Вибронагруженность корпусно-секционных шахтных насосов вертикальной и горизонтальной компоновок зависит от неуравновешенных центробежных сил вращающихся деталей проточной части. Поэлементная балансировка и синфазная сборка позволяют получить закономерность распределения остаточной неуравновешенности дискретных масс по длине ротора. Постановка и решение задачи уменьшения вынужденных колебаний позволяет прогнозировать долговечность шахтных насосов.
Вібронавантаження корпусно-секційних шахтних насосів вертикального та горизонтального компонування залежить від неврівноважених відцентрових сил обертаючихся деталей проточної частини. Поелементнє балансування та синфазна зборка дозоляють отримати закономірність розподілу залишкової неврівноваженості дискретних мас по довжині ротора. Постановка та рішення задачі зменьшення задачі зменьшення вимушених коливань дозоляє прогнозувати довговічність шахтних насосів.
The technique for calculation of the vertical vibrating mill rational parameters for superhard fragile materials grinding is development on the base of theoretical and experimental research of motion mechanics of the mill technological load, grinding media layer rational parameters, rational filling of the working chamber with ground material and necessary mill drive characteristics.
Шахтные центробежные корпусно-секционные насосы являются динамическими машинами, силовые нагрузки на которые обусловлены нестационарной гидродинамикой, неоднородностью поля неуравновешенных центробежных сил вращающихся деталей, технологическими и конструктивными несовершенствами. Указанные факторы имеют место вне зависимости от исполнения и работы агрегатов, т.е. горизонтальной или вертикальной их компоновки. Главной отличительной особенностью этих машин является отсутствие продольного разъема определяющего особенности технологии сборки.
Известно, что для лопаточных корпусно-секционных машин часть причин их неуравновешенности закладывается при проектировании и является неотъемлемой частью конструкторского исполнения и формирования ротора насоса. К ним следует отнести несимметричное расположение модулей и элементов колес, радиальные и торцевые биения рабочих колес, положение шпоночных пазов и их относительной ориентации на валу, разброс размеров в пределах посадок сопрягаемых деталей, погрешности балансировки и сборки и т.д.
Эксплуатационные поломки и отказы связанные с конструктивными и технологическими недостатками насосов можно отнести к пяти группам: 1) низкая износостойкость сопрягаемых и контактирующих деталей проточной части машины; 2) недостаточная прочность деталей; 3) низкая ремонтопригодность; 4) недостаточная всасывающая способность; 5) отсутствие устройств для контроля работы насосной установки [1]. Каждый из факторов значим в общей картине долговечности машины, однако первые два существенным образом влияют на эксплуатационный ресурс. При механическом контакте деталей ротора с неподвижными элементами корпуса и другими деталями происходит интенсивное изнашивание, потеря рабочих характеристик и даже разрушение их сопряженных поверхностей.
Исследования, направленные на выявление картины износа показали [2], что при работе насоса с числом ступеней более шести имеет место поперечное колебание вала, вибросмещения которого соизмеримо с величиной зазора между щелевыми уплотнениями, горловиной и ступицей колеса. Ускоренный износ по передним межступенным уплотнениям, узлами гидрозатвора- рубашки вала, разгрузки - дистанционной втулки напрямую связан с вибронагруженностью машины.
Задача увеличения долговечности корпусносекционных машин должна решаться в следующих направлениях: во-первых, поиск, исследование и внедрение высокопрочных износостойких материалов на основе хромистых чугунов, специальных полимерных композиций, нержавеющих хромо-молибденовых сталей и т. д. для сопряженных пар насоса; во-вторых, выявление факторов определяющих уровень вибронагруженности насоса и снижение ее технологическими или конструктивными методами.
Известно, что спектральные составляющие вибрации лопастных насосов обусловлены гидродинамическими и механическими источниками как собственно динамической машины, в совокупности с двигателем и соединительными элементами привода, так и технологическими несовершенствами, обусловленными механической обработкой, методикой предсборочной подготовки и сборки агрегата и т.д.
К гидродинамическим источникам вибрации лопастных насосов относятся: вихреобразование в потоке рабочей среды, неоднородность потока, турбулентные пульсации давления, воздушная и паровая кавитации и т.д.
Механические источники вибрации насосов связаны как с конструкцией и технологией изготовления собственно насоса, так и элементами сопряжения его с приводом и самого привода. Основными источниками первой группы являются неуравновешенные силы инерции вращающихся масс технологическими и сборочными несовершенствами в сравнении с геометрическим подобием машины, а также колебательными процессами в опорных узлах – подшипниках (качения или скольжения). Ко второй группе относятся колебательные процессы, связанные с соединительными муфтами, передаточными механизмами и приводными двигателями.
