугілля і шламу після складного процесу їх сушіння, в топках і печах малоефективно через значні витрати цих продуктів у вигляді просипів під колосники. Крім того, дрібні класи при спалюванні потрапляють в повітря і забруднюють атмосферу. Таким чином, вельми актуальним завданням є розробка прогресивної технології переробки кам'яновугільних шламів та дрібних класів для подальшого ефективного їх використання, а також зменшення забруднення водних об'єктів та атмосфери. [3]
Зольність гірничої маси, що знаходиться в мулонакопичувачі Ясинівського КХЗ, коливається в межах 30 - 70%, а вміст органічної маси складає 30 - 50%. Тому можна вважати, що в силу відносно низькій зольності флотаційних відходів, цей мулонакопичувач є техногенним джерелом сировини, з якого можна отримати не тільки енергетичне паливо, але і концентрат для коксування.
Якісні показники шламів коливаються в широких межах по глибині та площі розподілу, що утруднює їх переробку. Тому дослідження фізико-хімічних властивостей твердої маси цього об'єкта, методів їх збагачення і розробка технології також є актуальним завданням.
Наукова значимість роботи
Напружений паливний баланс в Україні і несприятлива екологічна обстановка в Донбасі вимагає розробки ефективних способів використання тонкозернистих високобаластних продуктів з відстійників шахт і мулонакопичувачів, які займають значні земельні площі і погіршують санітарний стан води та атмосфери. [5] У зв'язку з цим пошук способів залучення в паливний баланс вуглевмісних відходів просто необхідний.
У даній роботі розроблена принципова схема отримання з вугільних шламів мулонакопичувача Ясинівського КХЗ концентрату, придатного для цілей коксування.
Наявність шламів, а також їх відмінність по зольності є результатом недосконалості існуючої технології збагачення вугілля. Оскільки шлами представляють собою углеродносілікатную масу, фізична сутність методу переробки шламів полягає в розділенні їх на складові: вуглець-силікати, що повною мірою до недавнього часу при існуючій технології неможливо виконати досить ефективно. [4]
Вивчення теоретичних аспектів і практики застосування традиційних, спеціальних і нових методів збагачення дозволило виділити процес масляної агрегації серед більшості.
Справа в тому, що особливістю складованих у мулонакопичувачах відходів флотації є великий вміст ультратонких вугільних фракцій, які неефективно витягаються флотаційні методом. У той час як процеси масляної агрегації (агломерація, грануляція) мають можливість отримувати широкий клас крупності вугільних часток з високозольного шламу і здатні забезпечити їх ефективне зневоднення на простих апаратах. [1]
В результаті проведених дослідів, були отримані дані, які дозволили розробити математичну модель процесу збагачення вугільних шламів методом масляної агломерації. Базуючись на виявлених закономірностях і встановлених залежностях фізико-хімічних процесів масляної агломерації, проаналізовано канали управління схеми в умовах Ясинівського КХЗ.
Практична цінність
Розроблено технологічну схему збагачення флотаційних відходів, що знаходяться у мулонакопичувачі Ясинівського КХЗ. Вона дозволить поліпшити якість кінцевого продукту, розширити сировинну базу підприємства, а також дозволить ефективно організувати безвідходне виробництво металургійної продукції та значно зміцнить позиції підприємства на вітчизняному ринку.
Огляд досліджень за темою в ДонНТУ
На базі ДонНТУ були проведені дослідження процесів масляної агломерації енергетичного вугілля (СМА-ТЕС), створено ряд перспективних рішень щодо застосування масляної агломерації для потреб магістральних гідротранспортних систем (СМАГ-ГТ) і вдосконалено процес СМА «вугілля-золото».
В основу технології «МГ-ТЕС» був покладений «амальгамний» механізм процесу масляної агломерації з урахуванням режимних параметрів. Він здійснюється в спеціальному апараті, куди подається підігріта вода, подрібнене вугілля та кальцинована сода з розрахунку 0,01-0,05 мас.%. Апарат агломерації складається з двох послідовно розташованих судин: в 1-м реалізується етап «амальгамування», 2-й призначений для структуроутворення та обкатування гранул. В'яжуче (мазут при tм = 80 0С) подається на всас насосу, який сприяє розподілу його по всьому об'єму пульпи. Зневоднення агломерату здійснюється на стаціонарному щільовидному ситі, обладнаному бризгалами.
