Abstract
Content
- Introduction and justification timelines of the theme
- 1. The purpose and objectives of the study
- 2. Expected scientific novelty
- 3. The practical significance
- 4. Analysis of the current state of research question
- 4.1 Analysis of hard materials
- 4.2 Analysis of the final treatment methods difficult to machine materials
- Conclusion
- References
Introduction and justification timelines of the theme
Manufacture of match machine building products in market relations is possible through the use of materials that meet the level of high technology. Current industry using materials that have some individual characteristics, such as high strength chemical durability, heat resistance and often complex of these properties. There are high temperatures and pressure on the cutting edge tools during cutting such materials, with low thermal conductivity and high strength characteristics [1]. Effective abrasive machining difficult to machine materials (DMM) is possible through the using of cutting tools made of superhard materials. This is due to the fact that the structure of modern DMM and alloys are hard carbides and nitrides, physical and mechanical properties are close to the properties of abrasive materials. These products can handle only a tool made of diamond and cubic boron nitride [2].
Therefore, the development process to ensure the process of grinding of DMM is a hot topic for research. Little studied is the grinding of Hadfield steel, a high level of durability.
1. The purpose and objectives of the study
The purpose of master's work is to provide a given quality of surface treatment at the expense of rational modes of treatment and characteristics of the rational choice of the grinding tool.
To achieve this goal will be to perform the following tasks:
- Perform analysis of DMM in terms of grinding.
- Cause analysis of the modes of processing and grinding tools.
- Perform simulation of behavior of a single grain in the bundle.
- Offer advice on technological protection when handling the DMM.
The object of research in this paper is the grinding tool used to handle the DMM.
The subject of this study is the grinding of Hadfield steel.
2. Expected scientific novelty
Based on the analysis performed and the review of research on this topic developed by simulation the behavior of a single grain in conjunction with the grinding of Hadfield steel.
3. The practical significance
In this paper we developed recommendations for the treatment of intractable process of Hadfield steel.
4. Analysis of the current state of research question
4.1 Analysis of hard materials
In recent years, made cutting tools equipped with a tungsten hard alloys (THA) based on carbides or carbonitrides of titanium and nickel-molybdenum bond. Compared with hard tungsten alloys, THA have less friction and greater durability.
Since the processing THA appear larger values of cutting force components and efficient power sanding, then the probability of occurrence of cracks and chips on the treated surface. When sanding THA circles on metal and ceramic binders observed brining circles, smoothing the relief of the working surface of the circle. So better to polish diamond wheels are alloys based on organic binders [2].
Vanadium die steels belong to a class that. Their bad treatment of grinding abrasive wheels associated with the presence in their structure of solid chromium carbides, tungsten and molybdenum, hardness which is comparable to the hardness of fused [4].
Poor sanding marks new high-speed steels (compared to Р18) is explained as well as vanadium and die steels, the presence in their structure of solid chromium carbide, tungsten, molybdenum and vanadium. In this case, grains of white fused, typically used in grinding wheels for grinding tools and high-speed steel and has a microhardness of 20-21 GPa, are unable to compete with the carbides of chromium, vanadium, etc. In addition, the rapid blunting community causes an additional increase in temperature in the grinding zone. The formation of retained austenite, which creates additional stresses that may lead to the formation of sanding cracks [2].
DMM have high ductility, and therefore when they are treated the phenomenon of work hardening is manifested to a greater extent than in the processing of structural carbon steels. With a pulsating flow of the process of plastic deformation of high uprochnyaemost the material can lead to an increase in vibration. Therefore, the processing of such materials is necessary that the technological system has high rigidity [5].
One of the members is DMM Hadfield steel. It is characterized by high wear resistance, which is due to its ability to very intensive work hardening during plastic deformation occurring in the zone of frictional contact [3]. Designation of steel grade – 110Г13Л.
Chemical composition of steel 110Г13Л according to GOST 977-88: C 0,9-1,5%; Si 0,3-1,00%; Mn 11,5-15%; Ni is not more than 1%; Cr less than 1%; S is not more than 0,05%; P not more than 0,12%. It is intended for the manufacture of parts for wear in the operating conditions of friction, pressure and shock loads at which the samouprochnenie (hardening) of steel and its strength and wear resistance is greatly increased.
