Abstract
This paper summarizes some conclusions and experiences from installation and start-up of a new 100 MVA AC arc-furnace (EAF) in a weak 220 kV-network in the middle of Sweden. Reflections are made to the operation of the furnace itself as well as to it's impact on the supplying network. The first measurement performed, prior to installation, that formed a basis for contractual requirements, and registrations during and after start-up are presented. Considerations and ideas for flicker reduction and mitigation are also presented.
After start-up of the EAF, complaints due to flicker started. Measurements prior to and after startup identified the furnace as the dominating source. Further measurements also indicated that the control and design of several vital functions in the system did not operate properly. After several actions, mainly initiated from the steel mill, the flicker emission has been reduced to approximately 60% of the initial level.
Keywords: flicker, harmonics, power quality, arc furnace
1. Introduction
1.1. Network Description
The structure of the Swedish 220 kV and 400 kV transmission network is shown in Fig. 1. There are approximately 10500 km 400 kV and 4400 km 220 kV transmission lines. In about 120 transformer stations the power is transformed down to 130 kV or lower levels.
Sweden is a large country with a rather small population. Since power generation is concentrated to areas in the north (hydro-power) and to the south (nuclear power) lines are relatively long and there are areas in the middle of Sweden were the short-circuit power is low. One of those areas is Bergslagen, were many steel-mills are located.
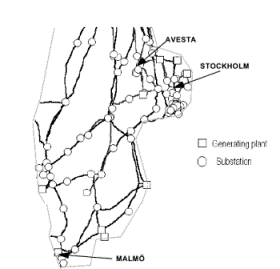
Fig. 1. Structure of the 400- and 220 kV transmission network in south of Sweden
In this paper a new 100 MVA Electric Arc Furnace(EAF) installation, located in Avesta, is discussed. The network around Avesta is shown in Fig. 2.
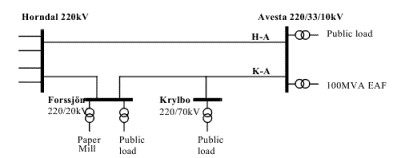
Fig. 2. Network feeding a new 100 MVA EAF in Avesta
The normal and minimum short-circuit power levels at the 200 kV PCC in Avesta are
maximum 3700 MVA
normal 3400-3500 MVA
low 3000 MVA
line H-A disc 2700 MVA
line K-A disc 2000 MVA
1.2. Measurements Prior to Installation
Several kinds of measurements, harmonics, flicker and determination of the actual short circuit power, were performed by the Swedish National Grid prior to formulating final contractual requirements. The following values were registered at the supplying point of the new furnace in 1994 (see Table 1.):
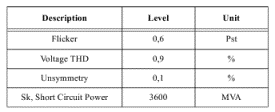
All values presented in Table 1, except Sk, refers to 95% non-exceeding weekly probability values measured in accordance with relevant IEC standards, [1] , [2].
1.3. Contractual Limits and Conditions
Since the number of both distorting and sensitive loads connected to the power system increases, there is a need for acceptable emission limits with respect to voltage deficiencies. Today when new contracts are for¬mulated, the Swedish National Grid also includes contractual limits for power quality levels, among them flicker limits [3].
Allowed flicker level in a substation is set to Pst95% .=1. Since flicker is related to voltage changes, all customers connected to the same point will be exposed to the same flicker-level. This also means that all customers connected to that point must share the total flicker emission limit level [4].
In some cases, as for Avesta, there is due to the low short circuit power a special contract allowing up to Pst 95%.=1,7 on the 220 kV-bus. This high level can only be accepted as long as no other customer is complaining. If there are complaints, the disturbing customer has to bring the level down to an acceptable level.
1.4. History and Relations to other customers
The installation in Avesta was commissioned in August 1995. Directly after the start-up the flicker level reached levels up to Pst95% = 2,9. Soon there were a lot of complaints from customers within a 50 km radius area from Avesta. Many MV-distribution companies were not informed of the furnace installation and made their own investigation to find the origin of disturbances.
At a meeting with concerned companies held in November 1995, furnace power limitations during certain hours of the day were agreed upon. The furnace-problems were also expected to be solved before January 1996. As the disturbances continued a 220 kV-network reconfiguration was carried out in order to separate the disturbing load from the public network, from January until May 1996. From March until November 1996 a sectionalizing point in the 70 kV grid was also changed.
