Производство марганец- цинковых ферритовых сердечников для электронной промышленности
Saw Mya Ni, and Kay Thi Lwin, перевод Федоров А.Е.
Реферат - керамические ферриты или магнитные материалы представляют собой твердые расстворы выбранных оксидов с оксидами железа. Наиболее распространены магнито-мягкие материалы, Mn-Zn и Ni-Zn ферриты, имеющие общую AB2O4 структуру. Марганец-цинковый феррит является предпочтительным для применения в технике СВЧ при частотах менее 2 МГц, тогда как Ni-Zn феррит является предпочтительным для применения при более высоких частотах в основном для силовых трансформаторов и индукторов мощности. Микроструктура и свойства керамических ферритов в решающей степени зависит от условий обработки. Физические свойства и характеристики спекания (Mn(1-х)Znx)Fe2O4 были проверены для эквимолярного состава, х = 0,5, при трех условиях спекания, три спекания (1100, 1200 и 1300 ° C) и трех периодов продолжительности спекания (1 час, 2 часа и 3 часа). Методами рентгеновского анализа и сканирующей электронной микроскопии были идентифицированы структуры марганец-цинковых ферритов. Физические свойства, плотность, усадка образца и пористость изучались одномерным методом и методом кипящей воды.
Ключевые слова-порошковая металлургия, марганец-цинковый феррит, (Mn (1-х)Znx)Fe2O4.
I. ВВЕДЕНИЕ
Сегодня, магнитные материалы можно найти в многих продуктах по всему миру: в бытовой технике, электронных продуктах, автомобилях, оборудовании связи и устройствах обработки данных. Эти материалы сейчас стали важной частью повседневной жизни и современной промышленности. Вначале применяли металлические магнитные материалы. Но для частот, превышающих 1 МГц, металлы и сплавы, как правило, не подходят в качестве мягких магнитов, а потери на вихревые токи очень высоки. Изучение ферритов с 1946 года показало, что электрическое сопротивление ферритов более чем в миллион раз выше, чем у металлов, что имеет огромное влияние в области применения магнитных материалов особенно на высоких частотах. Ферриты используются сегодня в радио и телевизорах, микроволновых печах и спутниковой связи, аудио-, видео- и цифровой записи и в качестве постоянных магнитов.
II. МЕТОДИКА
Методика эксперимента Mn-Zn феррита проводится следующим образом:
Подготовка материала –>Взвешивание–>Смешение–>Добавление вяжущего–>Прессование–>Спекание–>Анализ результатов
Сырье
В качестве сырья для производства марганец-цинковых ферритов использовались диоксид марганца (MnO2), оксид цинка (ZnO) и оксид железа (Fe2O3). Смешивали оксиды технического класса MnO2, ZnO и Fe2O3 чистота которых 93,22%, 84,54% и 80,33%. MnO2 соответственно, поскольку MnO труднодоступен на местном рынке. MnO2 (-270#) соединяли с коксом высокого качества (248 + 65 #) в восстановительной атмосфере. Для производства Mn-Zn ферритов был использован метод порошковой металлургии. Сырье (MnO, ZnO, Fe2O3) сушили и взвешивали в стехиометрическом соотношении, а затем смешивали в среде ацетона в течении 122 часов для тщательного и равномерного смешивания. 3% -й раствор ПВА добавляют в качестве связующего для улучшения уплотнения для смешанного порошка и 5%-й раствор PEG добавляют в качестве смазки для уменьшения трения. Готовый порошок подают на гидравлический пресс (30 МПа давления) и спекают при высокой температуре в муфельной печи, при трех различных температурах спекания 1100 ° C, 1200 ° С и 1300 ° С и трех интервалах времени спекания 1ч, 2ч и 3ч, соответственно, в целях достижения желаемых физических свойств и низкой пористости. Спеченные гранулы исследовались рентгеновским анализом и сканирующей электронной микроскопией для идентификации фазового состава. Физические свойства, плотность и усадка измерялись соответствующими методами. Пористость измерялась методом кипящей воды. Электрические и магнитные свойства, сопротивление, относительная проницаемость, намагниченность, коэрцитивная сила, остаточная, плотность магнитного потока, напряженности магнитного поля также были измерены.
III. Результаты и их обсуждение
Рентгеновский дифракционный анализ был использован для получения характеристик фаз. Фаза MnO была подтверждена рентгеновским дифракционным анализом (РДА), результат показан на рис. 1.