Due to its high hardness and wear resistance of Hadfield steel has rapidly gained acceptance in the industrial world, it was used for the manufacture of those parts that are in use constantly subjected to strong impact, and usually are easily damaged due to abrasion. Such, for example, rail crossings, cheeks crushers, balls for ball mills, teeth and the front wall of bucket excavators, crawler tracks, etc [6].
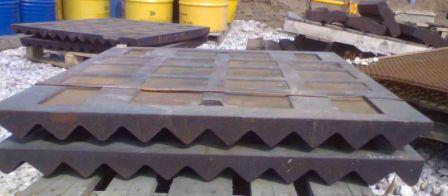
Figure 1 – Crushing of steel plates 110Г13Л
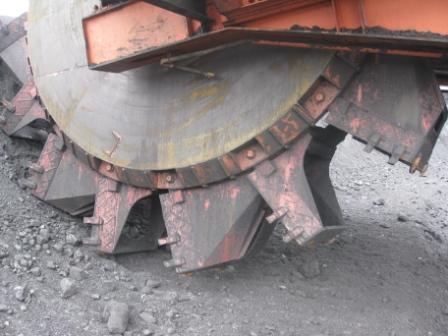
Figure 2 – The tooth excavator bucket of steel 110Г13Л
4.2 Analysis of the final treatment methods difficult to machine materials
There are many different methods of finishing materials, one of them is grinding.
Grinding – a type of metal cutting. In the grinding allowance is removed with abrasive tools – grinding wheels. Grinding wheel is a porous body consisting of a large number of small grains [7]. Grinding can handle almost any material, since the hardness of the abrasive (HB = 2200-3100) and diamond (НВ = 7000) is very high. For comparison, the hardness of tungsten carbide HB = 1300, HB = 2000 of cementite, tempered steel HB = 600-700 [8].
For grinding operations DMM dramatically increase performance requirements for abrasive tools. Traditional tools and techniques to improve performance grinding operations (use of metalworking fluids, the change of cutting tools and features) are not always effective enough.
Now much attention is paid to finding ways to improve the cutting properties of abrasive tools. In particular, common methods based on the introduction of substances into the cutting area improving machinability of materials, the use of cutting elements is not abrasive tools – ligaments and pores. Different varieties of these methods combined the concept of impregnation
. Impregnation of grinding wheels is not bad for their physical and mechanical properties, significantly improving their cutting ability [9].
Currently, treatment of high-vanadium high-speed steels by means of diamond grinding circles at the metal bond, after the electroerosion method changes, maintaining the cutting ability of the working surface of the circle in the process of electroerosion treatment effects. Spark provides a range of editing his great cutting ability as a first treatment and during the grinding process [10].
One way to improve performance when machining is introduction of creep feed grinding, which in most cases more efficient than processing blade tool, especially in the manufacture of parts made of superalloys and titanium alloys, corrosion resistant, high-and tool steels [11].
Creep feed grinding is characterized by significant cross-feed rates and small longitudinal feeds.
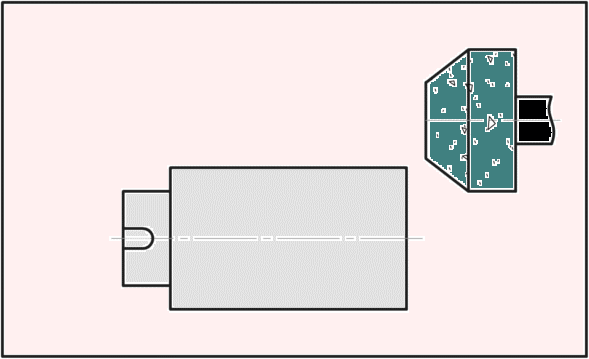
Figure 3 – Scheme of creep feed grinding
(animation: 8 frames, 10 cycles of repeating, 48 kilobytes)
At the present stage of technology one of the most important ways of dealing with processing details of the DMM is a conductive diamond grinding and abrasive wheels. For grinding of hard metal parts are used only diamond circles, and from high-temperature alloys, stainless and structural steels – diamond grinding wheels and less on the metal bond.
