Реферат з теми выпускної роботи
Зміст
- Вступ
- 1. Актуальність теми
- 2. Мета і задачі дослідження
- 3. Технологія отримання п'єзокерамічних елементів
- 4. Вплив деяких технологічних чинників на властивості п’єзокераміки
- 4.1 Залежність властивостей п’єзокераміки від виду оформлення напівфабрикату
- 4.2 Вплив складу свинецьвмісних засипок і способу пакування виробі,. при їх використовуванні на властивості п’єзокерамічних елементів.
- 4.3 Роль атмосфери спікання на формування службових характеристик п’єзокерамічних елементів при різних методах підготовки зразків.
- Висновки
- Перелік посилань
Вступ
В даний час важко перерахувати області науки і техніки, де б не використовувалися пристрої на основі п’єзокераміки. Широке розповсюдження отримали високоефективні п’єзокерамічні матеріали на основі твердих розчинів цирконату і титанату свинцю з різними модифікуючими добавками (система ЦТС).
Розширення областей застосування і посилювання експлуатаційних режимів п′єзокерамічних матеріалів вимагає знань про її стійкість до дії різних зовнішніх чинників: температурних, вологісних, механічних, електричних, радіаційних і т.д.
П′єзокераміка не
належить до класичних видів кераміки, оскільки в її склад не входить
глиниста речовина. П′єзокерамічні матеріали синтезуються з
оксидів металів. Проте застосування характерного для керамічної
технології прийому – випалення при високій температурі
– виправдовує віднесення п′єзокерамічних матеріалів
до сімейства кераміки. П′єзо (від грецького пієзо
– тиснути) указує на те, що цьому виду кераміки належить
особлива властивість – п'єзоелектричний ефект.
Кераміка на основі цирконата-титанату свинцю (ЦТС) останнім часом привертає всю більшу увагу як сегнетоелектрика, яка дозволяє виготовляти різноманітні оригінальні прилади.
Не дивлячись на значні досягнення по підвищенню якості матеріалів на основі ЦТС, прогрес у вдосконаленні вказаних матеріалів останніми роками різко знизився. Це пояснюється тим, що можливості поліпшення електрофізичних властивостей п′єзокераміки шляхом зміни хімічного складу, модифікації практично вичерпані. На перший план виступає задача пошуку нових прийомів вдосконалення структури вже існуючих матеріалів, яка може розв'язуватися за рахунок інтенсифікації операцій на окремих стадіях технологічного процесу, підвищення активності реагуючих компонентів з метою підвищення швидкості гетерогенних процесів. Тому абсолютно очевидною є важливість розвитку і удосконалення методів отримання п′єзоматеріалів, що максимально задовольняють вимогам виробництва і нових областей застосування з'єднань системи ЦТС.
1. Актуальність теми
П’єзокерамічні вироби знаходять широке застосування в різних областях народного господарства: в радіоелектронній техніці, акустиці, ультразвукових перетворювачах, медицині і ін. Проте, у міру розширення профілю використання зросли і посилилися вимоги до неї, що зумовило разом з пошуком нових складів удосконалення технології виробництва.
Існує безліч чинників, що беруть участь у формуванні структурно-чутливих властивостей (рис. 1). З'ясування їх ролі і інтенсифікація технології з метою поліпшення параметрів п’єзокераміки є важливою і актуальною проблемою.

Рисунок 1 - Чинники, що впливають на властивості п’єзокерамічних виробів.Курсивом виділені чинники, що вивчалися в роботі.
2. Мета і задачі дослідження
Мета роботи – дослідження впливу деяких технологічних чинників на електрофізичні властивості п’єзокераміки ЦТС для оптимізації технології виробництва виробів.
При цьому розв'язувалися наступні задачі:
- Вивчити вплив складу свинецьвмісних засипок і способу пакування виробів при їх використанні на властивості п’єзокерамічних елементів.
- Дослідити залежність властивостей від виду пресування, температури спікання і мікроструктури кераміки.
- Встановити взаємозв'язок між видом модифікаторів в складі і умовами спікання.
- З'ясувати роль атмосфери спікання на формування службових характеристик п’єзокерамічних елементів при різних методах підготовки зразків.