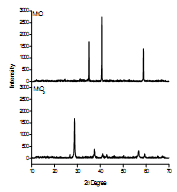 Рис. 1 Сравнение РДА исходных образцов порошков MnO и MnO2
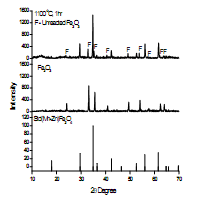 Рис. 2 Сравнение РДА исходных образцов порошков Mn-Zn ферритов спеченных при 1100°С в течение 1 часа со стандартной базой данных.
Следующие графы рентгенограммы Mn-Zn феррита показывают результаты спекания при различных температуре и времени. Рис. 2 показывает рентгеновский дифракционный анализ Mn-Zn феррита спеченного при 1100°С в течение 1 часа. Наблюдалась непрореагировавшая фаза Fe2O3, что позволяет сделать вывод: температура и время спекания не являются достаточными.
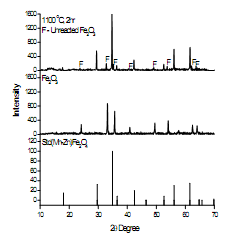 Рис. 3 Сравнение РДА исходных образцов порошков Mn-Zn ферритов спеченных при 1100°С в течение 2 часов со стандартной базой данных.
Рис. 3 показывает РДА Mn-Zn феррита спеченного при 1100 ° С в течение 2ч. При этих условиях наблюдалась фаза непрореагировавшего Fe2O3. Это позволяет сделать вывод: температура 1100 ° С и время спекания 2ч. не являются достаточными.
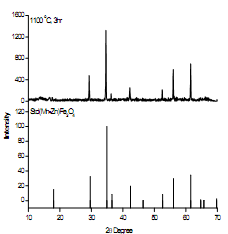 Рис. 4 Сравнение РДА исходных образцов порошков Mn-Zn ферритов спеченных при 1100°С в течение 3 часов со стандартной базой данных.
Рис. 4 показывает РДА Mn-Zn феррита спеченных при 1100 ° С в течение 3ч. При этих условиях наблюдалось формирование структуры шпинели.
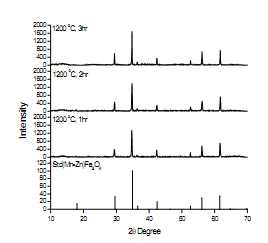 Рис. 5 Сравнение РДА исходных образцов порошков Mn-Zn ферритов спеченных при 1200°С в течение 1-го 2-х и 3-х часов со стандартной базой данных.
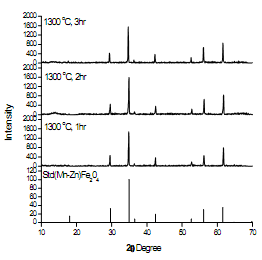 Рис. 6 Сравнение РДА исходных образцов порошков Mn-Zn ферритов спеченных при 1300°С в течение 1-го 2-х и 3-х часов со стандартной базой данных.
Рис. 5 показывает РДА Mn-Zn ферритов спеченных при 1200 ° С в течение 1-го, 2-х и 3-х часов. При этой температуре, образование шпинельной фазы было подтверждено на всех интервалах времени спекания. Рис. 6 показывает РДА Mn-Zn ферритов спеченных при 1300 °С в течение 1-го, 2-х и 3-х часов. При этой температуре, образование шпинельной фазы было подтверждено на всех интервалах времени спекания. Оптимальные условия для спекания Mn-Zn ферритов наблюдались при 1300 ° С в течение 3 ч, согласно показаниям РДА.
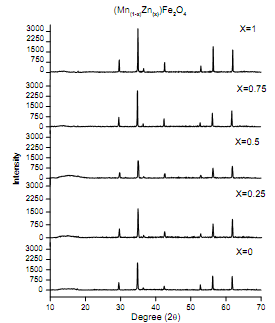 Рис. 7 Сравнение РДА образцов Mn-Zn ферритов сложной формы, спеченных при 1300°С в течение 1-го 2-х и 3-х часов со стандартной базой данных.
