Реферат за темою випускної роботи
Зміст
- Вступ
- 1. Мета і задачі
- 2. Переваги процесу брикетування
- 3. Вимоги до шихти і готових брикетів
- 3.1 Характеристика матеріалів, що брикетуються
- 3.2 Вимоги до металургійних властивостей брикетів
- 4. Схема технологічного процесу
- 5. Ефективність використання брикетів
- Висновки
- Перелік посилань
Вступ
Створення і впровадження більш раціональних і екологічно чистих виробництв є основним завданням сучасного людства, що зіткнулося з проблемою глобального екологічного забруднення і виснаження планети. Так, наприклад, чорна металургія є однією з найбільш матеріало-та енергоємних, а також екологічно шкідливих галузей промисловості. Загальна витрата матеріально-сировинних ресурсів по циклу від видобування руди та вугілля до прокатки складає до 7 т на 1 т готового прокату [1]. На металургійному комбінаті повного циклу потужністю 5 млн. т прокату в рік утворюється 2,3 млн. т шлаків, 0,8 млн. т пилу, шламів та окалини, 25 тис. т сполук сірки, 120 тис. т оксидів вуглецю, азоту та інших елементів [2]. Тому питання раціонального використання природних ресурсів, а також комплексної переробки відходів – найбільш актуальний на сьогодні для даної галузі промисловості.
Найбільш прийнятною не тільки з екологічної, але і з економічної точки зору є утилізація відходів всередині власного виробництва, так як це дозволяє використовувати їх у вигляді відносно дешевої сировини, що сприяє значному зниженню витрат на шихту, підвищенню якості та конкурентоспроможності продукції, а головне, зменшенню собівартості готової продукції.
1. Мета та задачі
Магістерська робота присвячена дослідженню процесу брикетування як одного з універсальних напрямків підготовки металургійних відходів.
Основна мета – розробка раціональної технології підготовки та брикетування залізовмісних відходів металургійного виробництва.
Новизна полягає в тому, що в роботі запропонована універсальна схема отримання залізовмісних брикетів з відходів Донецького металургійного заводу, з метою подальшої їх переробки на підприємстві.
У роботі, поставлені такі головні задачі:
- Розглянути основні види відходів, що утворюються на ПрАТ «Донецьксталь МЗ», вивчити їх особливості (фізико-хімічні властивості, гранулометричний склад тощо);
- Проаналізувати вимоги до металургійних брикетів і на підставі цього вибрати найбільш прийнятну схему підготовки відходів підприємства;
- Розробити технологічну лінію з виробництва залізовмісних брикетів;
- Визначити еколого-економічний ефект, що отримується за рахунок використання брикетів в доменному і сталеплавильному процесах.
2. Переваги процесу брикетування
На сьогодні виділяють три основні способи окускування в металургії – це агломерація, отримання окатишів і брикетування. Великого поширення набули перші два. Це пов'язано, перш за все, з високою продуктивністю агломераційних машин, а також з можливістю отримання продуктів високої якості.
Останнім часом через зменшення природних запасів, а також надмірного накопичення відходів, в металургії все частіше стали застосовуватися тонкофракційні матеріали – концентрати глибокого збагачення, а також шлами і пил. Однак, їх використання в агломераційному процесі і при виробництві окатишів, обмежена, оскільки призводить до погіршення якості готового продукту.
Так, наприклад, додавання шламів в аглошихту становить до 15% від загальної маси, оскільки перевищення цієї кількості веде до погіршення показників спікання, зростання шкідливих домішок в агломераті, порушення правил санітарної гігієни і техніки безпеки на робочих місцях, забруднення обладнання та повітряного басейну. А підготовка (зневоднення і термічна сушка шламів, огрудкування пилу, знемаслення шламів прокатного виробництва, обезцинкування шламів і пилу) металургійних відходів для додавання в аглошихту або окатиші вимагає порівняно високих капітальних і експлуатаційних витрат.