Випробування пілотної установки в різних режимах дозволили розробити раціональну режимну карту процесу. У результаті проведених дослідів були отримані наступні результати: вологість — 14-18%, середня крупність гранул — 1,5 мм. Після дренування вологість продукту була знижена до 9-10%.
Таким чином, результати досліджень, проведених ДонНТУ підтверджують теоретичні викладки і свідчать про те, що:
- Якісні показники продуктів агломерації практично не залежать від зольності вихідного вугілля;
- Витрати мазуту на одиницю маси вихідного вугілля знижуються при збільшенні його зольності;
- Зольність відходів процесу СМА значно перевищує рівень при збагаченні традиційними методами вугілля тонких класів, що дозволяє використовувати їх у промисловості будівельних матеріалів;
- Гранульований концентрат добре зневоднюється на стаціонарному ситі, що виключає необхідність застосування центрифуг і термічного сушки;
- Апарати агломерації конструктивно прості і можуть бути використані на базі флотаційних машин, що серійно випускаються;
- Включення процесу СМА в пилеприготувальний цикл ТЕС відкриває перспективу переходу від сухого подрібнення вугілля на більш продуктивне - мокре і знижує вибухо- та пожежонебезпеку цеху подрібнення на ТЕС. [1]
Групою науковців ДонНТУ та Науково-виробничим об'єднанням «Гаймек» було досліджено шість основних технологічних варіантів «гідротранспорт-агломерація» вугілля:
- Перемішування вугілля на головному терміналі гідротранспортних систем (МГТС) в гранули 1 типу (плівкові) — трубопровідний транспорт грануляту в потоці води — зневоднення і обеззолення в осаджувальних центрифугах кінцевого терміналу;
- Перемішування вугілля на головному терміналі у гранули 2 типу (менісковий) — гідравлічний транспорт грануляту — обезводнення і обеззолення в фільтруючих центрифугах кінцевого терміналу;
- Перемішування на головному терміналі частини вугілля в гранули 2 типу — транспортування по трубах суміші «вугілля-гранулят» — обезводнення в фільтруючих або осаджувальна центрифугах кінцевого терміналу;
- Перемішування вугілля в гранули 1 типу безпосередньо в трубопроводі з подальшим зневодненням і обеззоленням грануляту на осаджувальних центрифугах;
- Зневоднення транспортованого МГТС вугілля на кінцевому терміналі в центрифугах з наступним перемішуванням вугілля з фугату центрифуг у гранули 1 типу — зневоднення і обеззолення грануляту на осаджувальних центрифугах;
- Гідротранспортування вугілля — обезводнення центрифугуванням на кінцевому терміналі з подальшим перемішуванням вугілля з фугату центрифуг у гранули 2 типу — обезводнення та обеззолення гранул на ситах і в суміші з вугіллям на центрифугах.
Дослідження проводили на енергетичному й коксовому вугіллі при додаванні мазуту М100 і М40. Аналіз і узагальнення результатів дозволили зробити висновок про безсумнівну перевагу технології «гідротранспорт-агломерація».
Позитивні результати експериментів дають підстави вважати, що комбінування гідравлічного транспорта вугілля із процесом його масляної агломерації забезпечує можливість створення МГТС нового покоління, здатних транспортувати кам'яні і буре вугілля різних марок і модифікацій без істотних змін їх фізико-хімічних характеристик з дотриманням вимог екологічної чистоти. [1]
Існуючі технології процесів СМА «вугілля-золото» забезпечують витяг золота крупністю 5-500 мкм на рівні 79-99%. Дослідження ДонНТУ та Інституту біоколоїдної хімії НАН України показали, що цей процес можливо удосконалити за рахунок модифікації поверхні вуглемасляних гранул спеціальними речовинами і таким чином розширити галузь застосування процесу, забезпечивши витяг зерен крупністю менше 5 мкм. У результаті раціонального підбору компонент гранул і їх модифікації можна суттєво покращити ефективність адгезійного збагачення золота.