На рис. 7 показано Сравнение РДА образцов Mn-Zn ферритов сложной формы, спеченных при 1300°C в течение 1-го 2-х и 3-х часов со стандартной базой данных. На основании результатов можно сделать вывод, что оптимальные условия спекания (Mn(1- х)Zn(х))Fe2O4 при х = 0,5 1300 ° С в течении 3 часов. Результаты измерения физических свойств представлены на рис. 9-12. Графики, изображенные на рисунке показывают увеличение плотности и усадки спеченных гранул с увеличением времени и температуры спекания. Но пористость имеет обратный характер зависимости (рис. 12). Все эти графики подтверждают, что физические показатели увеличиваются с увеличением времени спекания и температуры. Максимальная температура спекания 1300 ° С и время спекания 3 часа дает 94% от теоретической плотности для (Mn(1- х)Zn(х))Fe2O4, х = 0,5.
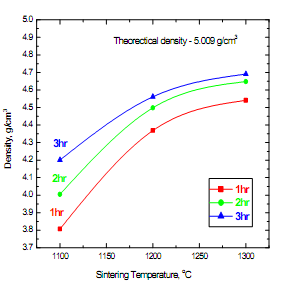 Рис. 8 Изменение плотности при различных условиях спекания Mn-Zn феррита
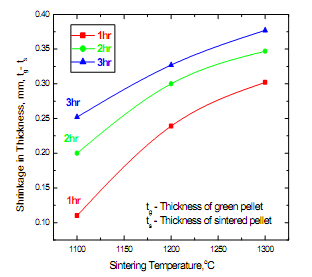 Рис. 9 Изменение уменьшения диаметра спеченных гранул при различных условиях спекания
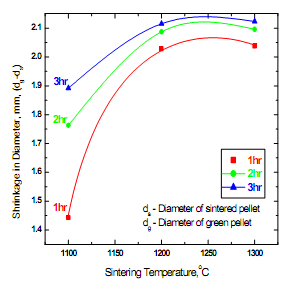 Рис. 10 Изменение усадки в толще спеченных гранул при различных условиях спекания
 Рис. 11 Изменение пористости в разных условиях секания для Mn-Zn ферритов. Идентификация шпинельной фазы проводилась методом сканирующей электронной микроскопии.
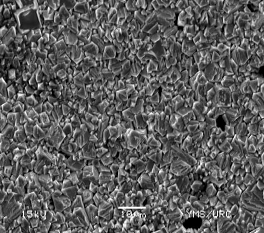 Рис. 12 SEM Микрофотография Mn-Zn ферритов, спеченных при 1200°C и 3 часа по 10µ шкале
Рис. 12 показывает электронную микрофотографию феррита спеченного при 1200 ° С и 3 часа при 10µ масштабе. Средний размер зерна составляет 3,2µ.
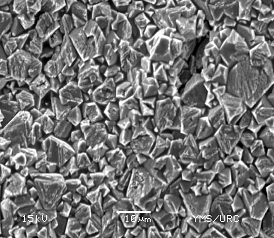 Рис. 13 SEM Микрофотография Mn-Zn ферритов, спеченных при 1250°C и 2 часа на 10µ шкале
Рис. 14 показывает электронную микрофотографию ферритов, спеченных при 1250 °С и 2 часа при 10µ масштабе. Средний размер зерна составляет 4 µ. Пористость уменьшается с увеличением времени спекания и температуры. Средний размер зерна составляет 4 µ.
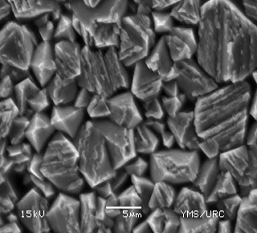 Рис. 14 SEM Микрофотография Mn-Zn ферритов, спеченных при 1250°C и 2 часа на 5µ шкале
Рис. 15 показывает электронную микрофотографию ферритов, спеченных при 1250 °С и 2 часа с 5µ масштабе, чтобы увеличить морфологию поверхности.
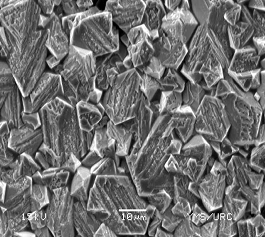 Рис. 15 SEM Микрофотография Mn-Zn ферритов, спеченных при 1300°C и 3 часа на 10µ шкале
Рис. 16 показывает электронную микрофотографию ферритов, спеченных при 1300 ° C и 3 часа 10µ шкале. Средний размер зерна составляет 6,9 µ. При увеличении времени спекания и температуры, увеличение роста зерна и средний размер зерна увеличивается с 3,2 µ на рис. 13, до 6,9 µ на рис. 16.
