Abstract
Сontent
- Introduction
- 1. Theme urgency
- 2. Goal and tasks of the research
- 3. The development of mechatronic system structure moving the conveyor pans of the mechanized complex
- Conclusion
- References
Introduction
The problem of the accelerated creation of competitive mining machines, is still today an urgent problem facing the mining machinery Ukraine.
Now main volume method of underground coal mining is provided by a combine complexes and plow equipment with powered supports (Pic. 1).
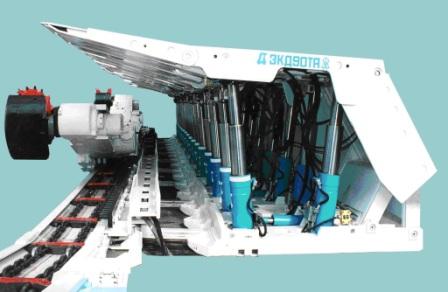
Pic. 1 – Mechanized complex (side view)
Creation and implementation of mechanized cleaning systems (MCS) in the practice of underground coal mining has played a crucial role in modernization of the coal industry. Mechanized sewage treatment systems have been used in the potash mines and production of a number of other minerals mainly with formation of bedding structure.
mechanized coal extraction process is accompanied by complex movements of the section lining and pipeline (Pic. 3, 4, 5), which is the guiding framework for the shearer, hydraulic jacks advancing mechanized roof supports. At present, the most common is the wave shifting of the conveyor (Pic. 2).
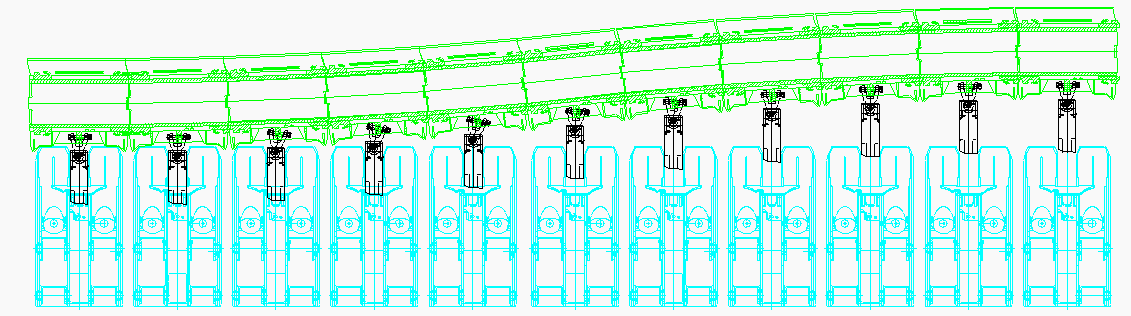
Pic. 2 – The wave shifting of the conveyor hydrocylinders of lining
In the initial position of downhole pipe rests against the slaughter, grain is located at one end of the lava and prepared for the removal of the strip, lining rasperty section and removed from the conveyor advancing one step (Pic. 2a) (the most common scheme of work-charged artificial linings). When the grain begins to move and cut coal is carried out, following the passage of the combine is the removal of thrust, shifting support units and their thrust, and at a distance of 12-15 m from the harvester moves and the conveyor (Pic. 2b) (the most common wave-like shifting of the conveyor). In the approach to combine roadway run terminal operations. P> Section
move, creating a wave of some of the combine, while the conveyor moved to the bottom is not completely (Pic. 2c), thus being prepared to form an oblique arrival to combine. Next to the face conveyor is retracted so that the wave of the curved conveyor coincide with the wave formed by the sections (Pic. 3a). After this harvester starts to move in the opposite direction and created the position of the conveyor causes him to carry out a notch in the coal seam (Pic. 3b). By the end of the notch is aligned sections of the lining of the combine (Pic. 3c), and then the alignment pipeline (Pic. 4a). Combine returns to drift in the pipeline is already aligned (Pic. 4b). As a result, the complex is in position, prepared to start the next strip of coal extraction.
