Природа подарила человечеству магнит в виде природного минерала магнетита, внешний вид которого представлен на фото1.
Химический состав этого минерала описывается формулой FeO · Fe2O3 . По сути - это феррит железа, поэтому он обладает магнитными свойствами.
Примерно семь веков до нашей эры в Европе и три века до нашей эры в Китае были найдены образцы этого минерала. Люди были поражены, обнаружив свойство этого камня притягиваться к железным изделиям. В Китае этот минерал носил название « привязчивый (нежный) камень», в Европе он получил название «камень из Магнесии» (так называлась область и город в Малой Азии, где он был найден впервые). Существует также легенда, что первым обнаружил магнитные свойства пастух по имени Магнус, железный наконечник палки которого притягивался к этому камню. В последствии этот минерал стали называть просто «магнит». В шестом веке до нашей эры о свойстве магнита притягивать железо упомянул греческий филосов Фалес. Первое практическое применение магнитных свойств магнетита нашло в создании компаса. Кусочек магнита, закрепленный на плавающей в воде дощечке, всегда показывал в одну сторону света. До нашего времени дошли сведения, что древние викинги в своих плаваниях пользовались компасом. Со временем конструкция компаса совершенствовалась: кусочек магнетита заменила игольчатая стрелка из стали, обладающей магнитными свойствами.
Лечебные свойства магнита стали также использоваться с древнейших времён. Царица Египта Клеопатра носила магнитный амулет, для сохранения молодости и красоты. В более поздние времена об благотворном влиянии магнитов писали великие врачи и философы: Аристотель, Авиценна, Гиппократ. В древнем Китае о применении магнитных камней для коррекции в теле энергии Ци - «живой силы» писалось в «Императорской книге по внутренней медицине». В средние века придворный врач Гилберт, который опубликовал сочинение «О магните», лечил от артрита королеву Елизавету 1 при помощи магнита. Использовал магнитотерапию и известный руский врач Боткин. В настоящее время магнитотерапия активно используется в Японии, США, Китае.
Толчком к совершенствованию магнитных свойств природного материала магнетита послужило открытие Эрстеда о взаимодействии электрического тока с магнитной стрелкой компаса и дальнейшие исследования Араго, Ампера, Фарадея о взаимодействии электрических и магнитных полей. Чем сильнее магнитное поле, тем эффективнее оказывалось это взаимодействие.
Первым искусственным магнитным материалом стала углеродистая сталь, содержащая около 1,2–1,5 % углерода, закалённая на структуру мартенсита. Однако магнитные свойства такой стали были чувствительны к механическим и температурным воздействиям. Наблюдалось так называемое явление «старения» магнитных свойств стали.
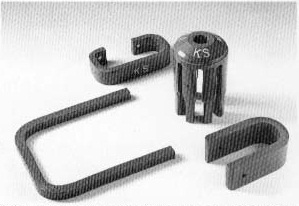
Легирование этой стали хромом до 3%, и вольфрамом, а позднее Co до 6% совместно с Cr до 6% позволило доктору Хонда из Тохокского университета создать сталь КS с высокой намагниченностью и достаточной хорошей коэрцитивной силой. Для получения высоких магнитных свойств сталь подвергалась нормализации, закалке и низкотемпературному отпуску. Высокая остаточная индукция у магнитов из такой стали достигалась уменьшением размагничивающего фактора. Для этого магниты делались удлинённой формы, а для уменьшения габаритов их изгибали в форму подковы и применяли полюсные наконечники.
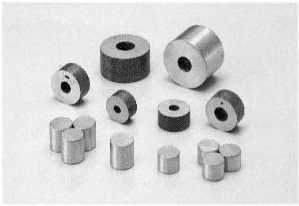
Исследования природы высококоэрцитивного состояния сплавов показали, что оно в первую очередь зависит от микроструктуры материала. В 1930 г. был достигнут прогресс в получении качественной микроструктуры твердеющих сплавов, и в 1932 году за счёт легирования стали KS никелем, алюминием и медью доктор Т. Мискима получил сталь МК.
