Выбор и обоснование параметров дискового тормозного устройства шахтной подъемной машины
Н.А. Скляров, канд. техн. наук, проф.,
Донецкий национальный технический университет
Источник: http://www.nbuv.gov.ua/.../St18_19.pdf
Проблема и её связь с научными и практическими задачами
В сложной цепи операций, связанных с добычей угля, важное место
занимают подъемные установки. Общая тенденция к повышению
концентрации производства, необходимость перехода к разработке
более глубоких горизонтов накладывают свой отпечаток на характер
развития и совершенствования оборудования шахтного подъема [1].
Значительные резервы повышения производительности шахтно-
го подъема состоят в увеличении емкости и скорости движения
подъемных сосудов, сокращении времени переходных процессов (за-
медления, ускорения), совершенствовании конструкции подъемных
машин и систем управления электроприводом подъема.
За последние тридцать лет в нашей стране максимальная ско-
рость движения сосудов шахтных подъемных установок увеличилось
в 1,4 раза и достигла 12 м/с, глубина подъема - в 1,8 раза и составляла
на ряде шахт 1500-2000 м, грузоподъемность сосудов - в 3 раза и дос-
тигла для угольных шахт 30 т, для железорудных - 50 т. Предполага-
ется, что в ближайшие годы глубина подъема, скорость движения и
полезная емкость сосудов будут возрастать более интенсивно. Проек-
тируются шахтные подъемные машины с емкостью скипа 50 т для
угольных и 100 т для железорудных шахт [2].
выступают вопросы их безопасной эксплуатации. Известно, что ос-
новным средством защиты подъемной установки от аварии является
его тормозная система.
Для обеспечения нормальной эксплуатации подъемные машины
обеспечиваются надежно действующими тормозными устройствами,
которые должны останавливать машину и груз на определенном пути
торможения и удерживать его в подвешенном состоянии при задан-
ном запасе торможения и заданном значении замедления.
Анализ исследований и публикаций
Значение эффективности
тормозных устройств возрастает в связи с интенсификацией произ-
водства, увеличением движущихся масс, скоростей движения и час-
тоты торможения. В современных подъемно-транспортных машинах
тормоза на протяжении короткого периода времени должны превра-
щать в тепловую энергию значительное количество механической
энергии и передавать ее в окружающую среду без снижения работо-
способности тормоза и машины в целом [2].
Не случайно в последние годы много исследователей уделяют
особое значение изучению динамических процессов, протекающих в
элементах тормозной системы и подъемной установки в режимах
торможения. Большой вклад в решение проблемы обеспечения без-
аварийной эксплуатации шахтных подъемных установок внесли
Е.С.Траубе, А.Г.Степанов, Н.Г.Гаркуша, А.Н.Шатило, Л.В.Колосов,
А.А.Белоцерковский, А.П.Нестеров и другие ученые.
Постановка задачи
Целью настоящей работы является обос-
нование и разработка рациональной схемы тормозного устройства
шахтной подъемной машины, обеспечивающего увеличение срока
службы тормозного устройства примерно на 30 %.
Изложение материала и результаты
Повышение надежности
и эффективности использования тормозных устройств подъемно-
транспортных машин проходит по следующим основным направле-
ниям: конструктивное усовершенствование механической части и
привода существующих тормозов и создание новых конструктивных
разновидностей тормозных систем; разработка и применение новых
материалов с повышенными фрикционными свойствами; широкое
использование достижений науки в трении и износах; применение
новых методов расчета тормозных устройств и фрикционных мате-
риалов и др.
Для определения тормозного момента должны быть известны:
назначение и режим работы механизма; конструктивные и расчетные
данные механизма (масса отдельных элементов, моменты инерции
элементов механизма, скорости движения); место установки; крутя-
щий момент, действующий на тормозном валу при торможении, с учетом потерь в элементах механизма от рабочего органа до тормоз-
ного вала; частота вращения тормозного вала. При применении лен-
точных и некоторых других конструкций скоростных тормозов нуж-
но знать также направление вращения тормозного шкива при
торможении.