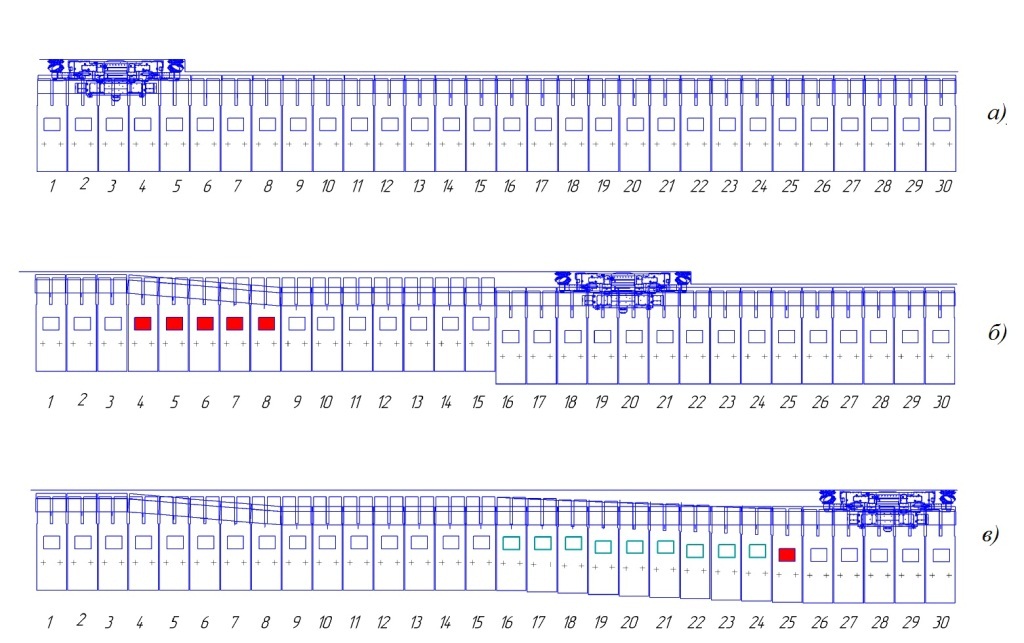
Рiс. 3 – Schemes of advancing roof supports for excavation of coal strip
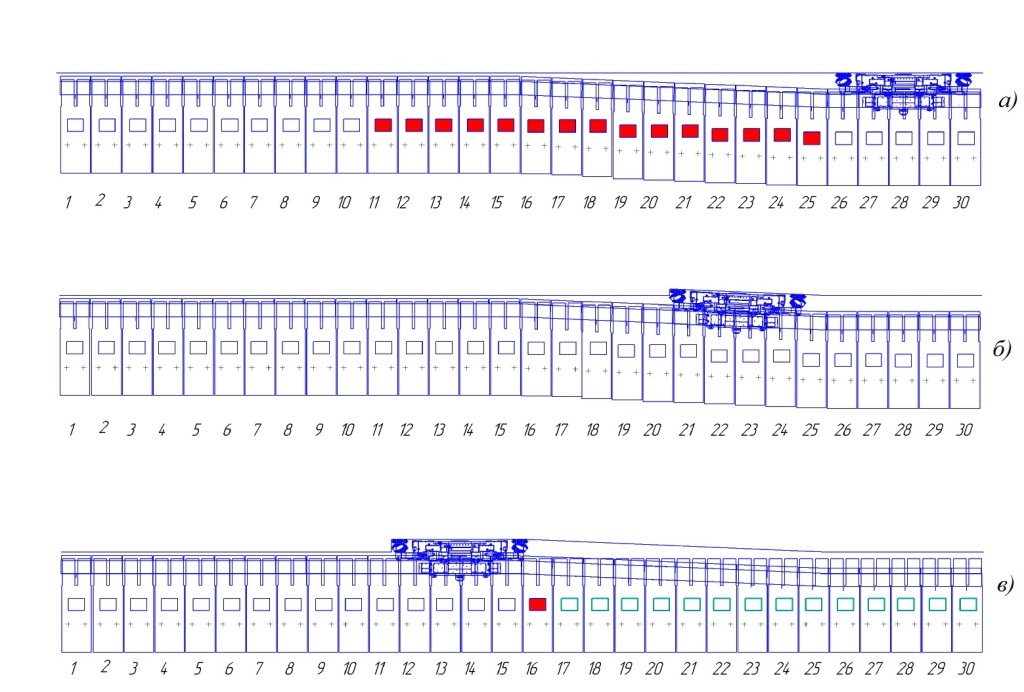
Pic. 4 – Terminal operations at the complex work (forming an oblique arrival, a notch combine, the alignment of the sections)
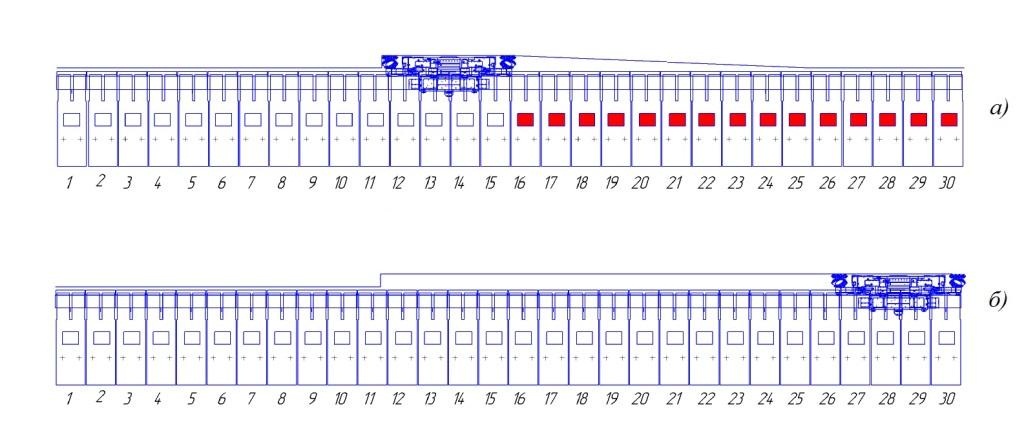
Pic. 5 – Terminal of operation (the alignment conveyor, pass combine)
The current process is advancing pans accompanied by a number of disadvantages [4, 5], as follows:
- control of the system is advancing hand;
- safety valve and the appearance of the maximum stress in the elements of movements, which are undesirable, as much impact on reducing their resource;
- exclude the possibility of selecting the optimal scheme of advancing that would accelerate the process of its implementation and to reduce the load of the moving elements of the system. li>
- pazrabotannaya structure of mechatronic system for moving the conveyor with an adaptive control system allows to eliminate the existing shortcomings of advancing, as well as to ensure selection of the best algorithms for advancing the light loading of the elements of movement. li>
1. Theme urgency
Today, the main characteristics of the mining industry in Ukraine is the intensification of work and reducing the cost of coal, which is achieved by increasing the load on the working face, an increase in their length and at the same time reducing their number. It is planned to increase the productivity of coal from one of lava up to 10 tons of coal per day and over, thus seeks to create a coal-mining enterprises of the "lava pit". In this regard, a mining equipment imposed ever-increasing performance requirements of the resource, reliability and performance that can not be achieved without equipping them with the various systems of automatic control and diagnosis[1, 2].
Currently intensively improve complexes with increased reliability and service life of machinery and equipment, working off of programmable systems, diagnostics of technical condition of machines, systems, operation and automatic control, thus achieving high stability of the complexes in the rational mode [3].