Это был шаг к созданию ряда сплавов, получивших общее название АlNiCo (по российским стандартам ЮНДК). Совершенствование технологии позволило получить целый ряд марок магнитов, наиболее лучшие по магнитной энергии из которых (с Ti), представлены в таблице 1. (ГОСТ 17809-72)
Сплав* на основе Fe |
Содержание элемента, % | Магнитные свойства (не менее) |
||||||
Ni | Al | Co | Cu | Другие элементы | (ВН)макс, кДж/м³ | Нс, кА/м | Вr,Тл | |
ЮНДК31Т3БА | 13-14 | 6,8-7,2 | 30,5-31,5 | 3,0-3,5 | 3-3,5 Тi 0,9-1,1 Nb | 32 | 92 | 1,15 |
ЮНДК40Т8АА | 14-14,5 | 7,2-7,7 | 39-40,6 | 3,0-4,0 | 7-8 Ti 0,1-0,2 Si | 32 | 145 | 0,9 |
ЮНДК35Т5БА | 14-14,5 | 6,8-7,2 | 34,5-35,5 | 3,3-3,7 | 4,5-4,7 Ti 0,8-1,1 Nb | 36 | 110 | 1,02 |
ЮНДК35Т5АА | 14-14,5 | 7,0-7,5 | 34-35 | 2,5-3,0 | 5,0-5,5 Ti 0,1-0,2 Si | 40 | 115 | 1,05 |
• Буквы БА обозначают столбчатую кристаллическую структуру, а буквы АА – монокристаллическую.
Сплавы системы ЮНДК при обычном литье получаются изотропными, что позволяет намагничивать их многополюсно, но уровень магнитных свойств далёк от максимально возможного. Для повышения индукции насыщения сплав льют в форму с охлаждаемой подложкой для направленной кристаллизации. Дальнейшее повышение магнитных свойств достигается за счёт применения термомагнитной обработки. Последняя состоит из нагрева магнитов до 1280-1300 °С, выдержки при этой температуре для получения однофазного состояния, быстрого охлаждения до 900 °С для сохранения однофазного состояния, затем последующее медленное охлаждение в магнитном поле с Н=160-280 кА/м для наведения магнитной текстуры за счёт выделения анизотропных по форме частиц магнитной фазы с высокой индукцией насыщения вдоль направления параллельного вектору напряжённости магнитного поля . Затем проводится отпуск при Е=560 - 630 °С для получения высококоэрцитивного состояния за счёт распада первичной фазы на вторичные: α + γ.
Литые магниты не деформируются. Они характеризуются высокой хрупкостью, отсутствием ковкости и высокой твёрдостью. Для получения требуемой геометрии магнитов применяется механическая обработка их шлифованием, при которой имеет место значительные потери материала. Для изготовления небольших и точных по размеру магнитов из ЮНДК применяется технология порошковой металлургии. Отлитый сплав подвергается размолу в порошок, который прессуют в изделие требуемой формы и спекают при высоких температурах в защитной атмосфере. Спечённые магниты термообрабатывают аналогично литым. Такие магниты имеют более низкие свойства, чем литые за счёт более низкой плотности и текстуры.
Очень хорошие (но дорогие) магниты изготавливались с большим содержанием кобальта (до 50%) - «пермендур» или никеля (до 45%)- «перминвар».
Близкие по механизму магнитного твердения , но деформируемые, сплавы были получены в системе железо-кобальт без Al:Fe-Cr-Co, Fe-Мо-Co «комол» , Fe-V-Co «викаллой», Fe-Ni-Co. Кристаллическая текстура на магнитах из этих сплавов наводилась холодным деформированием (прокатом), а магнитная - термообработкой, аналогичной, как для сплавов ЮНДК.