Огляд досліджень по темі в Україні
Крім вищевказаних досліджень в Україні були проведені експерименти по селективній масляній агрегації високозольних вуглевміснихі продуктів ОФ. Цей метод був названий «ОВЗУМС» і рекомендується використовувати для переробки енергетичного вугілля з глибиною збагачення вище 1-3 мм.
Характерною особливістю процесу є інтенсивне і недовготривале перемішування вуглевмісної суспензії з в'яжучим при невеликих його витратах. У результаті такої обробки виникають мікрофлокули, а гідрофільні частинки породи залишаються у воді. Для виділення зфлокульованого концентрату використовується осаджувальна центрифуга або флотаційна машина. В якості в'яжучої можуть використовуватися кам'яновугільні смоли. Найбільшу ефективність мають олія для омасленія шихти (мош), вбираюче масло, полімери бензольного відділення коксохімвиробництва.
Перший варіант цього процесу був реалізований на вуглезбагачувальній фабриці Авдіївського КХЗ. Установка для реалізації процесу створена на базі флотаційної машини МФУ-50. Перша камера була переобладнана як турбулізатор, на валу якого встановлено дві мішалки: верхня четирьохлопасна, хрестоподібна, нижня — стандартний імпеллер флотомашіни. Аераційна труба зі статором, піноз'ем були демонтовані.
Вихідний продукт подавали за допомогою насоса, підключеного до хвостової кишені сусідньої флотомашини. В'яжуче подавали дозувальним насосами. Для створення необхідного рН середовища додається водний розчин NaOH. Продукт перемішування з турбулізаторів самоплином переходив у другу камеру флотаційної машини. Ця камера (камера поділу) була обладнана стандартним блок-імпеллером зі зменшеною у два рази швидкістю обертання. Для зниження інтенсивності турбулентних потоків у цій камері над статором була встановлена «заспокійлива» решітка.
Концентрат масляної селекції зневоднюється разом з флотоконцентратом на барабанних фільтрах, потім присаджують його до шихти, яка йде на коксування.
У разі необхідності додаткової переробки основного концентрату ОВЗУМС використовували метод масляної грануляції. Суміш злива продукту та високов'яжучого надходила в гранулятор з приводом, де при високих швидкостях відбувається вторинне збагачення.
Другий варіант цього процесу був реалізований на ЦЗФ «Росія» в 1984-86 рр.. Переробці підлягав високозольний шлам енергетичного вугілля. У лабораторних експериментах вугілля класу 1-13 мм відокремлювали від загальної сировини, що надходить в апарат ОВЗУМС. Великі зерна використовувалися як зародиші (активних центрів) вуглемасляних флокул концентрату, що сприяють його кращому відокремленню від мінеральної компоненти при центрифугуванні.
Установка ОВЗУМС складалася з трьох апаратів масляної сепарації, які представляють собою ціліндроконічні ємності. У середині ці ємності обладнані консольним валом. Обойма кріпиться до кришки баку. На валу розташовано три імпеллера турбінного типу. Апарати масляної селекції встановлюються послідовно з невеликим перепадом висот, що забезпечує транспортування пульпи самоплином.
Огляд досліджень по темі у світі
Досвід роботи багатьох як вітчизняних, так і зарубіжних фабрик свідчить про ефективність процесів масляної агломерації при збагаченні ультратонкого вугілля. Оскільки досвід зарубіжних збагачувальних підприємств набагато більше, то доцільніше відобразити результати світових досліджень у вигляді таблиці 1.
