Fig. 3 – Work of signaling device: a)in normal conditions; b) in the absorption of drilling fluid.
Designed
signaling device works this way. When drilling in normal conditions,
the main stream of drilling fluid flowing past the throttle sleeve.
With the onset of absorption of drilling fluid velocity upstream is
reduced and the valve under the action of the spring moves in the down
position and rests on the ledge, cutting off the radial holes in stock.
The whole flow of drilling fluid begins to flow through the throttle
bushing. In this case, the resistance of fluid flow in the drill pipe
increases and performance gauge can be concluded about the beginning of
the absorption liquid in the well.
Similarly, signaling device triggered and the fall of
liquid level in the well below its spot, because this valve 10 to
completely cease to apply force from the drilling fluid in the annulus
hole.
Animation principle of signaling device circulation drilling fluid in the well
The application of this device allows you to control
the absorption of drilling fluid in the borehole regardless of whether
the fall of the liquid level due to changes in the resistance of fluid
motion while reducing its velocity in the annulus wells at the
installation switch.
To determine the
design parameters of signaling necessary to calculate the force exerted
by the fluid on the valve – a dynamic pressure sensor. Since the
theoretical solution of this problem is difficult, it was numerically
simulated by finite element method.
In modeling [2] determined the forces acting on the valve
plate signaling device that allows you to choose a return spring valve
and determine its sensitivity to changes in fluid flow.
Calculations were performed for two structures with
different modes of signaling rinse well, and taking into account the
rotation of the drill string without it. In this case, the simulation
for different sizes of valves – sensor speed pressure. The pressure
drop across the valve is calculated by numerical simulation using
finite elements.
As an example, modeling that was conducted for the
fluid flow rate 20-120 l / min for 93 mm diameter hole, covered with
casing diameter of 89 mm with an inner diameter of 79 mm. Model on
which the calculations were shown in Fig. 4. Simulation results were
shown in Fig. 5
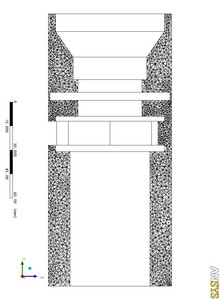
Fig. 4 – Computational grid model
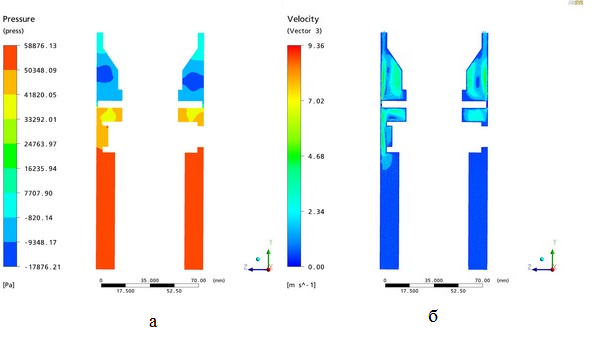
Fig. 5 – Simulation results: a) rub-pressure; b) fluid flow rate.
The simulation,
we determined the force acting on the valve. For example, one of valve
dependence of the force acting on the valve from the fluid flow can be
approximated by the following equation: y = 0.010x2 +0.033 x-0.6. A
plot is shown in Fig. 6.

Fig. 6 – Graph of the force acting on the valve on the supply of washing fluid
Thus, for any
value of the fluid from 20 to 120 l / min, using this relationship, we
can determine the necessary effort, which should provide spring
signaling the need for designing devices and developing the technology
of its application.
Taking into account the settlement was created a real
signaling device design fluid circulation in the hole, 3-D model is
made in the CAD package Compass 3D »and is shown in Fig. 7. In
this model, developed design documentation for the switch.
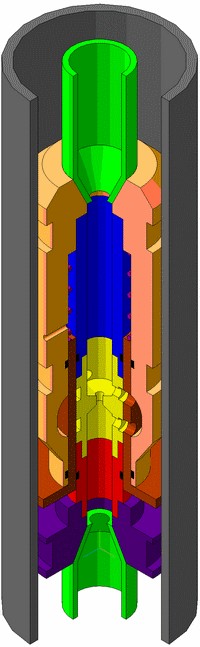
Fig. 7 – A real 3-D model of signaling device circulating drilling fluid in the well
At this stage of the work was carried out an analytical review of drilling fluid absorption
sensors based on which have been identified shortcomings in existing devices.
Proposed a refined principle of signaling and structural scheme designed to implement it.
For signaling circulation drilling fluid was
simulated in the package «ANSYS» to determine the forces
acting on the valve at his job. Calculations were performed for the
well O93 mm with and without rotation of the drill string, with normal
and elevated feeds drilling fluid and well O151 mm without rotation of
the drill string. Based on these calculations, it was concluded that
the rotation of the drill string does not affect the pressure loss in
the switch. The results of the simulation allowed to design a switch
for various drilling conditions.
Have also been proposed rational relationship of
design parameters that are included in the basis of recommendations
from the application of the developed sensors.
On the constructive scheme of the design signaling
device circulation drilling fluid for use in wells. The design of
signaling device patent of Ukraine for useful model number 50771 from
25.06.2010.
Application of the developed design signaling provides the ability to more accurately and quickly identify the
absorption of drilling fluid, which prevents accidents and saves resources and money.
- Патент України на корисну модель № 50771 МПК7
Е21В 25/00. Сигналізатор поглинання промивальної рідини в свердловині /
Каракозов А. А., Парфенюк С. Н., Роль А. В., Сайгайдак И. Д., Назарян А. О. –
опубл. 25.06.2010. – Бюл. №13. – 6 с., ил.
- Каракозов А.А., Парфенюк С.Н., Назарян А.О. Разработка
сигнализатора поглощения промывочной жидкости при бурении геологоразведочных
скважин / Наукові праці ДонНТУ. Серія "Гірничо-геологічна" Випуск
14(181), Донецьк, ДонНТУ – 2011, с. 252-256.