The reconfiguration, causing increased network losses and loss of redundancy, temporarily reduced the flicker level in the public network and the number of complaints, but did not solve the main problem. The short-circuit power reduction from 3500 MVA to 2700 MVA in the EAF point of supply was another disadvantage effecting arc-stability and the steel production.
In January 1997 several measures were taken by the steel mill in order to reduce the flicker level to Pst 95% = 1,7-2,0. This was achieved and the number of complaints have significantly decreased. It may therefore be considered that, close to EAF-installations, an acceptable flicker level can be higher than Pst 95% =1.0.
2. New 100 MVA Arc Furnace
2.1. Furnace Development
An EAF today is used mainly as a "melting machine" for steel scrap. The "melting machine" operates either with DC or AC. The AC-type is the earliest type and has been in use since the mid-thirties. Since then different steps have been taken to reduce production costs (measured in costs per ton steel). The development of the DC-EAF started at the end of the fifties, with the purpose to decrease the graphite (electrode -pole) consumption with at least 50%, due to the fact that only one graphite electrode is necessary. Unexpected troubles were however soon encountered with the furnace bottom, which was used as the second electrode (+pole). During this time the AC-EAF's ratings increased from about 10 MVA to about 50 MVA. At a lot of places where EAF's were located the supply grids did not "develop" at the same rate. A new problem occurred: The power quality degenerated due to large stochastic loads like EAF's.
Today there are EAF's larger than 400 tonnes and 350 MVA. Often used key-figures are 1000 kVA per ton daily production, more than 25 heats per day and between 0,5 - 1,2 million tonnes annual production.
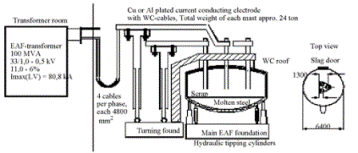
Fig. 3. Overview of a traditional AC-EAF with a tapping weight of 100 tonnes
As can be seen in Fig. 3. the mast movements are hydraulically controlled. There are other types of drives like wire winches operated by electric motors, different types of magnetic couplings and ball-screws operated by electric motors with or without variable speed drives.
2.2. EAF Operation
There are several distinct phases in the operation of the EAF, from the initial scrap loading using buckets, to the tapping of molten steel at the end of the melting cycle. After scrap loading the electrodes are lowered until a short circuit between at least two electrodes occurs. At this moment a current begins to flow and the EAF-regulator starts to lift one or more electrodes in order to establish an electric arc. Very often at startup the regulator fails to establish the arcs, and needs to repeat this procedure until the arcs are established.
One reason why the regulator can fail to establish an arc is that the scrap, if it is light, is immediately molten away due to the high currents that occur during a short circuit. During the first phase, with a rather low voltage, the electrodes "bore" holes in the scrap for protection of the wall-refractories. This takes 0,5 - 1,0 min¬utes, thereafter the voltage is increased to maximum. If a primary reactor is present it will be set to a high reactance. Both actions have the aim to create the longest possible arcs which are easier to control and maintain compared with shorter ones. (Consider the impedance-change per cm arc-length if it operates at 450 mm arc-length or at 200 mm arc-length). During melt-down, scrap also falls from the walls directly on to the electrode(s) and a short circuit occurs.
When the last bucket is charged the above described procedure is repeated. When all the scrap is molten to a "bath, no other wall protection than the slag is available. From this point the operation of the furnace depends upon what kind of steel being produced. In case of a malt-steel furnace there is an excellent opportu¬nity to foam the slag with oxygen-injection. With the slag nicely foaming, the wall protection is better than with scrap. There is no need to reduce the voltage at this point. Due to the conditions inside the furnace the power-factor will increase as well as the active power, decreasing the total melt time. In most malt-steel furnaces carbon-powder will be injected to chemically increase the melt energy.
In case of a stainless-steel furnace, the foaming slag praxis can not be used in a similar way, due to metallurgical aspects since a chromium oxidation would occur at a very uneconomical rate. The only solution to save the walls is then to decrease the voltage and shorten the arc-length.
At this time both stainless- and malt-steel furnaces operate very smoothly and the operation conditions are almost perfect for the arcs. Metal particles are pressed up in the furnace atmosphere from the arc-current-pressure towards the bath surface. This and a lower power-factor will together improve the arc-ignition.