Назва методу | Країна, вигляд установки, продуктивність | Етапи процесу | Реагент, витрати, % | Хар-ка вихідного матеріалу | Якість кінцевого продукту |
«Трент-процес» | США, промислова, 20 т/ч |
Змішування, грохотіння | Пічне масло, нафта, бензол, 25-35 | dи = 0-100 мкм, Аи = 10-35% |
dг = 3-6 мм, Ак = 4-26 %, Wг = 10-20 % |
«Конвертоль» | ФРГ, напівпромислова, 5 т/ч |
Змішування, центрифугування | Важкий мазут, 10-15 | dи = 0-1 мм, Аи = 15-20% |
Ак = 2-9,5 %, Wг = 10-15,5 % |
«Оліфлок» | ФРГ, промислова, 30 т/ч |
1 варіант — змішування, грохотіння, центрифугування | Легкі фракції мазута, 10-18 | dи = 0-1 мм | dг = 0,5 мм, Wг = 15-20 % |
2 варіант — змішування, центрифугування, грохотіння, флотація | Легкі фракції мазута, 10-18 | dи = 0-1 мм, Аи = 33 % |
dг = 0,5 мм, Ак = 8-9 %, Wг = 15 % |
||
Польща, досвідна | 3 варіант — Змішування, грохотіння | Дизельне масло, 16 | dи = 0-0,05 мм, Аи = 10-21% |
dг = 1 мм, Ак = 6-9 %, Wг = 15-20 % |
|
Масляная агломерація (CFRI) | Індія, досвідна | Кондиціювання, змішування, грохотіння, огрудкування | Легке масло, 6-12 | dи = 0-100 мкм, Аи = 12-40 % |
Ак = 5-21 % |
США, промислова, 250 кг/ч |
Змішування, грохотіння (+центрифугування), сушка | Легке масло, 0,5-3,Важке, 8-12 | dи = 0-0,1 мм, Аи = 17-40 % |
dг = 2 мм, Ак = 10-21 %, Wг = 7 % |
|
Індія, напівпромислова, 2 т/ч |
Кондиціювання, змішування, грохотіння, огрудкування | Легке масло,1-2, Важке, 10-18 | dи = 0-0,5 мм, Аи = 17-41% |
dг = 2-8 мм, Ак = 9-22 %, Wг = 10 % |
|
Сферична агломерація (NRCC) | Канада, досвідна, 5 кг/ч |
Кондиціювання, змішування, грохотіння, гранулювання | Дизельне паливо, 5, Мазут, 20-70 | dи = 0-0,015 мм, Аи = 15-20% |
dг = 6-10 мм, Ак = 5-8 %, Wг = 5 % |
Селективна агломерація (ВНР) | Австралія, напівпромислова, 5 т/ч |
Змішування, грохотіння | Легке масло, 8 - 14 | dи = 0-0,1 мм | dг = 2-5 мм, Ак = 7-9 %, Wг = 12 % |
«IPTACCS» | Австралія, напівпромислова, 30-50 т/ч |
Змішування, гідротранспорт, грохотіння | Продукти коксування, 10-15 | dи = 0-0,5 мм, Аи = 23-26 % |
dг = 1 мм, Ак = 10-13 % |
Аи — зольність вихідного, Ак — зольність концентрату, dг — крупність гранул,dи — крупність вихідного, Wг — вологість гранульованого концентрату. |
Зміст роботи
Результати досліджень властивостей відходів флотації, складованих у мулонакопичувачі ЯКХЗ, дозволили скласти гранулометричний і фракційний аналіз об'єднаної технологічної проби масою 100 кг. У табл. 2 — 3 наведено гранулометричний і фракційний склад об'єднаної проби відходів флотації.