- Визначити шляхи оптимізації технології виробництва п’єзокерамічних елементів.
3. Виробництво п’єзокерамічних виробів
До керамічних сегнетоелектриків відносяться титанат барія і ряд твердих розчинів на його основі, тверді розчини метаниобата свинцю і барія, тверді розчини титанату і цирконата свинцю, титанат свинцю і ін.
Особливістю цих матеріалів є те, що після дії на них постійного електричного поля вони стають п’єзоелектриками (п’єзокерамікою) і можуть бути використані як електромеханічні перетворювачі.
Деталі з сегнетокераміки є
виробами різних геометричних форм: циліндри, диски, призми, порожнисті
сфери і ін.
Для виготовлення сегнетоелектричної кераміки звичайно застосовують
вуглекислі солі і оксиди відповідних металів
[
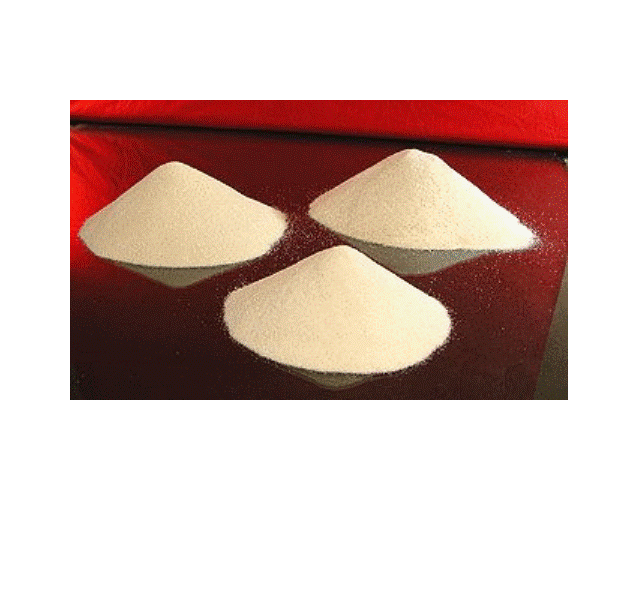
Рисунок 2 – Технологія виготовлення п’єзокерамічних виробів.
Вихідні матеріали, узяті у необхідній кількості, змішують і піддають синтезу при певних температурах. Отриманий після синтезу матеріал подрібнюють, пластифікують і оформлюють у деталь необхідної форми. Оформлені деталі піддають повторному нагріву, в процесі якого відбувається спікання мінеральних частинок і утворення полікристалічної структури [2].
Після механічної обробки до необхідних розмірів на деталі з сегнетокераміки наносять електроди методом впалювання, а потім поляризують їх постійною високою напругою.
Технологія виробництва передбачає перемішування і тонкий помел всіх складів у вібромлині. Простота конструкції вібромлина, невисока вартість і компактність дозволяють включати їх в діючі технологічні лінії без введення додаткових площ.
Тонкий помел у вібромлині є самим загальним способом збільшення поверхні взаємодії твердого тіла з навколишнім середовищем. Крім того, тонке подрібнення різко збільшує число вільних твердих частинок. Ці обставини приводять до підвищення активності твердих тіл як структуроутворюючих матеріалів і значно прискорюють розчинення, спікання, фазові і хімічні перетворення.
За відсутності вібромлина і, особливо, в лабораторних умовах допускається застосування кульових млинів для змішення і помелу мокрим способом.
Перед оформленням керамічної маси в деталь в неї вводять пластифікатори. Як останні можна застосовувати водний розчин полівінілового спирту, парафін, віск, декстрин і ін [2].
Застосування того або іншого пластифікатору визначається геометричною формою, розміром деталі і методом оформлення. Так, при оформленні деталей простих геометричних форм (дисків, циліндрів, призм і т. д.) як пластифікатор доцільно застосовувати 3-6 % водний розчин полівінілового спирту. При виготовленні деталей складної геометричної форми (порожнистих сфер, конусів і т. д.), що піддаються механічній обробці в необпаленому стані, як пластифікатор застосовують парафін. Цей же пластифікатор в суміші з олеїновою кислотою або воском застосовують при гарячому литті під тиском.