До того ж, для підприємств, які не мають власних аглофабрик, повернення відходів до власного виробництва у вигляді сировини робиться в принципі неможливим. Тому сьогодні набирає популярність такий метод окускування як брикетування.
Процес брикетування має ряд істотних переваг:
- пред'являє менш жорсткі вимоги до якості сировини, дозволяє окусковувати матеріали широких класів крупності менше 10 мм, практично в будь-яких пропорціях і складах;
- є технічно простим способом окускування;
- брикетна установка мобільна і не займає велику площу;
- при брикетуванні зберігаються властивості компонентів, що входять в брикети;
- з екологічної точки зору є більш чистим способом окускування;
- брикети розширюють сировинну і паливно-енергетичну базу металургії [3].
Проблемним питанням, що вимагає додаткового вивчення, є вибір зв’язуючого, яке б відповідало необхідній міцності брикету та мало прийнятну ціну.
Досвідом багатьох металургійних компаній встановлено, що процес брикетування найбільш повно реалізується спільно з іншими методами окускування – агломерацією і грануляцією з випалюванням. Вони не конкурують між собою, а економічно вигідно доповнюють один одного.
Брикетування відходів металургійного виробництва вже давно і досить міцно вкоренилося в розвинених країнах світу. Однак на Україну воно не набуло такого широкого розповсюдження і в даний час не перевищує 2%, хоча потреба в такому методі окускування може бути на порядок вище [4].
3. Вимоги до шихти і готових брикетів
В даний час існують різні схеми брикетування, які сильно відрізняються один від одного. Так, наприклад, розрізняють способи «холодного» і «гарячого» брикетування, що проходять відповідно при звичайних і високих температурах. Також брикетування зі зв'язуючим або без, при різному тиску пресування, з різними способами зміцнення сирих брикетів (термічний та хімічний) й ін.
При виборі оптимальної схеми виробництва брикетів для Донецького металургійного заводу необхідно врахувати ряд факторів: характер та обсяг відходів, що утворюються, область подальшого використання брикетів, а також вимоги до них, витрати підприємства на реалізацію даного проекту, його економічна та екологічна ефективність і пр.
3.1 Характеристика матеріалів, що брикетуються
Основні відходи, що утворюються на ПрАТ «Донецьксталь - МЗ» та потребують утилізації, належать до доменного, сталеплавильного і прокатного виробництва. Це колошниковий пил, пил центральної витяжної станції та аспіраційних установок, шлами мокрої газоочистки доменного газу, відсіви коксу, а також пил ЕСПЦ, окалина та чавунна стружка (Таблиця 1).
Таблиця 1 - Хімічний склад відходів
Матеріал | FeO | Fe2O3 | SiO2 | CaO | MgO | Al2O3 | MnO | C | S |
Колошниковий пил | 42.1 | 53.76 | 12.0 | 11.56 | 0.9 | 1.13 | 0.26 | 10.69 | 0.4 |
Домений шлам | 42.2 | 57.88 | 8.36 | 5.74 | 1.1 | 1.36 | 0.2 | 9.79 | 0.7 |
Пил ЦВС | 50.2 | 68.54 | 3.7 | 1.2 | 0.4 | 0.9 | 0.95 | 4.95 | 0.9 |
Пил ЭСПЦ | 49.6 | 65.17 | 7.28 | 6.5 | 1.0 | 0.8 | 1.52 | 1.21 | 0.6 |
Вапняний пил | 1.1 | 1.5 | 5.2 | 66.7 | 0.6 | 0.5 | - | - | 0.1 |
Окалина | 70.0 | 36.2 | 2 | 1.7 | 0.3 | 0.5 | 0.8 | - | 0.04 |
Ці відходи повинні відповідати певним вимогам. Так, шлами, які використовуються при окускуванні, повинні мати:
- вологість не більше 8-12%;
- крупність після сушки не більше 6 мм;
- мінімальний приведений вміст заліза не менше 45%;
- вміст цинку: при використанні брикетів в доменному виробництві – не більше 1%, в сталеплавильному – не регламентується.