Клас крупності, мм | Вихід, % | Зольність, % | Вміст сірки, % | Сумарний вихід надрешітного продукту | Сумарний вихід подрешітного продукту | ||||
Вихід, % | Зольність, % | Вміст сірки, % | Вихід, % | Зольність, % | Вміст сірки, % | ||||
> 1,0 | 1,19 | 5,18 | 1,35 | 1,19 | 5,18 | 1,35 | 100,00 | 42,25 | 1,51 |
0,5-1,0 | 6,19 | 10,27 | 1,32 | 7,37 | 9,45 | 1,32 | 98,81 | 42,69 | 1,51 |
0,3-0,5 | 9,19 | 15,23 | 1,40 | 16,56 | 12,66 | 1,37 | 92,63 | 44,85 | 1,52 |
0,1-0,3 | 26,07 | 27,14 | 1,45 | 42,64 | 21,51 | 1,42 | 83,44 | 48,12 | 1,54 |
0,044-0,1 | 25,71 | 48,50 | 1,45 | 68,34 | 31,67 | 1,43 | 57,36 | 57,65 | 1,58 |
0,0-0,044 | 31,66 | 65,09 | 1,68 | 100,00 | 42,25 | 1,51 | 31,66 | 65,09 | 1,68 |
Загалом | 100,00 | 42,25 | 1,51 | - | - | - | - | - | - |
Щільність розділення, кг/м3 | Вихід, % | Зольність, % | Вміст сірки, % | Сумарний вихід надрешітного продукту | Сумарний вихід подрешітного продукту | ||||
Вихід, % | Зольність, % | Вміст сірки, % | Вихід, % | Зольність, % | Вміст сірки, % | ||||
<1500 | 73,60 | 5,34 | 1,57 | 73,60 | 5,34 | 1,57 | 100,00 | 21,44 | 1,60 |
1500-1600 | 2,30 | 26,36 | 1,57 | 75,90 | 5,98 | 1,57 | 26,40 | 66,33 | 1,69 |
1600-1800 | 4,80 | 46,17 | 1,68 | 80,70 | 8,37 | 1,57 | 24,10 | 70,15 | 1,70 |
1800-2000 | 6,10 | 73,01 | 1,70 | 86,80 | 12,91 | 1,58 | 19,30 | 76,11 | 1,70 |
>2000 | 13,20 | 77,55 | 1,70 | 100,00 | 21,44 | 1,60 | 13,20 | 77,55 | 1,70 |
Загалом | 100,00 | 21,44 | 1,60 | - | - | - | - | - | - |
Виходячи з отриманих результатів гранулометричного і фракційного аналізів можна зробити висновок, що навіть при простій класифікації шламу по зерну 0,1 мм можна виділити 15-20% палива із зольністю до 16%. Таким чином, можна припустити про технічну можливість збагачення вторинного палива крупністю більше 0,1 мм гравітаційним методом.
Дослідження даного об'єкта показали, що зольність шламу не перевищує 65%. Гранулометричний аналіз проб показав можливість збагачення класу крупніше 1 мм гравітаційним методом, і менше цієї крупності — методом масляної агломерації.
Вивчення теоретичних аспектів і практики застосування традиційних, спеціальних і нових методів збагачення дозволило виділити процес масляної агрегації серед більшості. Він заснований на вибірковому змочуванні вуглецевих частинок спеціальним реагентом і виділенні їх з усього обсягу вуглемасляної суспензії.
Цей процес має багато переваг, основними з них є:
- збагачення тонкодисперсного вугілля з зольністю до 60-70%;
- ефективне зневоднення вугілля із застосуванням простих зневоднюючих апаратів;
- агрегація вугільних зерен у флокули й агрегати потрібної крупності та зольності.
Єдиним недоліком є велика витрата масляного реагенту [6]. Однак і цю проблему можна вирішити шляхом використання відходів коксохімічного виробництва, де вуглеводневі продукти після технологічної переробки виявляються непридатними для подальшого використання.
Великі масштаби виробництва коксу обумовлюють отримання значної кількості рідких і газоподібних продуктів коксування, які обчислюються мільйонами тонн в рік. Нарівні з коксом, вихід якого становить близько 70-80%, утворюються і летючі продукти. Значну питому вагу при виробництві коксу займає вихід газу, в якому міститься величезна кількість (табл. 4) цінних компонентів, що підлягають вилученню і переробці.
Продукт | Вихід, % на сухе вугілля | |||
з газового | з жирного | з коксового | з отощено-спікливого | |
кокс | 72,57 | 75,03 | 81,41 | 85,86 |
пірогенетична вода | 5,27 | 5,10 | 2,87 | 1,70 |
смола | 4,83 | 4,41 | 3,07 | 1,85 |
Сирий бензол | 1,37 | 1,05 | 0,8 | 0,38 |
газ | 14,74 | 13,0 | 10,85 | 9,9 |
амміак | 0,22 | 0,22 | 0,26 | 0,20 |
Діоксид вуглецю та сірководень | 1,0 | 1,19 | 0,74 | 0,11 |
Хоча зміст зазначених продуктів порівняно невелике, проте при значнихх масштабах коксохімічного виробництва на основі сполук, що вилучаються з коксового газу, виробляється більше 100 видів промислової продукції.
Характеристику основних промислових відходів коксохімічних заводів наведено в таблиці 5 [11].