Процес оформлення деталей може бути здійснений різними методами: напівсухим пресуванням, гарячим литтям під тиском і в окремих випадках простяганням через мундштук [3].
Кожний з перерахованих вище методів оформлення деталей має свої переваги і недоліки. Найпродуктивнішим і легко здійсненним у виробництві є напівсухе пресування, але застосовується воно тільки для отримання деталей простих геометричних форм.
Гаряче лиття під тиском дозволяє оформляти деталі будь-якої геометричної форми, проте викликана при цьому необхідність введення в процес додаткової операції – випалювання пластифікатора, збільшує виробничий цикл на 70-80 год і вимагає установки додаткових пічних агрегатів, що обмежує можливість застосування даного методу у виробництві.
Метод простягання через мундштук доцільно застосовувати тільки для оформлення циліндрових деталей невеликих діаметрів (3-5 мм). Остаточне випалення деталей є найважливішою технологічною операцією, в процесі якої відбувається утворення монолітного тіла, званого керамічним черепком [2].
Умовою отримання високоякісних деталей є правильне їх укладання, рівномірний нагрів з певною швидкістю до встановленої температури і витримка при цій температурі.
Температура випалення залежить від вигляду і кількості домішок, що є у вихідних матеріалах. Час нагрівання і час витримки при максимальній температурі визначається не тільки складом і технологією приготування порошків, але і розмірами деталей, а також величиною садіння.
Швидкість нагріву доцільно застосовувати не вище 150 °С в годину, а швидкість охлаждения – в межах 150-200 °С в годину або охолоджувати з піччю (у разі випалення в камерних печах). Виключенням є крупногабаритні деталі з товщиною стінки більше 15 мм, швидкість нагрівання яких, так само як швидкість охолоджування, не повинна перевищувати 50-60 °С в годину.
Перераховані вище методи
оформлення не можуть забезпечити отримання деталей з сегнетокераміки
необхідної геометричної форми і заданих розмірів. Ця задача
розв'язується за допомогою механічної обробки деталей (заготівок) в
сирому
(необпаленому) і
обпаленому станах. В необпаленому стані звичайно механічно
обробляються заготівки, що відпресували, з метою додання ним необхідної
геометричної форми, отримання якої іншим методом не представляється
можливим.
Механічну обробку обпалених керамічних деталей або заготівок можна проводити точінням або шліфуванням на металообробних верстатах.
Дуже велике значення має механічна міцність зчеплення срібних електродів з поверхнею керамічних деталей. Найвище значення цієї міцності досягається при ретельному обезжиренні механічно оброблених деталей, виконанні санітарно-технічних вимог в процесі нанесення срібної пасти і дотриманні температурного режиму впалювання срібла в кераміку [3].
Завершальною операцією технологічного процесу є поляризація деталей постійним струмом високої напруги.
Істотними чинниками в цьому процесі є підготовка деталей до поляризації (ретельне їх очищення і обезжирення), середовище поляризації і нагрів деталей у разі поляризації в гарячому стані [3].
4. Вплив деяких технологічних чинників на властивості п’єзокераміки
4.1 Залежність властивостей п’єзокераміки від виду оформлення напівфабрикату
Першорядне значення у формуванні структури і властивостей п’єзокераміних елементів має метод оформлення напівфабрикату.
Істотна перевага холодного напівсухого пресування в прес-формах по простоті технологічного процесу, високої продуктивності і можливості механізації ослабляється неоднорідністю виробів по шільності, неможливістю виготовлення деталей складної форми.
Ізостатичне (гідростатичне) пресування дозволяє подолати недоліки одноосного пресування, проте, у свою чергу, неточність розмірів виробів, шерохуватість поверхонь вимагає додатково трудомісткої механічної обробки.
Переваги гарячого пресування – поєднання процесів пресування і спікання, отримання шільності зразків, близької до теоретичної, яка забезпечує підвищення рівня властивостей на 10-20%. Проте гаряче пресування має ряд недоліків: низька продуктивність, циклічність, збільшення зносу матриць.