По конструктивным исполнениям рабочих элементов тормозные устройства разделяют на колодочные - с рабочим элементом в
виде колодки, которая трется по внешней или внутренней поверхно-
сти тормозного барабана; ленточные – с рабочим элементом в виде
ленты трущейся по тормозному барабану; дисковые- с рабочим эле-
ментом в виде целых дисков или отдельных сегментных колодок; ко-
нические - с рабочим элементом в виде конуса.
Дисковые тормоза разделяют на однодисковые; многодисковые
без усиления; многодисковые с усилением; автоматические, которые
замыкаются под действием веса транспортируемого груза.
К преимуществам дисковых тормозов относятся:
- большая энергоемкость (известная многодисковый тормоз
авиационного колеса с энергией разового торможения 33*106 Дж;
удельная энергоемкость дисковых тормозов составляет (17-25) 104
Дж на 1 кг массы тормоза;
- большие тормозные моменты при сравнительно небольших
размерах самого тормоза (за счет увеличения числа пар поверхностей
трения, например, встроенный дисковый тормоз с внешним диаметром дисков 548 мм может создавать тормозной момент, равный 40
050 Нм);
- стабильность работы, практически линейная зависимость
тормозного момента от коэффициента трения (только в тормозах без
самоусиления);
- большая суммарная площадь поверхности трения (получаемая
путем увеличения числа поверхностей трения), что разрешает
уменьшить необходимое давление между поверхностями трения и таким образом, повысить долговечность фрикционных пар;
- уравновешенность тормоза - осевые силы могут быть замкнуты внутри тормоза и не воспринимаются валом и подшипниками ма-
шины;
- трения по плоскости, которая обеспечивает равномерное распределение давления по всей поверхности трения, а итак, и более рав-
номерное изнашивание, чем при тертые по цилиндрической поверх-
ности;
- незначительное изменение площади фактического контакта
тормозной накладки при увеличении размеров элементов трения (в
основном об осевом направлении) вследствие нагревания в процессе
работы;
- независимость тормозного момента вот направления обраще-
ния тормозного вала.
На основе всестороннего анализа достоинств и недостатков
тормозных устройств различных типов и исполнений экспертным
методом для современной многоканатной подъемной машины выбра-
но дисковое устройство, приводные элементы которого работают с
применением рабочей жидкости при рабочем и предупредительном
торможении (рис.1).
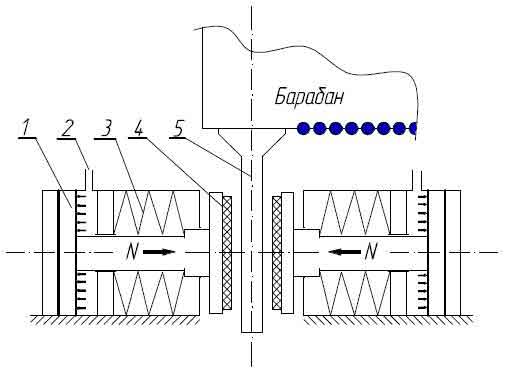
Рисунок 1 - Схема приводного элемента дискового тормозного устройства
В приводных элементах дискового тормозного устройства тор-
мозное усилие создается предварительно сжатыми тарельчатыми
пружинами 3, которое через поршень 1 передается непосредственно
на тормозные колодки 4. Для растормаживания по трубопроводам 2
подается рабочая жидкость под давлением под поршень 1. Тормозные
элементы комплектуются попарно для взаимного уравновешивания.
Комплекты пружин каждого тормозного элемента должны развивать
одинаковые усилия и иметь одинаковую твердость, чтобы в процессе
работы не возникало неуравновешенное усилие, которое нагружает
диск 5.
Достоинством схемы является простота конструкции тормозно-
го элемента, небольшие габаритные размеры, несложная система
подведения рабочей жидкости, сравнительно легкое обеспечение
герметичности, простота обслуживания и ремонта.
По этой схеме выполнено большинство тормозных элементов
(фирмы ASEA, GHH, "Сименс", EPR и др.), которые на практике под-
твердили свою надежность.
Были выбраны основные параметры дискового тормозного уст-
ройства и определены их числовые значения: усилие нажатия пру-
жин; количество тормозных элементов; размеры и техническая ха-
рактеристика пружин тормозного элемента; размеры цилиндра и
штока; давление рабочей жидкости.
На многоэлементных дисковых тормозных устройствах приме-
няются тормозные колодки в виде кольцевого сектора, прямоуголь-
ника, круга (рис. 2).
