Abstract
Contents
INTRODUCTION
Conveying, widely spread, as the object of control that best suited to automation, is the primary means of delivery of coal from production faces of coal mines.
Analysis of trends in the coal industry in the last decade shows that the application of advanced systems design and modern technology intensive excavation works, the increase rate of progress of treatment and development workings, the widespread introduction high energy mining equipment for loading and transportation of coal, is not always accompanied by a study of optimization problems operational conditions, economic spending power and material resources, the effective ventilation of mines, Dust Ignition Proof, environmental and industrial safety. Undue financial savings for the development, implementation and modernization of mining equipment and advanced technology also affects the efficiency, reliability and safety.
GOALS AND OBJECTIVES
The object of research is the conveyor line with automatic control system.
The subject of research is the electric main conveyor belt.
Mode of the conveyor is characterized by:
The automation of conveyor transport, to ensure its effective operation, it is necessary to accomplish the following tasks:
Therefore, the purpose of this work is to ensure effective operation of the main shaft assembly lines by adjusting the speed of the electric conveyor belt.
For successful implementation of the objectives necessary to make adequate mathematical models and to investigate the physical processes occurring in the facility, on the basis of modern computer programs and methods of calculation.
URGENCY OF WORK
The modern underground conveyor lines are characterized by significant extent and use powerful conveyors for transportation cargo, as well as presence several routes. It is a complex objects to automations as with positions of control them, so and provision to safety to their exploitations.
The primary task to automations conveyor line is a centralization of starting control and stops conveyor when ensuring their automatic protection for the reason reductions of the expenseses for transportation useful fossilized and reductions of the consuption material.
Today one of the actual tasks is a problem of the automatic regulation to capacity conveyor for stabilization flow and optimization mode to their exploitations.
The most further improvement to exploitations conveyor requires the system development, optimizing mode of their work on criterion of the minimum of the expenseses for transportation useful fossilized. In condition of unevenness of the flow of coal one of the ways of the decision of this problem is a building SAC (System of automated control) to stabilizations of the waited load conveyor to account of the regulation to velocities worker organ of the conveyor
SCIENTIFIC NOVELTY
In today's conveyor belts are used unregulated asynchronous drive. The disadvantages of it are difficult start, slipping belts and shock loads in the drive, increased wear of equipment, significant energy consumption at partial load and the pipeline empty.
Significant increase in economic efficiency can be achieved by harmonizing the operating modes and parameters of a conveyor belt with the actual input flows. To do this, first and foremost, you must have the possibility of complete information about the properties and characteristics of the traffic.
Currently, none of the used in the coal mines of office automation conveyor belt does not function smoothly controlling the speed of the electric drive on a long period of time depending on the incoming traffic on the tape.
SURVEY OF RESEARCH AND
DEVELOPMENTS
ACC.1M (Automated control of conveyors) designed to control and monitor the work of stationary and semi-unbranched transport lines, consisting of tape and drag conveyors, can also be used to manage an extensive transport lines (up to three branches, each of which is managed as a separate assembly line) in mines, including the hazardous gas and dust. Can also be used in mines, concentrators and other enterprises, especially where there is a potentially explosive atmosphere.
ACC.2M (Automated control of conveyors) designed to control and monitor the work of stationary and semi-unbranched transport lines, consisting of tape and drag conveyors, can also be used to manage an extensive transport lines (up to three branches, each of which is managed as a separate assembly line) in mines, in including the hazardous gas and dust. Can also be used in mines, concentrators and other enterprises, especially where there is a potentially explosive atmosphere[9].
Automated control system of conveyor lines ACSCL designed to:
Based on the analysis of existing systems and automated mining conveyors, we conclude that the currently applied complex and automation shaft conveyors have some significant drawbacks.
In particular, equipment such as ACC.1M performed using an outdated element base, which limits the functionality of devices such as: control mechanisms of the pipeline, gathering, transmission and display of information on the status of the pipeline. Reliability and safety of pipelines is also reduced due to frequent failure relay and semiconductor components caused by the instability of their work and rapid wear of the contact groups.
RESULTS
To estimate the possible reduction of energy consumption in the application of controlled electric conveyor belt, compared with non-regulated electric, we calculated the relative consumption of electric energy in the transportation of cargo the same amount of systems with non-regulated electric, with a frequency-regulated electric, smooth speed control of conveyor belt, with two-speed electric with different ratio of the nominal angular velocity equal to 1:2 and 1:3, providing discrete control of linear speed of conveyor belt.
In assessing assumed that the automatic control system for variable frequency drives maintains a constant load per unit length of the pipeline. In this case, electric conveyor running at optimum power consumption. Numerical values are given for the electric conveyor belt type 2Л80У. The data obtained electrical energy consumption-driven conveyor shown in Table. 1 in relative units. For the base value taken electricity consumption unregulated electric.
For the base value taken electricity consumption unregulated electric. Analysis of the data table. 1 that the use of continuous adjustment of the linear tape speed, for example by frequency-controlled electric drive, can reduce energy consumption by 26 ... 38% compared with non-regulated electric. Application of the discrete control of linear speed of conveyor belt with two-speed electric drive with a ratio of angular velocities of 1:2 and 1:3 can reduce electricity consumption by 5 ... 21% compared with an uncontrolled drive. Saving energy in the application of variable drive, the higher the lower the loading conveyor[2].