Колошниковий пил, що виноситься потоком газу через колошник доменної печі і осідає у пиловловлювачах, за складом приблизно відповідає складу шихти, що плавиться, але містить ще 9-11% С і до 12% СаО – це робить його цінною сировиною для брикетів [5].
За фракційним складом найбільш прийнятними є матеріали крупністю 0-5 мм. Так як наявність в сировині переважно великих зерен призводить до утворення структури брикетів з великими порожнечами, які необхідно заповняти зв’язуючим. Це не тільки збільшує вартість брикетів, але й зменшує їх міцність та термічну стійкість. Великий вміст у відходах пиловидних класів вимагає інтенсивного перемішування компонентів шихти, підвищення витрати зв’язуючого і тиску пресування.
Особливе значення для рудних концентратів та відходів виробництва має вологість. Наявність в матеріалі, що брикетується, більше 6-8% вологи негативно впливає на міцність брикетів.
Одним з важливих компонентів шихти є зв’язуюче – допоміжний матеріал, який поліпшує злипання частинок і підвищує міцність брикетів до заданого рівня. Воно повинно відповідати наступним вимогам:
- забезпечувати високу холодну і гарячу міцність при мінімальній витраті;
- забезпечувати швидку реакцію між частками;
- вносити мінімальну кількість шкідливих, баластних та інших домішок, що є небезпечними для обслуговуючого персоналу і знижують якість кінцевого продукту;
- бути поширеними і мати невисоку вартість;
- не вимагати складних прийомів і операцій по їх використанню;
- забезпечувати максимальну вологостійкість.
Зв’язуюче є визначальною умовою міцності і значною мірою – відновлення брикетів. Додавання його в шихту строго регламентовано. Так, при збільшенні витрати зв’язуючого, брикети стають більш міцними, але їх собівартість зростає, до того ж, знижується вміст заліза та інших корисних компонентів [6].
Для досягнення заданих вимог, все шихтові матеріали відправляють на попередню підготовку. Підготовка відходів до брикетування є досить витратним процесом, що складається з наступних технологічних операцій:
- вирівнювання вологості, хімічного і фракційного складів шляхом спеціальної (пошарової) укладки сирих і сухих компонентів шихти;
- для перезволоженої сировини слід передбачити її хімічну чи теплову сушку;
- гасіння вапна, яке використовується в якості зв’язуючого;
- видалення сторонніх фракцій і металевих включень розміром понад 10 мм, які можуть привести до поломки бандажів преса;
- подрібнення сировини надлишкової крупності й ін..
3.2 Вимоги до металургійних властивостей брикетів
Як і до інших матеріалів, до брикетів висуваються жорсткі вимоги не тільки по хімічному і гранулометричному складам, а й за фізико-механічними властивостями.
Брикети можуть мати різний хімічний склад, з різним використанням легуючих добавок і флюсів. Включення того чи іншого компоненту залежить від вимог металургійного переділу, в якому планується подальше їх використання. Найчастіше роблять двох-або-трикомпонентні брикети. Чим менше компонентів і чим ближче вони за складом один до одного, тим більш гомогенна шихта, і, як наслідок, вище якість брикетів. До того ж збільшення кількості матеріалів призводить до ускладнення технології підготовки і усереднення шихти.
Основними параметрами металургійних брикетів є механічна і термічна міцність, пористість і щільність, атмосферостійкість. У той же час кожен металургійний процес пред'являє додаткові вимоги до брикетів.
Зокрема, брикети, що задовольняють вимогам доменної плавки, повинні бути стійкі при температурі 900-1300 °С, мати опір стисненню вище 58 Н/см2, володіти високою пористістю і газопроникністю і, разом з тим, бути водостійкими. Розм'якшення матеріалів, призначених для доменної плавки, повинно здійснюватися в інтервалі температур від 1050 до 1200 °С.
Брикети для сталеплавильного виробництва повинні витримувати нагрів до 1500 ° С протягом трьох хвилин і при цьому не розвалюватися на шматки, а також мати пористість не більше 5-10%, їх опір стисненню повинне бути не нижче 25 Н/см2 [7].