Магниты системы ЮНДК былы лидером в производстве и потреблении, пока их не потеснили магниты из ферритов. Весь период, пока магниты ЮНДК господствовали на рынке магнитов , японские исследователи Като и Такей из Токийского университета искали более совершенный материал на основе природного магнетита. Замещение части оксида двухвалентного железа в составе магнетита на оксид кобальта при синтезе феррита по керамической технологии привела к созданию твёрдого раствора кобальтого и железного ферритов. Коэрцитивная сила такого феррита достигла 48-72 кА/м (600-900 Э).Высокие магнитные свойства кобальтого феррита достигались технологией близкой к технологии сплава ЮНДК,а именно, термомагнитной обработкой при температуре 450-500 °С в сильном магнитном поле. Пока шла Вторая мировая война японские учёные были первыми в прогрессе магнитных материалов, однако позднее учёные из фирмы Филлипс нашли бариевый феррит с гексагональной кристаллической структурой химического состава ВаОּ 6Fe2O3. В нём уже не было кобальта, а коэрцитивная сила достигла 160 кА/м (2000 Э). Отработка керамической технологии- подбор исходных сырьевых материалов, отработка режимов синтеза ферритовых порошков и помолов порошков до частиц однодоменного размера, прессование изделий из суспензии в магнитном поле, оптимизация режимов спекания изделий позволили поднять остаточную индукцию до результатов, приемлемых для потребителей. В Японии коммерческие ферритовые магниты появились в 1955 году, в России – в середине 60-тых. Позднее бариевые ферриты были модифицированы в стонциевые. Последние постепенно вытеснили бариевые, т.к. оказались более технологичными (требовали помолы до меньшей степени дисперсности, не требовали очень точной регулировки температуры спекания и являлись экологически более безопасными). В составе ферритовых магнитов содержится 85-90% оксида железа, который является отходом металлургической отрасли с установок регенерации травильных хлоридных растворов Рутнера. Такого оксида железа образуется в год сотни тысяч тонн , а ферритов производится десятки тысяч тонн в год. Сырьём для ферритовых магнитов может быть и высококачественный суперконцентрат природного магнетита, которого в мировой промышленности на порядок больше синтетического оксида железа. Безграничный источник очень дешёвого сырья и сравнительно простая технология изготовления ферритовых магнитов обеспечила им лидерство в объёмах производства и потребления. Магниты из ЮНДК были вытеснены ферритовыми в первую очередь в производстве громкоговорителей, затем в электродвигателях для автомобилей и бытовой техники, а также других применениях, где вес магнита не играет существенной роли. Только очень высокая рабочая температура (500 °С) сохраняют для магнитов из ЮНДК нишу для их потребления.
В поисках материалов с высокой коэрцитивной силой были найдены такие сплавы, как «висмутит» - сплав Ag-Mn-Al (Нс=5000Э) и Pt-Co, содержащие драгоценные металлы. Эти сплавы не вышли из рамок опытного производства, в силу дороговизны и потому, что в лаборатории U.S.Air Force Material Research было найдено интерметаллическое соединение с большой константой магнитокристаллической анизотропии. Это - соединение самария с кобальтом: SmCo5 . Из него изготовили магнит. Очень быстро были достигнуты свойства (ВН)макс=16-24 МГсЭ , а на соединении Sm2Co17 - 32 МГсЭ, коэрцитивная сила была поднята до 560 – 1000 кА/м. Магниты из SmCo начали производиться промышленно в 1980-ых годах. В это же время было найдено соединение Nd2Fe14B. Магниты из этого материала появились в Японии и США одновременно в середине 1980-тых годов, но технология их производства отличались. В Японии производство организовывалось по типу магнитов SmCo: производство порошка из литого сплава, затем прессование в магнитном поле и спекание. В США был принят Meltspinning process: сначала производится аморфный сплав, затем он превращается в порошок, из которого изготавливается композиционный материал (bonded- связанный). Магнитный порошок связывается резиной, винилом, нейлоном или другими пластиками в компактную массу, которую прессуют (инжектируют) или каландруют в изделия. Магниты из композиционного материала имеют более низкие свойства, чем спечённые, но не требуют гальванических покрытий, легко обрабатываютя механически, зачастую имеют красивый внешний вид окрашенный в различные цвета. Магниты из Nd2Fe14B появились на рынке постоянных магнитов в 1990-ых годах и очень быстро достигли на спечённых образцах энергии в 50 МгсЭ (400 кДж/м3). Этот материал быстро вытеснил другие, в первую очередь - в миниатюрной электронике.
Магнитотвёрдые материалы на основе редкоземельных металлов обладают более высокими магнитными параметрами по сравнению с магнитами из ЮНДК за счёт высокой коэрцитивной силы, а по сравнению с ферритами - за счёт высокой остаточной индукции. Основная магнитная характеристика (ВН)макс у типичных магнитов из NdFeB в 10 раз выше (310-330 кДж/м3), чем у ферритовых (28-32 кДж/м3), поэтому, везде где требуется уменьшение веса и габаритов магнитов применяются магниты из NdFeB: сотовые мобильные телефоны, микронаушники, персональные ноутбуки и т.д. Магниты из SmCo превосходят ферритовые по магнитной энергии в 5 раз, но дороже последних в 12 раз. Поэтому вытеснить ферритовые магниты с рынка самариевым магнитам не по силам.
В таблице 2 представлено сравнение основных характеристик лучших магнитов из разных материалов.