Against the background of the complex mehatronizatsii and intensification of treatment works there is a need to provide a high service life and reliability of structural elements of the system moving conveyor, as well as to increase the speed of the conveyor and advancing sections of mechanized bolting after the passage of the combine.
3. Goal and tasks of the research
Summary of the hydraulic drive powered supports and associated conveyor components are based on the writings of Prof. Horina, Y. Ponomarenko, S. Grebenkina, A. Balandin, J. Shein, A. Dokukina etc.[7, 8, 9, 10]
A great contribution to the development of the science of the hydraulic drive and problem-solving research and development of hydraulic powered roof supports made ??of institutions IGD im. AA Skochinskiy, Giprouglemasha, NGO "Avtomatgormash," NSU, IGTM Nadu, "Dongiprouglemash" DonUGI, DonNTU. P>
Further improvement involves moving conveyor it mehatronizatsiyu based adaptive control system[6], which will provide an opportunity to increase resource jacks by avoiding peak loads, and with it will provide the optimal choice of time and effort of the algorithm moving pans
3. The development of mechatronic system structure moving the conveyor pans of the mechanized complex
In connection with the need to improve the system of advancing the conveyor structure was developed mechatronic system for moving the conveyor chutes with an adaptive control system, which is presented in Figure 6. p>
main elements of this structure are: p>
– spatially moving mass of the i-th and (i +1)-th pans;
- Ci – space a shifting mass of the i-th section of roof supports;
- OXYZ— coordinate system rigidly attached to the slaughter;
- ГД – advancing hydraulic jack;
- БУ – computer control unit with joystick;
- АР – automatic discharge;
- ГА – accumulator;
- ГР – control valve;
- ДР – throttle;
– the i-th position sensor rod advancing hydraulic jack;
– the i-th pressure sensor in the hydraulic cylinders of the system;
– the i-th sensor in the compounds of the efforts of pans;
– the i-th sensor state switching devices.