The use of abrasive wheels for metal bond is possible with continuous electrochemical grinding wheel dressing. The advantage of this method of grinding is the lack of friction with the machined surface of the ligament. For this purpose we sometimes use a reversible power source, giving the half-wave back. Known use of electroneutral abrasive tools, in which the electrochemical and mechanical processes are separated in space. Electrochemical removal from the workpiece surface is carried out in this case, the additional terms. All types of processing methods using anodic processes can be very effectively used in industry [12].
Conclusion
In sum, it should be noted that the processing of high DMM with the achievement of the required quality of parts is an important task for research. A wide variety of DMM involves a number of ways of processing, but as a rule, the most high-performance and the ultimate way to handle such products used grinding.
First of all, based on the properties of the material, shape and quality of the workpiece, it is necessary to select and shape characteristics of the grinding wheel. Since in the process of grinding is DMM intense heat (it can affect the strength of the treated surface) and the formation of wear of the grinding wheel and workpiece – sludge (may adversely affect the quality of surface finish) – requires a more sophisticated system of SOTS.
Due to the high hardness of DMM, the character of wear of the cutting surface of the grinding wheel wear is different from the grinding of carbon steel. The hardness of the material grains of the grinding wheel is comparable with the hardness of the workpiece. Therefore, for the processing of such materials using silicon carbide, synthetic or natural diamond.
Many researchers have proposed to control the state of the working surface of grinding wheel by means of its changes in order to avoid negative effects of increasing cutting forces in the process of grinding.
The grinding process DMM assumes a perfect system and COTS devices to manipulate the working surface of grinding wheel. These devices belong to the technological protection of the grinding process. Consequently, the theme of Engineering support during grinding articles of difficult to machine materials
is relevant and can be chosen as the theme of master's work.
References
- Куприянов В.А. Мелкоразмерный инструмент для резания труднообрабатываемых материалов. – М.: Машиностроение, 1989. – 136 с.
- Прогрессивные методы абразивной обработки металлов / И.П. Захаренко, Ю.Я. Савченко, В.И. Лавриненко, С.М. Дегтяренко; Под ред. И.П. Захаренко. – К.: Техника, 1990. – 152 с.
- Иванов Ю.Ф., Алешина Е.А., Колубаев Е.А., Колубаев А.В., Сизова О.В., Громов В.Е. Закономерности формирования структуры поверхностного слоя стали Гадфильда при трении // Физ. мезомех. – 2006. – Т. 9. – № 6. – С. 83-90.
- Основы проектирования и технология изготовления абразивного и алмазного инструмента. / Ю.М. Ковальчук, В.А. Букин, Б.А. Глаговский и др.; Под общей ред. Ю.М. Ковальчука – М.: Машиностроение, 1984. – 288 с.
- Труднообрабатываемые материалы [Электронный ресурс]. – Режим доступа: http://iron–lab.ru
- Специи для стали [Электронный ресурс]. – Режим доступа: http://wolframpo.ru
- Лоскутов В.В. Шлифование металлов: Учебное пособие для профессинально-технических училищ. – М.: Машгиз, 1962. – 280 с.
- Ящерицын П.И., Еременко М.Л., Жигалко Н.И. Основы резания материалов и режущий инструмент. – Минск: Высшая школа, 1975. – 528 с.
- Никитин А.В. Шлифование труднообрабатываемых материалов импрегнированными кругами как способ их режущих свойств // Инструмент и технологии. – 2010. – №28. – Вып. 2 – С. 52-58.
- Матюха П.Г., Габитов В.В. Удельная себестоимость шлифования стали Р6М5Ф3 в зависимости от способа правки и электроэрозионных воздействий на рабочую поверхность кубонитового круга // Сверхтвердые материалы. – 2009. – № 5. – С. 63-69.
- Глубинное шлифование деталей из труднообрабатываемых материалов / С.С. Силин, В.А. Хрульков, А.В. Лобанов, Н.С. Рыкунов. – М.: Машиностроение, 1984. – 64 с.
- Вайнберг Р.Р., Васильев В.Г. Электрохимическое шлифование токопроводящими абразивными и алмазными кругами. – М.: Машиностроение, 1976. – 32 с.
Remark! This master's work is not completed yet. Final completion: December 2012. The full text of the work and materials on the topic can be obtained from the author or his head after this date.