Гаряче лиття під тиском дозволяє одержувати вироби дуже складної форми з великою точністю геометричних розмірів, але в порівнянні з іншими методами відрізняється низькою продуктивністю [2].
Для з'ясування ролі методів оформлення напівфабрикату використовували одноосне пресування в прес-формах і всебічне гідростатичне пресування (табл. 1). Аналіз отриманих результатів, як і очікувалося, показує про перевагу всебічного гідростатичного пресування над холодним пресуванням.
Таблиця 1 – Порівняльні результати середніх значень електрофізичних властивостей залежно від способу пресування і температури спікання кераміки ЦТССт-3
Тсп°С | Тиск | Партія | ρ, г/см3 | ε33/ε0 | tgδ,% | Kp | d31, 10-12Кл/Н | Qм |
1260 | однвісне | П-2 | 7,62 | 1330 | 0,56 | 0,595 | 131 | 700 |
1260 | ВГП | П-2/5 | 7,68 | 1120 | 0,54 | 0,599 | 122 | 780 |
1240 | однвісне | П-2 | 7,66 | 1320 | 0,57 | 0,578 | 125 | 970 |
1240 | ВГП | П-2/5 | 7,7 | 1190 | 0,48 | 0,592 | 125 | 1090 |
1220 | однвісне | П-2 | 7,90 | 1230 | 0,49 | 0,599 | 124 | 720 |
1220 | ВГП | П-2/5 | 7,68 | 1110 | 0,50 | 0,589 | 118 | 790 |
1220 | однвісне | П-2 | 7,91 | 1260 | 0,51 | 0,593 | 126 | 790 |
1200 | ВГП | П-2/5 | 7,75 | 1030 | 0,51 | 0,578 | 109 | 910 |
4.2 Вплив складу свинецьвмісних засипок і способу пакування виробів при їх використанні на властивості п’єзокерамічних елементів.
Отримання п’єзокераміки, що містить свинець, пов'язано з великими труднощами, обумовленими термічною дисоціацією цих з'єднань і, як наслідок, втратами оксиду свинцю в процесі термічної обробки. Оксид свинцю починає помітно випаровуватися з температури ~ 750°С.
Випаровування оксиду свинцю приводить до порушення стехіометрії і отримання матеріалу з невизначеними складом і властивостями [4].
Отримати вироби заданого складу, здавалося б, можна, введенням до складу початкової шихти надлишку оксиду свинцю, рівного втратам при термічній обробці кераміки. Проте цей шлях не може дати бажаних результатів, оскільки випаровування оксиду свинцю залежить не тільки від об'єму печі, але і від газообміну з навколишнім середовищем, конфігурації виробів (поверхні випаровування) і деяких інших чинників. Не можна забувати також про сильну корозійну дію пари оксиду свинцю на футерування печі і силітові нагрівачі, а також про велику токсичність цієї пари. Задача збереження оксиду свинцю при отриманні свинецьвмісної п’єзокераміки із заданими складом і властивостями привернула увагу багатьох дослідників [1].
Зменшення втрат оксиду свинцю в процесі спікання кераміки можна досягти, якщо проводити термічну обробку виробів в закритому просторі з додатковим джерелом пари оксиду свинцю. В лабораторній практиці, в дослідних виробництвах і в промисловості знайшов застосування спосіб попередження втрат свинцю при спіканні п’єзокерамічних виробів, який полягає у використанні нікелевих пакетів із засипкою. Сутність даного способу полягає в наступному (рис. 2).

1 - корпус пакету, 2 - кришка, 3 – екран, 4 – зразки, 5 – підсипка, 6 – засипка, 7 - ущільнений шар засипки, 8 – алундові, пластини, 9 - підставка
Рисунок 3 – Спосіб пакування виробів в нікелевий пакет і йго розміщення в робочому об'ємі печі [2].
В нікелевий пакет, що складається з корпусу і кришки, на дно укладають алундові пластини для попередження зміни поверхні дна при викривленні корпусу. Пластини покривають шаром засипки, яку ретельно вирівнюють і ущільнюють. Встановлюють шар виробів, присипаючи їх засипкою за допомогою просівання її через сито. Далі встановлюють подальші шари зразків або виробів, пересипаючи їх засипкою для попередження припікання зразків між собою.
