RUS
| UKR
||
DonNTU |
Master's
portal of DonNTU
Irina Sokol
Faculty: Mining and Geology
Speciality "Technics and technology of investigation of deposits
of minerals"
Substantiation of parameters and development of complex
technological and auxiliary equipment for multitrip drilling a wells
drillship "Diorite"
Scientific adviser: Professor Kalinichenko
Oleg
Resume
Summary of research and
developments
Relevancy
Multiple run hole boring has
special place in technical system of marine drilling industry regarding
to the specific weight, relevance and technological specifics. The
abovementioned marine drilling industry is an important source of
receiving geological and geotechnical information in offshore coastal
areas. So far, a large proportion of boreholes with depth of 30-40
meters arepenetrated by units UMB -130 and UMB-130m, operated from
unspecialized and ship drilling rigs. Despite sufficiently high
efficiency of such units, during the performance of basic operations
involving core drilling, the level of performance of auxiliary
operations, foremost arrangement of submersible drilling assembly on
ship’s deck, is still labor-intensive process.
The technological system of
drilling contemplates necessity of multiple change of submersible
drilling assembly by increase and decrease of rate of injection into
hydropercussion drilling assembly. So far, such operation is supported
by standard control valve, using of which doesn’t make exact
fixation in hydraulic system of rated consumption of liquid in order to
put into service hydropercussion machine on the stage of core sampling,
as well as operative increaseof consumption up to the fixed value for
transfer of hydraulic hammer into blocked position with support of
water jet washing of precipitations on the bottom hole. Considering
that ship drilling rigs of “Diorit” type have limited
working floor, thus, development and close-together arrangement of
production equipment with support of the safety level and reduction of
labor intensity of deck setup during the operation of unit UMB-130m are
relevant. Purpose and tasks of research development:
Purpose of work – identification of parameters, design
engineering and development of close-together arrangement plan of
auxiliary and control equipment, increase of safety level
andworkability during the holes drilling by unit UMB-130m.
Research tasks:
1. Carry out an
analysis of working operations in the cycle of hole construction by
unit UMB-130m and found the necessary list of technological and
auxiliary equipment in order to perform safety conditions, reduce labor
intensity and increase operational characteristics of hole drilling
from ship drilling rig "Diorit".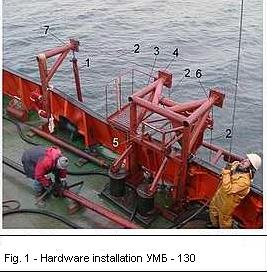
2. Validate
parameters and design the structure of universal control valve, which
ensures fixed fluid supply into injection line of submersible drilling
assembly drive.
3. Design
auxiliary equipment, plan of its close-together arrangement on the
limited working floor of ship drilling rig "Diorit" and technology of
application of engineering development during processing of submersible
drilling assembly on the ship deck in the process of chute-lifting
operations.
All operations connected with arrangement of submersible drilling
assembly on the deck (figure Nr. 1) forcore drilling, disassembly and
erection of elements of submersible drilling assembly do not meet
requirements of safe works. Besides that, the process of drilling
assembly is not producible after its trip in hole. Therefore, there was
developed new complex of arrangement of technological and auxiliary
equipment on the ship “Diorit”, which supported technical
and economical safety level and reduction of labor intensity of deck
setup during the operation of unit UMB-130m. Thereto, the ship "Diorit"
provides new arrangement of auxiliary and technological equipment.
The primary elements are the following:
1) Canting device
secures safe manipulations with drilling assembly. It is possible to
put horizontally drilling assembly along the board on the deck,
transfer assembly from horizontal into vertical with further carrying
assembly over the board.
2) Holders are
for safe arrangement and fixation of submersible drilling assembly in
horizontal position along the board over the deck.
3) Control valve
(figure 7) is designated for operative change of fluid consumption of
injection line of pump manifold. Valve is located in the working area
of drill men on the rigid zone of injection line of pump manifold and
connected to it by supply pipe with hose coupling.
Design features of developed equipment
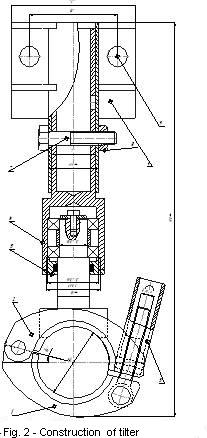
Canting device clamp (figure 2) is
installed with possible shaft rotation in vertical plane, securing
manipulations with long assembly within the limited space. Submersible
drilling assembly is located horizontally on holders (figure 3) and
secures movement of assembly into vertical position for carrying it
over the board. If necessary, canting device may be removed from the
ship board.
Holder (figure 4) is a frame, which
changes position depending on works performed. If the assembly is
located horizontally, the holders take operating position. During the
drilling it is not reasonable to use holders, therefore, they are
brought down due to the turn of bolt 6 and take the most bottom
position. It enables to expand pass for work people on deck. Bearing
holders are located along the board over the deck. The package includes
two holders. Submersible drilling assembly is supported by bearing
holders; core equipment is connected to it. Cargo adapter is connected
to submersible drilling assembly adapter. Erected drilling assembly is
fixed in canting device clamp.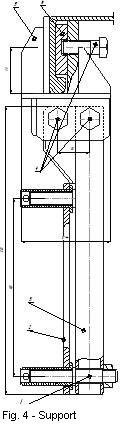
Later, submersible drilling assembly with
a help of draw works and standard cargo boom stands vertically and
carried over the board and fixed in clamp.
