Problem and its link with scientific and practical problems.
One of the most labour-consuming operations executable by load-lifting machine, its loading cargo-carried organ material call-off quantity is. For loose materials this problem in the best way dares application grab bucket to which loading process goes automatically.
Grab cranes and loaders are widely applied at loading, unloading and piling operations in the industry and on transport, and also to the special technological purposes — passings of vertical trunks of shafts, lifting of the blown up muck from open test pits etc. In metallurgical and a machine industry grab buckets are applied to preparation and charge supply. In building grab buckets apply on excavation work.
In many books and scientific articles in view of complexity of the processes proceeding during working by grab buckets, the mass of assumptions, simplifications in the questions linked with calculation of a construction is accepted. Dependences have empirical character, are extremely inaccurate, contain assemblage of the factors gained by practical consideration. Therefore researches in the field of a justification of rational parametres of grab buckets represent scientific and practical interest. Investigating processes, refine dependences, factors, it is possible to gain an essential positive effect: decrease of power consumption, specific consumption of materials, costs on service.
The analysis of researches and publications.
In connection with an intensification of manufacture and a high scale of mechanization of operations, at the factories and loading platforms of the country the grab bucket find worthy application. The majority of them is replaceable load-handing organ and are used on cranes of different types that raise universality of cranes. Such ample opportunities on application force to give a lot of attention the researchers, aimed to rationalize available samples, to search new ways of the solution of problems. The big contribution to the solution of questions and problems by calculations of the grab bucket have brought in A.A.Vajnson, R.L.Zenkov, B.A.Tauber, Y. M.Tashnikov, N.A.Shevchenko, And. M.Jasinovsky, etc.
Sweetly to note, that the Ukrainian scientists became the initiators of working out of GOST 24599-87 "grab buckets the rope for bulk cargoes. General-technical conditions". A.M.Jasinovsky was the Project head.
Statement of problem.
The purpose of the research is the justification of parameters of the grab bucket for raise of efficiency of its(his) use. Having carried out research on agency of geometrical parameters of the rope grab bucket on force in a closing rope, it is possible to judge rational values of these parameters and to give concrete recommendations by definition grab bucket parameters at projection and manufacture.
Account of a material and results.
To the basic processes which are passing in a time in use of the grab bucket refer to: depressing of the open grab bucket on a material, filling up grab bucket by material, lifting and migration of the loaded grab bucket, opening of the filled grab bucket.
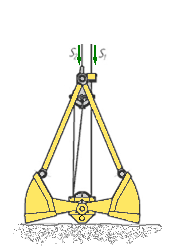
Figure 1 — Process of operation of the rope grab bucket
In a time in use on a construction act static and the dynamic loads, which definition it is rather inconvenient. Practical interest represents agency of parameters of the grab bucket on operation process, and power consumption as its performance. Definition of dependences between parameters and power consumption will allow to size up their agency quantitatively.
For a subject of research the commercial machine of the two-rope grab bucket in capacity 1,5 m3 is chosen. The grab bucket is intended for capture and an overloading of loose cargoes. The general view is presented in a Fig. 2.
In a Fig. 3 the design scheme of the grab bucket used in given researches is figured. In figure geometrical parameters are marked out: sizes, characteristic angles, shoulders of forces.
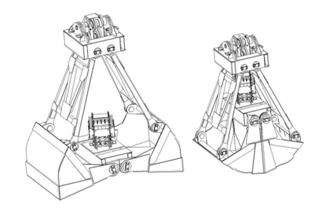
Figure 2 — Grab bucket general view
Research objective is definition of agency on power consumption of process of filling by material of geometrical parameters of the grab bucket:
- p — length of side crimp of the grab bucket, m;
- r — distance between jaw joints, m;
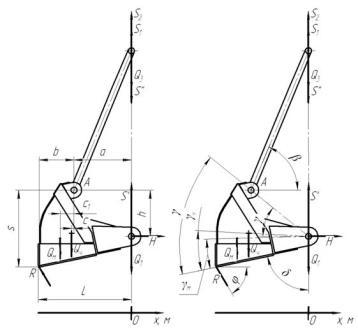
Figure 3 — The circuit design
Change of these parameters will lead to change of geometry of a jaw, as consequence, and to change of shoulders of the forces acting on a jaw, and also characteristic angles. For constructive reasons distance between jaw joints r it is not recommended to take more semispan of jaws of grab bucket L, otherwise the jaw trailing wall starts to touch a curve of filling a material. It will lead to that the active face will be inferred from a material and the grab bucket will be filled ineffectively.
Lowering of current value of force in a closing rope diminishes loading by the propeller, and, hence, and power consumption of process of filling. Criterion of an estimation of power consumption is area FS between a force curve in a closing rope and axes of co-ordinates. Research of agency of various parameters of the grab bucket on area FS will allow to determine paths of lowering of power consumption of process of filling at the expense of sampling of rational value of these parameters.
The current force in closing rope S2 was defined on (1):