К основным геометрическим и технологическим несовершенствам рабочих колес, влияющим на вибронагруженность насосных агрегатов следует отнести:
а) большие отклонения по шагу и профилю диффузора между лопатками как в самом колесе, так и между колесами; б) межлопаточная огранка, волнистость по выходному каналу из рабочего колеса, эксцентриситет горловины относительно технологической базы; в) Большие радиальные и торцевые биения поверхностей как коренного, так и покрывного дисков; г) наиболее существенным фактором, влияющим на вибрацию ротора является разномассовость рабочих колес. Для литых колес наблюдается разброс по весу в пределах 1.2…2.5кг; для штампо - сварных 0.3…0.4 кг [3]; д) отбалансированные, но отличающиеся по весу колеса собранные на вал корпусно-секционной машины будут содействовать возникновению вибрации насоса и агрегата в целом.
Распределение неуравновешенных масс колес с учетом их веса на роторе (селективная сборка) не решает задачи снижения вибронагруженности машины. Такое распределение колес приводит к стохастическому расположению остаточных дисбалансов и может привести к резкому росту вибрации ротора. Причем как аппроксимации, так и инструментальному анализу такое распределение в корпусно-секционных машинах не может быть подвергнуто. В том числе и прогнозированию распределения вибропараметров по длине ротора. Многочисленные теоретические решения задачи о колебаниях роторов с установленными по длине массами с неуравновешенностью не имеет практической реализации для корпусно-секционных машин именно из-за невозможности прогнозировать распределение вышеуказанных факторов при сборке.
Решение задачи снижения вибронагруженности и минимизации энергетических потерь на процессы связанные с динамикой корпусно-секционной машины и ее вынужденные колебания требует разработки методов упорядочения и систематизации позиций неуравновешенных масс по длине ротора. Учитывая что фактор неуравновешенности является случайным, зависящим от вышеуказанных геометрических и технологических несовершенств элементов машины то задача подразделяется на: 1) разработки технологий сопутствующих снижению указанных геометрических и технологических несовершенств; 2) разработки методов балансировки, синхронизации при сборке элементов агрегата по выделенному управляющему фактору, контроль вибропараметров и на этой основе прогнозирование долговечности и ресурса агрегата.
Технологические несовершенства минимизированы соотношениями между радиальным, торцевым биениями коренного диска и радиальными биениями горловины и ступицы рабочих колес [4], что позволяет проектировать технологические процессы изготовления рабочих колес высокой точности. Соответственно оснастка, специальный инструмент, выбор баз, порядок операций закладывается и для изготовления деталей проточной части насосов.
В качестве фактора детерминированного позиционирования остаточной неуравновешенности колес по длине вала принята балансная мера [2],[3] определяемая по результатам динамической балансировки элементов ротора. Коррекция неуравновешенной массы проводиться выборкой по дуге окружности с формированием шпоночного паза в диаметрально противоположной стороне относительно зоны коррекции. При этом на валу колеса устанавливаются парами, с направлением положительной разности балансной меры в одну сторону от оси симметрии вала, а минимум ее величины приравнивается расстоянию от вершин параболы распределения или цепной линии до директрисы. При такой организации сборки огибающая колеблющаяся системы с факторами неуравновешенности описывает в пространстве катеноид - минимальную поверхности. Это определяет минимум энергетических потерь при колебаниях системы вне зависимости от любой из двух форм распределения балансных мер – по цепной линии или параболе т.к. пределах вершины цепная линия аппроксимируется параболой. При такой детерминированной сборке становиться возможным количественно оценить изменение выибропараметров вдоль образующей насоса, износ и возможность прогнозировать долговечность и ресурс работы корпусносекционной машины[5].
Задача прогнозирования ресурса работы динамических машин напрямую связанна с теоретическим анализом их вибронагруженности и возможностью сравнения теоретических колебаний с экспериментальными данными. Из вышеприведенного анализа понятно, что динамические прогибы вала под действием возмущающей нагрузки адекватны уравнениям, описывающим распределение балансных мер.
В таком случае интенсивность возмущающих сил Qвоз, в общем случае переменная во времени величина может быть представлена в виде:
- для случая распределения балансных мер по длине вала параболической зависимостью:

- для случая распределения балансных мер по длине вала по цепной линии:
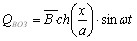
Первый из сомножителей характеризуют нагрузку в продольном направлении, т.е. по валу, второй сомножитель – возмущающую нагрузку от привода агрегата; w - угловая частота возмущающей нагрузки;
В таком случае вынужденные колебания вала с дискретными массами [6] установленными с равномерным шагом с учетом сил затухания будут описываться:
- для случая аппроксимации распределения балансных мер по параболической зависимости:

- для случая аппроксимации распределения балансных мер по уравнению цепной линии:

где EJ – жесткость вала; F – площадь поперечного сечения вала;
- вес единицы объема;
- коэффициент затухания; а, b – параметры, описывающие уравнение цепной линии.
Для получения выражения (3) в виде гармонических составляющих разложим продольную составляющую нагрузки в ряд Фурье:
При имеем для
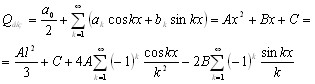
где ;
; 2l – длина вала ротора турбомашины.
Для возмущающей нагрузки с аппроксимацией продольных сил по уравнению цепной линии:

В таком случае уравнение колебаний вала под действием возмущающей нагрузки (5) приобретет вид:
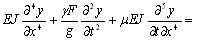

при аппроксимации нагрузки в виде (6):
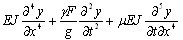
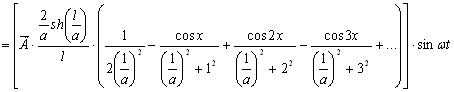
Решение уравнений (7, 8) методом Галеркина Б.Г. [7] позволяет описать колебания роторов динамических турбомашин в зависимости от принятой системы распределения неуравновешенностей. Для корпусно-секционных насосов сравнение трендовых характеристик с результатами решения вышеуказанной задачи при действии переменной во времени нагрузки для системы с дискретно расположенными массами позволяет прогнозировать их ресурс.
Выводы:
1. Разработаны технологические методы и подходы при производстве деталей и узлов насосных агрегатов с нормированием несовершенств, а также методы поэлементной балансировки динамических машин, позволяющие создать систему их упорядочения и координирования при сборке.
2. Методика синфазной сборки корпусно-секционных машин в основу которой положена распределение балансных мер или их положительной разности по параболическому закону или по закону цепной линии позволяет осуществить разработку и внедрение машин малой вибронагруженности и повышенного ресурса. В настоящее время насосы, созданные по разработанной технологии имеют ресурс до 16–18 тыс. часов.
3. Решение задачи вынужденных колебаний роторов корпусно-секционных турбомашин в зависимости от принятой системы распределения неуравновешенностей для дискретно расположенных масс и сравнение трендовых характеристик с полученными теоретическими результатами позволяет прогнозировать их ресурс.
4. Анализ функций распределения балансных мер показывает, что в качестве возмущающих сил при рассмотрение вынужденных колебаний роторов динамических турбомашин с учетом затухания может быть принята функция цепной линии параболического вида или близкая к ней эквидестантная кривая распределения балансных мер.
Литература
1. Алиев Н.А. Динамические аспекты технологической стратегии производства высокоточных рабочих колес центробежных многоступенчатых шахтных насосов.// Збірник наукових праць НДІГМ імені М.М. Федорова. Проблеми експлуатації шахтних стаціонарних установок. Випуск 95. Донецьк, 2002. С. 67-82.
2. Алиев Н.А. Технологическое обоснование методики сборки многосекционных шахтных насосов // Наукові праці Донецького національного технічного університету. Серія: гірнично-електромеханічна Вип. 51. Донецьк. 2002.
3. Алиев Н.А., Бондарь Ю.В., Исаев А.Е. Технология и методика изготовления и сборки многосекционных шахтных насосов горизонтальной и вертикальной компоновки малой вибронагруженности // Международный сборник научных трудов. Прогрессивные технологии и системы машиностроения. Донецк: ДонНТУ 2003 Вып. 24 с. 3-12.
4. Алиев Н.А. Метод нормирования технологических несовершенств при механической обработке рабочих колес многосекционных шахтных машин: Сборник научных трудов / НГУ. Днепропетровск, 2003. №17, Т.2., с. 214-224.
5. Грядущий Б.А., Алиев Н.А., Бондарь Ю.В. Корреляционно–статистический метод оценки остаточного ресурса шахтных машин динамического действия. Сборник научных трудов. / НГУ. Днепропетровск 2003. №17. Т.2. с. 16-30