Table 1 – Consumption to electric energy by drive of the conveyor
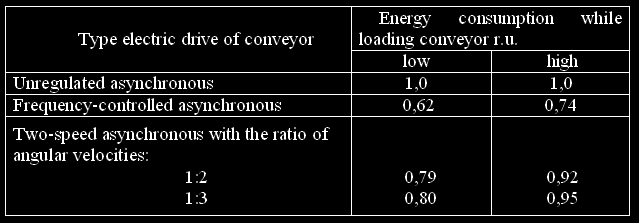
Fig. 1 shows the results of mathematical modeling of the conveyor belt in a traffic ac Q, due to the cyclical nature of the lava. Shown on the graph that in the absence of regulation of the velocity V, mass of the load on the tape mg (c), as well as the static moment Mc (i) the resistance of the electric motor depending on the traffic varies significantly, adversely affecting engine reliability and efficiency of its energy consumption. If, however, adjust the speed depending on traffic can achieve the optimal values of the energy performance of electric conveyor belt Pmex (k), as well as increase the life of load-bearing body, gearbox, and commercials. Therefore it is expedient for reducing traffic, reducing the frequency of rotation of the driving AD. This is to ensure the constancy of the specific gravity moved by mg (h), and, consequently, since the motor Mc (s).
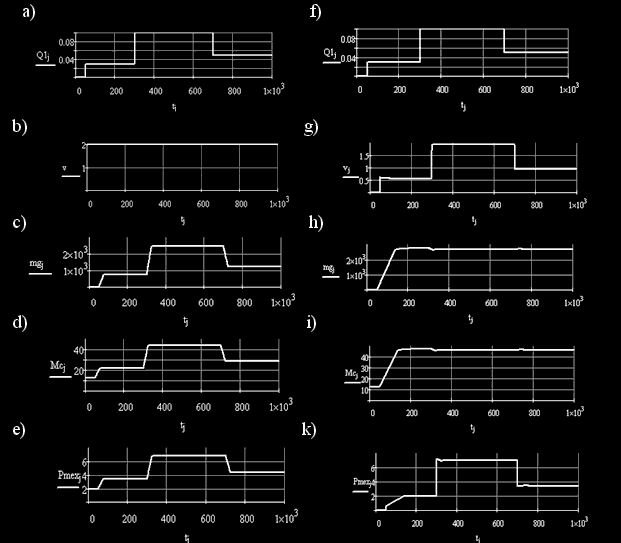
Figure 1 - The results of mathematical modeling
Based on the results of mathematical modeling to conclude that the need to regulate the speed of the electric conveyor belt, and form a block diagram of a device that implements the principle of frequency regulation:
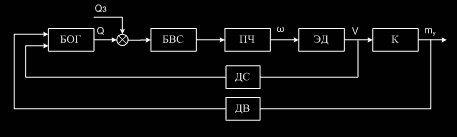
Figure 2 - Block diagram of speed control device
БОГ – - block definition cargo; БВС – block speed selection; ПЧ – frequency converter; ЭД – electric motor; К – conveyor; ДС – speed sensor; ДВ – weight sensor.
Weight of the sensor, which is a conveyor scales, and from the speed sensor - signals are sent to block traffic definition (БОГ), which form its value, which goes to the block rate selection (БВС). Further, compared with the value that generates the load setpoint (ЗН) and a signal to control the drive frequency (ПЧ). The latter directly controls the speed of an induction motor.
Function determining the choice of traffic and speed microcontroller performs. Signals from the sensors are received at the analog input of the microcontroller. ADC module, which includes in its structure converts this information into a binary code for further processing and generation control signal, which is via an RS-485, reaches the final destination of the unit - inverter[7].
CONCLUSIONS
Thus, the use of variable-frequency electric conveyor provides smooth control of linear tape speed, maximizes energy savings of transportation of cargo with a variable traffic. Equally important is the possibility of starter belt. Note that the feature of variable frequency drives the conveyor is a need for an induction motor with forced cooling to the regulation of the angular velocity below the nominal engine cooling conditions have not changed. This ensures that under heating conditions constant, equal to the nominal value, the moment at all speeds of electric drive.
Implementation of the proposed structural scheme in a unified system of automated control underground mine transport complex would enhance its effectiveness by improving reliability, increasing the service life and life of process equipment, reduce downtime, a significant reduction in electricity consumption in the transportation of minerals due to optimization of loads at idle, or close to them, modes.
REFERENCES
- Малиновский А.К. Автоматизированный электропривод машин и установок шахт и рудников: Учебник для вузов. – М.: Недра, 1987. – 277 с.
- Энергосберегающий асинхронный электропривод. Под ред. И. Я. Браславского – М.: Academa, 2004. – 202 с.
- Соколовский Г.Г. Электроприводы переменного тока с частотным регулированием. – М.: Academa, 2006.
- Масандилов Л.Б., Москаленко В.В. Регулирование частоты вращения асинхронных двигателей.- М.: Энергия, 1978 – 96с.
- Копылов И.П. Электрические машины: Учебник для вузов. – М.: Высшая школа, 2002. – 607 с.
- Регулируемый электропривод. Опыт и перспективы применения: Доклады научно-практического семинара, М.:Издательство МЭИ, 2006. - 96с.
- Лукомский Л.В., Ставицкий В.Н. Автоматизация технологических объектов и процессов. Поиск молодых. — 2011 // Материалы XI Международной научно-технической конференции. — Донецк, ДонНТУ — 2011.
- Осипов О.И. Частотно-регулируемый асинхронный электропривод: Учебное пособие - М.: Издательство МЭИ, 2004. - 80с.
- Фигаро Б.И., Павлячик Л.Б. Регулируемые электроприводы переменного тока - Мн.: Техноперспектива, 2006. -383 с.
- "Применение регулируемого электропривода в шахтных ленточных конвейерах". Electronic resource. Access mode: http://www.ntc-esp.ru/art3.html
When writing this master of the abstract work is not completed yet. Date of final completion: December 2011. Full text of the work and materials on the subject can be obtained from the author or his supervisor after this date.