Спікання виробів в засипці дозволяє створювати більш рівномірні подачу і відбір тепла від обпалюваних виробів, а також необхідне газове середовище, яке робить значний вплив на процес формування керамічного черепка при спіканні і може порушити первинну структуру матеріалу, з якого виготовлені вироби [5 ].
Недостатня кількість оксиду свинцю в засипці, рівно як і повне насичення дають незадовільні технологічні результати. В першому випадку засипка вступає в реакцію з матеріалом виробів, в другому - надлишок оксиду свинцю сприяє такому її спіканню, при якому вироби не можна відділити від неї. Нормальна засипка легко відділяється від виробів.
Для запобігання втрат PbO з виробів в роботі підбирали і вивчали застосування 30 і 50% засипки, що є сумішшю ZrO2 і PbO заздалегідь синтезованих при (1300±20) °С×0,5 год.
Експериментальні перевірки показали перевагу засипки з 30% PbO в порівнянні з 50%-вими. Рівень властивостей на п’єзокерамічних елементах спостерігається вище (табл.2) і до того ж вона порівняно легко відділяється від спеченої кераміки, що указує на відсутність взаємодії між ними.
Таблица 2 – Вплив складу засипок на властивості п’єзокерамічних елементів
Матеріал кераміки | Тип засипки | Т,°С×τ, час | ε33/ε0 | tgδ,% | d31, 10-12Кл/Н | Kp | Qм |
ЦТС-19 | 30%PbO + 70% ZrO2 | 1330×2 | 2120 | 2,92 | 173 | 0,590 | 78 |
ЦТСтБС-1 | 30%PbO + 70% ZrO2 | 1330×2 | 3950 | 3,50 | 310 | 0,628 | 43 |
ЦТС-19 | 50%PbO + 50% ZrO2 | 1330×2 | 1980 | 2,75 | 154 | 0,580 | 84 |
ЦТССтБС-1 | 50%PbO + 50% ZrO2 | 1330×2 | 3930 | 3,80 | 290 | 0,620 | 39 |
Істотний вплив надає і спосіб пакування виробів (табл.3).
Таблица 3 – Вплив кількості засипки на властивості п’єзокерамічних елементів
Матеріал кераміки | Кількість засипки | Т,°С×τ, год | ε33/ε0 | tgδ,% | d31, 10-12Кл/Н | Kp | Qм |
ЦТССт-3 | зразки повністю в засипці | 1240×2 | 1360 | 0,55 | 130 | 0,560 | 810 |
ЦТСтБС-4 | зразки повністю в засипці | 1240×2 | 1050 | 0,65 | 110 | 0,540 | 920 |
ЦТСтБС-1 | зразки повністю в засипці | 1330×2 | 4000 | 1,90 | 290 | 0,615 | 41 |
ЦТССт-3 | зразки присипані | 1240×2 | 1370 | 0,52 | 135 | 0,565 | 830 |
ЦТСтБС-4 | зразки присипані | 1240×2 | 1070 | 0,60 | 120 | 0,620 | 940 |
ЦТСтБС-1 | зразки присипані | 1330×2 | 4100 | 1,85 | 320 | 0,630 | 44 |
Повне засипання пакету з виробами в порівнянні з їх присипкою приводить до погіршення властивостей п’єзокерамічних елементів, що пов'язано з труднощами дифузії О2 з атмосфери.
4.3 Роль атмосфери спікання на формування службових характеристик п’єзокерамічнх елементів при різних методах підготовки зразків.
Для підвищення властивостей одновісноспресованих зразків використовували технологію кисневого спікання.
Дієвим способом активації спікання оксидних керамічних матеріалів і управління їх властивостями є використання штучних газових середовищ з різним парциальним тиском кисню.За літературними даними [6], величина Po2 в газовому середовищі при спіканні істотно впливає практично на всі властивості п’зокераміки.