Багато в чому ці параметри залежать від розмірів і форми брикетів, які можуть бути різними – від блоку 600х300х200 мм и масою 70-100 кг, до гранул діаметром 5-10 мм і масою до 10 г. Розмір окускованої сировини для умов доменної плавки обмежують деякими граничними значеннями. З урахуванням можливостей виносу потоком газу, газопроникливості, відновності та інших умов її мінімальний розмір складає 10-12 мм, а максимальний – 60-100 мм.
Форма брикетів впливає істотним чином не тільки на їх міцність, а й на тривалість металургійної обробки. Брикети овальної, чечевідної та блізькосферичної форми (Рисунок 1) більш терпимі до тиску і при додатку навантаження приймають більш зручне положення, розподіляючи зусилля рівномірно на весь розташований нижче масив. Гострі виступи брикетів більш схильні до сколів, тому відсутність гострих ребер, крайок і виступів в брикетах підвищує їх міцність.
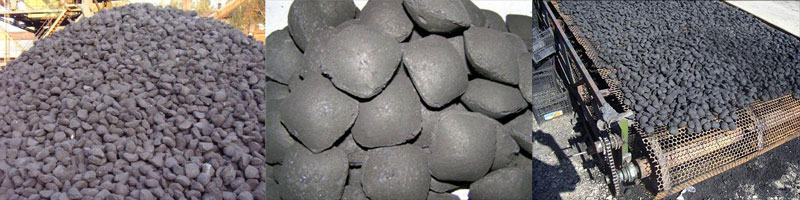
Рисунок 1 – Оптимальна форма металургійних брикетів
4. Схема технологічного процесу
На підставі проведеного аналізу, з урахуванням поставлених вимог, найбільш прийнятною є схема «холодного» брикетування з використанням як зв'язки – вапна. Гашене вапно є порівняно дешевим і достатньо міцним зв’язуючим матеріалом та, одночасно, флюсом. Для досягнення необхідної міцності брикетів його додають у кількості до 10% від маси шихти. Зміцнення брикетів відбувається в спеціальних камерах за рахунок реакції карбонізації [8].
Запропонований спосіб брикетування складається з наступних операцій (Рисунок 2):
- Зберігання компонентів шихти
- Дозування і змішування сировинних матеріалів;
- Пресування отриманої шихти в брикети заданої форми;
- Обробка «сирих» брикетів (сушка, карбонізація);
- Доставка споживачам.
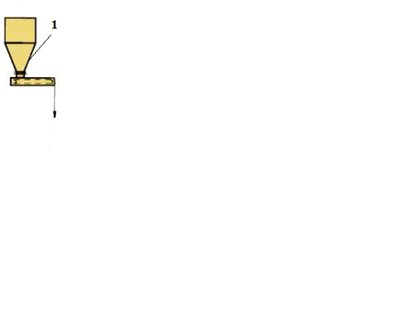
1 – бункер з шихтою, 2 – бункер зі зв’язуючим, 3 – ємність з водою, 4 – змішувач сухої і зволоженої шихти, 5 – подрібнювач, 6 – прес, 7 – гуркіт, 8 – відсів, 9 – ділянка набору міцності, 10 – готові брикети .
Рисунок 2 – Схема технологічного процесу виробництва брикетів
Зберігання матеріалів, які пройшли попередню підготовку, здійснюється на відкритих чи закритих майданчиках. Тонкодисперсні матеріали, для запобігання їх пилиння, зберігаються в закритих бункерах. Тривале зберігання гашеного вапна навіть в закритих бункерах для запобігання його карбонізації не рекомендується.
Підпитка і дозування є важливими операціями по підготовці шихти до брикетування. Постійна, стійка підпитка сприяє рівномірній роботі обладнання, а правильне дозування забезпечує не тільки заданий хіміко-мінералогічний склад брикетів, але й високу міцність [9].