2.3. Production
In scrap based steel-production, production-economy is very important. The raw-material: scrap, alloys etc. have a price set by the world-market. The main competition is the conversion costs, costs to transform the scrap and alloys to a steel product requested on the steel market. There is also a difference between the maltand the stainless steel industry, based on more process steps required by stainless steel production. With time these differences will disappear due to a heavy enlargement of the stainless steel industry world wide. A common issue is production reliability without interruptions. In 1994 the world production of steel was about 1300 million tonnes total (including blast-furnaces). Stainless steel was produced at a rate of 13 million tonnes or 1% of the total.
In the western world the main cost carriers for the conversion is manpower, electricity, refractories and graphite consumption. All these except for manpower are considered as expendable supplies and therefore possible savings in the efforts of lean production. Various actions can be considered in order to reach convenient key-figures, setting the scrap in a proper position in the furnace, to use a scrap mix suitable for the furnace (depending on electrical data) and to operate the furnace regulator at stable working points. When these parameters matches the key-figures, the production is effective and the impact to the grid is the lowest possible. The common point in all cases is to operate the furnace with arc-stability.
2.4. Ratings and EAF Power Supply System
The EAF installation in Avesta discussed in this paper has the following data:
Steel-shop:
Investment based on annual production: 520000 tonnes.
100% stainless steel production.
Heat weight: 85 ton
Number of heats per day: 20
Estimated electric energy consumption: < 430 kWh/ton steel.
Electrical data:
Step down transformer:
U1 / U2 220 / 33 kV (no taps)
Sn 120 MVA
ek 15,7%
SVC-equip ment:
Un 33 kV
Sn120 MVAr
Furnace equipment:
Series reactor:
Xl 3.1 - 1.21, 0.0 W (6 taps)
EAF-Transformer:
U1 / U2 33 / 1,0-0,75-0,5 kV (21 taps)
Sn 100 MVA
ek 6,0 -11,0%
EAF-electrode impedance: 0,36 +j 2,49 mΩ.
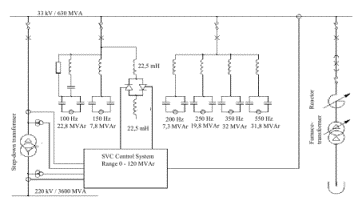
Fig. 4. One-line diagram over the power supply system in Avesta
It is very important that voltage drops caused by short circuits in the EAF appears over the proper impedance in the system, see Fig. 4.. In this case the series reactor is the most important component. Two things are essential about the reactor: If it is a core reactor, the core must not be saturated during a short circuit in the furnace and secondly, it's reactance should be chosen at a value which is enough to limit the short circuit current. The step-down transformer impedance has to be kept low to ensure that the reactive power from the SVC can be maintained considering the voltage drop that occurs during an electrode short circuit.
3. Measurements and Analysis
3.1. Real-time Measurements
Due to the stochastic nature of an arc-furnace loading, measurements for analysis and evaluation of the system performance as well as registration of harmonic emission must be performed in real-time. Harmonic measurements in accordance with IEC 1000-4-7, which basically deal with quasi-stationary harmonics, will only show averaged values of harmonics after FFT-transformation with no information on interharmonics.
Real-time registrations have been performed in two different furnace installations in order to compare both furnace- and SVC characteristics. In Avesta two 16-channel instruments were synchronized for simultaneously monitoring furnace characteristics and of effects from SVC-equipment and impact on the supply system. With one instrument located close to the furnace, electrode-movements and velocity as well as currents and voltages on the low-voltage side were recorded. The second instrument, located in the SVC-control room, monitored characteristics of the 220 kV supply and the behaviour of the SVC.
From the real-time registrations performed some time after start-up several conclusions could be drawn. One was that the SVC did not respond properly to load changes caused by the EAF. Both the control strategy and the reactive power measuring points have now been changed. Also a new design of the 100 Hz-filter could be motivated after real-time measurements of the filter currents.
The other furnace installation, with a 40 MVA EAF, provides two differently sized step-down-transformers. The flicker emission as well as the SVC- and furnace characteristics were studied with two different cou-pling-impedances between the as could be expected SVC and the grid. The result from these registrations confirmed that with a reduced impedance between the SVC and the grid, also the flicker level was reduced.
3.2. EAF Control System
It was described earlier in this paper how the scrap behaves at melt-down. In this section both melt-down as well as the refining and superheating phases and their different requirements on the regulator, hydraulic and control systems are discussed.
Regulators for EAF's are almost all made so that the balance between voltage and current controls the output to the electrode mast servo system. Independently of whether a regulator is analogue or digital this balance is achievable but the accuracy can be higher with a digital type. Also a lot of other considerations and functions can be realized with a digital regulator.