Let's agree force calculation in a closing rope on expression (1) at the fixed value of other parameters of the grab bucket in the given operation we name experience, and the value of area FS gained thus we will name experimental, as against discovered on an approximating polynomial (2) which we will name design FSр.
Linear approximation is applied. The approximating polynomial will look like:

Factors of approximation (2) are on expressions:

For the solution of objects in view and conducting of
experience grab bucket parameters r and ? we will name normalized and we will
mark out them accordingly X1 and Х2. The investigated
range of parameter is disjointed on K = 2 steps. The step of change of
parameters is brought in Tab. 1. Hence, instead of real independent magnitude
Х it is inducted it normalized aberration Z, and dependence FS=f (X1, X2)
is substituted by expression FS=f (Z1, Z2).
Parameter | Designation | Amendment unit | Amendment limit | Step |
p | X1 (Z1) | m | 1,035-1,435 | 0,2 |
r | X2 (Z2) | m | 0,85-1,05 | 0,1 |
A series from 4 experiences was spent. Values of current force in a closing rope pays off by means of the program written in the environment of MathСad 14.0. The obtained data are treated in the environment of Microsoft Excel. By means of this application graphs of current force in a closing rope depending on magnitude of disclosing of a jaw (a Fig. 4) are builted and the areas restricted to curves of force and axes of co-ordinates are counted. By means of expressions (3) — (5) factors of approximation have been discovered and after scalings the approximating polynomial is gained:

of variation for the gained empirical data less than 5 %, therefore it is possible to draw a leading-out, that linear approximation is satisfactory.
As a result of the carried out research parameters of the grab bucket r and p are gated out, the extent of their agency on power consumption of process of filling is defined. Approximating dependence of power consumption of process of filling from the given parameters is gained:

Factors of this dependence a1 there is more than null, a2 — there is less than null. Practically it means that for lowering of power consumption the parameter p should be diminished, and parameter r — to augment taking into account constructive reasons. By results of the spent researches for security smaller power consumption is recommended to accept following values of parameters: r = 1,05 m, p = 1,035 m.
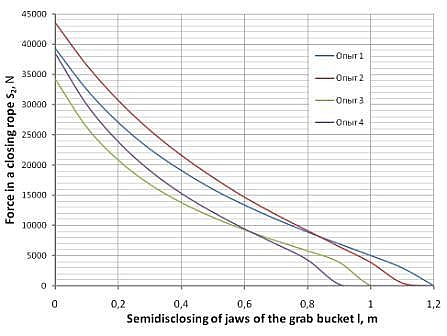
Figure 4 — The graph of change of force in a closing rope
The list of sources.
- Таубер Б.А. Грейферные механизмы. — М.: Машиностроение, 1967.- 424 с.;
- Таубер Б.А. Грейферные механизмы. — М.: МАШГИЗ, 1985. - 270 с.;
- Михайлов И. В. Математическая модель движения грейфера. Вестник АГТУ. 2006. №1 (30);
- Вайнсон А.А. Андреев А. Ф. Крановые грузозахватные устройства: Справочник. М.: Машиностроение, 1982 - 356 с.;
- Зенков Р. Л. Методика расчета грейферов. — Тр. ВНИИПТмаша/ВНИИПТмаш, 1966, вып. 8 (72), с. 3 - 77.
- Шевченко Н.А., Б.П. Румянцев. К вопросу теоретического исследования кинематики грейферного механизма. Автоматизация производственных процессов в машиностроении. Львов,1972, №16. – с.69-72;
- Ясиновский А.М. Динамические нагрузки, воздействующие на канатный грейфер при эксплуатации//Морские порты.- М.: Рекламинформбюро ММФ. 1975. С. 99-101 (ОИИМФ);
- Ясиновский А.М. К методике прочностного расчета элементов челюстей канатных грейферов//Сборник «Детали машин и подъемно-транспортные машины», вып.8. Киев, «Техніка», 1968. С. 101-110 (ОПИ).
- Ясиновский А.М. Экспериментальное определение эксплуатационных нагрузок в элементах натурных канатных грейферов//Сборник «Детали машин и подъемно-транспортные машины», вып.7. Киев, «Техніка», 1968. С. 91-99 (ОПИ).
- ГОСТ 24599-87 Грейферы канатные для навалочных грузов. Общие технические условия;