Для исключения влияния дискового тормоза на главный вал
подъемной машины необходимо, чтобы количество приводных эле-
ментов было всегда четным, и располагались бы они попарно с диа-
метрально противоположных сторон диска. Для подъемной машины
Ц-3,5х2А принимаем усилие нажатия, развиваемого пружинами од-
ного цилиндра в положении «Заторможено» P = 100кН. Тогда тор-
мозное усилие, развиваемое одной парой элементов составит:
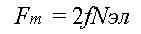
(1)
гдеFт - тормозное усилие , которое создается парою приводних эле-
ментов (парою цилиндров), H; f - коэффициент трения материала о метал; Nэл - усилия нажатия на тормозной элемент, который развивается
штоком, H.
Тормозное усилие Fт при коэффициенте трения 0,4 составляет
80 кН.
Тогда тормозной момент, создаваемый парою приводных эле-
ментов, установленных с противоположных сторон тормозного ди-
ска рассчитаем по формуле:
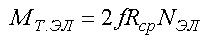
(2)
где МТэл - тормозной момент, создаваемый парою приводних елеме-
нтов, Нм; Rср - средний радиус тормозного диска,м.
При среднем радиусе тормозного диска Rср = 2 м тормозной
момент составит 160000 Нм.
Необходимое количество пар приводних элементов определяют
по формуле:
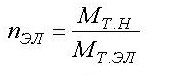
(3)
где Mтн - необходимый тормозной момент, создаваемый при пред-
варительном торможении подъомной машини, Нм (согласно ГОСТ
12.2.112-86 [3] Mтн =1050000Нм), а количество пар приводных эле-
ментов составит 6,56 ,принимаем nэл 8 штук.
На многодисковых тормозах рекомендуется принимать давление
10-20 МПа. Диаметры цилиндра и штока рассчитывются соответст-
венно по формулам:
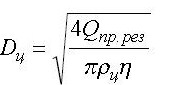
(4)
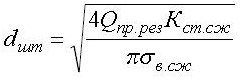
(5)
где Qпр.рез - максимальное усилие, действующее на поршень, разви-
ваемое в конце на поршень в конце его хода, Н; sв.сж - предельное напряжение материала штока на сжатие, H/cм2; Кст.сж - запас прочности штока в период сжатия; rц - давление масла в цилиндре, Па;h - коэффициент поленого действия приводного элемента.
Необходимая площадь поршня (теоретическая):
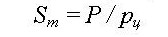
(6)
С учетом к.п.д
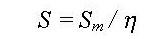
(7)
Площадь поршня с учетом диаметров цилиндра Dц и штока dшт
составляет:
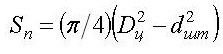
(8)
Усилие, развиваемое поршнем:
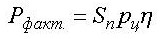
(9)
Для реализации преимуществ дискових многоэлементных тор-
мозных устройств необходимы фрикционные материалы високого
качества. В данном случае выбран металлокерамический материал
на железной или медной основе с коэффициентом трения 0,4, который
имеют в сравнении с асбокаучуковыми и асбобакелитовыми ряд пре-
имуществ:
- допускают значительно большее удельное давление ;
- имеют более високий и стабильный коэффициент трения;
- допускают высокую температуру нагрева;
- имеют значительно большую теплопроводность.
На рис. 2 представлена возможная геометрия тормозного элемента.
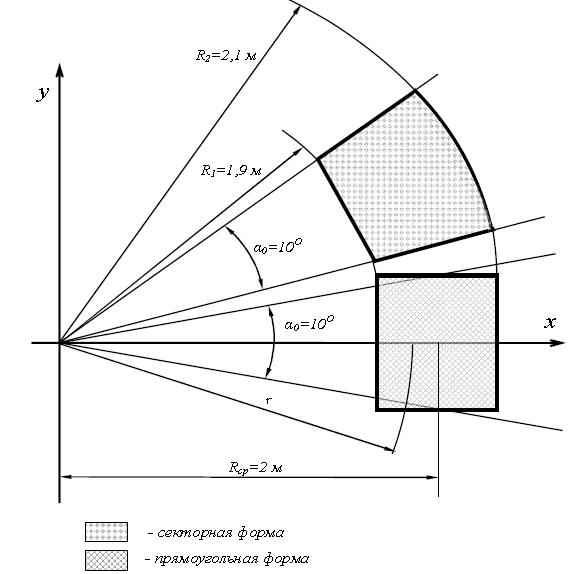
Рисунок 2 – Геометрия тормозного элемента прямоугольной и секторной формы
Принимаем тормозной элемент секторной формы и рассчитыва-
ем его площадь по формуле:
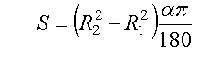
(10)
Распределение давления прижатия тормозного элемента к диску
представлено на рис. 3. Минимальное давление Pmin =1,4 МПа.