ППеремішування шихти відбувається в спеціальному двохвальному змішувачі: спочатку в сухому вигляді, а потім з додаванням вологи або пари, якщо це необхідно. Підготовлена суміш прямує на прес.
Пресування брикетів є найважливішою, головною ланкою процесу брикетування, що визначає сутність даного методу окускування. Воно надає брикетам потрібну форму, об'єм і щільність, що багато в чому визначає їх кінцеву міцність. Пресування включає такі операції, як подача шихти, підпресовка (попереднє ущільнення) шихти, заповнення пресуючих осередків, ущільнення шихти і витяг брикетів.
Вальцьові преси є найбільш поширеними. Вони мають високу продуктивність до 100 т брикетів на годину і більше, розвивають великі тиски пресування (до 150 МПа), що дозволяє отримати досить міцні брикети [10].
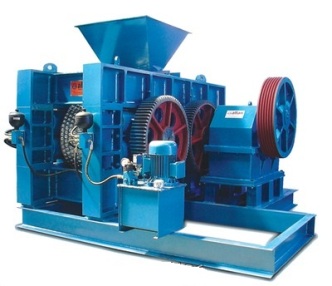
Рисунок 3 – Вальцовий прес
Процес пресування полягає в тому, що шихта направляється в щилину між двома ваками, що обертаються назустріч один одному. При обертанні валків відбувається зближення осередків, захоплення шихти та її ущільнення. При подальшому обертанні валки розходяться, і брикети під власною вагою і невеликим розширенням після зняття тиску випадають з осередків.
Поряд з простотою формоутворення вальцьові преси мають і недоліки: відсутність повного закриття формуючих елементів, а також необхідність підпресовки.
Відсів та повернення дріб’язку. При пресуванні на брикетах утворюються кромки, задирки, які при добуванні і падінні продукту обламуються. Деякі брикети при випаданні з осередків руйнуються. Це призводить до утворення деякої кількості дріб'язку, що є некондиційним продуктом. Його доцільно відсіяти і повернути в процес, що підвищує його економічність, а також запобігає запилювання при подальшому русі брикетів по технологічній лінії.
Зміцнення брикетів є заключною ланкою процесу брикетування, що визначає кінцеву міцність брикетів. Свіжі брикети мають невисоку міцність, що призводить до необхідності їх зміцнення. Під час зміцнення відбуваються складні фізичні і хімічні процеси.
Карбонізація, тобто взаємодія СаО з вуглекислим газом, є діючим способом зміцнення брикетів. ЇЇ доцільно вести в спеціальних стрічкових сушилах, з використанням, наприклад, димових газів, що містять 20-25% CO2. При атмосферному тиску і температурі 60-65 °С тривалість карбонізації становить приблизно 2-2,5 години. Добавка в брикети матеріалів, що виділяють СO2, також скорочує тривалість карбонізації [11].
Для підвищення ефективності зміцнення поряд з інтенсивною сушкою слід застосовувати природну сушку карбонізацією вуглекислим газом, що містяться в атмосферному повітрі, це забезпечить додаткову міцність.
Правильна організація відвантаження готового продукту сприяє зменшенню кількості зруйнованих брикетів.
Якщо брикетна установка розташована поблизу споживача, для доставки брикетів можна використовувати конвеєрний транспорт, розташований в галереї, що запобігає потраплянню вологи. Останнє дозволяє відмовитися від бункерів готової продукції та від транспорту, що значно здешевлює вартість брикетів.
Для зменшення бою брикетів при падінні з висоти всі завантажувальні вузли повинні бути забезпечені жолобами, які пом'якшують удар. Місця падіння брикетів повинні бути обгумованими [12].
5. Ефективність використання брикетів
Використання брикетованої сировини в доменній плавці має суттєві відмінності від використання традиційних матеріалів. Залежно від сировини, компонентного складу і способу пресування брикетований матеріал може мати надзвичайно різноманітні властивості – відновлюваність, разм’якчення, усадку.