№ | Назва відходів | Клас токсичності | Тип (органічний или неорганічний) | Пожаробезпека | Агрегатний стан |
1 | Порода (відходи вуглезбагачення) | 4 | органічний | негорючий | тверде |
2 | Хвости флотації | 4 | органічний | негорючий | Суспензія |
3 | Фуси кам'яновугільні | 2 | змішаний | горючий | смоляна маса |
4 | Кисла смолка сульфатного відділення | 2 | змішаний | негорючий | в'язка смоляна маса |
5 | Полімери бензольного відділення | 3 | змішаний | горючий | рідке |
6 | Смола та масла | 2 | змішаний | горючий | рідке |
7 | Відпрацьований розчин сіроочісток | 2 | змішаний | негорючий | рідке |
8 | Відпрацьована H2 SO4 | 2 | неорганічний | негорючий | рідке |
9 | Кубові залишки фталевого ангідрида | 2 | змішаний | горючий | тверде |
У результаті дослідження сировинної бази коксохімічного заводу, а також аналізу роботи багатьох підприємств у цій області були виявлені такі альтернативні реагенти як — кисла смолка, полімери бензольних відділень, відпрацьовані мастила та мазути, кубові залишки фталевого ангідриду.
При виборі потрібного реагенту керувалися, перш за все, безпекою вибираної речовини і агрегатним станом (табл. 5). Оптимальним варіантом у цьому випадку є полімер бензольного відділення.
Крім того, ці речовини не знаходять кваліфікованого застосування: основна кількість полімерів спалюється або використовується на утилізаційних установках для подачі в якості добавки у вугільну шихту. Слід звернути також увагу, що ця група продуктів коксохімічних виробництв має обмежений збут. [12] В результаті застосування полімерів бензольного відділення процес селективної агломерації протікає швидше і якісніше, це показали і наші дослідження. Використовуючи досвід роботи аналогічних фабрик, прийняли витрати полімерного в'яжучого в межах 15-20%. Аналізи експериментів показують, що промисловий процес агломерації на першому етапі доцільно вести в концентрованих суспензіях, що значно збільшує його продуктивність без помітного погіршення якості.
В результаті застосування полімерів бензольного відділення процес селективної агломерації протікає швидше і якісніше, це показали і наші дослідження. Використовуючи досвід роботи аналогічних фабрик, прийняли витрати полімерного в'яжучого в межах 15-20%. Аналізи експериментів показують, що промисловий процес агломерації на першому етапі доцільно вести в концентрованих суспензіях, що значно збільшує його продуктивність без помітного погіршення якості.
З огляду на досвід роботи фабрик-аналогів і деяких особливостей ЯКХЗ, слід використовувати процеси змішування, агломерації та зневоднення.
Доцільним буде використання модифікованої флотаційної машини для операції змішування та агломерації. Змінюючи режим роботи флотаційної машини МФУ, регулюємо крупність углемаслянного агломерату. Для зневоднення використовуються прості зневоднюючі апарати механічної дії: дугові сита.
Однак, фракційний аналіз вугілля крупністю більше 0,1 мм показує, що зони № 6 і № 7 мають дуже важку категорію збагачуваності, а решта — середню. Визначення категорії збагачуваності здійснюється відповідно до показника збагачуваності за ГОСТом 10100-84:
Значення категорії збагачуваності характеризує наявність зростків в зонах № 6 і № 7. Для їх розкриття передбачаємо операцію подрібнення до крупності 0,1 мм з добавкою в'яжучого. Це забезпечує зрив оксі-плівки з поверхні вугільних частинок.
Збагачення інших зон, що мають середню категорію збагачуваності проводимо на установках гравітаційної дії — гвинтових сепараторах з попередньою гідравлічною класифікацією і подальшими операціями осадження і фільтрування.
З метою повторного використання в'яжучого гранулят піддають обезмасленню. Регенерацію масляної фази з суспензії здійснюють за рахунок відстоювання суспензії в згущувачі при температурі в межах 10-20 0С.
Проведені спільно з Авдіївським КХЗ випробування з використання гранульованого концентрату, отриманого з органічної частини відходів, показали доцільність присадки його до основної коксової шихті (масова частка до 5-10%). Досить хороший кокс утворюється на основі 100%-ного грануляту, отриманого з цим в'яжучим. [10]
Принципова схема збагачення флотовідходів Ясинівського КХЗ представлена на рис.2.