Спікання всіх досліджених матеріалів значно поліпшується з підвищенням Po2 в газовому середовищі. Якщо в кисневому середовищі щільність кераміки досягає максимального значення при практично нульовій відкритій пористості, то спікання в газових середовищах з низьким Po2 приводить в порівнянні з повітряним середовищем до зниження шільності кераміки і зростання відкритої пористості. Зниження Po2, при спіканні викликає збільшення кристалитів. Спікання в кисні приводить до підвищення міцності всіх досліджених марок п’єзокераміки.
Використання методу гідростатичного пресування і спікання в середовищі кисню дозволяє досягти майже теоретичної шільності кераміки, як і у разі використання гарячого пресування. Що стосується електрофізичних властивостей кераміки, то в [7] наголошується незначне збільшення коефіцієнта електромеханічного зв'язку.
Можна виділити наступні основні чинники, що визначають характер впливу Po2 на властивості ЦТС.
Оскільки кисень здатний в значних кількостях розчинятися в твердій фазі ЦТС і заповнювати структурні вакансії, а інертні гази, зокрема азот повітря, не володіють такою здатністю, підвищення величини Po2, і особливо, спікання в чистому кисні сприяють швидкому і ефективному заліковуванню залишкової пористості. При спіканні в кисні можливо отримати високощільну кераміку ЦТС, яка не поступається по величині об'ємної шільності (до 99,5-99,9 теоретичної) гарячепресованим керамічним виробам.
Підвищення Po2 приводить до таких зсувів концентрації власних дефектів, які викликають зсув електрофізичних параметрів (до 5-7% для немодифікованого ЦТС) у бік більшої сегнетом’якості [8].
Зміни Po2, викликають зміни валентних станів елементів змінної валентності, що входять до складу модифікуючих добавок. За рахунок цього чинника можна збільшити такі параметри, як п’єзомодуль. до 15-25% в порівнянні із звичайним спіканнямм на повітрі.
Зменшення концентрації кисневих вакансій знижує швидкість масопереносу в ЦТС при температурах вторинного спікання. Це приводить до зменшення швидкості вторинної рекристалізації і розміру зерен в кераміці. Разом з підвищенням шільності цей чинник також сприяє збільшенню міцності п’єзокерамічних елементів.[2]
Висновки
На підставі проведених досліджень можна зробити наступні висновки:
Доведена перевага 30%-вих свинецьвмісних засипок в порівнянні з 50%-вими. Встановлено, що присипка зразків засипкою забезпечує більш високий рівень параметрів в порівнянні з властивостями зразків засипаних повністю, що пов'язано з труднощами дифузії кисню до виробів.
Показана перевага поєднання холодного пресування в прес-формах із спіканням в кисневому середовищі порівняно з технологією всебічного гідростатичного пресування в першу чергу по продуктивності при майже однакових рівнях властивостей..
Перелік посилань
- Глозман, И.А. Пьезокерамика / И.А.Глозман. – М.: Энергия, 1967. – 272с.
- Прилипко, Ю.С. Функциональная керамика. Оптимизация технологии: Монография / Ю.С.Прилипко. – Донецк.: Норд-пресс, 2007. – 492с.
- Яффе, Б. Пьезоэлектрическая керамика / Б. Яффе , У.Кук, Г.Яффе. – М.: Мир, 1974. – 288с.
- Смажевская, Е.Г. Пьезоэлектрическая керамика / Е.Г.Смажевская , Н.Б. Фельдман. – М.: Советское радио, 1971. – 200с.
- Шишковский В.И. Влияние состава газовой фази при спекании на электрофизические свойства и прочность пьезокерамики ЦТС / В.И. Шишковский, В.В. Приседский, Н.А. Задорожная, В.В Климов // В сб.: Материалы для электронной техники. – М.: НИИТЭХИМ, 1979. – С. 8-13.
- Фесенко, Е.Г. Новые пьезокерамические материалы / Е.Г.Фесенко. – Изд. Ростовского университета, 1983. – 160с.
- Поляков, А.А Технология керамических радиоэлектронных материалов/ А.А. Поляков. –М.: Радио и связь, 1989 –200с.
- Уорден. К Новые интелектуальные материалы и конструкции. Свойства и прменение/ К. Уорден – М.: Техносфера, 2006. –224с.