При додаванні брикетів в доменну піч збільшується її продуктивність. Відбувається це, за рахунок поліпшення газопроникності стовпа доменної шихти, внаслідок чого збільшується витрата дуття, зменшується винос колошникового пилу і знижується витрата коксу.
На сьогоднішній день запатентовано значну кількість складів брикетів, призначених для використання в доменному переділі, і способів їх виробництва. Найбільш характерними є залізорудні офлюсовані брикети, офлюсовані рудно-вугільні брикети, залізофлюсні брикети різних складів, брикети з колошникового пилу та інші [13].
Сталеплавне виробництво пред'являє менш суворі вимоги до механічної міцності брикетів, тому їх використання там дає кращі результати, а тому більш поширене, ніж в доменному виробництві.
Використання брикетованих залізовмісних відходів як оборотного продукту в сталеплавному виробництві в даний час є не тільки поширеним способом утилізації пилу, але і одним зі способів вилучення цинку. Раціональна схема переробки цинквмістного пилу електросталеплавильного цеху Донецького металургійного заводу представлена нижче (Рисунок 4).
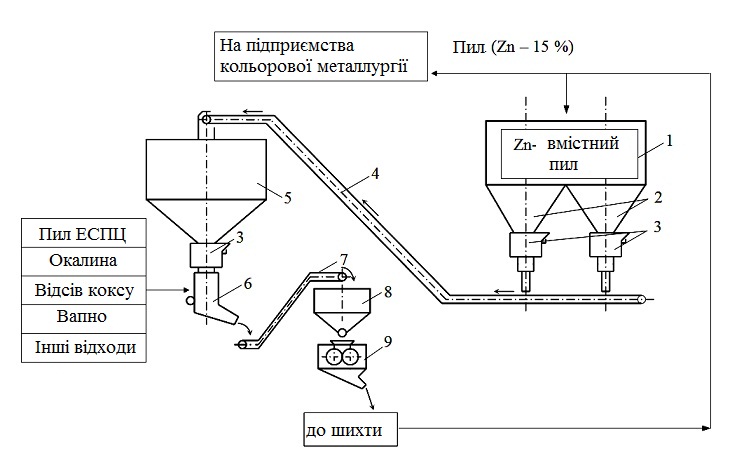
1 – рукавний фільтр, 2 – бункер, 3 – шлюзові дозатори, 4 – скребковий конвеєр, 5 – накопичувальний бункер, 6 – вібро-зволожувач, 7 – стрічковий конвеєр, 8 – бункер суміші; 9 – вальцьовий прес.
Рисунок 4 – Комплексна схема утилізації електросталеплавильної пилу
Вловлений в рукавному фільтрі пил з бункерів через шлюзові дозатори подається на скребковий конвеєр, яким транспортується в накопичувальний бункер. З бункера сухий пил через дозатор подається в вібраційний змішувач-зволожувач, в якому пил зволожується водою і змішується з іншими відходами. Зволожена суміш подається стрічковим конвеєром в проміжний бункер, з якого вона надходить в вальцьовий прес. Готові брикети транспортують в шихтове відділення електросталеплавильного цеху і подаються в піч разом з шихтою.
Після декількох циклів вміст цинку в пилу зросте і при досягненні певної концентрації, придатної для вилучення цинку, його виводять з циклу і відправляють на підприємства кольорової металургії як цінну вторинну сировину.
Досвід використання брикетів в сталеплавильному виробництві показує, що добавки брикетованих матеріалів істотно поліпшують техніко-економічні показники (скорочують тривалість плавки, сприяють швидкому наведенню шлаку, знижують угар металу, зменшують витрати металобрухту) [14].
Висновки
Літературний аналіз вітчизняного та зарубіжного досвіду в області брикетування показує що:
- Процес брикетування дозволяє знизити антропогенне навантаження на навколишнє середовище за рахунок утилізації металургійних відходів.
- Впровадження брикетного виробництва сприяє зменшенню пилогазових викидів, що утворюються при традиційних способах окускування залізорудної сировини.