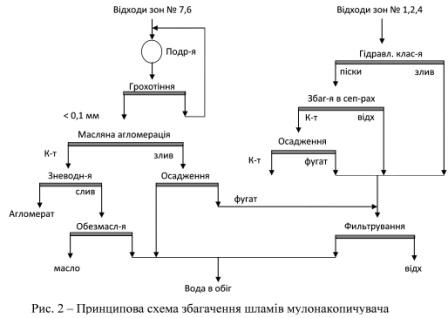
Висновок
Запропонована схема дозволяє отримати агломерати розміром 0,5-5 см, вологістю в межах 10-14% і зольністю до 16%. Варто зазначити, що отримані гранули відрізняються кращою спікливою здатністю і можуть служити додатковою сировиною коксохімічного виробництва.
Література
- Белецкий В.С., Сергеев П.В., Папушин Ю.Л. Теория и практика селективной масляной агрегации углей. — Донецк, 1996
- Использование отходов обогащения путем их сжигания в топках с псевдоожиженным слоем/ А.А. Рандел, Д.В. Гоулл и др.// Новое в теории и практике псевдоожижения. — М.: Недра, 1980
- Лурий В.Г., Михеев О.В., Никишечев Б.Г. Новый способ окускования шламов и мелких классов каменных углей/Московский горный институт, М.:1993
- В.П. Надутый, А.М. Эрперт, А.И. Шевченко «Метод оценки качества шламов из илонакопителей» / Геотехнічна механіка: Міжвід. зб. наук. праць // Ін-т геотехнічної механіки ім. М.С. Полякова НАН України. — Дніпропетровськ, 2005. — Вип. 61
- Папушин Ю.Л. Энергетическое использование высокозольных шламов Донбасса// Матеріали науково-практичної конференції "Донбас — 2020: Наука і техніка — виробництву"— 2002
- Елишевич А.Т., Оглоблин Н.Д., Белецкий В.С., Папушин Ю.Л. Обогащение ультратонких углей — Донецк: Донбасс, 1985
- Диденко В.Е. Технология приготовления угольных шихт для коксования. — К.: «Вища школа. Головное изд-во», 1989
- Шендрик Т.Г., Белецкий В.С. Исследование межфазных взаимодействий в процессе масляной агломерации соленых углей// Экотехнологии и ресурсосбережение. — №1, 1995
- Папушин Ю.Л. Особенности извлечения масляной агрегацией коксующейся угольной фракции из илонакопителей// Научные труды ДонНТУ — Выпуск 15(131) — [Электронный ресурс] — режим доступа: http://www.nbuv.gov.ua/portal/natural/Npdntu/Gir/2008_15/S22.pdf
- XuMuK.ru/Сайт о химии./Коксование/[Электронный ресурс] — режим доступа: http://www.xumuk.ru/encyklopedia/2055.html
- Борисенко А.Л. Термическое обезвреживание в коксовых печах отходов коксохимических предприятий/УХИН/[Электронный ресурс] — режим доступа: http://www.nbuv.gov.ua/portal/natural/ukhj/2009_5-6/11.pdf
- Власов Г.А., Саранчук В.И., Чуищев В.М. Утилизация промышленных отходов на ОАО «Авдеевский коксохимический завод»/Экология окружающей среды/[Электронный ресурс] — режим доступа: http://www.eco-mir.net/show/352/
- Тесаловская Т.М.; Жиляев Ю.А.; Андрейков Е.И.; Степанова Л.А.; Акулов П.В.; Мальков Н.Н.(патент РФ)/Ru-Patent.info/Способ получения высокотемпературного пека для производства пекового кокса/[Электронный ресурс] — режим доступа: http://ru-patent.info/21/75-79/2176657.html
- Сергеев П.В., Белецкий В.С., Елишевич А.Т. Способ обогащения и обезвоживания угля «ОВЗУМС»/А.с. СССР №15584473// Открытия. Изобретения. — 1990, №15
- Офенгенден М.Е. Исследование повышения селективности флотации тонких угольных шламов:дис.кан.техн.наук — Сталино, 1952