In all regulator systems, the voltage and the current, and sometimes also the active power, is measured in each phase. Measured values can be evaluated in several ways. In some modern computerised systems it is optional to use impedance, current, power-factor, active power or in some cases phase symmetry, as the lead value. However most common is to control the impedance in each electrode, which obviously is a "difficult task", especially during melt-down. The only help in this case is the primary reactor, which at this time is set to its highest reactance. To respond properly to the stochastic changes in current magnitude, necessary calculations has to be made fast and accurate actions has to be taken. One method to improve the total performance is to use several closed loops, also incorporating mechanical movements. This gives higher gain (speed), and a shorter integration time (time delay) in the system. Low-impedance short circuits and unwanted arc interruptions can only be avoided with a fast and accurate system.
At operation on baths during refining and superheating, the regulator alone controls the arc-stability. In this mode of operation the primary reactor (if present) is out of operation. The arcs are shorter and the leading quantity for the regulator is heavily affected by small disturbances in the arcs.
If the working points are wrongly chosen, a too high power-factor will be the result, and the EAF will operate unstable due to poor arc ignition. Instability in the furnace will cause unwanted voltage fluctuations and higher flicker levels. The working point is determined by voltage and current measurements. Other electric properties, like power and power-factor are the prime variables but voltage and current behaviour are normally the measured quantities to get the wanted characteristics.
3.3. SVC (Static Var Compensation)
The basic purpose with the SVC is to provide a controlled reactive power source. Both the active and reactive power variations will cause voltage fluctuations in the system. The network impedance is mainly inductive and therefore the voltage drop due to active power is smaller compared to the same "amount" of reactive power. A short-circuit in the furnace will mainly consume reactive power, causing a large voltage drop in the system. If this can be compensated with a very fast reactive power production the voltage will be more stable the arc stability improved. Since SVC's with thyristor-bridges can only control the current after a certain delay after the measurement, a thyristor-based technique has limitations and provides a rather low flicker-reduction ratio. With time new HV-semiconductors will be available providing entirely new solutions for compensation, arc stability and flicker reduction.
One main question remains and deals with measurements and selection of feedback signals and the control strategy. Different strategies, often based on analogue technique, exists for the SVC-control. Some of them are based on symmetrizing the unbalanced active load and compensating the reactive power demand, while others control reactive current. Often a combination of these two methods are used, with different time-constants, providing a fast but less accurate initial open loop control sensing the reactive current component and a much slower closed loop for the reactive power compensation.
The fact that the "process" (arc-furnace) is stochastic and causes very rapid changes in many parameters, current and voltage magnitude and phase as well as 3-phase symmetry, makes it necessary to have solid and effective measuring systems and control algorithms. To achieve a faster response time, digital techniques will probably be required for measuring and control purposes. A digital technic will also open means for more sophisticated overall control strategies, involving information exchange between essential furnace control functions and the SVC-equipment.
3.4. Filter Design
The capacitor-banks included in SVC's are often designed as harmonic filters, with series reactors, tuned to specific frequencies. The frequency-spectra for systems with EAF contains not only harmonic components, but also a large amount of interharmonics ranging from a few hertz up to 250 - 300 Hz.
Design of filters used in EAF-applications must be made with concern to interharmonics generated by the furnace as well as harmonic frequencies generated by the TCR. The stochastic nature of an EAF also requires sufficient margins used to avoid transient thermal and dielectric stress. Since a "worst case condition" is hard to predict, relevant protective measures against various overload conditions becomes essential.
Traditional overcurrent and thermal overload protections is sufficient to protect the filter-reactors. Capacitors however are sensitive to overvoltages with a much steeper voltage-time characteristic and will therefore require two kinds of overvoltage protections, one with an inverse-time-characteristic for protection of limited slow overvoltages and surge-arresters protecting against transient overvoltages. The surge arresters are normally located across the capacitors forming the low-order filters. For harmonics measurements using traditional FFT- or DFT-transformation over several periods, the resolution of individual frequency components will be more or less averaged. This may result in a false information considering actual load conditions. One method to improve, especially low-frequency, resolution is with a "transient FFT-algorithm". A gliding window of one period length is FFT-transformed every half cycle, making it possible to determine both variations in the fundamental component amplitude and higher frequency components. Wavelet-transforms may also be considered to improve evaluation of the non-repetitive signals caused by arc-furnaces.