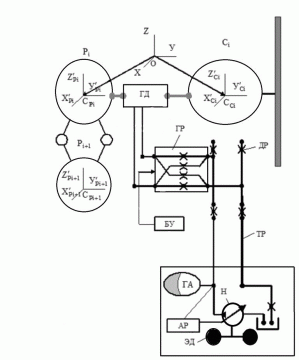
Рiс. 6 – The structure of the mechatronic system for moving the conveyor with an adaptive control system.
(Animation: 12 frames, 5 cycles of repetition, 292 Кб)
Description of the principle of the control system.
Signals from the sensors (proximity switches, parameters, state of the switchgear and effort in the joints) come to the sensory system that receives these signals and transmits the information system.
Information System produces a visualization of the information received and issue it to the operator, and transmits information to the adaptive control system to optimize the management process of advancing. The operator selects a particular algorithm for moving the conveyor. In the adaptive signal control system worked through the management units advancing through which implemented one or the other advancing algorithm. Initially, the algorithm provides for the movement of the conveyor pans in one, as the highest priority, but if the effort will move the large, will be applied to a different algorithm. Also, the adaptive system is associated with the automatic discharge. P>
Thus, the bust is advancing several options from which to select the most appropriate time and efforts in advancing a system that provides the ability to eliminate the maximum load on the final stage of advancing, advancing hydraulic jack to raise resources and gidromagistraley. p>
Conclusions
- State mining today is characterized by the intensification of work, reducing the cost of coal, the need to improve life and reliability of mining machines.
- Providing high rates of lava mining today is accompanied by an increase in feed rate of shearers and, therefore, needs to accelerate the process of advancing the pipeline and support units.
- The current process of advancing the pipeline accompanied by a number of shortcomings: manually operated, the advent of peak loads in the elements of movement, which reduces the service life and reliability of the design, as well as preclude the use of alternative algorithms for moving the conveyor chutes to choose the most optimum conditions of time and effort.
- Structure developed mechatronic system for moving the conveyor with an adaptive control system allows to eliminate the existing shortcomings of advancing, as well as to ensure selection of the best algorithms for advancing the light loading of the system elements.
- Way forward is to develop a mathematical model of the mechatronic system for moving the conveyor and the rationale for the choice of parameters for its operation.
Ol>
References
- Отличительные особенности машин современных механизированных комплексов / Н.И. Стадник, А.В. Сергеев, А.В. Мезников, В.П. Кондрахин. – Донецк: С. 111.
- К вопросу повышения технического уровня высокопроизводительных комплексов / Семенченко А. К., Шабаев О. Е., Семенченко Д. А., Степаненко Е. Ю., Мотин Н. Н. // Наукові праці Донецького національного технічного університету, випуск 14 (127), Серія: гірничо-електромеханічна, Донецьк - 2007.
- Очистные механизированные комплексы для добычи угля в длинных забоях / Габов В.В. проф., // Горная техника - 2004
- Горные машины для подземной добычи угля: Учеб.пособ. для вузов / П.А. Горбатов, Г.В. Петрушкин, Н.Н. Лысенко, С.В. Павленко, В.В. Косарев; Под общ. ред.П.А. Горбатова. – Донецк, 2006. – 669с.
- А.К. Семенченко, Д.Э. Макаренко, Ю.М. Кирилюк. Математическая модель перемещения конвейера и секции механизированной крепи очистного комплекса. УКД 622.232/ Научные работы ДонНТУ-2010.
- Обоснование параметров системы перемещения конвейера и секции крепи комплекса МДМ / Д.Е.Макаренко. квалиф. магистр. раб., ДонНТУ – 2010.
- Баландин А.А. Исследование гидросистем передвижения секций механизированных крепей и совершенствование методики их расчета: дис. канд. техн. наук. – М., 1981. – 190 с.
- Хорин В.Н. Гидравлические системы механизированных крепей / В.Н. В.Н. Хорин, С.В. Мамонтов, В.Я. Каштанова. – М.: Недра, 1971. – 388 с.
- Хорин В.Н. Объемный гидропривод забойного оборудования / В.Н. Хорин. – М.: Недра, 1980. – 415 с.
- Пономаренко Ю.Ф. Инженерная методика проектного расчета параметров гидросистемы механизированных крепей / Ю.Ф. Пономаренко, А.А. Баландин. – М.: ИГД им. А.А. Скочинского, 1981.