With a help of draw works submersible
drilling assembly together with clamp is brought down freely along
pooled on branches of guide rope with centration about axis of support
pipe. In the event of ship transfer and with permissible tolerance of
rope branched from vertical (up to 5-6), additional direction of
drilling assembly to well bore, is provided by support inlet. 
Upon contact with inlet the clamp is stopped, the assembly continues
moving down to the bottom. Boring pump is turned on, and depending on
the selected way of drilling, control valve sets necessary fluid supply
into pressure pipeline. Then drilling is carried out.
After hole making for the whole core run
the drilling pump is switched off, and assembly together with clamp
raises up. The clamp is fixed on extensible levers. Drilling assembly
is released by opening of half-door, and with a help of cargo boom and
draw works is moved to the working deck for core recovery.
Conditions of operating change of the way of rock breaking on the
holes interval
Technological plan of drilling contemplates necessity of multiple
change of submersible drilling assembly by increase and decrease of
rate of injection into hydropercussion drilling assembly. In order to
change rock breaking down the hole, control valve is proposed (figure
6), which allow operative and repeatedly change of fluid supply into
submersible drilling assembly on the passable holes interval. 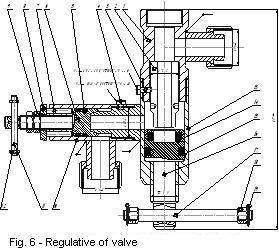
Valve secures nominal fluid consumption
in order to include into work hydropercussion machine on the stage of
core sampling and operative inclusion of fluid consumption up to the
fixed value with support of water jet washing of precipitations on the
bottom hole.
Regulation of supply into submersible
drilling assembly is carried out by change of position of piston 1 with
a help of screw 2 with screw pitch 8 mm. At that, piston 3 is
previously fixedwith a help of screw 4 in specific position, wherein
portion of fluid Q1 is poured out, which exceeds overall consumption of
Q in value of rated fluid supply Q2 for operation of hydraulic hammer
(figure 7,a). 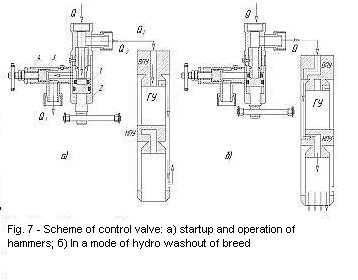
In order to work in hydraulic washing-out mode, screw 2 is turned (1,5
- 2 turns). At that, piston 1blocks fluid access into drain channel,
all fluid flows tosubmersible drilling assembly, securing activation of
water treatment system and top water level. In such position of piston
1, the whole stream flows to the core tube interior and further to the
borehole bottom, providing intensive water jet washing on the bottom,
or securing washing of core cylinder formed in core tube.
Conclusion:
New arrangement of auxiliary equipment on
the ship “Diorit” enables to increase ergonomic efficiency
of unit UMB-130m by technical development, directed on reduction of
labor intensity and increase of safety level and produceability of
performance of operations on the deck.
References
- Калиниченко О.И., Каракозов А.А., Зыбинский П.В. Новые
технические средства и технология поинтервального бурения
инженерно-геологических скважин на шельфе.//Труды ДонГТУ. Серия
Горно-геологическая. – Донецк. – 2001. – Вып. 36.
– С. 144 – 148.
- Калиниченко О.И, Хохуля А.В Основные проблемы и пути
совершенствования техники и технологи многорейсового бурения скважин на
морских акваториях Науковий вісник. №7, Національного гірничого
університету. Науково технічний журнал Дніпропетровськ, 2009. С. 45
– 50
- Калиниченко О.И., Зыбинский П.В., Каракозов А.А. Гидроударные
буровые снаряды и установки для бурения скважин на шельфе.- Донецк:
«Вебер» (Донецкое отделение), 2007. – 276 с.
http://apcp.apmath.spbu.ru/ru/staff/tuzov/onapr.html - 10.12.2004 г.
- Лукошков А.В. Техника исследования морского дна. - Л.:
Судостроение, 1984. - 264с.
- Милн П. Подводные инженерные изыскания [Текст]: Пер. с анг. - Л.:
Судостроение, 1984. - 344 с.
- Применение погружных автономных установок для однорейсового
бурения подводных скважин /Калиниченко О.И., Коломоец А.В., Квашин Е.В.
и др. // Техн. и технол. геол.развед. работ; орг.пр-ва. Обзор /ВИЭМС.
– М.,1988.-Вып.2. - 46 с.
- Наук. пр. Донецьк. нац. техн. ун - ту / Донецьк.нац.техн. ун - т;
Пiд заг.ред.О.А.Мiнаєва.- Донецьк,2003.-С.52- 56. - (Серiя
гiрничо-геологiчна; Вип.63.[электронный ресурс]. - Режим доступа:
http://info.donntu.ru/el_izdan/sbornik_ggf_N63_2003/M21.pdf
In presently time master's degree work is in the stage of development.
After January 2011 the complete text of work can be got for an author
or Scientific supervisor.
DonNTU |
Master's
portal |
Resume