Был выполнен расчет нагрева тормозного элемента по специ-
альной математической программе Maple v9.5. При этом были приня-
ты следующие допущения:
- тепловой поток, который подводится к тормозному диску, рас-
пределяется равномерно по кольцевой поверхности трения, а поток,
который подводится к фрикционным накладкам – равномерный по их
площади трения;
- тепловой поток, который возникает на поверхности трения –
линейный и направленный по нормали к поверхности трения.
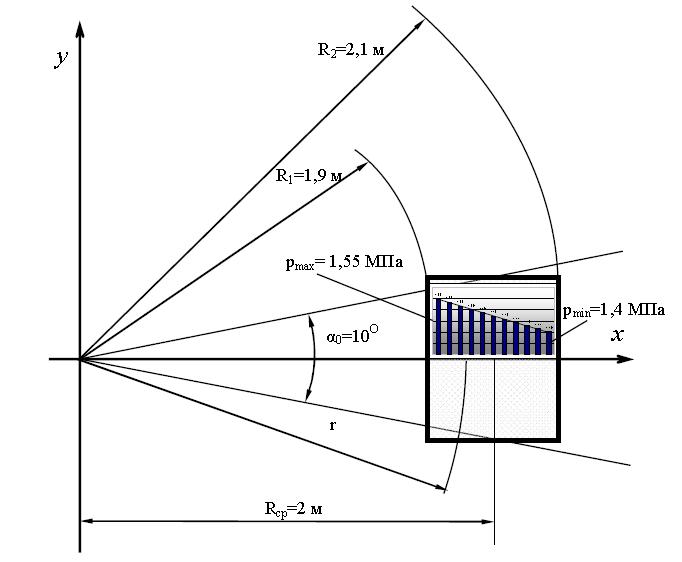
Рисунок 3 – Распределение давления прижатия тормозного элемента
Выводы и направления дальнейших исследований
Таким об-
разом, в результате сравнительного анализа различных схем и конст-
рукций тормозных систем была предложена схема и рассчитаны ос-
новные параметры дискового тормозного устройства шахтной
подъемной машины Ц-3,5х2, а именно: для создания необходимого
тормозного момента 1050 кНм определено количество тормозныхэлементов, которое составило 16 штук; для обеспечения усилия при-
жатия тормозной колодки в 100кН расчетный диаметр тормозного
цилиндра составил 129 мм, штока – 40 мм; определено максимальное
давление на тормозную колодку при наибольшем прижатии её к тор-
мозному диску в 1,55 МПа, которое находится в допустимом преде-
лах для выбранного фрикционного материала «металлокерамика на
железографитной основе»; расчетная температура во время торможе-
ния на поверхности трения при пятисекундном торможении состави-
ла 134,5°С для тормозной колодки и 109,7°С – для тормозного дис-
ка, что не превышает максимально допустимой для выбранного
фрикционного материала. При этом срок службы тормозного устрой-
ства увеличивается с 18 месяцев для колодочного тормозного устрой-
ства до 23,4 месяцев для дискового тормозного устройства.
В дальнейшем, с целью уточнения полученных данных, плани-
руется провести экспериментальные исследования на реальной подъ-
емной машине.
Список литературы
- Липаков А.Н. Новые тормозные системы для рудничных локомотивов / А.Н. Липаков //
Вопросы рудничного транспорта. - №13. - С.198-206.
- Александров М.П. Тормозные кстройства: справочник / М.П. Александров. – М.: 1984.
- Транспрт электровозный рудничный: общие требования безопасности , ГОСТ 12.2.112-
86 - 10 с.
НАЗАД К БИБЛИОТЕКИ