Магнитные свойства
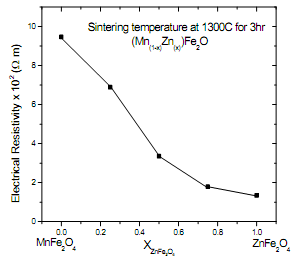 Рис. 16 Изменение электрического сопротивления Mn-Zn ферритов.
Изменение электрического удельного сопротивления (ρ) при увеличении содержания цинка феррита, при комнатной температуре, представленный в Рис. 17. Очевидно, что электрическое удельное сопротивление уменьшается быстро, при добавлении цинка в феррит.
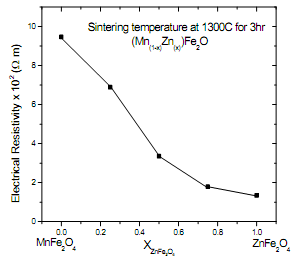 Рис. 16 Изменение электрического сопротивления Mn-Zn ферритов.
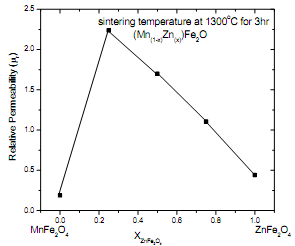 Рис. 17 Изменение относительной проходимости при различном содержанием марганца и цинка в феррите.
Зависимость относительной проницаемости при комнатной температуре представлена в Рис. 18. Максимально схожая проницаемость (Mn(1-х)Znx)Fe2O4 наблюдался в ZnFe2O4 состава 0.25. Типичная петля гистерезиса Mn-Zn феррита, замеренная осциллографом, представлена на Рис. 19. Получены следующие показания магнитных свойств марганец-цинкового феррита: высокая проницаемость, небольшая коэрцитивная сила, малый остаточный магнетизм, малая петля гистерезиса, быстрый ответ в высокочастотном магнитном поле и низкое электрическое сопротивление.
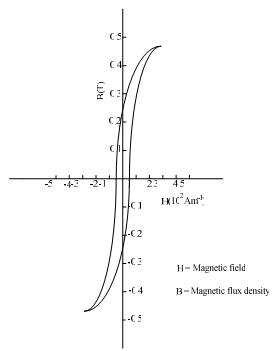 Рис. 18 Типичная петля гистерезиса марганец-цинкового феррита.
IV. ЗАКЛЮЧЕНИЕ
Были изучены особенности спекания и физические свойства феррита методом рентгено-дифракционного анализа и просмотром на электронном микроскопе. Изучено изготовление марганец-цинковых ферритов в различных условиях. Оптимальное условие спекания – температура 1300ºC и время 3часа. Плотность и усадка шариков образцов увеличиваются с увеличением времени спекания и температуры. Максимально схожая проницаемость проходимость (Mn(1-х)Znx)Fe2O4 наблюдался в ZnFe2O4 состава 0.25. Пористость уменьшается с увеличением времени спекания и температуры. Электрическое удельное сопротивление MnFe2O4 уменьшается быстро при добавлении цинка в феррит. Магнитные свойства марганец-цинкового феррита находятся в диапазон стандартных величин. Природа B-H кривой также согласуется с стандартной природой B-H зависимости (Mn(1-х)Znx)Fe2O4.
Ссылки
[1] Heck, C. 1974. Magnetic Materials and their Applications. London: Butterworths
[2] Donald R. Askeland. 1994. The Science and Engineering of Materials. 3rd ed.Bostom: PWS Publishing Company.
[3] William .D.Callister, Jr. 1994. Materials Science and Engineering.
[4] Carl A.Keyser. 1986. Materials Science in Engineering
[5] Roberts. J. 1960. High Frequency Application of Ferrites
[6] David Jiles, 1998. Introduction to Magnetism and Magnetic Materials. 2nd ed.U.S.A.: A CRC Press Company.
[7] By Thomas G. Reynolds. No Date. Ferrites.
[8] Kingery. W. D., Bowen. H.K, Uhlmann D.R. 1976. Introduction to Ceramics.
|