Материал | Марка | Вr, кГс | Нсj, кЭ | Нсв, кЭ | (ВН)макс, МГсЭ | Тмакс.Раб., °C |
NdFeB | N42 | 12,6 | 17 | 11,6 | 40 | 120 |
SmCo | 26 | 10,6 | 15 | 9,3 | 26 | 300 |
NdFeB | B10N | 6,8 | 9,1 | 5,8 | 10 | 150 |
AlNiCo | 5 | 12,5 | 0,64 | 0,64 | 5,5 | 540 |
Ceramic | 8 | 3,9 | 3,25 | 3,2 | 3,5 | 300 |
Flexible | 1 | 1,6 | 1,38 | 1,37 | 0,6 | 100 |
На рис. 1 представлена динамика продаж (в иенах) японской продукции из разных магнитных материалов в период 1950 – 2000 года.
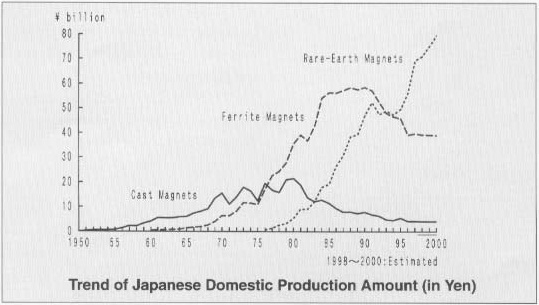
Достигнув максимума в 70-80 годах продажи магнитов из AlNiCo быстро снизились до уровня 1960 г., однако у этих магнитов есть достоинство – высокая рабочая температура = 500 °С, которая оставляет для них нишу применения. Ферритовые магниты достигнув пика своего производства в 1985-1995 годах тоже пошли на убыль. У этих магнитов также есть свои достоинства: высокое электрическое сопротивление, позволяющее работатьв ВЧ- и СВЧ- приборах, дешевизна и рабочая температура до 300 °С, позволяющая использовать их в электродвигателях и электрогенераторах. Магниты из NdFeB быстро вытесняют другие материалы , если применение ограничивается «комнатными» температурами (-30 °С÷ +30 °С).
Аналогичная динамика характерна для всего мирового рынка магнитов.
На рис. 2 представлена диаграмма развития разных магнитотвёрдых материалов в период 1920 -2000 г.г. Скачки на отдельных участках кривых соответствуют появлению новых видов МТММ или новых марок этих материалов.
Помимо совершенствования магнитных свойств МТММ шло совершенствование и их механичеких свойств. Большим достижением в этом направлении оказалось создание композиционных материалов «Flexible», при этом, если в качестве связующих веществ исползуются пластические материалы винил или найлон, то материал называется «bonded» - cвязанный), если резина, то «rubber». Достоинством магнитопластов является возможность получения сложных форм изделий с высокой точностью размеров, высокая коррозионная устойчивость в сочетании с большой величиной удельного сопротивления и малым весом. Уровень магнитных свойств зависит от природы магнитного порошка – наполнителя композиционного материала. В таблице 3 представлены сравнительные уровни свойств композиционных материалов с разными связующими и текстурой.
Материал | (ВН)макс, МГсЭ | Вr, кГс | Нсв, кЭ | Плотность, г/см³ |
Flexible 0,6 (c ферритом изотропный) | 0,6 | 1,73 | 1,33 | 3,8 |
Flexible 1,6 (c ферритом анизотропный) | 1,6 | 2,65 | 2,2 | |
Rubber Magnet (изотропный) | 1 | 1,9 | 1,2 | |
Rubber Magnet (анизотропный) | 2,6 | 1,85 | 1,3 |
Наличие на рынке большого спектра промышленно выпускаемых магнитотвёрдых материалов с широким спектром магнитных свойств позволяет обеспечить практически все потребности технического применения, а высокий уровень магнитных свойств при относительной дешевизне магнитов из NdFeB или его композиций дало толчёк к массовому применению изделий с магнитными свойствами в быту: магнитных развивающих игр - конструкторов, магнитной бижутерии, магнитных аппликаций в разного рода бандажах и т.д. На фото 2 представлены варианты композиций из прекраснейшей в своём роде игрушки - кубика из 216 магнитных шариков, так называемого NEOCUBE. Приобретя такое изделие, каждый может играя, физически почувствовать, что такое магнитное поле, и насколько далеко продвинулось человечество в совершенствовании свойств магнитных материалов.