- При вживанні металургійних брикетів в доменному виробництві спостерігається: істотне збільшення продуктивності, економія первинної сировини, зниження витрат енергоресурсів, підвищення виходу придатного, поліпшення якості металу.
- Використання процесу брикетування для переробки електросталеплавильного пилу дозволяє організувати рециклінг цинку, його накопичення і подальше використання на підприємствах кольорової металургії.
- Організація брикетних фабрик дозволяє знизити вартість кінцевого продукту за рахунок повернення корисних матеріалів в технологічний процес, а також завдяки зниженню виплат на розміщення відходів.
На сьогодні, у чорній металургії України, незважаючи на зростання потреби в нових матеріалах, брикетування не знаходить належної уваги, яке воно по праву заслуговує. Хоча для його розвитку є широка як сировинна, так і технологічна база. Тому залучення в цю сферу виробництва сучасних металургійних підприємств є актуальним завданням не тільки екології, а й економіки.
Перелік посилань
- Банный Н.П. Экономика чёрной металлургии СССР / Н.П. Банный, А.А. Федотов, П.А. Ширяев и др. – М.: Металлургия, 1978. – 344 с.
- Буторина И.В. Основы устойчивого развития металлургического производства / И.В. Буторина. – Донецк: Каштан, 2005. – 332 с.
- Вегман Е.Ф. Окускование руд и концентратов / Е.Ф. Вегман. – 3-е изд., перераб. и доп. – М.: Металлургия, 1984. – 256 с.
- Равич Б.М. Брикетирование в цветной и чёрной металлургии / Б.М. Равич. – М.: Металлургия, 1975. – 232 с.
- Фоменко А.И. Утилизация шламов металлургических производств / А.И. Фоменко // Изв. вузов: Чёрная металлургия. – 2001. – № 11. – С. 70-71.
- Тюренков Н.Г. Брикетирование руд / Н.Г. Тюренков. – М.: Металлургиздат, 1948. – 128 с.
- Ожогин В.В. Взаимосвязь показателей механической прочности брикетированных материалов / В.В. Ожогин // Вісник Приазов. держ. техн. ун-ту: Зб. наук. пр. – Маріуполь, 2006. – Вип. 16. – С. 17-21 [электронный ресурс] – Режим доступа: eIRPSTU
- Корж А.Т. Особенности технологии подсушки шламов известью / А.Т. Корж, А.Ф. Голубов // Чёрная металлургия: Бюл. ЦНИИЧермет. – 1971 – № 5. – С. 49-50.
- Носков В.А. Валковый пресс для брикетирования мелкофракционных отходов производства и сырья / В.А. Носков // Металлург. и горноруд. пром-сть. – 1999. – № 2 – С. 100-102 [электронный ресурс] – Режим доступа: MetalJournal
- Ожогин В.В. Совершенствование ресурсосберегающей технологии получения и использования высокопрочных шламовых брикетов в аглодоменном производстве: дис. канд. техн. наук: 05.16.02. – Мариуполь, ПГТУ, 2004. – 207 с.
- Пат. 2083681 РФ, МПК6 С21С5/06, С22В1/24, 1/242. Брикет для производства чугуна и стали / Агеев Е.Е., Бондарев Ю.А., Булгаков В.Г. и др.; опубл. 10.07.1997.
- Носков В.А. Экспериментальные исследования основных параметров и режимов брикетирования мелкофракционных техногенных отходов в валковых прессах / В.А. Носков, Б.Н. Маймур, В.И. Петренко и др. // Металлург. и горноруд. пром-сть. – 1999. – № 6. – С. 104-107 [электронный ресурс] – Режим доступа: MetalJournal
- Информационно-рекламный проспект фирмы "Sahut-conreur" [электронный ресурс]. – Режим доступа: Sahut-conreur
- Ожогин В.В. Рециклинг пылевидных отходов сталеплавильного производства / В.В. Ожогин // Бюл. науч.-техн. и эконом. информ.: Чёрная металлургия. – 2006. – № 8. – С. 72-74.