Several incidents have occurred damaging the resistors in the 100 Hz-filter, hence it was determined later that the first design of these resistors not fully considered the thermal load due to a large amount of inter-harmonics. After a new design the rated current and the thermal time-constant of the resistors have been significantly increased.
3.5. Flicker Propagation and Mitigation
Measurements of flicker were also simultaneously performed in several points close to another industry including an EAF rated 60 MVA. The public distribution system, which is connected to a 400 kV grid with a short-circuit-power at PCC of approximately 8000 MVA, is mainly radial and with only minor generation connected. From this measurements two conclusions were made:
• The flicker reduction between different voltage levels in a public radial network is rather small, here only around 10%.
• A flicker level of Pst=1.7 does not necessarily generate substantial complaints from local LV-customers. The arc-furnace is however rather old and the majority of the customers have been exposed to these, and maybe higher, flicker levels for a long time.
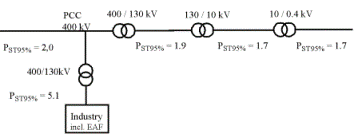
Fig. 5. Determination of flicker propagation in a public radial network
Several medium-sized hydro-power plants (< 50 MVA) are located close to, and can be connected to, the public 10 - 20 kV distribution system in Avesta. The flicker level can locally be reduced when these units are kept on line reducing the network impedance.
Also some large paper-mills are located close to Avesta. In Fig. 6. a flicker registration, in a local 20 kV-distribution system supplying a paper mill, is shown. When the mill was shut-down between Christmas and New-Year, with a short-circuit power reduction of 50%, the flicker level increased by approx. 50%.
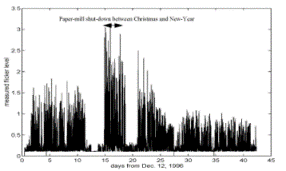
Fig. 6. Flicker-registration showing the influence of a holiday shutdown in a paper mill
4. Present Status and Future Improvements
After the improvements carried out in December 1996, the flicker level at the PCC i Avesta was reduced from approx. Pst95% = 2,3-2,4 to Pst95% = 1,7-1,9. The effect on the flicker level can be seen in Fig. 7. show¬ing a flicker registration performed prior to and after the improvements.
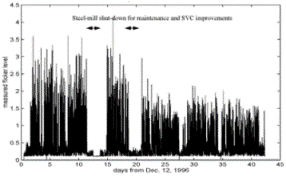
Fig. 7. Flicker registration in the 220 kV-system at approx. 30 km distance from Avesta.
In order to further improve production and better adopt it to the present grid conditions, some of the equipment, (step-down transformer and furnace transformer), will soon be changed. This will also solve some of the spare part requirements.
Since the power demand in this region is increasing the National Grid is now investigating an overall revision of the transmission system. Some limited alternatives to slightly improve the short-circuit level in Avesta is also being investigated.
5. Conclusions
The experiences from the discussed EAF-installation in Avesta are many, and some of them can be summarized as follows:
The most important factor for an economical, effective and low-impacting EAF-installation is the arc-stability. Since many parameters influence the arc-stability these installations require a system approach.
Digital technology will open new possibilities to perform fast, accurate and effective overall control of both the furnace and the SVC.
Measurements of electrical properties prior to installation, identifying emission levels and contractual requirements for equipment procurement, as well as performance verification during and after start-up are all essential for a successful EAF installation.
In case of an arc-furnace as a dominating flicker-source, a correlation between customer complaints and actual flicker level indicate that, based on weekly non-exceeding Pst95% probability values, an acceptable flicker level may be higher compared to the general short-time severity limits suggested in various standards.
The flicker attenuation in a public radial network can be very low. However an local reduction can be achieved if available generation, or other rotating AC-machines, can be connected to the public distribution system.
6. References
[1] IEC: "Electromagnetic Compatibility (EMC)" Part 4: "Testing and measurements techniques". Section 7: "General guide on harmonics and interharmonics measurement and instrumentation for power supply systems and equipment connected thereto". IEC 1000-4-7 1991-07
[2] IEC: "Flickermeter Functional and design specifications". IEC 868, 1986, Amendment 1 1990-07
[3] STRI: "Proposal for Limits and Responsibility Sharing with Regard to Power Quality". S-94-061, 1994
[4] F Jonas, K Ahlgren: "A Method for Sharing of Permissible Power Quality Levels", PQA-97